DIY solar generator: instructions for making an alternative energy source
Alternative sources of energy, allowing to provide the premises with heat and electricity in the required amount - an expensive "pleasure", requiring significant financial costs for the acquisition, installation and installation.
Making a solar generator with your own hands is much cheaper and quite affordable for many home masters. Consider the instructions that describe all the nuances of the manufacturing process.
The content of the article:
- How does a solar power generator work?
- What do you need for work?
- Photo converter type selection
- How to make a frame for plates?
- Select transparent item
- Installation of silicon photocells
- How to test the mounted unit?
- The final stage of work
- Where and how to place the generator?
- Conclusions and useful video on the topic
How does a solar power generator work?
A solar generator is a complex of photoelectric semiconductor elements that directly convert sun energy into the electric.
The quanta produced by the rays of light when hit on a photographic plate knock an electron from the final atomic orbit of the working element. This effect creates a lot of free electrons, which form a continuous stream of electric current.
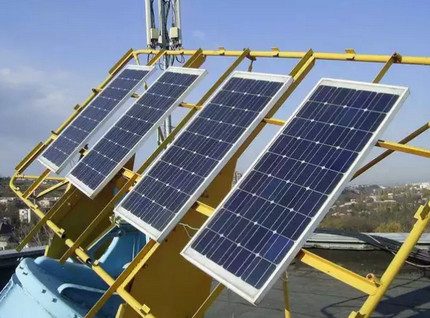
As the active material, silicon is used. It is highly efficient and provides a photoelectric conversion coefficient in the normal mode at the level of 20%, and under favorable conditions - up to 25%.
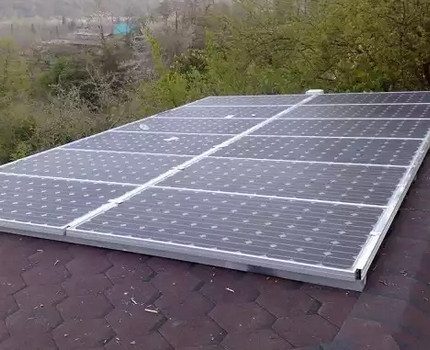
A thin coating of passive chemical elements such as boron or phosphorus is applied on one side of the silicon wafer.It is on this surface that as a result of intense exposure to sunlight, the active release of electrons occurs. Phosphorus film reliably holds them in one place and does not allow to fly apart.
On the working plate are metal "tracks". Free electrons are built on them, thus creating an ordered movement, that is, an electric current.
The minuses of the plates include only the complexity and cost of the process of cleaning silicon itself, and in order to avoid these problems, they are actively mastering the use of alternatives in the form of gallium, cadmium, indium and various copper compounds. However, silicon elements have no real competitors yet.
The easiest way to build a converter of solar energy into electricity is to buy a ready-made solar battery and install it on the roof of a house or garage:
What do you need for work?
For the manufacture of a generator consisting of a kit solar panels, tools and materials are required, such as:
- modules for converting sunlight into energy;
- aluminum corners;
- wooden slats;
- chipboard sheets;
- a transparent element (glass, plexiglass, plexiglass, polycarbonate) to create protection for silicon wafers;
- screws and screws of various sizes;
- dense foam rubber with a thickness of 1.5-2.5 mm;
- high-quality sealant;
- diodes, terminals and wires;
- a screwdriver or a set of screwdrivers;
- soldering iron;
- hacksaw for wood and metal (or grinder).
How much materials will be needed will directly depend on the planned size of the generator. Large-scale work will entail additional costs, but in any case it will be cheaper than the purchased module.
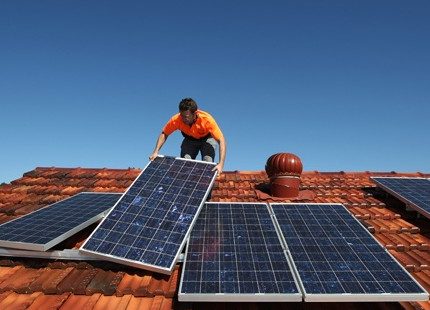
For the final testing of the assembled unit, an ammeter is used. It allows you to capture the actual efficiency of the installation and helps determine the actual return.
Photo converter type selection
Do-it-yourself activities to create a solar generator with a choice of the type of photovoltaic silicon converter.
These components are of three types:
- amorphous;
- monocrystalline;
- polycrystalline.
