Check valve for a pumping station: what is needed and how is it installed
When arranging an autonomous water supply system, it is necessary to carefully select not only the pump, but also a variety of protective pipe fittings. Among the important devices, one of the significant places is occupied by the check valve for the pumping station, which helps to maintain a stable pressure in the hydraulic system.
It prevents premature wear of pumping equipment and prevents malfunctions.
The content of the article:
Types and purpose of back-stop valves
The dimensions of the check valve are small, but without this trifle, the pressure in the plumbing system support will be impossible. It belongs to the category of pipe fittings, whose main task is to prevent the reversal of the flow of water in the pipes of the water supply system.
Household pumping equipment is not designed for its movement in an abnormal direction.
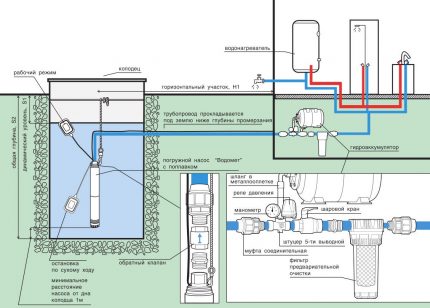
There is a market pumping station models, in the packaging of which manufacturers lay the presence of a check valve. These options include a suction hose with a non-return valve. But in most cases, this armature has to be purchased independently.
Similar gates are placed both on the suction line and on the inlet to the domestic water supply system immediately after the pump with a hydraulic accumulator or in front of the pump station.
Depending on the installation location in the scheme of the water supply system, non-return valves are divided into:
- Bottom line. Prevent the reverse movement of the water raised from the source when turning off the pumping equipment. They create conditions for the operation of the unit without constant filling with water before starting it and the suction line.
- Piping. Among them axial and folding varieties. Prevent a drop in the working pressure in the system.
If there is no non-return valve at the end of the suction pipe of the pumping station, then when the pump stops, water will begin to flow back by gravity. As a result, air congestion will form in the mains; in the conditions of a “dry run”, seals will break. As a result, water will penetrate the electric pump and cause it to burn out.
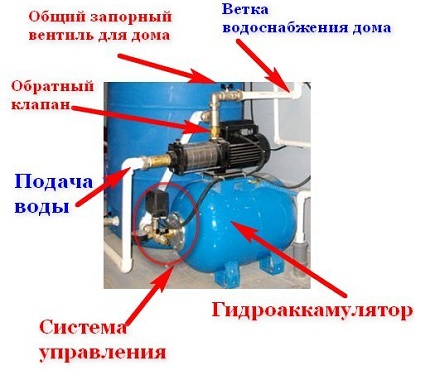
Most modern pumps are protected against such processes. But the water for starting in them will have to be poured after each stop of the unit.
In some models of pumps, it is possible to reverse the impeller at all, which may lead to its failure. The installation of this valve on the line of fluid intake from the source is mandatory, otherwise no electronic protection will help the water unit.
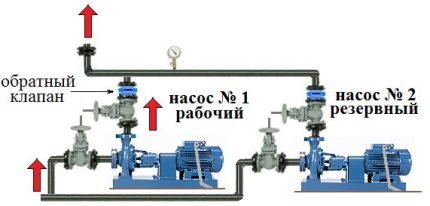
With a non-return valve, the situation is somewhat different. Here he protects not the pump, but the water distribution system inside the house. By locking water in the pipes, preventing it from returning back to the accumulator, a back-lock helps maintain the required value in the system working pressure. Without it, water will tend back into the storage tank, forcing it to work in an emergency mode.
Check valves increase the efficiency and reliability of the pump station, while protecting the pump, plumbing and plumbing system from water hammer. In general - an indispensable device. But it takes a lot of effort to open the shutter to the water, which reduces the flow pressure after passing through it by 0.1–0.3 atm.
Bottom check valve
Bottom types of check valves are installed at the inlet of the water pumping line. They are used to equip surface pumping systems to protect against pressure drop.
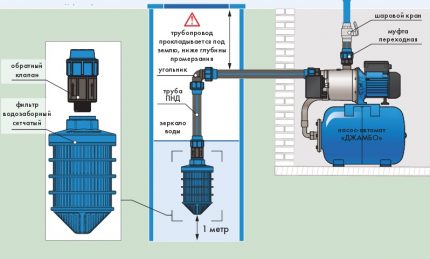
By design specifics bottom check valves are subdivided into:
- Spring loaded. Their working locking mechanism consists of a spring and a disk, which, when the spring is reduced under the pressure of the water, moves along the body of the device and passes the stream.
