Jak wybrać rury z włókna szklanego: specyfika produkcji i przegląd wiodących producentów
Dzięki połączeniu pozytywnych właściwości szkła i polimerów, rury z włókna szklanego mają prawie nieograniczone możliwości zastosowania - od układania kanałów wentylacyjnych po układanie szlaków petrochemicznych.
W tym artykule rozważamy główne cechy rur z włókna szklanego, znakowanie, techniki wytwarzania kompozytu polimerowego oraz skład składników spoiwa, które określają zakres kompozytu.
Dajemy również ważne kryteria wyboru, zwracając uwagę na najlepszych producentów, ponieważ ważną rolę w jakości produktów przypisuje się możliwościom technicznym i reputacji producenta.
Treść artykułu:
Ogólna charakterystyka włókna szklanego
Włókno szklane - tworzywo sztuczne, które zawiera elementy z włókna szklanego i wypełniacz wiążący (polimery termoplastyczne i termoutwardzalne). Oprócz stosunkowo niskiej gęstości wyroby z włókna szklanego charakteryzują się dobrymi właściwościami wytrzymałościowymi.
Ostatnie 30–40 lat z włókna szklanego jest szeroko stosowane do produkcji rurociągów do różnych celów.
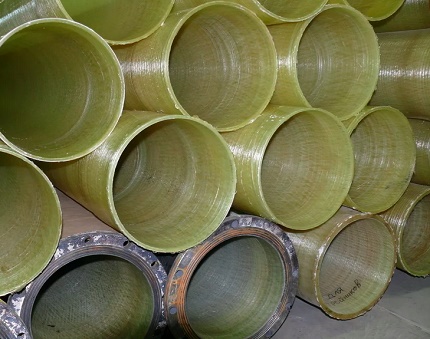
Autostrady łączą cechy szkła i polimerów:
- Lekki Średnia waga włókna szklanego wynosi 1,1 g / cm3. Dla porównania ten sam parametr dla stali i miedzi jest znacznie wyższy - odpowiednio 7,8 i 8,9.Dzięki łatwości prace instalacyjne i transport materiału są ułatwione.
- Odporność na korozję Składniki kompozytu mają niską reaktywność, dlatego nie podlegają korozji elektrochemicznej i rozkładowi bakteryjnemu. Ta jakość jest decydującym argumentem za włóknem szklanym do podziemnych obiektów użyteczności publicznej.
- Wysokie właściwości mechaniczne Bezwzględna wytrzymałość na rozciąganie kompozytu jest gorsza niż w przypadku stali, ale parametr wytrzymałości właściwej znacznie przewyższa polimery termoplastyczne (PVC, HDPE).
- Odporny na warunki atmosferyczne. Zakres temperatur granicznych (-60 ° С .. + 80 ° С), obróbka rur ochronną warstwą żelkotu zapewnia odporność na promienie UV. Ponadto materiał jest odporny na wiatr (limit wynosi 300 km / h). Niektórzy producenci twierdzą, że złącza rurowe są odporne na trzęsienie ziemi.
- Ognioodporność. Niepalne szkło jest głównym składnikiem włókna szklanego, więc materiał jest trudnopalny. Podczas spalania toksyczna dioksyna nie jest uwalniana.
Włókno szklane ma niską przewodność cieplną, co tłumaczy jego właściwości termoizolacyjne.
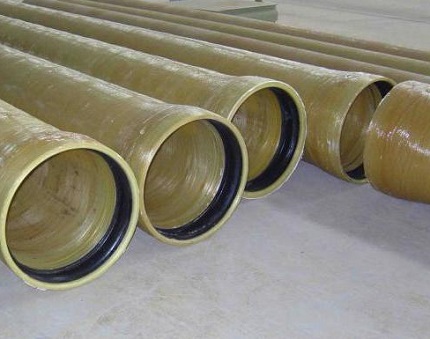
W miarę zużycia wewnętrznych ścian włókna stają się odsłonięte i odrywają się - cząsteczki mogą dostać się do transportowanego medium.
