Gas filters: types, device, purpose and features of the choice of filter for gas
A necessary technical device for the gas distribution system is a gas filter - a device that performs the functions of elementary cleaning of the working environment from pollution. But how is it arranged and is it possible to do without it? This is what we will talk about in our publication - we will consider the design features of filters, their varieties.
We also give recommendations on the correct selection of a suitable option, based on the characteristics of operation. In addition to the material presented, we will pick up visual photos, diagrams and thematic videos.
The content of the article:
Design and features of the filter
Thanks to elements such as filters installed on the line, long-term operation of instrumentation, stop valves and other significant components is ensured. Therefore, equipping gas systems with filter elements is not just a desirable, but a prerequisite, given the technological features use of household gas.
Despite the apparent external simplicity of execution, gas filters are quite diverse in technical and operational terms. So, in practice, devices that structural performance conditionally should be divided into angular and linear.
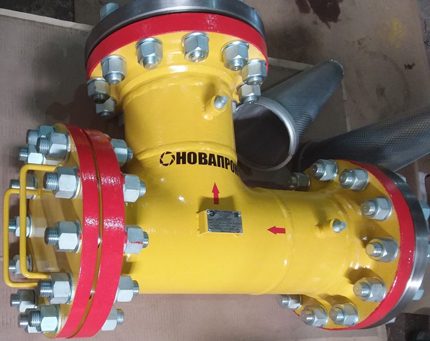
In addition, differences in the design of gas filters are also manifested in direction of travel gas flow through the device. Accordingly, there are two types of execution: direct-flow and turning.
Traditionally, the body part of gas filters is made of metals - cast iron, steel, aluminum, and here it is also necessary to consider the variety body designs.
Finally, gas filters are also separated by such a criterion as filtration material:
- reticulate;
- cassette.
For the first option is characteristic metal gridwoven from thin wire.
In the second case, usually we are talking about special printed cassetteswhere a thin kapron thread or horse hair is used. These materials are additionally soaked with special (viscin) oil.
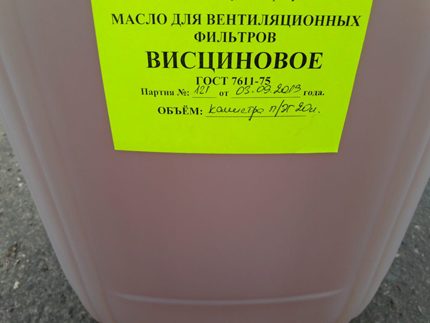
The filter material used in the design of gas filters must have the appropriate chemical and physical properties, provide physical resistance to the working environment. All these nuances are taken into account during development and design.
How is the gas filter inside?
Regardless of the variety of gas filters, almost all have a similar internal technological system, with the exception of some individual parts.
The picture below shows the diagrams of typical gas filters that are widely used in the operation of gas networks.
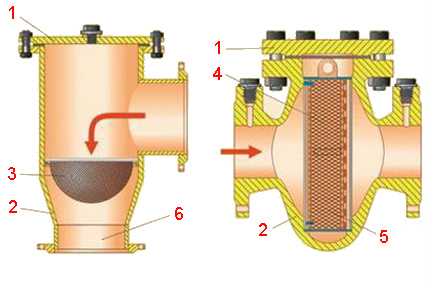
It should be noted some of the subtleties of the internal design. For example, metal strainers are inherent in the factor of increasing the degree of refinement of the cleaning due to the accumulation of clogging. At the same time, accordingly, the throughput of the filter element decreases. This effect is especially pronounced in multilayer structures.
In cassette systems where horse hair is used as a filter element, on the contrary, the degree of subtlety of cleaning weakens. This is due to the fact that the passing gas stream during operation of the device gradually carries away part of the filter material in the form of small particles.
Therefore, in order to reduce the amount of entrained particles and maintain effective filtration, they strive to select the optimal speed of the working medium during the operation of cassette filters.
Differential pressure and principle of operation
In general, the boundary permissible values of pressure drops when using gas filters should be 5,000 Pa (for mesh elements) and 10 000 Pa (for cartridge type elements).
Accordingly, at the time of the start of operation of any type of gas filter, these parameters must correspond to the numbers:
- 2,000 - 2,500 Pa (for mesh type elements);
- 4,000 - 5,000 Pa (for cartridge type elements).
It is not difficult to describe the operation of the filter mesh mechanism: household gas passing through a piping system meets a filter on its way and passes into the device through an inlet pipe.
Penetrating through a metal grid, household gas is cleaned of foreign contents and then passes to the outlet pipe.

The debris trapped by the net falls into the lower area of the strainer housing (in some designs) or it is forcibly cleaned. During servicing, debris accumulated in the bottom area is removed through an opening, which remains closed by a plug at the time the filter is operated.
A slightly more sophisticated cartridge filter element works, taking into account the features of the material used. Inside the filter along the working medium there is a cassette filled with hair. Additionally, a bump stop is installed in front of it - a metal plate that protects the cartridge from damage by large foreign bodies of a rigid structure.
The device of this cartridge is simple - it is usually a rectangular (tubular) frame, the outer parts of which are closed by a wire mesh. The inner area of the frame is filled with filamentous nylon or natural (horsehair) material. When filling, a homogeneous material is densely packed and additional lubricant is added.