- Casement. The main organ is one or two transverse valves that open under the pressure of the pumped water and return to their places when it stops.
According to the method of fastening to the end of the suction hose or pipe, the bottom valves are divided into sleeve and flange. In tandem with household pumping units, the coupling type is most often used.
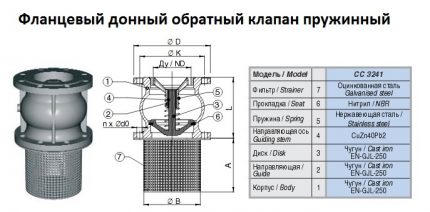
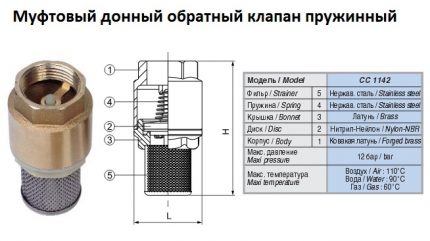
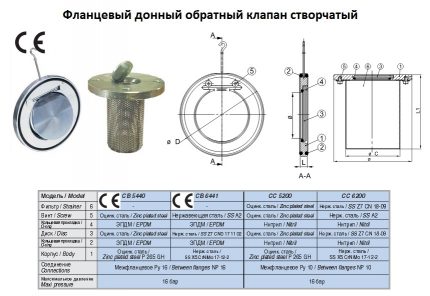
A strainer is recommended in front of the bottom check valve. He must exclude the penetration into the pumping system of biological contaminants and particulate matter with an abrasive effect.
The device must be installed in the direction indicated by the arrow on the housing. The distance from the bottom of the water intake to the check valve should be at least 0.5 - 1.0 m, depending on the class of the unit and the manufacturer's recommendations. Between the water mirror in the well or well and the valve, there must be a water thickness of at least 0.3 m.
Pumping systems with submersible pump equipped with a check valve without filter, as they are equipped with built-in cleaning devices to protect the functional "filling" from friction. The check valve in this case is installed in front of the supply pipe immediately after the pump unit. Used to prevent pressure drop in the network.
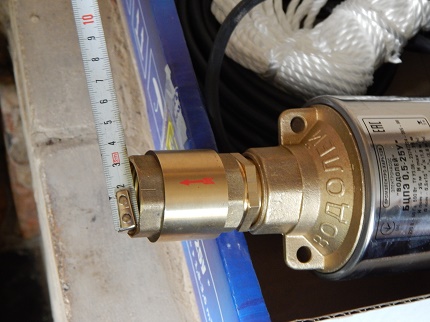
Pressure Support Check Valve
There are several designs of non-return valves for pipelines with a general principle of operation. All of them must provide unidirectional movement of the working fluid, for which they have a locking mechanism inside. It opens in the direction of flow, without obstructing it, and when you try to reverse the flow of water, it immediately closes.
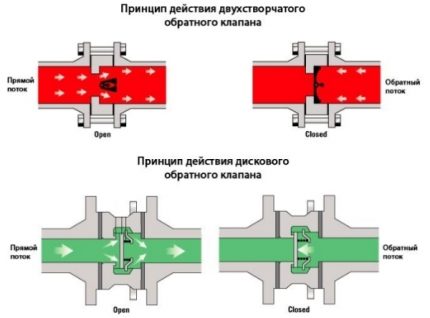
A conventional check valve consists of:
- housing;
- locking regulatory element (working body);
- springs (in some models it is absent).
The energy of the pressure of the water flowing in the forward direction squeezes the locking element from the seat, thereby creating a working window for the unhindered movement of the liquid. And when the current is reversed, this shutter returns to its original position under the action of a spring and water pressure, blocking the pipeline.
Products of this type of pipe fittings are structurally different, used for stamping materials, as well as the method of fastening to pipes. At the same time, almost all types of check valves can be used when installing pumping stations, but this is not always practical and expedient.
Constructive varieties of products
The locking element can move in parallel, perpendicularly and at an angle to the axis of the pipeline. Most often, with dry pipes, it lowers into the saddle under its own weight. The device provides normal pressure in the water supply, preventing the return current supplied to the water intake.
Therefore, when installing individual models of non-return valves, it is necessary to monitor not only the arrow of the direction of flow, but also the correct location of the cover, where the guide for the moving locking part is located.
