How to build your own blades for a wind generator: examples of self-made blades for a wind turbine
The use of alternative energy sources is one of the main trends of our time. Clean and affordable wind energy can be converted to electricity even in your home if you build a windmill and connect it to a generator.
You can build blades for a wind generator with your own hands from ordinary materials, without using special equipment. We will tell you which shape of the blades is more effective, and help you choose the right drawing for a wind farm.
The content of the article:
How does a simple wind generator work?
A wind generator is a device that allows you to convert wind energy into electricity.
The principle of its operation lies in the fact that the wind rotates the blades, sets in motion a shaft along which the rotation enters the generator through a gearbox that increases speed.
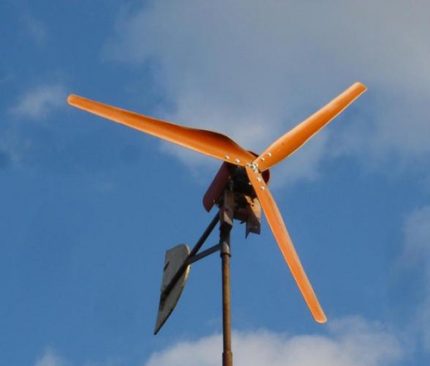
Two main types of wind generators are divided:
- veterinary;
- horizontal.
Vertically oriented models are built so that the propeller axis is perpendicular to the ground. Thus, any movement of air masses, regardless of direction, sets the structure in motion.
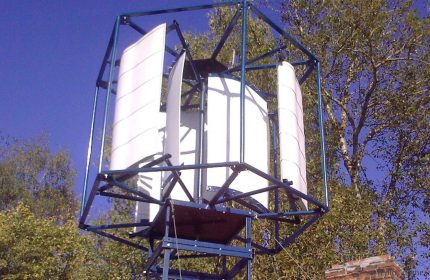
The horizontal wind generator resembles a weather vane. For the blades to rotate, the structure must be turned in the right direction, depending on the direction of air movement.
To control and capture changes in wind direction, special devices are installed.Efficiency with this arrangement of the screw is much higher than with a vertical orientation. In domestic use, it is more rational to use wind generators of this type.
Which blade shape is optimal?
One of the main elements of a wind generator is a set of blades.
There are a number of factors associated with these details that affect the efficiency of the windmill:
- weight;
- the size;
- the form;
- material;
- quantity.
If you decide to design blades for a makeshift windmill, be sure to consider all these parameters. Some believe that the more wings there are on the generator screw, the more wind energy can be obtained. In other words, the more the better.
However, this is not the case. Each individual part moves overcoming air resistance. Thus, a large number of blades on the screw requires more wind power to complete one revolution.
In addition, too many wide wings can cause the formation of the so-called “air cap” in front of the propeller, when the air flow does not pass through the wind turbine, but bends around it.
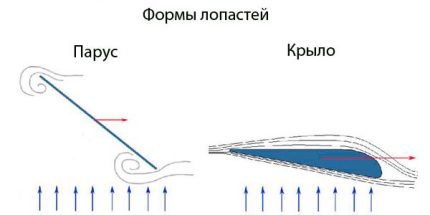
The most effective is a single-blade wind generator. But to build and balance it yourself is very difficult. The design is unreliable, albeit with a high efficiency. According to the experience of many users and manufacturers of windmills, the most optimal model is a three-blade.
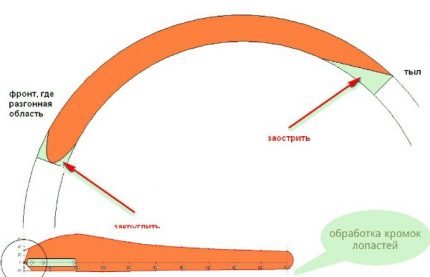
Properly selected blade shape for a wind generator is the foundation of its good work.
For home manufacturing, the following options are suitable:
- sailing type;
- wing type.
The blades of the sailing type are simple wide stripes, like in a windmill. This model is the most obvious and easy to manufacture. However, its efficiency is so small that this form is practically not used in modern wind generators. The efficiency in this case is about 10-12%.
A much more effective form is the wing profile blades. The principles of aerodynamics are involved here, which fly huge planes into the air. A screw of this shape is easier to set in motion and rotates faster. Air flow significantly reduces the resistance that a wind turbine encounters in its path.
