Sensors for gas boilers: types, principle of operation, characteristics
A modern gas boiler is a complex engineering unit used to heat water and residential premises. Special sensors for gas boilers help to monitor and link the work of all its mechanisms. Their principle of action is worth sorting out. Do you agree?
It is thanks to the sensors that the key principles of the operation of gas equipment are observed - safety and automation are ensured. In the article we presented, all types of these compact devices and the features of their installation are described in detail. Based on our advice, you will be able to perfectly equip the boiler.
The content of the article:
The main types of sensors
The main principle of operation of all sensors is signal conversion and interpretation of the result for promptly informing the user about changes in the operation of the gas boiler.
Gas equipment is equipped with a set of additional equipment, thanks to which it can be programmed for operation in a certain mode.
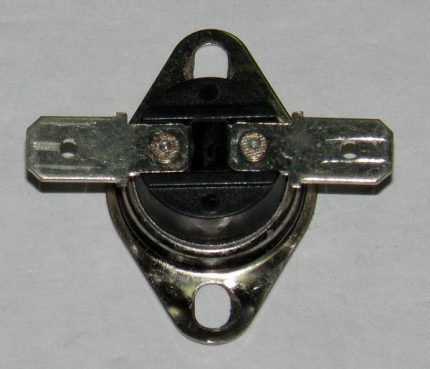
Key sensors responsible for equipment safety:
- traction;
- temperature (outdoor and indoor);
- flame;
- pressure sensors (presostat);
- overheating.
Consider the characteristics and features of the operation of each of them.
To determine the traction force, the device uses a traction sensor or thermal relay to gas boiler, he is responsible for the correct combustion of gas.
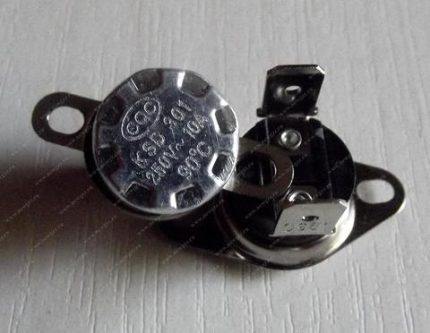
The draft is necessary to rid the boiler of carbon monoxide. Normal draft "removes" the products of combustion from the room, and not into it, weak can provoke attenuation of the column and, as a consequence, an accident.
Most often, such sensors are installed in the smoke exhaust. In the event of a sensor breakdown, smoke from combustion products enters the room and poses a threat to life safety.
The type of sensor depends on the type of boiler to which you want to connect it.The first type is boilers with natural draft, the second - with forced draft.
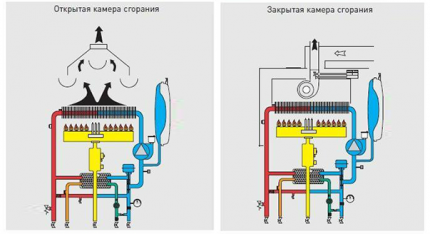
In natural draft devices, the combustion chamber is open. During normal operation, carbon monoxide exits through the chimney, and a safety thermostat monitors the presence of draft and the temperature of the flue gases. In such boilers, a sensor is used in the form of a metal plate with a contact attached to it.
The principle of its operation is to signal the valve, which at the right time will block the gas flow to the burner. Inside the thermal relay is a metal strip that responds to temperature changes.
The thermal relay is set to a specific temperature in accordance with the fuel in the boiler. If natural gas is used, then the temperature limits will be from +75 ° С to +950 ° С, in the case of using liquefied - + 75- + 1500 ° С.
If there is a failure in the process of carbon monoxide exit (through a chimney to the street), in other words, the traction force is violated, then the device works. When this happens, the temperature inside the device rises, the metal expands, the sensor activates and the boiler cools down.
Owners of natural-draft gas appliances should pay attention to the concept of “reverse thrust”. In simple words, this is a process in which carbon monoxide enters a room, rather than being discharged into a chimney.
Failure occurs with temperature fluctuations, incorrect installation of the chimney or its clogging, and inaccurate calculations of the size of the chimney can also affect. Regardless of the cause of the back draft, it must be removed immediately in order to avoid carbon monoxide poisoning.