Technologie wytwarzania rur z włókna szklanego
Właściwości fizyko-mechaniczne produktu końcowego zależą od techniki produkcji. Złączki kompozytowe są produkowane na cztery różne sposoby: wytłaczanie, pultruzja, odlewanie odśrodkowe i nawijanie.
Technologia nr 1 - Wytłaczanie
Wytłaczanie jest procesem technologicznym opartym na ciągłym wymuszaniu pastowatego lub bardzo lepkiego materiału przez narzędzie formujące. Żywicę miesza się z pokruszonym włóknem szklanym i utwardzaczem z tworzywa sztucznego, a następnie podaje do wytłaczarki.
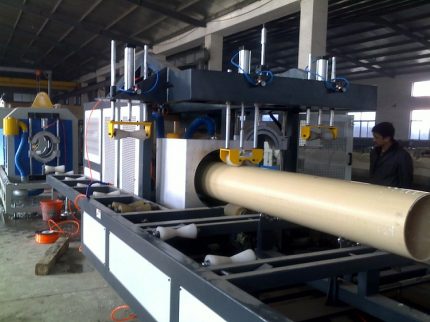
Wysoko wydajna linia do wytłaczania pozwala uzyskać bezramowe produkty kompozytowe w niskiej cenie, ale zapotrzebowanie na to jest ograniczone ze względu na niskie właściwości mechaniczne. Podstawą matrycy polimerowej jest polipropylen i polietylen.
Technologia # 2 - Pultruzja
Pultruzja to technologia wytwarzania kompozytowych długich elementów o małej średnicy o stałym przekroju. Przechodząc przez ogrzewaną matrycę do formowania (+140 ° С), detale są „wyciągane” z materiału z włókna szklanego impregnowanego żywicą termoutwardzalną.
W przeciwieństwie do procesu wytłaczania, w którym nacisk jest determinującym czynnikiem, w jednostce pultrusyjnej rolę tę pełni efekt ciągnięcia.

Proces technologiczny:
- Włókniste włókna z cewek są wprowadzane do kąpieli polimerowej, gdzie są impregnowane żywicami termoplastycznymi.
- Przetworzone włókna przechodzą przez jednostkę wstępnego formowania - nici są wyrównane i zyskują pożądany kształt.
- Nieutwardzony polimer dostaje się do matrycy. Ze względu na kilka grzejników tworzony jest optymalny tryb polimeryzacji i wybierana jest prędkość ciągnięcia.
Utwardzony produkt jest ciągnięty przez maszynę ciągnącą i krojony na segmenty.
Charakterystyczne cechy technologii pultruded:
- dopuszczalne polimery - żywice epoksydowe, żywice poliestrowe, winyle;
- prędkość ciągnięcia - zastosowanie innowacyjnych zoptymalizowanych polimerów „pultrudowanych” pozwala przyspieszyć przeciąganie do 4-6 m / min. (standard - 2-3 m / min.);
- rozruch rozruchowy: minimalna - 3,05 * 1 m (siła ciągnąca do 5,5 t), maksymalna - 1,27 * 3,05 m (siła - 18 t).
Wyjściem jest rura z idealnie gładkimi ścianami zewnętrznymi i wewnętrznymi, o wysokim wskaźniku poziomu i wytrzymałości.
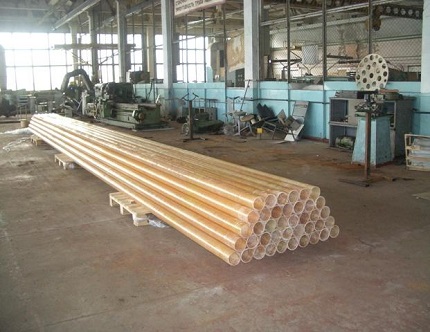
Wady tej metody nie dotyczą jakości oryginalnego produktu, ale samej technologii. Argumenty „przeciw”: wysoki koszt i czas trwania procesu produkcyjnego, niemożność wytwarzania rur o dużej średnicy zaprojektowanych do znacznych obciążeń.