Each option has its advantages and disadvantages, and the choice in favor of any of them is made based on the amount of funds allocated for the purchase of all system components.
Features of amorphous varieties
Amorphous modules do not consist of crystalline silicon, but of its derivatives (silane or silicon hydrogen). By spraying in a vacuum, they are applied in the thinnest layer on high-quality metal foil, glass or plastic.
Finished products have a faded, blurry gray tint. Visible silicon crystals on the surface are not observed. Main advantage flexible solar panels reasonable price is considered, however, their efficiency is very small and ranges from 6-10%.
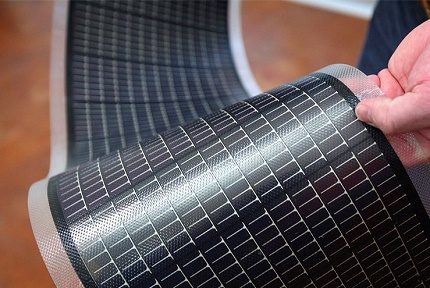
The specifics of polycrystalline types
Polycrystalline solar panels produced by the gradual very slow cooling of the silicon melt. The resulting products are distinguished by a rich blue color, have a surface with a pronounced pattern resembling a frosty pattern, and are effective in the region of 14-18%.
Higher efficiency-productivity is hindered by areas within the material that are separated from the general structure by granular boundaries.
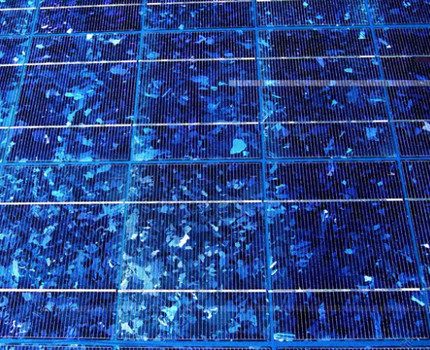
Characteristics of monocratillic options
Single crystal modules are characterized by a dense dark color and consist of solid silicon crystals. Their effectiveness exceeds the performance of other elements and amounts to 18-22% (under favorable conditions - up to 25%).
Another advantage is its impressive service life - according to manufacturers over 25 years. However, with prolonged use, the efficiency of single crystals decreases and after 10-12 years, the photographic efficiency is already no more than 13-17%.
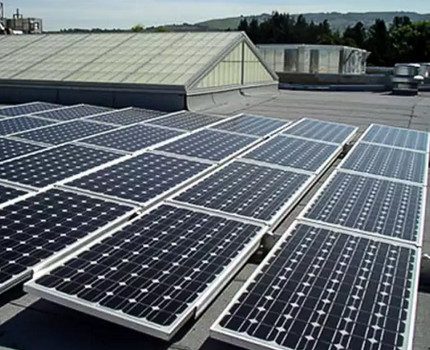
To create a solar generator at home, they mainly take poly- and single-crystal plates of various sizes with their own hands. They are purchased in popular online stores, including on eBay or Aliexpress.
Due to the fact that solar cells are valued quite highly, many suppliers offer customers products of group B, that is, fragments with a slight defect that are suitable for full operation. Their cost differs from the standard price by 40-60%, so that collecting a generator costs a reasonable price, which is not too affordable.
How to make a frame for plates?
For the manufacture of the frame of the future generator, durable wooden battens or aluminum corners are used. The wooden version is considered less practical, since the material requires additional processing to avoid subsequent decay and delamination.
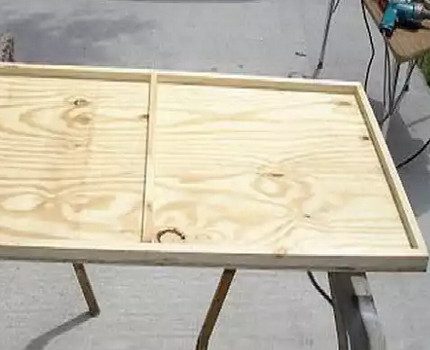
Aluminum has much more attractive physical characteristics and, due to its lightness, does not exert unnecessary load on the roof or other supporting structure where it is planned to install the unit.
In addition, due to the anti-corrosion coating, the metal does not rust, does not rot, does not absorb moisture and easily tolerates the effects of any aggressive atmospheric manifestations.
To create a frame structure from aluminum corners, the size of the future panel is first determined. In the standard version, 36 photocells with a size of 81 mm x 150 mm are used per block.