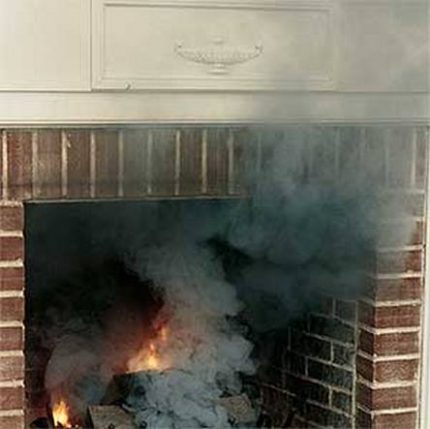
In forced draft devices, a closed combustion chamber is installed and gas is discharged from the fan turbine. A pneumatic relay sensor made in the form of a membrane is used here.
Under normal traction, the membrane deforms slightly under the force of carbon monoxide. When the flow becomes too weak and the membrane remains motionless, the contacts disconnect and the gas valve closes. Such a sensor monitors both the operation of the fan and the speed of the combustion products.
If there are doubts about the operation of the device that interrupts the gas supply in case of gas leakage, it is advisable to install next to the gas equipment carbon monoxide sensor. Installing it is highly recommended, but optional.
The reasons for the draft sensor triggering are: errors in the installation of the boiler or chimney, clogging of the chimney, or stopping the fan (only in devices with forced draft).
The principle of operation and the device for the automation system of a gas boiler are described in detail in the next articlewhich we recommend that you familiarize yourself with.
The principle of operation of the pressostat
A pressure switch or pressure sensor protects the boiler from overheating during a sudden change in gas pressure or a decrease in water flow.
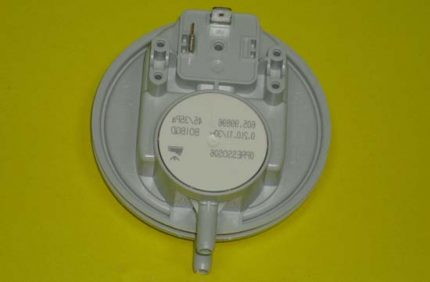
Visually, this is a standard electric sensor or relay, in most cases with two electrical circuits-spotters. It is these circuits that determine two key modes of operation of the device:
- 1 mode assumes normal pressure during which the thermostatic membrane of the sensor does not change its location and the first group of contacts closes. The boiler functions normally due to the passage of current through this circuit. Also, it is always connected to the general circuit of the unit.
- 2 mode the mode is activated when some parameter of the system exits the norm. Inside the relay, the thermostatic membrane shifts and bends.The first controller circuit is disconnected thanks to the membrane, and the second is closed. The boiler equipment stops the correct operation. The operation of the standby mode informing the boiler user about the accident is activated using the secondary sensor circuit.
The sensor is triggered even in the case of the slightest increase in temperature in the combustion chamber. It monitors the minimum / maximum value of the pressure force, and also records the onset of moisture condensation in the combustion products or directly in the gas itself.
What controls the overheating sensor?
The overheating sensor is a small device that protects the gas boiler from boiling, which can occur when the temperature rises above +100 ° С. When the boundary temperature in the heating circuit is reached, the overheating sensor disconnects the contacts and turns off the gas apparatus.
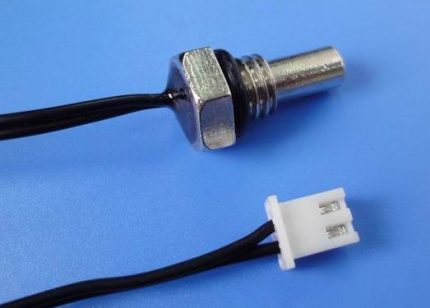
The basis of the device is either thermistors or biometric plates, sometimes it can be NTC working sensors.
Causes of overheating of a gas boiler and options for eliminating them:
- Lack of circulation in the heating circuit due to clogged filters. It is necessary to carefully clean all filters, rinse them or, if necessary, replace with new ones.
