How to make a Buleryan oven with your own hands: step-by-step instructions on how to make
Externally, the Buleryan furnace resembles a potbelly stove with a fancy design. But the effectiveness of this device is much higher, and the scope is wider.
Models of industrial production are quite widespread, but by making a Buleryan oven with your own hands, you can provide heat to the garage, utility building, and even a small house. Agree, the idea is interesting, and the savings on the purchase of a new unit are very tangible.
In the prepared article you will find all the necessary information for the construction of a heating unit. We will tell you how the Buleryan furnace is arranged and works, describe what materials and tools will be needed during the work, and also give step-by-step instructions for making homemade products.
In addition, the article provides practical tips for arranging a chimney and servicing a heating installation. Following our recommendations, you can organize efficient and safe heating of a small room.
The content of the article:
The principle of operation of the Buleryan stove (Berneran)
The principle of the buleryan is genius in its own way. It combines the features of the long-burning furnace and convection of air masses through special tubes. These elements allow you to immediately visually distinguish the Buleryan furnace from other devices of this type. The combustion chamber is designed so that the fuel burns slowly.
Typically, the load is designed for 12 hours of continuous operation. This allows you to ensure round-the-clock operation of the device with only two fuel loads: morning and evening.
The highlight of the design is the air tubes. They are integrated into the body of the combustion chamber and are a part of it. The upper and lower cut of these tubes remains open.
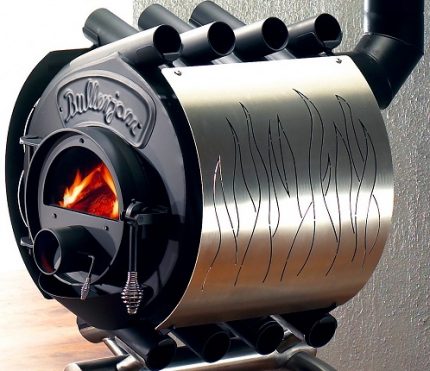
From below, cold air enters the air ducts, which heats up quite quickly and exits through the upper openings into the room.Convection is carried out constantly, so gradually all the air in the room warms up well and quickly to a comfortable level.
The use of tubes as a device case has another undoubted plus: the constant air circulation does not allow the surface to warm up to a dangerous level. As a result, getting burned by touching the Buleryan furnace is much more difficult than when it comes in contact with the surface of the stove.
In this way, you can heat not only air, but also water. To do this, you will have to connect the Buleryan furnace with a heat exchanger through which it will pass water heating circuit.
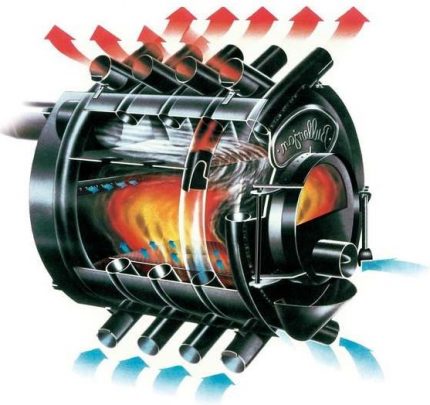
It is worth noting that to ensure the fuel combustion process in such a device, an ignition is first performed, during which the firewood is gradually added in small portions until the chamber is full. After that, it remains only to load firewood into the furnace every 12 hours.
In the furnace, the process of slow combustion of wood is carried out, which takes place in two stages, as in other boilers of this type. First, the fuel burns slowly with a small amount of oxygen. As a result of this process, combustible gas is generated. Then it connects with the air.
The second stage is the combustion of this gas-air mixture, which releases a large amount of thermal energy.
Factory stoves and long burning boilers They are characterized by high efficiency, because they allow you to get much more heat than with conventional wood burning. The efficiency of the Buleryan furnace due to the implementation of this technology is about 80%.
The performance of even small models can exceed five cubic meters of warm air per hour, which is quite enough even for spacious rooms.
Design and device features
Buleryan furnace consists of elements such as:
- a combustion chamber formed of bent tubes and strips of metal;
- secondary combustion chamber;
- back wall;
- front wall;
- door for loading fuel;
- branch pipe for a chimney;
- an ashpit;
- injector;
- chimney gate;
- power regulator;
- blew, etc.