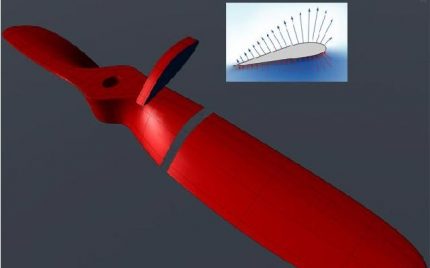
The efficiency of this model reaches a value of 30-35%. The good news is that you can build a wing blade with your own hands using a minimum of tools.All basic calculations and drawings can be easily adapted to your windmill and use free and clean wind energy without restrictions.
What are the blades made of at home?
The materials that are suitable for the construction of a wind generator are, first of all, plastic, light metals, wood and a modern solution - fiberglass. The main question is how much labor and time are you willing to spend on making a windmill.
PVC sewer pipes
The most popular and widespread material for the manufacture of plastic blades for a wind generator is an ordinary PVC sewer pipe. For most home generators with screw diameters up to 2 m, 160 mm pipes will suffice.
The advantages of this method include:
- low price;
- availability in any region;
- simplicity of work;
- a large number of diagrams and drawings on the Internet, a wide experience of use.
Pipes are different. This is known not only to those who make home-made wind power stations, but to everyone who has encountered the installation of a sewer or water supply system. They differ in thickness, composition, manufacturer. The pipe is inexpensive, so you do not need to try to further reduce the cost of your windmill, saving on PVC pipes.
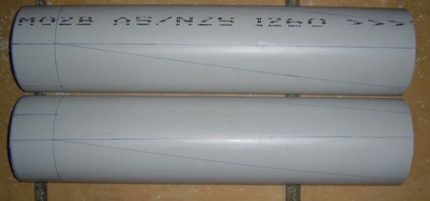
First you need to decide on the pattern. There are many options, each form has its advantages and disadvantages. Perhaps it makes sense to experiment first before cutting out the final version.
Since the price of the pipes is low, and you can find them in any hardware store, this material is perfect for the first steps in modeling the blades. If something goes wrong, you can always buy another pipe and try again, the wallet will not suffer much from such experiments.
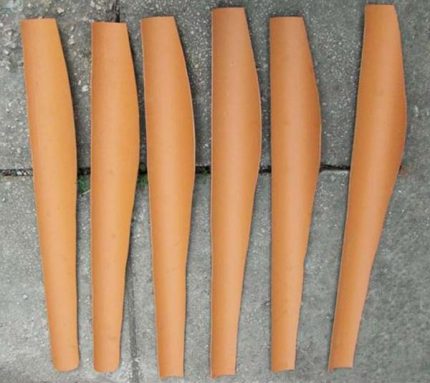
Amateur designers prefer PVC, since during the test, a broken blade can be replaced with a new one made in 15 minutes right on the spot with a suitable piece. Simple and fast, and most importantly - affordable.
Photo-instructions for the manufacture of blades of a windmill from polymer pipes will help to visually master the steps and the sequence of the process:
All preparatory steps have been completed, now the blades must be attached to the part rotating after the wind:
Aluminum - thin, light and expensive
Aluminum is a light and durable metal. It is traditionally used for the manufacture of blades for wind generators. Due to its light weight, if you give the plate the desired shape, the aerodynamic properties of the screw will be at a height.
The main loads that the windmill experiences during rotation are aimed at bending and breaking the blade. If plastic during such work quickly cracks and fails, you can count on an aluminum screw for much longer.
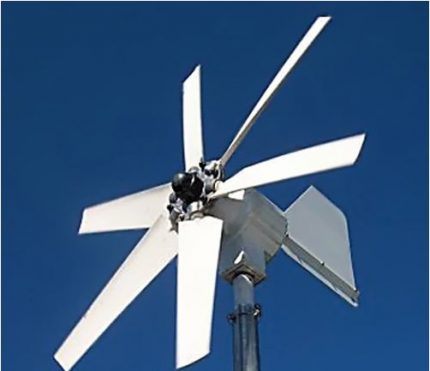
Another disadvantage of aluminum parts is the complexity of manufacturing. If the PVC pipe has a bend that will be used to impart the aerodynamic properties of the blade, then aluminum is usually taken in the form of a sheet.
