Pressure switch for compressor: device, marking + wiring diagram and adjustment
Using an air pneumatic relay allows you to automate the filling of the compressor receiver with compressed gas. The equipment operator with a pressure switch does not need to monitor the process, trying to fix the limit parameters. As a result, engine failure is prevented. Significant results, isn't it?
If you plan to purchase a pressure switch for a compressor, then you have come to the address. It is here that you will find a vast amount of extremely useful information about the principles of operation of the device, its configuration and connection methods.
We have described in detail the existing types of pneumatic relays. They brought options for connecting to a household and industrial network with extremely clear schemes. Disassembled typical breakdowns and ways to prevent them. The information and useful tips that we presented are supplemented by graphic, photo and video applications.
The content of the article:
- The principle of operation of the pressure switch
- Complector unit automation
- Types of pressure control devices
- Pneumorelay legend structure
- Air Relay Connection Diagrams
- Installation of relays and accessories
- Adjustment and commissioning
- Possible device malfunctions
- Breakdown Methods
- Conclusions and useful video on the topic
The principle of operation of the pressure switch
The name of the relay is determined by its purpose - controlling a reciprocating compressor to maintain the required atmospheric pressure working force in the receiver. Infrequently, it can be found on a screw-type device that is responsible for compressing and supplying air.
I take into account the magnitude of the pressure force in pneumatic automation, the device acts on the voltage line, closing or opening it. Thus, insufficient pressure in the compressor starts the motor, at the time it reaches the necessary level, it turns it off.
This standard principle of operation, based on connecting a normal closed circuit to the circuit, is used to control the engine.
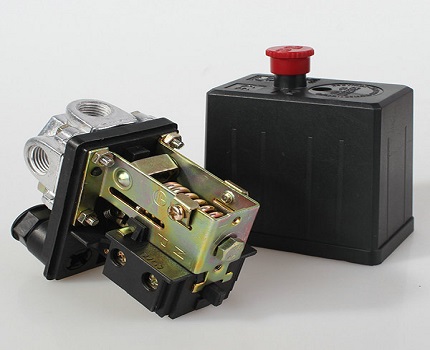
Modifications with the opposite algorithm of operation are also presented: reaching the minimum values in the compression scheme, the pressure switch turns off the electric motor, at maximum - it activates. Here the system is activated in a normally open circuit.
The acting systems are spring mechanisms with varying degrees of stiffness, reproducing the reaction to fluctuations in the air pressure unit.
In the process of functioning, indicators are formed that are formed as a result of the elastic tensile or compressive forces of the springs and the onslaught of the pressed atmosphere device. Any changes automatically activate the action of the spiral and the relay block connects or disconnects the power supply line.
However, it should be borne in mind that the device of the review model does not provide for regulatory influence. Exceptionally impact on the engine. At the same time, the user has the opportunity to set the peak value, upon reaching which the spring will work.
Complector unit automation
The design of the relay is a small-sized unit, equipped with receiving pipes, a receiving element (spring) and a membrane. Mandatory subassemblies include an unloading valve and a mechanical switch.
The sensing unit of the pressure switch is composed of a spring mechanism, the change in the compression force of which is carried out by a screw. According to factory standardized settings, the coefficient of elasticity is set to a pressure in the pneumatic chain of 4-6 bar, as reported in the instructions for the device.

The degree of rigidity and flexibility of the spring elements is subordinate to the ambient temperature indicators, therefore absolutely all models of industrial devices are designed for stable operation in the environment from -5 to +80 ºC.
The tank membrane is connected to the relay switch. In the process of movement, it enables and disables the pressure switch.
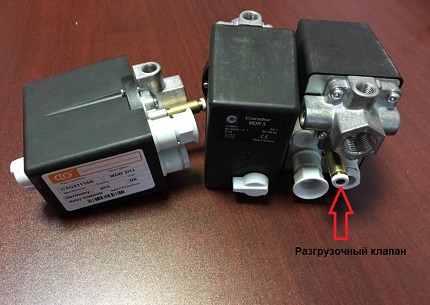
The discharge element is located between the check valve of the ejector and the compression unit. If the motor drive stops working, the unloading department is activated, by means of which excess pressure (up to 2 atm) is vented from the piston compartment.
With a further start or acceleration of the electric motor, an onslaught is created that closes the valve. This prevents overloading of the drive and simplifies starting the device in off mode.
There is an unloading system with a time interval for switching on. The mechanism remains in the open position at the start of the motor for a given period. This range is enough for the engine to achieve maximum torque.
A mechanical switch is required to start and stop automatic system options. As a rule, there are two positions in it: “on” and off. The first mode includes a drive and the compressor operates according to the inherent automatic principle. The second - prevents accidental starting of the motor, even when the pressure in the pneumatic system is low.