For correct subsequent operation, a small gap is left between the fragments (about 3-5 mm). This space allows you to take into account the change in the basic parameters of the base, exposed to atmospheric manifestations. As a result, the total size of the workpiece is 83 mm x 690 mm with a frame corner width of 35 mm.
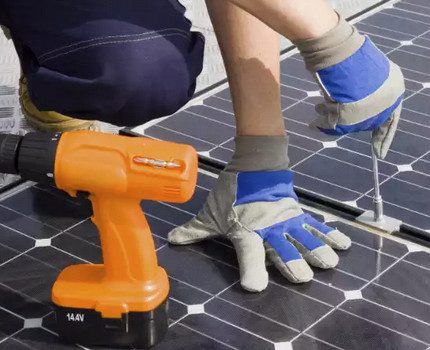
After sizing, the necessary fragments are cut out from the corners and, using fasteners, assemble them into frame frames. A layer of silicone sealant is applied to the inner surface of the structure, being very careful that there are no gaps or voids.
The integrity, strength and durability of the mounted structure depend on this. A protective transparent material is laid on top (glass with anti-reflective coating, plexiglass or polycarbonate with special parameters) and securely fastened with hardware (1 short and 2 long frame and 4 corners of the case).
For work using a screwdriver and screws of suitable diameter. At the end, the transparent surface is carefully cleaned of dust and small debris.
Select transparent item
The main criteria for choosing a transparent element to create a generator:
- ability to absorb infrared radiation;
- the level of refraction of sunlight.
The lower the refractive index, the higher the efficiency of silicon wafers. Plexiglass and Plexiglas have the lowest light reflectance. Polycarbonate also has far from the best performance.
To create frame structures for home solar systems, it is recommended to use anti-reflective transparent glass or a special type of polycarbonate with anti-condensation coating, which provides the necessary level of thermal protection, if possible.
The best characteristics in terms of absorption of infrared radiation are strong thermal absorbing plexiglass and glass with the option of infrared absorption. In plain glass, these figures are much lower. The efficiency of infrared absorption depends on whether silicon wafers are heated during operation or not.
If the heating turns out to be minimal, the photocells will last a long time and provide stable returns. Overheating of the plates will lead to interruptions in work and the rapid failure of individual fragments of the system or the entire complex.
Installation of silicon photocells
Immediately prior to installation, safety glasses placed in aluminum frames are well cleaned of dust and degreased with an alcohol-containing composition.
The purchased photocells are evenly placed on the marking substrate at a distance of 3-5 millimeters from each other and mark the angles of the overall structure. Then proceed to the soldering of the elements - the most important and time-consuming part of the assembly of the generator.
Soldering of the active elements of the generator is carried out according to the scheme in which “+” are the tracks on the outside, and “-” are the channels located on the inside of the plate.
To correctly connect the contacts, first apply a flux (acid for soldering) and solder, and then carry out the processing in a strict sequence from top to bottom. At the end, all the rows are interconnected.
The next step is the sizing of photocells. To do this, a little sealant is squeezed into the center of each silicon wafer, the formed chains of elements are turned upside down and placed in strict accordance with the markings applied earlier.
Gently press the plates with your hands, fixing them in the right place. They act very carefully, trying not to damage or bend the material.
The contacts of the photocells located at the edges are output to a separate bus (wide silver conductor) as “+” and “-”. Additionally, the complex is equipped with a blocking diode. Connecting with the contacts, it prevents the batteries from discharging through the frame structure at night.
In the bottom of the frame, drill holes through which the wires are brought out. So that they do not sag, they use silicone sealant in their work.
The following photo gallery will introduce the steps of assembling a solar panel of 60 elements:
The photocells assembled by soldering must now be fixed on the base. Can be glued to plywood and covered with glass. However, in the example, gluing is first done to the glass:
In order for the battery, designed to accumulate charge, not to absorb the energy generated by photocells, its solar battery is connected via the Stocks diode:
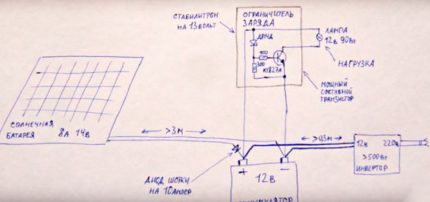
This mini power station is capable of generating up to 15 V. It should be noted that the maximum productivity will be noted only on sunny cloudless days. In cloudy weather, the device will generate much less or will not generate energy at all. Therefore, the battery is selected for it so that the stock is enough for at least a day.
How to test the mounted unit?