Technologia # 3 - Odlewanie odśrodkowe
Szwajcarska firma Hobas opracowana i opatentowana technika formowania odśrodkowego. W tym przypadku produkcja odbywa się od zewnętrznej ściany rury do wewnętrznej za pomocą formy obrotowej. Skład rurociągu obejmuje: zgniecione szklane wieże, piasek i żywice poliestrowe.
Surowce są podawane do obracającej się matrycy - powstaje struktura zewnętrznej powierzchni rurociągu. W miarę produkcji składniki stałe, wypełniacz i włókno szklane są mieszane z ciekłą żywicą - polimeryzacja przebiega szybciej pod wpływem katalizatora.
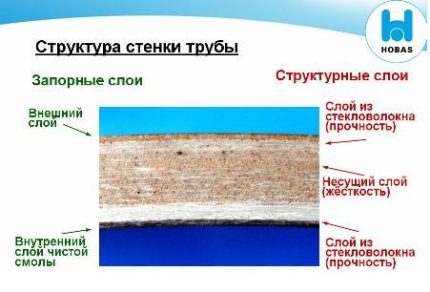
Dodatkowe zalety:
- wysoka dokładność wymiarów oryginalnego produktu (wewnętrzna sekcja formy obrotowej odpowiada zewnętrznej średnicy gotowego produktu);
- możliwość odlewania ściany o dowolnej grubości;
- wysoka sztywność pierścienia kompozytu polimerowego;
- uzyskanie gładkiej powierzchni na zewnątrz i wewnątrz łączników rurowych.
Wadą odśrodkowej produkcji rur z włókna szklanego jest energochłonność i wysoki koszt produktu końcowego.
Technologia nr 4 - uzwojenie progresywne
Najpopularniejszą techniką jest ciągłe nawijanie.Rura jest tworzona przez naprzemienny trzpień z włóknem szklanym z polimerami z procesami chłodzenia. Metoda produkcji ma kilka podgatunków.
Technologia pierścienia spiralnego
Układarka włókien to specjalny pierścień, na obwodzie którego znajdują się dysze obrotowe z nitkami.
Element roboczy stale porusza się wzdłuż osi ruchomej ramy i rozprowadza włókna wzdłuż linii śrubowych.
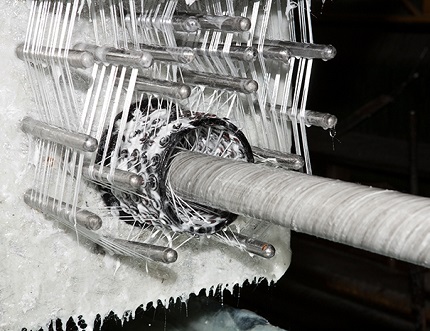
Główne zalety metody:
- równomierna wytrzymałość na całej powierzchni autostrady;
- doskonała tolerancja obciążeń rozciągających - wyklucza się pęknięcia;
- tworzenie produktów o zmiennej średnicy i przekrojach o złożonej konfiguracji.
Ta technika umożliwia uzyskanie rur o dużej wytrzymałości przeznaczonych do pracy pod wysokim ciśnieniem (sieci inżynieryjne pompa-kompresor).
Spiralne zwijanie taśmy
Technika jest podobna do poprzedniej, z tą różnicą, że układarka podaje wąską wstęgę włókien. Gęstą warstwę wzmacniającą uzyskuje się poprzez zwiększenie liczby przejść.
Tańszy sprzęt jest zaangażowany w produkcję niż metoda spiralnego pierścienia, ale kilka istotnych wad związanych jest z uzwojeniem „wstążkowym”:
- ograniczona wydajność;
- luźne układanie włókien zmniejsza wytrzymałość rurociągu.
Metoda taśmy spiralnej jest istotna w produkcji złączek do rur o niskim, umiarkowanym ciśnieniu.
Metoda wzdłużno-poprzeczna
Ciągłe nawijanie odbywa się - układarka umieszcza jednocześnie włókna podłużne i poprzeczne. Nie ma ruchu wstecznego.