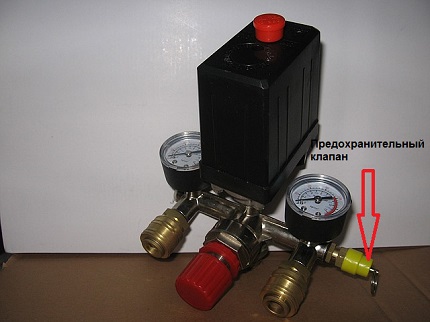
Safety in industrial structures must be at a high level. For these purposes, the compressor regulator is equipped with a safety valve.This ensures system protection in the event of an incorrect relay operation.
In emergency situations, when the pressure level is higher than the permissible norm, and the telepressostat does not work, the safety unit is turned on and the air is vented. According to a similar scheme safety valves in heating systems, the principle of operation and devices of which are described in our recommended article.
Optionally, as an additional protective equipment in the survey device, it can also be used thermal relay. With its help, monitoring the power of the supply current is performed for timely disconnection from the network with increasing parameters.
To avoid burnout of the motor windings, the power is turned off. Setting the nominal values is carried out by means of a special control device.
Types of pressure control devices
There are only two variants of the compressor unit automation. The determination is made based on their principle of operation. In the first version, the mechanism turns off the electric motor when the set limits of the air mass pressure level in the pneumatic network are exceeded. These devices are called normally open.
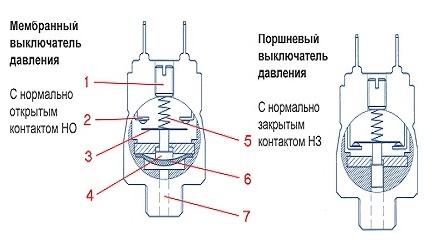
Another model with the inverse principle - turns on the engine, if the pressure drop is determined below the permissible mark. Devices of this type are called normally closed.
Pneumorelay legend structure
The marking of the air pressure switch indicates the entire optional set of the device, design features, including information about the factory settings of the pressure differential.
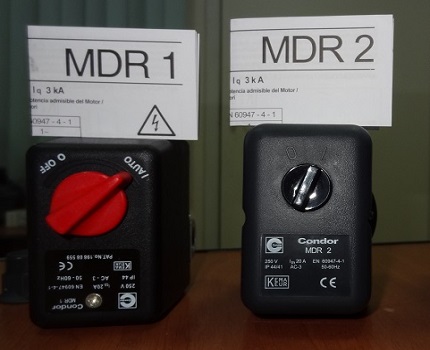
Let us examine in more detail the notation on the example of devices for air ejectors RDK - (*) (****) - (*) / (*):
- RDK - a series of relays for compressors;
- (*) - number of threaded ports: 1 - one port with 1/4 ”NPT internal thread; 4 - four connectors;
- (****) - type of structural design of the case: T10P - execution 10 with a lever switch; T10K - button switch; T18P - execution 18 with the switch switch; T19P - 19 s;
- (*) - factory settings for threshold operation: 1 - 4 ... 6 bar; 2 - 6 ... 8 bar; 3 - 8 ... 10 bar;
- (*) - diameter of the discharge valve: the absence of a symbol means a standardized parameter of 6 mm; 6.5 mm - 6.5 mm.
The difference between the minimum and maximum pressure thresholds is set by the manufacturer and, as a rule, has a value of 2 bar.
However, manual adjustment of the range of two values is also possible - maximum and minimum, but only downward.
The specifics of the pressure switch settings for pumping stations are described in next article, the contents of which we advise you to read.
Air Relay Connection Diagrams
Compressor pressure switch is made to connect to various wiring diagrams. In accordance with the rating of the power supply line, the corresponding model of the relay block is selected.
Option # 1: to a network with a rating of 220 V
If the drive motor is a single-phase device, in this case a relay with a rating of 220 V is installed with two groups of contacts.
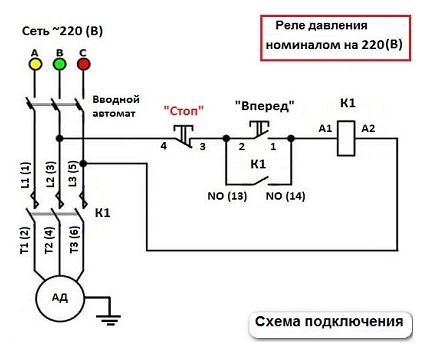
Option # 2: to a three-phase network with a voltage of 380 V
For the three-phase load of the 380 V circuit, one of the options can be used: modification of the relay to 220 V or 380 V, with three contact lines, for simultaneously disconnecting all three phases.