The gas passing through such a cassette is cleaned of foreign contents and enters the perforated metal grill. This is another component of the cassette filter that protects against entrainment of particles of filter material into the system.
As it becomes clogged, the cartridge is removed as part of the maintenance and cleaned / rinsed with special solvents.
Optimum differential pressure control
Almost all gas filter designs provide differential pressure control. Some designs (usually outdated) for such purposes are equipped with fittings, where the indicator is connected.
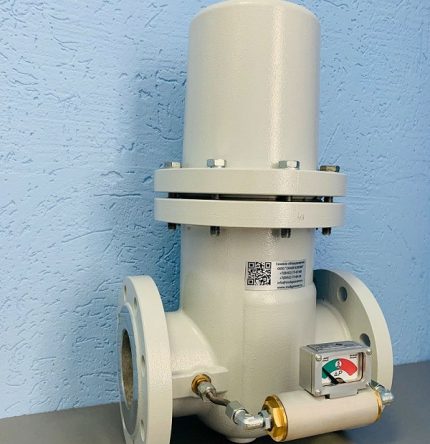
Other, more modern products are equipped with an indicator element directly. Such an element is built into the body of the device and is an information scale, usually divided by color zones (green and red). There are indicators with one and two pointers.
Option # 1 - a single pointer indicator
Under conditions of normal operation of the gas filter, the indicator pointer is in the green region, which clearly shows the optimal level of differential pressure.
If the arrow of the indicator moves to the area of the scale, painted in red, this factor indicates that the filter is clogged.
On such differential indicators, the primary attention of the personnel is given to the red segment of the scale and the corresponding indicator. When the red arrow is present in the region of the red segment, the filter is subject to preventative maintenance followed by cleaning or replacing the filter material.
Option # 2 - indicator with two arrows
For this embodiment, the control scale is divided into two segments, painted black and red. Pointing elements (arrows) also correspond to the colors of the segments.
The black area is used to control the pressure drop at the current time. The red color area is used to control the drop at times of maximum consumption.
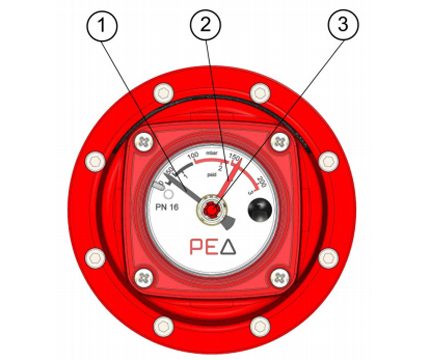
The features of such indicators are that if the pointer to the black segment of the scale has the ability to return to the origin, the pointer to the red segment is not endowed with this ability.
If the red pointer fixes an overestimated difference, the arrow (red) irrevocably stops at the reached mark. Returning to the zero mark is only possible manually during maintenance.
Features of choosing a filter for gas
When choosing a suitable gas filter, the following features should be considered:
- pipe diameterwhere installation is supposed;
- gas flow (calculated parameter);
- pressure - you need to know the value of the absolute pressure at the inlet of the filtering device;
- density - it is desirable to have data on the density of the gaseous medium.
Filtering devices of different manufacturers differ in appearance and characteristics. However, each product is marked accordingly. Marking allows you to choose a filter based on the main criteria.
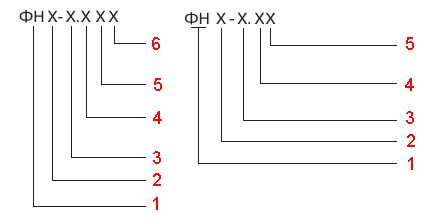
In order to comply with a sufficient degree of purification by the filter element, the selection usually takes into account the restriction of the flow rate of the medium passing through the filter device.
The speed parameter, as a rule, is determined by the parameter of the maximum allowable differential pressure. If the filter is in a clean state, then the differential is allowed at a level of not more than 50% of the maximum allowable value.
Usually, in order to accurately select a filter for a gas pipe, it is convenient to use special tables. If access to the tables is not possible or a unique selection is required, it is logical to use the calculation formula shown in the figure below.
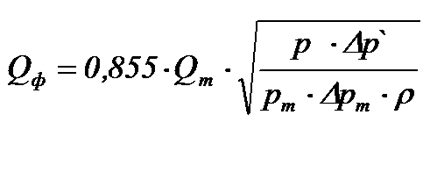
Traditionally, the choice of a gas filter is compared diameter the linear pipeline on which the device is supposed to be installed. At the same time, the throughput of the device is associated with the flow parameters at the gas distribution point - they are guided by a similar value or higher.
Conclusions and useful video on the topic
Video about gas filters, their features and the need for their use:
The operation of gas pipelines without the use of filters will be ineffective and impractical. Under such operating conditions, there is a risk of rapid failure of technological equipment, which affects the economic side of operating systems. Of course, the lack of filters affects the degree of safety of equipment.
Want to complement the above material with interesting facts? Or you still have questions about the topic of the article Ask them to our experts and other visitors to the site, write your comments and tips - the feedback block is located below.