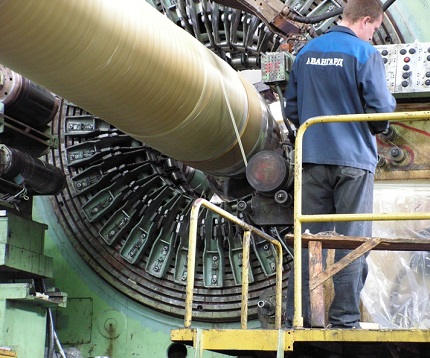
Charakterystyka metody:
- Jest stosowany głównie przy tworzeniu rur o przekroju do 75 mm;
- istnieje możliwość naprężenia gwintów osiowych, dzięki czemu uzyskuje się wytrzymałość, jak w metodzie spiralnej.
Wzdłużna technologia poprzeczna jest bardzo wydajna. Maszyny pozwalają zmieniać stosunek zbrojenia osiowego i pierścieniowego w szerokim zakresie.
Technologia ukośna wzdłużna
Rozwój inżynierów w Charkowie jest poszukiwany przez krajowych producentów. Podczas nawijania poprzecznego układarka wyświetla „zasłonę” składającą się z wiązki nici wiążących. Taśma jest podawana do ramy pod niewielkim kątem nakładania się z poprzednim wzmocnieniem pierścieniowym.
Po zakończeniu przetwarzania całego trzpienia włókna są zwijane za pomocą wałków - resztki polimerów wiążących są usuwane, powłoka wzmacniająca jest zagęszczana.
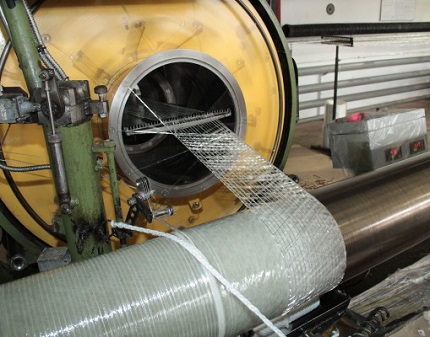
Cechy walcowania między warstwami:
- szczelność z włókna szklanego;
- nieograniczona średnica produkowanych rur;
- wysokie właściwości dielektryczne z powodu braku ciągłego zbrojenia wzdłuż osi.
Moduł sprężystości włókna szklanego „warstwowego” jest gorszy od podobnego parametru innych technik. Ze względu na ryzyko pęknięć międzywarstwowych metoda ta nie jest wykonalna przy tworzeniu rurociągów pod wysokim ciśnieniem.
Parametry wyboru rur z włókna szklanego
Wybór szklanych rur kompozytowych opiera się na następujących kryteriach: sztywność i ciśnienie obliczeniowe, rodzaj elementu wiążącego, cechy konstrukcyjne ścian i metoda połączenia. Istotne parametry są wskazane w dołączonych dokumentach i na każdej tubie - skrócone oznaczenie.
Sztywność i ciśnienie
Sztywność z włókna szklanego określa zdolność materiału do wytrzymania obciążeń zewnętrznych (ciężkość gleby, ruch drogowy) i nacisku na ściany od wewnątrz.Zgodnie z normą ISO złączki rurowe są sklasyfikowane w kilku klasach sztywności (SN).
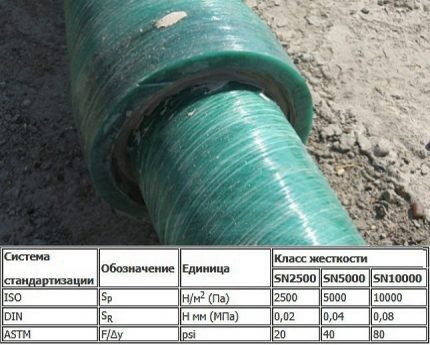
Stopień sztywności wzrasta wraz ze wzrostem grubości ścianki rury z włókna szklanego.
Klasyfikacja według ciśnienia nominalnego (PN) odzwierciedla gradację produktów w odniesieniu do bezpiecznego ciśnienia płynu w temperaturze +20 ° C przez cały okres użytkowania (około 50 lat). Jednostką miary dla PN jest MPa.
Niektórzy producenci, na przykład Hobas, wskazują ułamkową charakterystykę dwóch parametrów (ciśnienia i sztywności). Rury o ciśnieniu roboczym 0,4 MPa (klasa PN - 4) o stopniu sztywności (SN) 2500 Pa będą oznaczone - 4/2500.