Both methods have different schemes. Consider the first option:
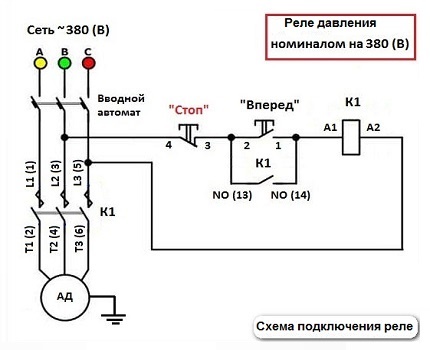
Having chosen the second method, power is supplied from one phase (zero) and in this case the relay rating should be 220 V. In more detail, on the following diagram:
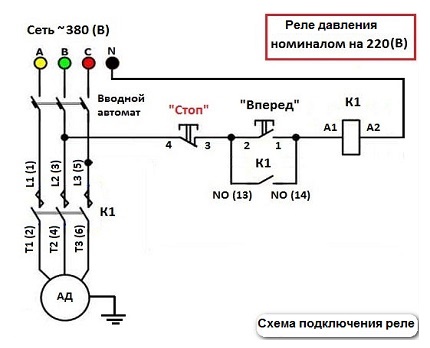
After connecting to the power supply, it is necessary to deal with the additional features presented in the air blocks for ejectors.
Installation of relays and accessories
In some modifications of the pressure switches, you can find additional equipment in the form of flange connections, through which additional equipment is connected. These are mainly three-way parts, with a diameter of ¼ inch.
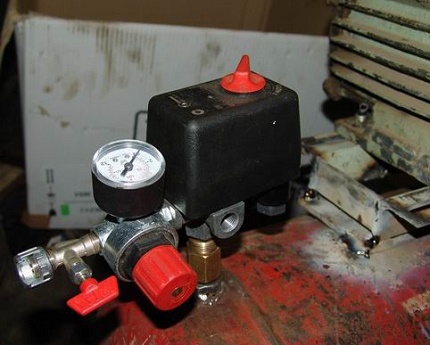
To commission the device, it must be connected to the receiver. Installation consists of the following steps:
- Through the main outlet opening, the device is connected to the compressor.
- A pressure gauge is connected to the device with flanges. There may also be other auxiliary mechanisms requiring activation: a safety valve or an unloading valve.
- Channels that are not used for connection are necessarily closed with plugs.
- Further, according to the wiring diagram, the relay is connected to the contacts of the motor control circuit.
Engines with low power can be connected directly, in other cases, an additional installation of an electromagnetic starter of appropriate power is required.
Before proceeding to the settings of the threshold parameters of the operation, it is worth paying attention to the operating conditions. First, the adjustment is carried out under pressure. Secondly, the supply of electricity to the engine must be cut off.
Adjustment and commissioning
Factory set parameters do not always meet customer requirements. In most cases, this is due to insufficient compression force at the highest parsing point.
Also, the response range of the pressure switch may not be suitable. In this case, independent adjustment of the actuator will be relevant.
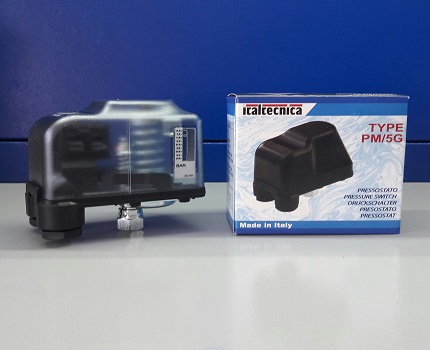
To start setting the working compression value, you will need to inspect the engraving plate, where the parameters of the electric motor and compressor are indicated.
We need only the highest value that the device creates. This indicator indicates the maximum pressure force that can be set on the relay for the correct operation of the entire pneumatic system.
If you set the specified value (in the figure 4.2 atm), then when all factors are taken into account - power differences, development of the service life of the parts, and more - the compressor may not reach the maximum pressure, and accordingly, it will not turn off.
In this mode, the working elements of the equipment will begin to overheat, then deform and eventually melt.

For reliable operation without shutdowns, it is required to set the highest shutdown pressure on the relay, not reaching the nominal value engraved on the compressor, namely lower by 0.4-0.5 atm. According to our example - 3.7-3.8 atm.
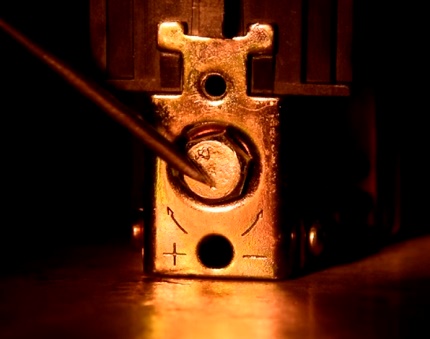
Having determined the level to be set, it is necessary to remove the relay housing. Under it are two control elements - a small and a large nut (in Figure 1.3).