- "Airing" of the heating circuit. You can get rid of it by simply removing the air.
- The duct is clogged due to a large layer of scale, while it is audible that the boiler is “knocking” or making pops. Remove excess in the apparatus using special chemicals or acids.
- During the start-up of the boiler, noise sounds are heard, and the device may generate an “insufficient circulation” error. A similar situation is possible during the start-up of the boiler, after its long-term shutdown and without preliminary running of the ventilation system. The cause may be a blockage in the pump due to downtime. It is necessary to disassemble the pump and rinse thoroughly, and then repeat the start again.
- The installation location of the equipment was not selected correctly. In this case, if the room has increased humidity or low temperature, then the metal of which the boiler is made will quickly deteriorate.
For any reason of overheating, it must be removed immediately to avoid boiler breakdown or explosion. The user will be able to get rid of overheating both independently and using the services of an experienced master.
Outdoor and indoor temperature sensors
The main task of the temperature sensor for a gas boiler is to control the temperature and timely inform about its changes. Modern response devices operate on the principle of electrical resistance, which allows you to record operational readings.
According to the method of transmitting information, temperature sensors are:
- wired (communicate with the controller using a cable);
- wireless (wireless radio is used for signal transmission, such models consist of 2 parts).
By type of management they are divided into simple (maintain room temperature) and programmable (there are many functions that allow you to influence the thermal regime in the house).
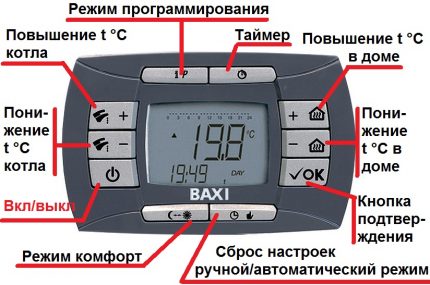
Some sensor models have a built-in thermostat that allows you to control the humidity level in the room. There is also a function to reduce / increase humidity.
By the method of placement, the following devices are distinguished:
- waybills - fastened to pipes of the heating circuit;
- submerged - are in constant contact with the coolant.
Wherein indoor located directly in the room, and street are installed outside and react to temperature changes outside the window.
The first two types are used for the coolant, i.e.for the boiler, and the second two for air temperature control. Overheads are mounted on the outer surface of the pipeline using a special tape or clamp.
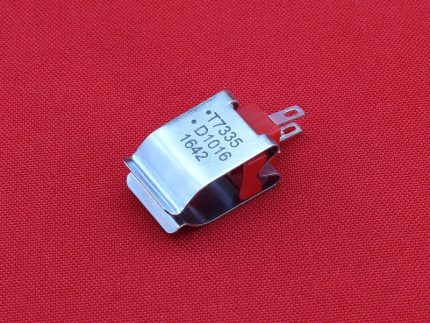
Submersible water heating sensors for the boiler are located only in special places inside the device in close proximity to the coolant.
The response element for measuring the degree of temperature can be an electric transducer (thermocouple, resistance thermometer), pre-configured for a certain range. Such devices can be with a display; in some models, calibration is pre-arranged.
An outdoor temperature sensor allows the boiler to work not all the time, but only if necessary. This increases the life of the gas boiler and the consumption of gas itself. When installing it, protection against mechanical and weather (moisture, frost) effects should be provided in advance.
The set of portable equipment includes:
- the actual sensor;
- terminals for clamping the electric cable;
- cable box;
- a plastic case in which all the parts of the device will be located.
With changes in temperature outside the window, the gas boiler sensor sets into operation a weather-dependent program that makes changes to the temperature regime of heating water for heating.
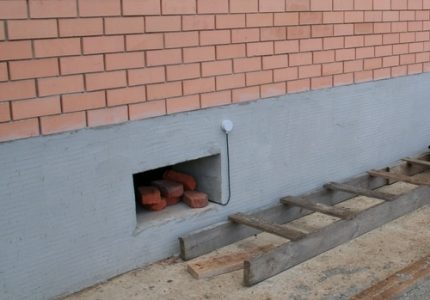
The room sensor responds to changes in room temperature, then sends information to the automation that controls the boiler. And already it gives a signal to reduce or increase the heating power of the heating circuit.