The back wall is made of two sheets of metal, separated by a small space. This protects part of the device from heating to high temperatures, and also increases the overall efficiency of the furnace. In the secondary combustion chamber, the combustion of combustible gases generated during fuel decay in the primary section of the combustion chamber is performed.
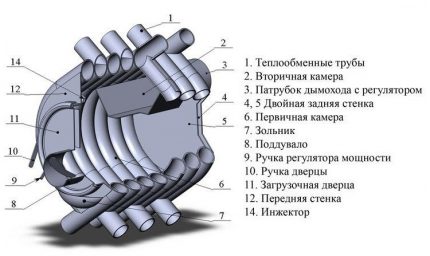
In addition to the door, there is a handle on the front wall with which the amount of air entering the chamber is regulated. The chimney gate performs similar functions. You can use only one of these elements to control the combustion process, or use them simultaneously.
Dimensions of the ash pan, i.e. containers for collecting ash are small, and this is justified. If the Buleryan furnace is started up correctly, then in the course of operation the firewood will burn up almost completely, so the minimum amount of ash will be obtained or it will not be at all.
A number of important elements are mounted in the front door. It is collected separately and then hung using welded metal hinges. For the sake of increasing the efficiency of the device, some manufacturers close the Buleryan furnace with a double case. This is not a required but desirable element in the design.
If there is enough sheet metal available, at the end of the main assembly of the furnace, curved elements can be welded from above onto the tubes, which will hide the tubular “ribs” and make the device safer.
Do-it-yourself process
Given the not the simplest design of the device, it makes sense to draw up a drawing of the Buleryan furnace in advance or find a finished project, for example, on the Internet. It is necessary to cut and cook sheet metal a lot, which requires a welding machine and skills to work with such equipment.
For successful metal cutting, experts recommend using patterns.
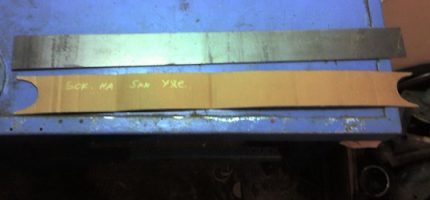
The main material for the manufacture of the Buleryan stove is sheet metal with a thickness of 5-6 mm and metal pipes with approximately the same wall thickness and an outer diameter of 50-60 mm.
To give the tubular elements the desired configuration, it is desirable to use hydraulic pipe bender. To check the position of the individual elements relative to each other, use the construction hydraulic level.
For the normal course of the working process, you will need a number of devices and materials:
- electrodes to the welding machine;
- pipe cutter;
- roulette;
- marker;
- clamps;
- square;
- ruler;
- sanding machine.
They usually start with metal cutting and pipe cutting. Then the metal residues are removed, and the individual elements are welded together, gradually assembling the furnace.
It is necessary to cut the required number of tubes (for example, eight pieces, depending on the features of the project) 120 cm long. Using a pipe bender, they are bent to a radius of 225 mm.Consistently from a sheet of metal, elements of the rear and front walls, doors, adjusters and strips for the body are cut out.
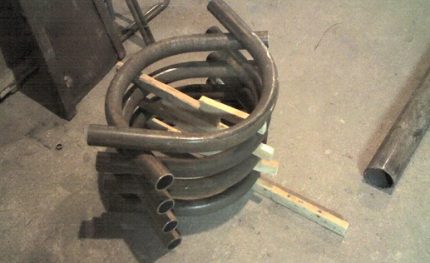
The remaining metal is used for the manufacture of door elements, ashpit, nozzles, etc. Separately make blanks for the V-shaped camera. The metal strips for the body are cut a little wider than the outer diameter of the tubes. Oval cuts are made at the ends so that they can be welded close to the tubes.
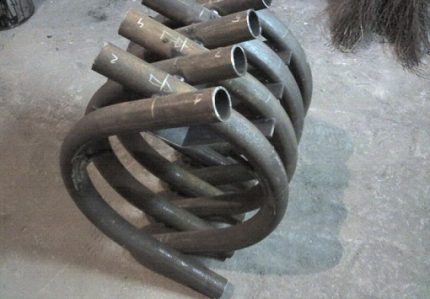
The inlet and outlet nozzles can also be made of strips of sheet metal by bending them into a ring. An alternative is to simply cut pieces of suitable length from a metal pipe. But its diameter should be larger than that of the structure, which is used for the device case.