After cutting the part according to the pattern, which in itself is much more complicated than working with plastic, the resulting workpiece will still need to be rolled and given to it the correct bend. At home and without a tool, this will not be so simple.
Instead of expensive aluminum, you can use scraps of roofing sheet or pieces of corrugated board remaining after installation:
Fiberglass or fiberglass - for professionals
If you decide to approach the issue of creating a blade consciously and are ready to spend a lot of effort and nerves on it, fiberglass will do. If you have not dealt with wind generators before, starting an acquaintance with modeling a fiberglass windmill is not a good idea. Still, this process requires experience and practical skills.
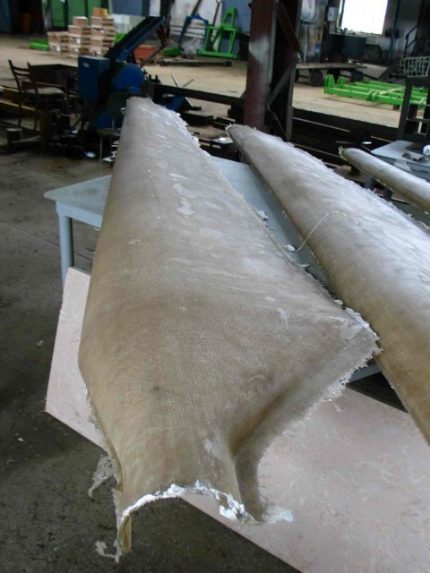
For the manufacture of fiberglass is taken - a thin and durable material that is produced in rolls. In addition to fiberglass, epoxy glue is useful for fixing layers.
Start by creating a matrix. This is such a workpiece, which is a form for a future part.
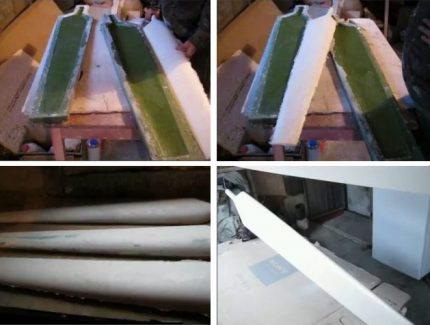
It is very difficult to make a blank on your own, you need to have a ready-made model of a blade made of wood or other material before your eyes, and only then a matrix for the part is cut out from this model. Such matrices need at least 2. But, having made a successful shape once, it can be used many times and thus built more than one windmill.
The bottom of the mold is thoroughly greased with wax. This is done so that the finished blade can be easily removed subsequently. Lay a layer of fiberglass, coat it with epoxy glue. The process is repeated several times until the workpiece reaches the desired thickness.
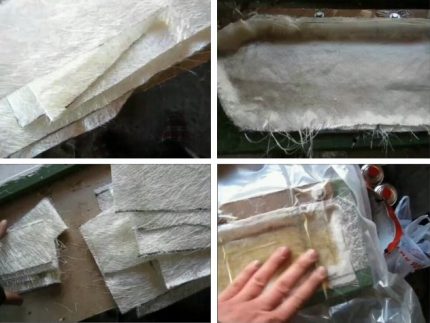
When the epoxy glue dries, half of the part is carefully removed from the matrix. Do the same with the second half. The parts are glued together to form a hollow volumetric part. A lightweight, durable, aerodynamically shaped fiberglass blade is the pinnacle of excellence for a home-lover of wind farms.
Its main disadvantage is the difficulty of implementing the idea and a large amount of marriage at first, until the ideal matrix is obtained, and the creation algorithm is not refined.
Cheap and cheerful: a wooden part for a wind wheel
A wooden blade is an old-fashioned method that is easy to implement but ineffective at today's level of electricity consumption. You can make a detail from a solid board of light wood, such as pine. It is important to choose a well-dried wooden blank.
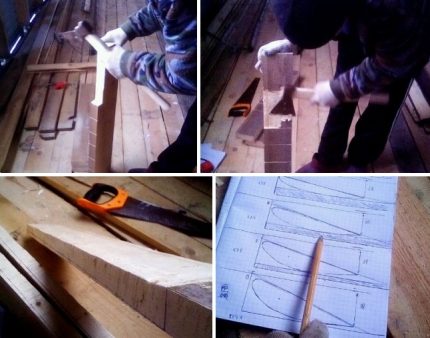
It is necessary to choose a suitable shape, but take into account the fact that the wooden blade will not be a thin plate, like aluminum or plastic, but a three-dimensional structure. Therefore, giving the workpiece a little shape, you need to understand the principles of aerodynamics and imagine the shape of the blade in all three dimensions.