Rodzaj spoiwa
Właściwości operacyjne rury w dużej mierze zależą od rodzaju spoiwa. W większości przypadków stosuje się dodatki poliestrowe lub epoksydowe.
Cechy spoiw PEF
Ściany są wykonane z termoutwardzalnych żywic poliestrowych wzmocnionych włóknem szklanym i dodatkami do piasku.
Zastosowane polimery mają ważne cechy:
- niska toksyczność;
- utwardzanie w temperaturze pokojowej;
- niezawodne połączenie z włóknami szklanymi;
- obojętność chemiczna.
Rury kompozytowe z polimerami PEF nie podlegają korozji ani agresywnym mediom.
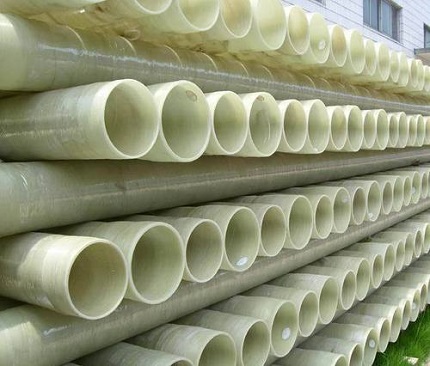
Charakterystyka epoksydowa
Spoiwo nadaje materiałowi większą wytrzymałość. Granica temperaturowa kompozytów z epoksydami wynosi do +130 ° С, a maksymalne ciśnienie wynosi 240 atmosfer.
Dodatkową zaletą jest prawie zerowa przewodność cieplna, więc zmontowany bagażnik nie wymaga dodatkowej izolacji termicznej.
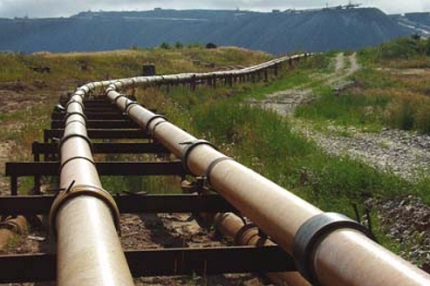
Projektowanie ścian z rur kompozytowych
Zgodnie z projektem wyróżniają: jedno-, dwu- i trójwarstwowe rury z włókna szklanego.
Charakterystyka produktów jednowarstwowych
Rury nie mają powłoki ochronnej, dzięki czemu są tanie. Cechy złączek rurowych: brak możliwości zastosowania w regionach o trudnym terenie i trudnym klimacie.
Ponadto produkty te wymagają starannej instalacji - kopania dużej objętości wykopu, układania piaszczystej „poduszki”. Jednak szacunek prac instalacyjnych rośnie z tego powodu.
Cechy rur dwuwarstwowych
Produkty wewnątrz wyłożone są powłoką filmową - polietylen wysokociśnieniowy. Zabezpieczenie zwiększa odporność chemiczną i poprawia szczelność linii pod obciążeniami zewnętrznymi.
Jednak działanie armatury w rurociągach naftowych ujawniło słabości modyfikacji dwuwarstwowych:
- brak przyczepności między warstwą strukturalną a podszewką - naruszenie solidności ścian;
- pogorszenie elastyczności folii ochronnej w temperaturach ujemnych.
Podczas transportu medium zawierającego gaz podszewka może się rozwarstwić.
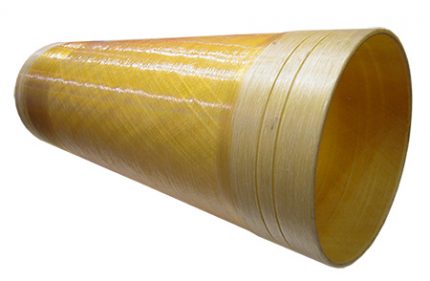
Parametry rury trójwarstwowej
Struktura rur z włókna szklanego:
- Zewnętrzna warstwa polimerowa (grubość 1-3 mm) - wzrost odporności mechanicznej i chemicznej.