The assembly of the device begins with the tubes. Correctly bent elements must be staggered so that the rear side of the structure is at the bottom and the front is at the top.
To ensure that the pipes are in the correct position, use wooden blocks with a thickness equal to the outer diameter of the metal elements.
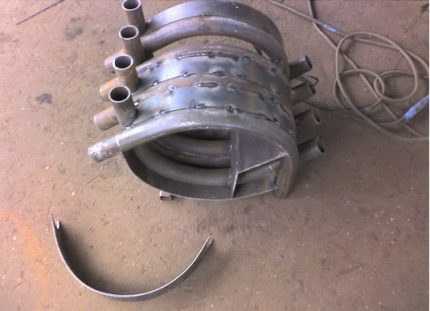
If the pipes are cut and bent correctly, it will be possible to lay out such a “pyramid” on an even footing without any problems. After this, pipes should be welded to each other in places of contact.
The resulting construction can now be turned over and welded in the space between the “ribs” of the V-shaped tray. It will separate the primary combustion chamber from the secondary. In one of the tubes of the front wall, an injector should be made to supply air to the secondary combustion chamber.
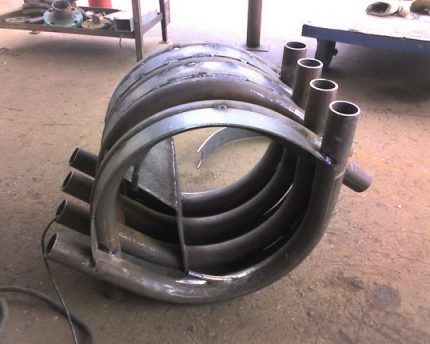
After this, it is possible to continue the formation of the stove body by welding metal strips previously cut to the ribs. The best option is when about two-thirds of the diameter of the pipe is recessed into the body, and the third part of these elements remains outside. With the manufacture of the front wall of the stove will have to tinker.
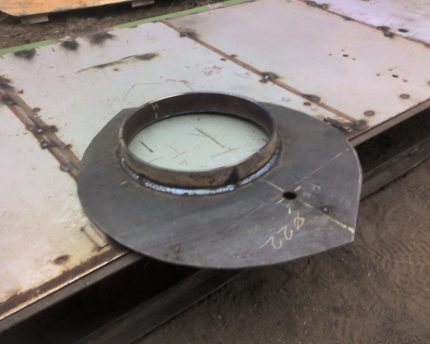
In the blank for the door, a hole for the blower is first made. A pipe is welded to it, in which a damper will be installed that regulates the air flow entering the primary combustion chamber.
For the shutter, you need to cut a round part, the diameter of which exactly matches the size of the nozzle. A pin is welded to the damper. After that, a hole is made in the nozzle along the axis, into which this pin is inserted.
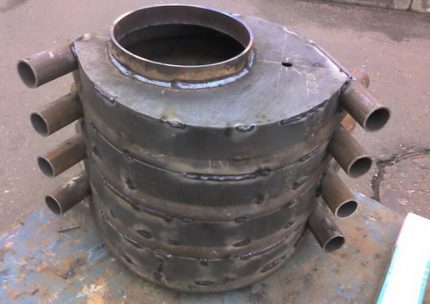
A hole for the door is made in the blank for the front wall. A narrow strip of metal is welded to it around the circumference.
Two such strips of metal need to be welded to the door itself, one on the very edge, the other should be inside at some distance from the first. If everything is done in accordance with the drawings, the “collar” on the front wall will definitely fit into the gap between the edges of the door.
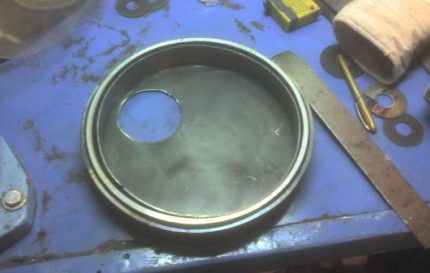
It is recommended to lay an asbestos cable in this space in order to ensure maximum tightness when closing the door.Now you need to weld its inner part to the door, as well as hinges on one side and an eccentric latch on the other.