Before finally sealing the assembled generator, it must be tested to identify potential failures during the soldering process.The most reasonable option is to check each soldered row separately. So immediately it becomes clear where the contacts are connected poorly and re-processing is required.
For the test, use a household ammeter. Measurement is carried out on a cloudless sunny day at lunchtime (period from 13 to 15 hours). The design is placed in the yard and installed at an appropriate angle.
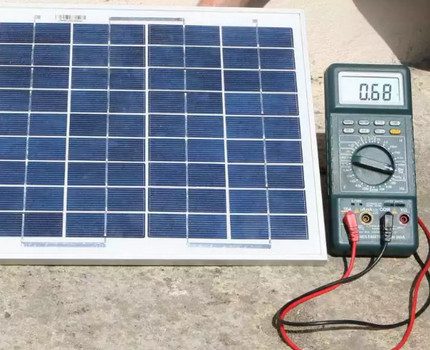
An ammeter is connected to the output contacts of the solar battery and the short circuit current is measured. If the device shows results above 4.5 A, the system is completely correct and all connections are soldered clearly and correctly.
The lower data that appears on the tester's display indicates violations that need to be tracked and re-soldered. Traditionally, self-made solar generators made from photocells with a small defect (group B) show numbers from 5 to 10 amperes on the test.
Aggregates of factory production show data 10-20% higher. This is due to the fact that silicon wafers of group A are used in the production, which have no defect in the structure.
The final stage of work
If the test showed that the battery is fully operational, it is sealed with a special silicone sealant or a more expensive and durable epoxy compound.
The work provides two ways of conducting:
- Full pouring - when the entire surface is covered with a hermetic composition.
- Partial processing - when the sealant is applied only to the extreme elements and the empty space between the elements.
The first option is considered more reliable and provides the system with full protection against external factors. Photocells are clearly fixed in place and work correctly with maximum efficiency.
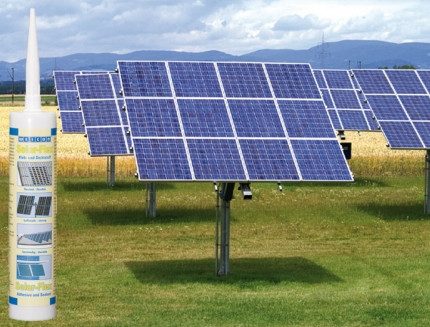
When the filling is done, the sealant is allowed to “seize”. Then cover with a transparent element and firmly pressed to the plates.
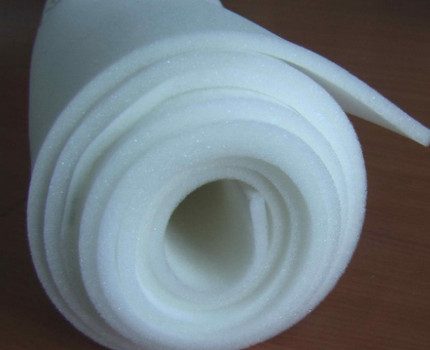
Then, a load is placed on the surface, which acts on the layers and squeezes out air bubbles from them. The finished generator is tested again and finally mounted on a previously prepared place.
Where and how to place the generator?
The installation location of the solar generator is chosen very carefully and without haste. Plates that receive light must be placed at an angle so that the rays do not “fall” to the surface perpendicularly, but, as it were, gently “flow” along it.
Ideally, the structure is positioned so that it remains possible, if necessary, to adjust the angle of inclination, in this way, "catching" the maximum amount of sun.
It is perfectly acceptable to supply a solar system from solar panels on the ground, but most often they choose the roof of the house or utility room for placement, namely that part of it that faces the most consecrated, mainly southern side of the site.
It is very important that there are no tall buildings and powerful, sprawling trees nearby. Being in close proximity, they create a shadow and interfere with the full operation of the unit.
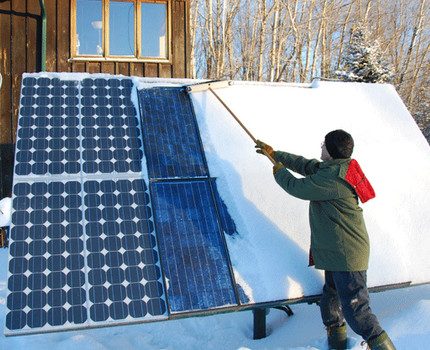
The average optimum for installing a solar generator is considered to be a roof tilt angle of 45 °. With this arrangement, the solar cells absorb the solar flux very efficiently and produce the amount of energy necessary to ensure the correct functioning of the house.