The principle of operation is that the user must initially set the required temperature in the room, and the equipment itself will control the gas equipment.
The boiler will be switched on only if the air temperature in the heated room is lower than the previously set temperature. Thus, you will reduce the monthly gas bill by about a third.
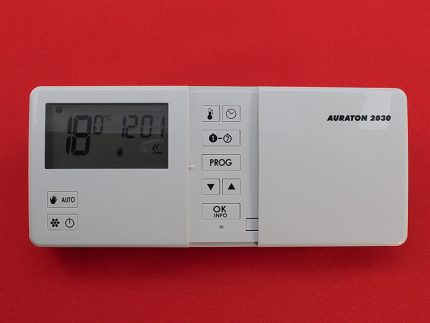
When choosing a temperature sensor, pay particular attention to the temperature range. The best option would be from - 10 ° C to + 70 ° C. Also consider the threshold temperature. There are models that respond to a decrease in temperature by 1/4 degree.
This is not very convenient, as the boiler will often turn off. However, most are triggered by a change in temperature of 0.5 or 1 degree.
The dimensions of the device itself are mainly small: 2 × 3 cm. In wired models, the cable length must be at least 5 m. If you use wireless communication, be sure to test the radio signal.
Rules and Nuances automation adjustments gas heating equipment are detailed in the article, the material of which is fully devoted to this issue.
Flame detector - reliable protection for your boiler
One of the key guarantees of safe operation for a gas boiler is a flame sensor. Its main task is to send the flame attenuation signal on the burner to the automatic system to shut off the gas as quickly as possible in order to prevent its leakage and explosion of the entire device. Also, this sensor should inform the controller about the quality of gas combustion, the presence of a flame, and the intensity of combustion.
Varieties of flame sensors
They depend on the method of flame control during the operation of a gas boiler. Control may be direct or indirect. Thermometric, photoelectric, ultrasonic, ionization and refer to direct methods.
Indirect is considered control over the formation of carbon monoxide in the furnace, the fuel pressure in the pipeline through which it enters, the pressure force or its oscillations in front of the burner. This also includes checking an inexhaustible source of ignition.
A sensor based on the thermoelectric control method includes a thermocouple (it includes a sensor and an electromagnetic valve). The thermocouple is located in close proximity to the boiler burner, and the electromagnetic valve is mounted on the gas pipeline through which gas is supplied to the ignited burner.
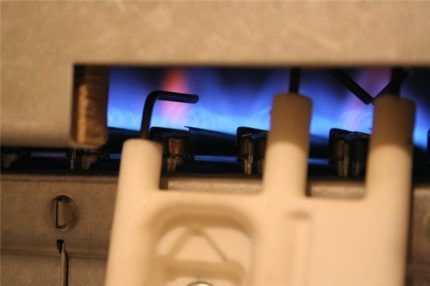
Many modern devices install flame ionization sensors. Their principle of operation is that when a flame is burned, an ionization current arises between the housing and the sensor electrode. It is formed in the case of attraction of ions. If such a current is absent, then this becomes a signal to stop the gas supply.
If the necessary amount of free electrons and negative ions is formed during the combustion of the igniter flame, then automation will activate a key device that allows the main burner to work.
Please note that the correct operation of the ionization sensor is possible only with the exact phase connection of the heating boiler to the mains.
It is this mechanism that is much more effective than others in the case of gas combustion, since the gas does not actually produce light, and therefore the photocell does not always respond. Infrared radiation lasts a little longer, which may be enough to accumulate a large amount of gas, which automatically makes the infrared flame sensor less safe.
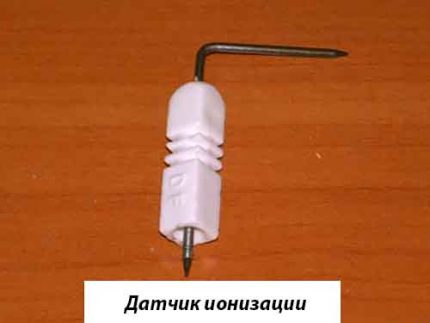
Photosensors control the flame of the key burner, but they are not used to diagnose the igniter flame due to the insufficient size of its flame. Such sensors are divided according to their response to the wavelength of the light flux: some are triggered by the visible and infrared spectrum of the light flux from the burning flame, while others “see” only its ultraviolet component.