- Warstwa strukturalna - warstwa strukturalna odpowiedzialna za wytrzymałość produktu.
- Wkładka (grubość 3-6 mm) - wewnętrzna powłoka z włókna szklanego.
Wewnętrzna warstwa zapewnia gładkość, szczelność i wyrównuje cykliczne wahania ciśnienia wewnętrznego.
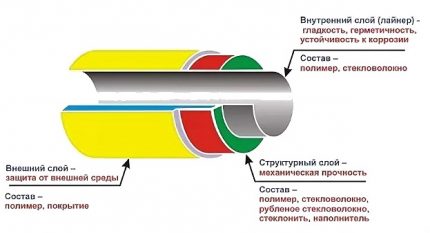
Metoda dokowania z włókna szklanego
Zgodnie z metodą połączenia asortyment złączek rurowych wykonanych z kompozytu dzieli się na 4 grupy.
Grupa nr 1 - dokowanie z kolcami
Elastyczne gumowe uszczelki są montowane w rowkach współpracujących na kolcach na końcu rury. Pierścienie podporowe są formowane na urządzeniach z elektronicznym sterowaniem, zapewniającym dokładność ich położenia i wielkości.
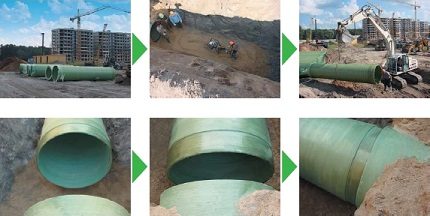
Grupa nr 2 - kolec nasadowy z uszczelką i korkiem
Podczas aranżacji autostrady lądowej należy zrekompensować wpływ sił osiowych na rurociąg. W tym celu oprócz pieczęci umieszczany jest ogranicznik. Element wykonany jest z metalowego kabla, polichlorku winylu lub poliamidu.
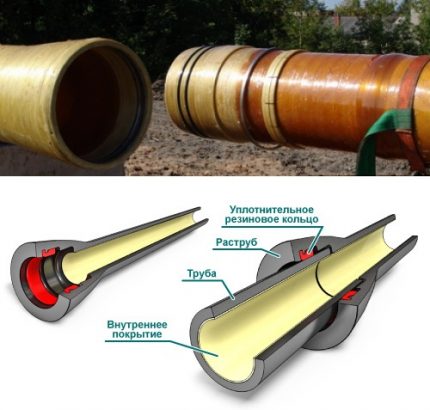
Grupa nr 3 - połączenie kołnierzowe
Dokowanie złożonego rurociągu z armaturą lub metalowymi rurami. Wymiary łączące kołnierzy z włókna szklanego są regulowane GOST 12815-80.
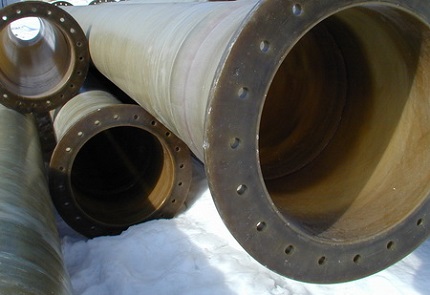
Grupa nr 4 - utrwalanie za pomocą kleju
Nieodłączna metoda łączenia - na końcówki nakładana jest kompozycja zbrojonych materiałów szklanych z dodatkiem poliestrowego składnika „zimnego” utwardzania. Metoda zapewnia wytrzymałość i szczelność linii.
Oznaczenie ochronnej warstwy wewnętrznej
Metodologia produkcji produktów rurowych pozwala wytwarzać produkty o różnym składzie warstwy wewnętrznej, co determinuje odporność linii na transportowane medium.
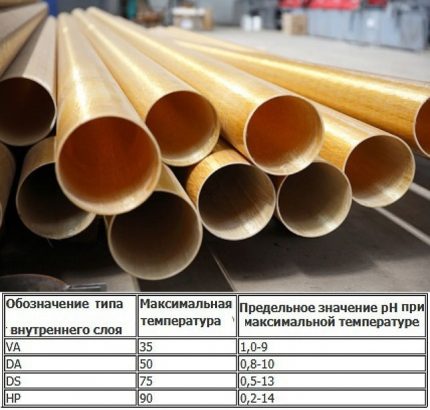
Krajowi producenci stosują następujące oznaczenia powłok ochronnych.