Internal constipation in the check valve can be made in the form of:
- a spool consisting of a stem and locking plates;
- whole or divided into two wings;
- ball with a spring mechanism and gaskets.
In valves with a diameter of more than 400 mm, when the disc returns to the seat, it hits the body quite strongly, which inevitably leads to breakage of the device. To avoid premature wear of valves, these valves are equipped with hydraulic dampers, which make the drive stroke smooth.
However, such shock-proof check valves are not used in everyday life. There are simpler and cheaper analogues on sale.
If the check valve is needed in a small size, then the model should choose either a ball valve or a two-leaf one. In the first case, a small ball moves inside and back with the movement of water, and in the second case, the pipe is shut off due to two halves of the disk fixed to one rod. The case of both products is small due to the lack of a moving spool inside with a wide spacing.
There are also non-return type constructions with forced opening / closing of the shutter. Flow control in this case is carried out by mechanical or manual devices. However, such back-stop valves in everyday life with pumping stations are not used. It is simply not needed for pumps.
Classification by type of mounting
In addition to structural differences in the operating element, check valves used for installations with pumping stationsdiffer in the method of attachment. The choice here depends on the material of the pipelines and the technology of their connection.
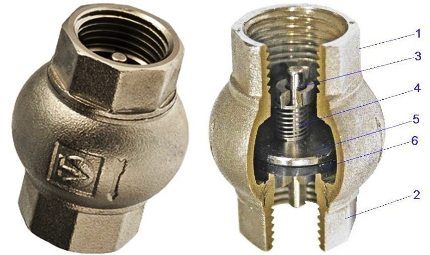
According to the method of connection with pipes, non-return valves are divided into:
- Coupling.
- Flanged.
- Wafer.
- Fatty (for welding).
The first variety is connected to pipelines by means of a threaded transition, and the second is connected thanks to flanges with gaskets. Wafer type check valves do not have their own fasteners at all, they are fixed between the flanges of other water supply elements using long studs.
The welding option is more suitable for use in pipelines through which aggressive media are pumped. With pumping stations they are not mounted. Wafer type check valves are available only in disc or double leaf design.
For water supply systems most often, non-return valves with a spring-loaded locking mechanism and a coupling connection are selected. They are easier to mount and dismantle, as well as repair by replacing the spring, which is the weakest link in this pipe fitting.
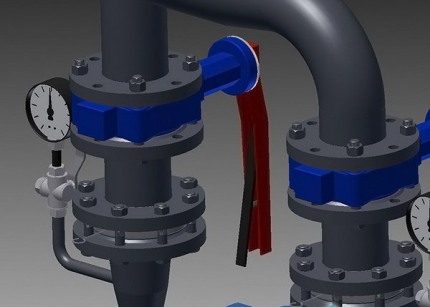
Material variation
The check valve body can be:
- bronze;
- brass;
- cast iron;
- stainless steel;
- plastic.
The most durable models are stainless steel, they are least susceptible to corrosion processes. From cast iron, non-return valves turn out to be bulky, so in everyday life they can rarely be found. They are mainly used on pipes with a large cross section. Such pipes are not connected to domestic pumping stations.
The most popular products are made of brass. This metal is relatively cheap, does not rust and is optimally suited to all types of pipes. Plastic products should be taken only for low-pressure pipelines and polypropylene pipelines.
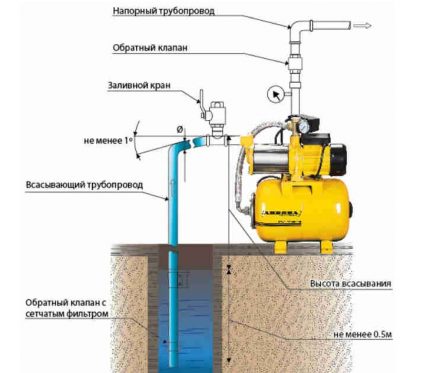
The working locking element is made of:
- stainless steel;
- aluminum;
- plastics.
In principle, all of these materials are equally good. The locking parts are small in size and are always made of high strength and durable. Failures most often occur in the spring mechanism. Therefore, the springs in the vast majority of models come from stainless steel, which is famous for its anti-corrosion characteristics and reliability.
In the stores you can also find combined check valves, the cases and covers of which are made of different materials. Each manufacturer seeks to reduce the cost of their products and offer the market some kind of novelty. Fortunately, all fittings are tested, it is only necessary to require a certificate of compliance with relevant norms and standards.