For correct operation, the photosensors must have “direct contact” with the flame of the burner, so they are mounted in close proximity to it. They are installed on the side of the burner at an angle to its axis of 20-30 °. Because of this, the photosensors are subject to overheating by thermal radiation from the unit walls and heating through the viewing window.
In order to protect the photosensor from overheating, heat-resistant quartz glasses and forced blowing are used, which is carried out either by compressed air of reduced pressure or by air produced by the fan.
The flame sensor can be triggered. when the key gas-air ratio is violated or the ignition device or valve is contaminated. If the flame sensor breaks down for any reason, it should be replaced immediately. This will save the life and health of you and your family.
Equipping gas heating equipment with a full range of safety sensors and automation devices does not exclude the need for regular maintenance. How technical inspections and repairs of gas units are carried out is described in detail in our recommended article.
Conclusions and useful video on the topic
Even more interesting information about the sensors for boilers is in the videos below.
About the various types of boilers and their sensors. The example shows the installation of a draft sensor.
The author, using an example, tells in detail traction and temperature sensors: location, operating principles and useful subtleties.
A complete step-by-step check of the flame sensor at home, the features of its operation are demonstrated.
Sensors, if they are not included in the package for the boiler, should be selected by the same manufacturer as the gas apparatus. Failure of any of them threatens with an accident or breakdown of the boiler, therefore, requires immediate intervention.
All the described sensors are used for one purpose - to protect the user of the gas boiler from accidents and life-threatening situations. The purchase of each of them is an investment in the safety of equipment, housing and human life.
Want to tell how you picked up sensors for your own gas equipment? Have useful data not noted in the article? Please write comments, share your opinion and information, post a photo on the topic of the article in the block below.
My boiler is equipped with all of the above sensors, in addition, it measures the temperature in the street. I somehow do not see the need for it.
Everything works properly, there are, however, moments that trigger one or the other sensor. Basically this is by pressure, then I add water to the system, or by draft. The latter is especially often honking in foggy weather. It is convenient that the letter of the problem lights up on the boiler display, and there is a decryption in the service book. Automation, of course, is the right thing.
It is not always possible to find all trouble codes in the service book. Here I have a Baxi Mainfour 24 boiler with an open combustion chamber. So in the service book about half of the faults are simply absent. And you have to visit such places in search of various deciphers.
Who wrote this? “A traction sensor or thermal relay for a gas boiler is used to determine the draft force, and it is responsible for the correct combustion of gas.”
This is a bimetal sensor. a plate (as in an electric kettle). Thanks to him, NOTHING will be deduced! And just t ex. The temperature sensor heats the gases at 120 ° C, it gives an accident and turns off the gas. Similar overheating of water 95 ° C.
The overheat protection sensor is also a bimetal plate, most often. And in the photo thermal resistance. Measuring t in the boiler. Sometimes 2 pcs for heating and 1 for hot water.
“Thanks to this small draft sensor, carbon monoxide will not enter the room, but will be vented through the chimney into the street.” It is due to the ingress of hot otkh. gases to the sensor it is triggered. What are 950 oC? Look at him - it says 120 ° C!
Confused with t outbreaks of fuel. Add calories to bimetal. plate. Do not confuse people, where did you see the 950 ° C traction sensor?
Hello Oleg. Yes, you are right, the draft sensor of a gas boiler is a bimetallic relay that operates to turn on and off a gas boiler. A thermal relay is mounted inside, and a metal strip is also located - it is it that responds to temperature changes.
As for temperatures, they depend on the type of fuel: natural gas - temperature range 75-950 ° C, liquefied gas - temperature range 75-1500 ° C. That is, it is possible to configure the sensor to respond in these ranges. This does not mean that he will be sure to be set to the maximum rate.
There are sensors that work in a smaller range.For clarity, I attach a photo.