Litera wskazuje dopuszczalne użycie:
- A - transport cieczy z materiałami ściernymi;
- P. - dostarczanie i odprowadzanie zimnej wody, w tym picie;
- X - dopuszczalne użycie w agresywnych chemicznie środowiskach gazu i cieczy;
- G. - systemy zaopatrzenia w ciepłą wodę (limit 75 ° C);
- Z - inne płyny, w tym o wysokiej kwasowości.
Powłokę ochronną nakłada się warstwą do 3 mm.
Przegląd produktów wiodących producentów
Wśród różnorodności prezentowanych produktów znajdują się renomowane marki o wieloletniej pozytywnej reputacji. Należą do nich produkty firm: Hobas (Szwajcaria), Steklokompozit (Rosja), Amiantit (koncern z Arabii Saudyjskiej z zakładami produkcyjnymi w Niemczech, Hiszpanii, Polsce), Ameron International (USA).
Młodzi i obiecujący producenci rur kompozytowych z włókna szklanego: Polyek (Rosja), Arpipe (Rosja) i Fabryka Włókna Szklanego (Rosja).
Producent nr 1 - marka HOBAS
Fabryki marek znajdują się w USA i wielu krajach europejskich. Produkty Hobas zyskały światowe uznanie za ich doskonałą jakość. Rury GRT ze spoiwem poliestrowym są wykonywane techniką odlewania odśrodkowego z włókna szklanego i nienasyconych żywic poliestrowych.
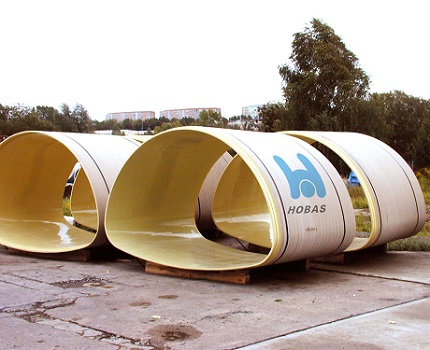
Charakterystyka rur kompozytowych Hobas:
- średnica - 150–2900 mm;
- Klasa sztywności SN - 630-10 000;
- Poziom ciśnienia PN - 1-25 (PN1 - rurociąg bezciśnieniowy);
- obecność wewnętrznej powłoki antykorozyjnej podszewki;
- odporność na kwasy w szerokim zakresie pH.
Rozpoczęto produkcję kształtek: kolanek, adapterów, rur kołnierzowych i trójników.
Producent # 2 - firma Steklokompozit
Firma „Steklokompozit” ustanowiła linię do produkcji rur z włókna szklanego Flowtech, technologia produkcji - ciągłe nawijanie.
Zaangażowany sprzęt z podwójnym zapasem substancji żywicznych. Do układania warstwy wewnętrznej stosuje się żywice high-tech, a na warstwę strukturalną nakłada się tańszą kompozycję. Technika ta pozwala zracjonalizować zużycie materiału i obniżyć koszty produkcji.
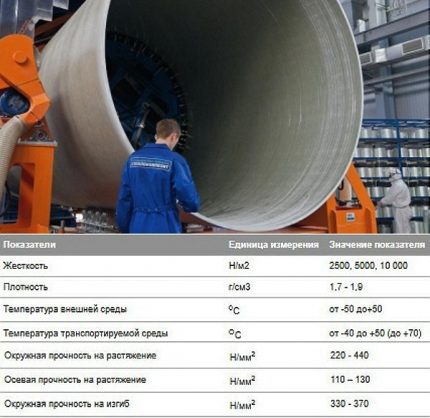
Producent # 3 - marka Amiantit
Głównymi składnikami rur Flowtite firmy Amiantit są włókno szklane, żywica poliestrowa, piasek. Stosowaną techniką jest ciągłe nawijanie, zapewniające utworzenie wielowarstwowego rurociągu.