Nearby there are arrow indicators of the direction in which the twisting will be carried out - thereby compressing and expanding the spring mechanism (2,4).
A large screw clamp and spring are used to control compression parameters. When twisting clockwise, the spiral contracts - the compressor shut-off pressure increases. Reverse adjustment - weakens, respectively, decreases the pressure level for shutdown.
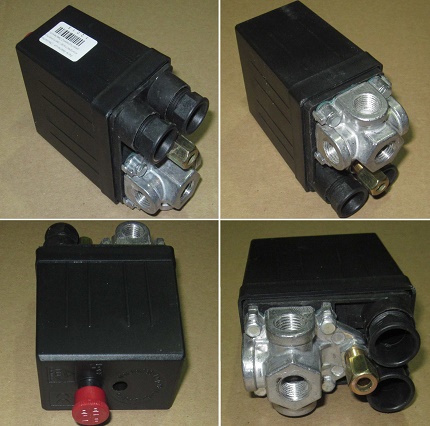
When playing back the settings, the receiver should be at least 2/3 full.
Having understood the purpose of the elements, we proceed:
- To ensure the proper level of security, turn off the power.
- Changing the level of compression of the springs is carried out by turning the nut a few turns in the required direction. On the board near the large-diameter adjusting screw, according to the standards, there is a legend with the Latin alphabet P (Pressure), the smaller one ΔР.
- The adjustment process is monitored visually on a pressure gauge.
For convenience, some manufacturers make adjusting valves to change the nominal value on the surface of the device.
Possible device malfunctions
Several malfunctions characteristic of pressostats are noted. In most cases, they are simply replaced with new devices. However, there are minor problems that can be fixed independently without the help of a repairman.
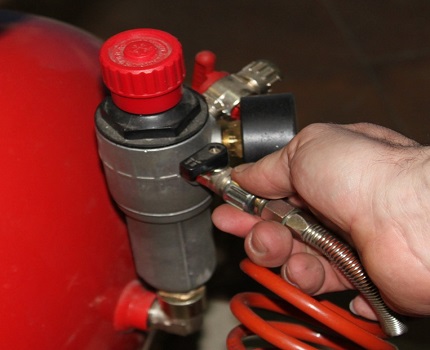
More often than others there is a malfunction characterized by air leakage from the relay when the receiver is on. In this case, the trigger may be the trigger. It is enough to replace the gasket and the problem will be fixed.
Frequent activation of the compressor indicates loosening and shifting of the adjusting bolts. Here you will need to double-check the threshold for turning on and off the relay and configure them according to the instructions in the previous section.
Breakdown Methods
A solution to a more complex problem lies ahead if the compressor does not work. There may be several sources. Consider one of them - the fusion of the pressure switch contacts due to erosion arising from sparks of electricity.

To eliminate this type of malfunction, you can use one of the methods: clean the surface, which extends the service life by at least 3 months, or repair it by replacing the contacts in the terminal clamps.
Phased briefing of the second option:
- Bleed all air from the receiver and turn off the power to the ejector. Remove the pressure switch.
- Having removed the protective case, we disconnect the wiring connected to the group of contacts.
- Using a screwdriver, it is necessary to remove the terminal with the contacts and drill burnt out lines from it.
- You can replace the wire with copper wire. It is necessary to select taking into account the diameter of the hole, because it should sit tightly in the landing slot. It is inserted into the hole and crimped on both sides.
- Similar actions are done with the rest of the charred lines.
- After the contact group is assembled, it is mounted in its original place and the pressure switch cover is screwed on.
The compressor relay operates in difficult conditions, subject to wear and tear and failure.
Despite the fact that the repair is not cost-effective, those who are familiar with the device can perform it on their own. However, the option of replacing with a new device still remains beneficial.
Conclusions and useful video on the topic
Details about the device of the pressure switch, as well as the visual process of adjusting its parameters in the plot:
It is also possible to independently assemble the control unit for the compressor, about this in the video material:
Pneumatic devices are considered safer and more convenient to operate than electric or gasoline samples. A wide selection of additional equipment working with compressed air is presented: guns for washing, tire inflation or painting, and many others.
Using the relay, it becomes possible to work automatically while maintaining the required compression level in the receiver.
Please write comments in the block form below the test article. Share your own experience in operating the compressor with a pressure switch, ask questions, publish a photo on the topic. It is possible that your recommendations will be useful to site visitors.