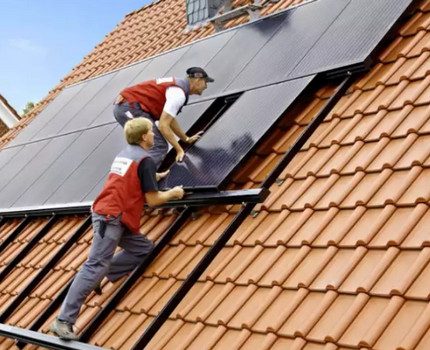
For the European part of the CIS countries, slightly different indicators apply. Professionals recommend taking as a basis a stationary tilt angle of 50-60 °, and in movable structures during the winter season, place batteries at an angle of 70 ° to the horizontal.
In summer, change position and tilt the photocells at an angle of 30 °.
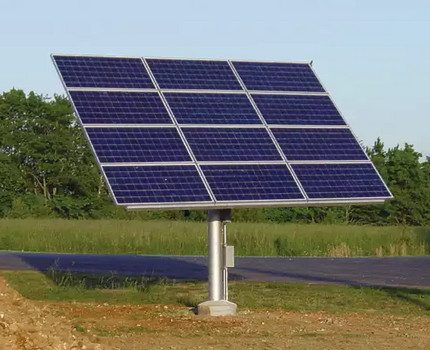
Immediately prior to installation, the roof is additionally strengthened and equipped with special durable supports, since not every design has the ability to withstand the full weight of the equipment for converting solar energy.
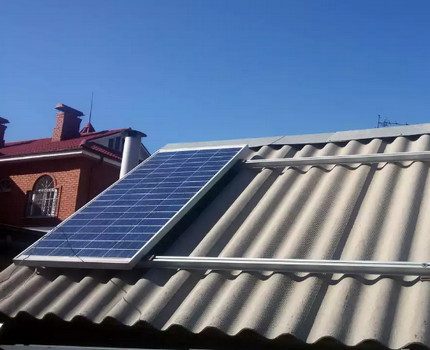
In some cases, reinforced rafters are placed under the roof, protecting the roof from collapse, which is potentially possible due to increased load, which increases significantly in the winter season, when snow accumulates on the roof surface.
To start working the solar system will require batteriesinverter and charge controller. You will learn about the rules for selecting devices and their inclusion in the chain from the articles recommended by us.
Conclusions and useful video on the topic
Features and nuances of soldering photocells for making an effective solar generator with your own hands at home. Tips and advice for masters, interesting ideas and personal best practices.
How to properly test a photocell and measure its basic parameters. This information is useful in subsequent calculations of the exact number of plates required for the full operation of the system.
A complete step-by-step description of the process of collecting a solar battery for a generator at home. Rules of operation, from the acquisition of the necessary elements to the general test of the manufactured device.
Knowing the arrangement of solar generators, assembling them at home is not a big deal. Of course, the work will require attention, accuracy and scrupulousness, but the result will justify all the financial and labor costs. The complete unit will fully provide the building with heat and electricity, creating the necessary level of comfort for residents.
Immediately swipe at a large project is not worth it. To begin with, it makes sense to try your hand at assembling a small unit, and then, having completely mastered all the nuances of the process, proceed with the construction of a more powerful and large-scale installation.
And what method of building a mini-power plant did you choose to equip a summer cottage? Please write comments, share useful information and photographs on the topic of the article in the block below. Ask questions about controversial or obscure points.
Quite a long time ago, an ever-increasing payment for electricity began to worry, because I myself began to think about the problem of alternative sources. I wanted to install solar panels on my site, but my hands didn’t reach, and finances did not allow me. But, as I understand it, making them yourself is not so difficult, of course, you need to get confused a bit, but still there will be free electricity later on, besides less harm to nature.
You can collect it, only adequate effectiveness can you achieve only if you live in the south of our country. At one time I got into the topic of solar generators, but, unfortunately, in Siberia we have enough solar energy only during a couple of summer months.
And I didn’t even think before that you could assemble a solar energy generator on your own. I looked at the list of necessary materials - it seems that there is nothing particularly complicated. Just think about where to get the modules. If I can’t find it in the city, I will order it through the Internet. I’m tired of overpaying the state for electricity, I don’t understand where the large sums in the bill come from, if in the country I hardly consume electricity.