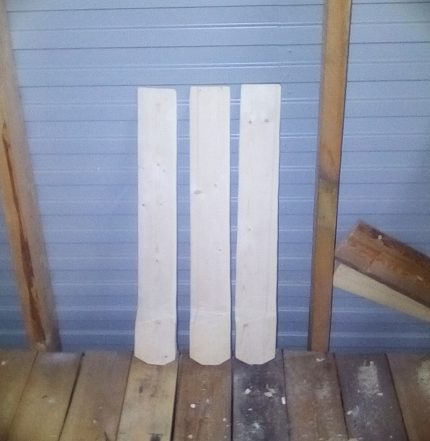
The main disadvantage of this design is the large weight of the screw. In order to budge this colossus, the wind must be strong enough, which is difficult in principle. However, wood is an accessible material. Boards suitable for creating a wind turbine screw can be found right in your yard without spending a dime. And this is the main advantage of wood in this case.
The efficiency of a wooden blade tends to zero. As a rule, the time and effort that goes into creating such a windmill is not worth the result, expressed in watts. However, as a training model or a trial copy, the wooden part is quite the place to be. And the weather vane with wooden blades looks spectacular on the site.
The following selection of photographs will introduce the steps of making a windmill with blades cut out of plywood:
The working part is ready and tested for operability, which means that it remains only to paint and fasten it to the mast:
Drawings and examples of blades
It is very difficult to make the correct calculation of the wind generator screw without knowing the main parameters that are displayed in the formula, as well as having no idea how these parameters affect the operation of the wind turbine.
It is better not to waste your time if there is no desire to delve into the basics of aerodynamics. Ready-made blueprints with preset indicators will help you choose the right blade for a wind farm.
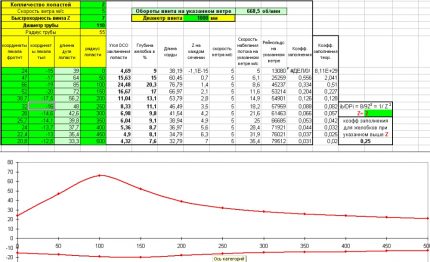
Such a small wind generator will not be able to provide you with high power. Most likely, you can hardly squeeze more than 50 watts out of this design. However, a two-bladed propeller made of light and thin PVC pipe will give a high rotation speed and ensure the operation of the windmill even with a small wind.
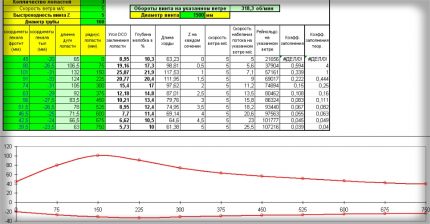
A three-blade propeller of this shape can be used for more powerful units, approximately 150 W at 12 V. The diameter of the entire propeller in this model reaches 1.5 m. The wind wheel will rotate quickly and easily start to move. Three-winged windmills are most common in home power plants.
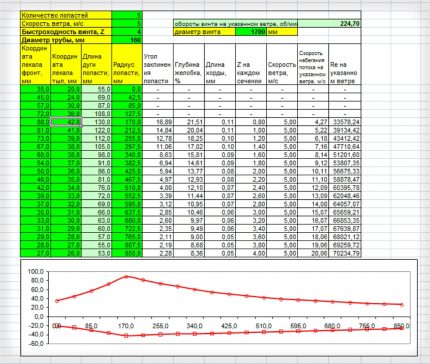
Such a five-blade propeller can produce up to 225 revolutions per minute at a design wind speed of 5 m / s. To build a blade according to the proposed drawings, you need to transfer the coordinates of each point from the columns "Front / Rear Pattern Coordinates" to the surface of the plastic sewer pipe.
According to the table below, you can calculate the diameter of the windmill with 2-16 blades. In this case, you can select the size taking into account the desired output power.