To achieve a shutter tightness when lowering it into the saddle, rubber, plastic, and hard metal alloy surfacings are used in various combinations.
Installation of valves with pump station
When choosing a non-return valve, it is necessary to take into account its nominal pressure, throughput and bore diameter. All these data are contained in the technical passport.
Installation can be done independently, following the instructions for the pumping station. In it, the manufacturer must indicate the recommended places for installing all the necessary fittings.
Installation option OK on a submersible centrifugal pump:
The main thing here is to find out the presence / absence of a check valve in the pump station unit. If it is already a regular element of the water supply installation, then this valve should not be additionally installed.
In this case, constipation will only reduce the capacity of the pipes, but there is no benefit from it. It is not worth spending money and time to install an unnecessary element, which will also create even small difficulties for the water flow.
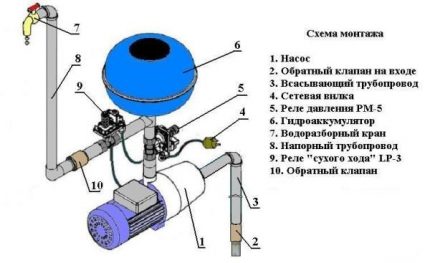
If the water supply system scheme suggests the possibility of emptying the pressure line or the pump is operating in reverse mode, then the upper check valve cannot be installed after the water pressure unit. He simply will not allow such actions, blocking the flow of water to the water unit.
The sequence of installation of the “valve + gate” combination depends on the technology of starting the pump. There are models that were originally designed to run on a closed gate valve. In these cases, the check valve must be installed after the shut-off valve.
Manufacturers recommend installing reverse constipation in the “lower” position in all cases together with mesh coarse filter. Water must first be cleaned of sand. The internal parts of the system will wear out faster from contact with abrasive particles.
It’s better to immediately take back constipation with a removable or non-removable mesh. It will protect the device from sand, with it you will not have to install an additional filter.
When choosing a mounting point for a non-return valve, consider:
- water flow direction;
- availability of fittings for subsequent repair and maintenance;
- restrictions on strict horizontal or vertical installation of certain types of backward constipation;
- the presence of sand in the water, which can lead to clogging.
Spring check valves with a lifting shut-off element are least affected. The quickest and easiest way to install pipe fittings with wafer type connection. But more often for water pipes in private houses, inexpensive analogues with flange or coupling fastening are selected.

When installing the check valve, it is important to install it correctly. The spool axis must be strictly vertical.And when installing a rotary product, the axis of rotation of the “flap” should always be higher than the center line of the water flow.
The direction of the flow of water and the correct location of the check valve allows the arrow on its body. It is difficult not to notice it, it is even more difficult to make a mistake with installing the locking device in the right position.
Conclusions and useful video on the topic
Video # 1. All about the technology of installing a check valve for water:
Video # 2. Overview of check valves for backflow blocking:
Video # 3. Which option of a non-return valve should be preferred for a cottage water supply system:
The use of check valves simplifies the operation of pumping stations and reduces the risk of accidents in the water supply system. Do not save on this small but important product.
Manufacturers now offer a mass of options for this valve of different sizes, the method of operation of the constipation and the type of fastening. For any water supply system and type of pump, it will be easy to find the optimal solution.
We will be glad to know your opinion. Those who want to clarify difficult technical points, share their experience or point out a material deficiency in the block below can leave comments.
The problem of the non-return valve is that when it fails, it starts to let water through. And keeping track of this is quite difficult. But you can. It is necessary to shut off water everywhere, and check the pressure level in the system if it slowly drops, that is, the probability that the non-return valve is out of order. It is inexpensive, and it makes sense to buy a completely metal one.
Very useful videos, without them, my father and I would have puzzled for a very long time over the installation of the check valve. In fact, it turned out that it is installed at times easier than we thought. Installed as shown in the video, everything works without unnecessary problems. Now you can not be afraid of unplanned equipment breakdown, since the valve will not allow water to go back to the excavation when pumping is stopped, and the filter will not allow grains of sand and debris accidentally falling into the wellbore to the working parts of the pump unit.
Remember, when installing the bottom OK on the external pump into the well, it eats up 2m of water. That is, if you have a 7m water mirror, then setting it so OK you will not be able to pump water. The pump simply does not raise 7 + 2 = 9m of water. Therefore, either deepen the caisson below 2m. Or use OK with adjustable lifting of the locking membrane (per cord).