Struktura włókna szklanego obejmuje sześć warstw:
- zewnętrzne uzwojenie taśmy włókninowej;
- warstwa energetyczna - posiekane włókno szklane + żywica;
- warstwa środkowa - włókno szklane + piasek + żywica poliestrowa;
- powtarzająca się warstwa mocy;
- podszewka nici szklanych i żywicy;
- włókninowa powłoka ochronna z włókna szklanego.
Badania wykazały wysoką odporność na ścieranie - dla 100 tysięcy cykli żwiru utrata powłoki ochronnej wyniosła 0,34 mm.
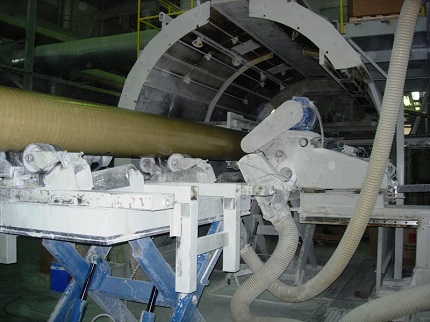
Producent # 4 - Polyec
Polyek LLC dokonuje różnych modyfikacji produktów z rur szklanych Fpipes. Technika produkcji (ciągłe ukośne uzwojenie wzdłużno-poprzeczne) umożliwia tworzenie rur trójwarstwowych o średnicy do 130 cm.
Polimerowe materiały kompozytowe biorą udział w tworzeniu rur osłonowych, połączeń kolumn podnoszących wodę, rurociągów wodociągowych i systemów grzewczych.
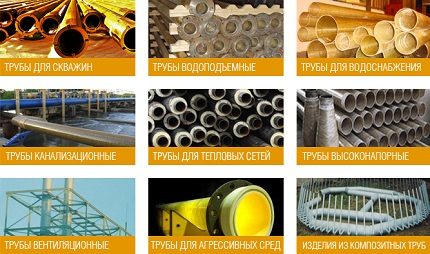
Oprócz rur z włókna szklanego rynek oferuje wiele produktów z innych materiałów - stali, miedzi, polipropylenu, plastiku, polietylenu itp. Które ze względu na bardziej przystępną cenę są aktywnie wykorzystywane w różnych obszarach codziennego użytku - w instalacjach grzewczych, wodociągowych, kanalizacyjnych, wentylacyjnych i innych.
Możesz zapoznać się z charakterystyką rur z różnych materiałów w naszych następujących artykułach:
- Rury z tworzyw sztucznych: rodzaje, specyfikacje, funkcje instalacyjne
- Rury i kształtki z polipropylenu: rodzaje produktów PP do montażu rurociągów i metody połączeń
- Rury wentylacyjne z tworzywa sztucznego do okapów: rodzaje, ich charakterystyka, zastosowanie
- Rury i kształtki miedziane: rodzaje, oznakowanie, cechy rozmieszczenia rurociągu miedzianego
- Rury stalowe: rodzaje, asortyment, przegląd cech technicznych i niuanse montażowe
Wnioski i przydatne wideo na ten temat
Technologia produkcji i możliwość zastosowania rur z włókna szklanego:
Porównanie technik ciągłego i okresowego nawijania:
W prywatnych mieszkaniach rury z włókna szklanego są używane dość rzadko. Głównym powodem jest wysoki koszt w porównaniu do plastikowych odpowiedników. Jednak w sferze przemysłowej doceniono jakość kompozytu, a zużyte metalowe linie do włókna szklanego są masowo wymieniane.
Czy masz pytania po przeczytaniu naszego artykułu? Zapytaj ich w bloku komentarzy - nasi eksperci postarają się udzielić wyczerpującej odpowiedzi.
A może chcesz uzupełnić prezentowany materiał o odpowiednie dane lub przykłady z własnego doświadczenia? Napisz swoją opinię pod tym artykułem.
Kiedyś nie wybrałem odpowiednich rur z włókna szklanego do zaopatrzenia w wodę i problemów, oczywiście, że wiele mi przyniosły. Z jakiegoś powodu narzekali na cząstki w wodzie, ale ciągle płynęli.