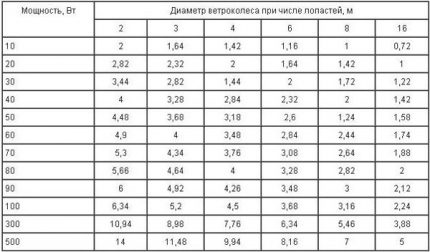
As practice shows, servicing a wind generator more than 2 meters in diameter is quite difficult. If, according to the table, you need a larger windmill, consider increasing the number of blades.
With rules and principles calculating a wind generator Introduces the article, which step by step outlines the process of computing.
Performing Wind Turbine Balancing
Balancing the blades of a wind generator will help make its operation as efficient as possible. To balance, you need to find a room where there is no wind or draft. Of course, for a wind wheel more than 2 m in diameter, it will be difficult to find such a room.
The blades are assembled into a finished structure and installed in working position. The axis should be located strictly horizontally, in level. The plane in which the screw will rotate must be set strictly vertically, perpendicular to the axis and ground level.
The screw, which does not move, must be rotated 360 / x degrees, where x = the number of blades. Ideally, a balanced windmill will not deviate by 1 degree, but will remain motionless. If the blade turned under its own weight, it needs to be slightly corrected, reduce weight on one side, eliminate deviation from the axis.
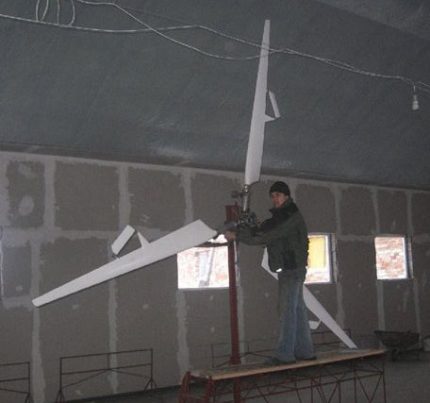
It is also important to ensure that all parts rotate strictly in the same plane.To check at a distance of 2 mm on both sides of one of the blades set the control plate. During movement, no part of the screw should touch the plate.
To operate a wind generator with manufactured blades, it will be necessary to assemble a system that accumulates the received energy, conserves it and transfers it to the consumer. One of the components of the system is the controller. How to do windmill controller, you’ll find out by reading our recommended article.
Conclusions and useful video on the topic
To build a windmill with your own hands from improvised materials is quite possible. If you start with simpler models, then the first attempt is likely to be successful. With experience, take on more complex ideas to get the most efficient and powerful wind generator.
Video # 1. How to make a windmill from PVC pipes:
Video # 2. DIY wind generator:
Video # 3. Galvanized steel windmill:
If you want to use clean and safe wind energy for household needs and do not plan to spend a lot of money on the purchase of expensive equipment, homemade blades made of ordinary materials would be a good idea. Do not be afraid of experiments, and you will be able to further improve existing models of propellers of a windmill.
Do you want to tell how you personally made blades for a windmill, which provides electricity to the country? Would you like to share useful information with site visitors or ask a question? Please write comments in the block below.
I put a wind generator in my private house. For a long time I was looking for what blades to make better. As a result, I settled on PVC pipes. The tree seemed heavier and less efficient in generating electricity. And in this article, it looks like a wooden windmill is as a trial. Interested in the manufacture of fiberglass blades. I wonder if there is a big difference between the two in watts received?
If done independently, the blades of plastic water pipes are unrivaled. Lightweight, inexpensive material, in addition, the process of manufacturing a blade from it is very simple. Aluminum is stronger and more durable, but the high price is deterrent. Fiberglass is too complicated to manufacture. Wooden ones are heavy, although, in my opinion, adequate wooden blades can be made that will work normally. The main thing is that the tree is dry and without knots.
Which is better: three long blades or six short? Your opinion
That 3 short, that six short - does not matter. The main thing is the diameter of the covered surface. So there are three long ones. According to rough estimates, in order to get 1 kW with all losses (directly to the network, excluding the battery-inverter circuit) at a speed of 4 m / s, a diameter of 13 m is needed. The same diameter at a wind speed of 10 m / s already yields 17 kW. If all this is poured into the battery and then back, then somewhere else in half to the loss. Very much depends on wind speed. If the area is always almost calm - it makes no sense.