The eccentric lock provides a tight fit of the door to the front wall of the stove for maximum tightness, which is important in the process of long burning of firewood.
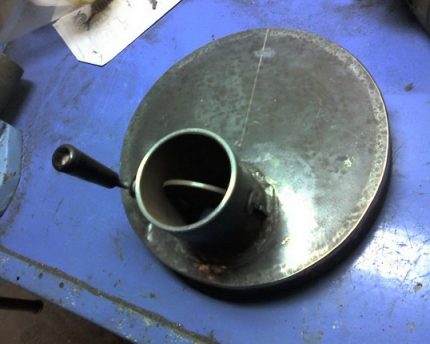
An inexperienced master is better to order this item from a professional turner. Hinges and a metal latch pin are also mounted on the furnace body.
Now weld a double rear wall with a hole for the pipe for the chimney. This element is first applied to the finished structure to make sure that its contours exactly match the outlines of the pipes fastened together.
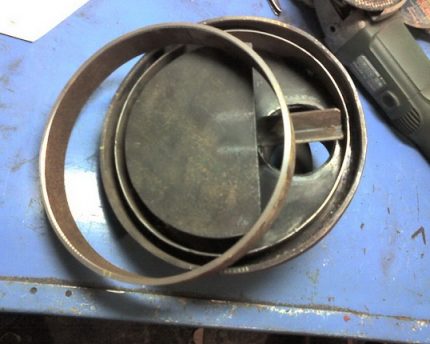
At this stage, you can cut off excess without any special problems. This also applies to other elements - before welding they are checked for coincidence and corrected, if necessary. Now the oven is almost ready. You need to weld four legs to the body. They can be made from bent sections of thick wire.
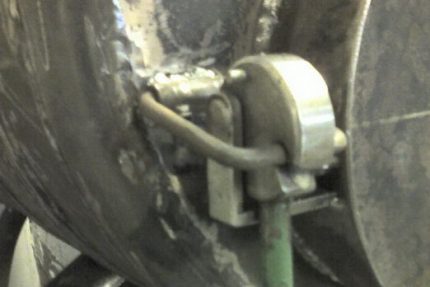
The legs are welded to the front and rear walls of the housing. The finished device is installed on a flat and solid base, covered with fire-resistant materials: asbestos, even slate, ceramic tile, etc.
The walls around the furnace also does not hurt to protect against exposure to high temperatures.
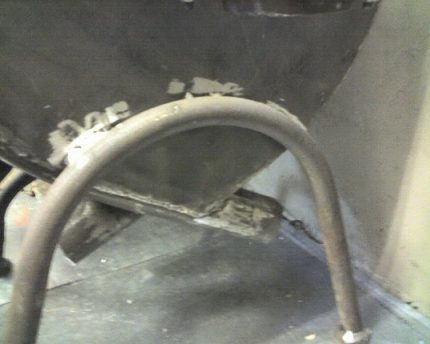
Now, a pipe is connected to the chimney pipe and fixed with a sleeve connection. In this case, the pipes are installed in a position against the direction of gas movement, although the manufacturer recommends doing otherwise. It is recommended to insulate the chimney, for example, using mineral wool.
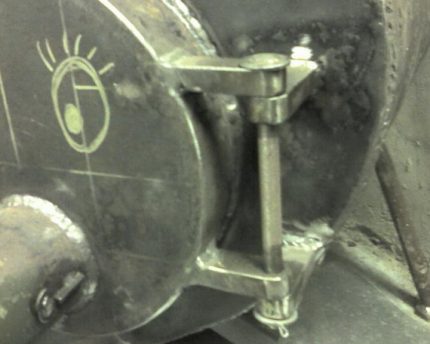
Useful Tips
“Wrong" installation chimney pipes due to the need to protect the structure from resin, which is formed as a result of wood combustion. If this moment is not foreseen, then the resin will flow out of the stove, and with such an installation it will remain in the chimney and gradually burn out.
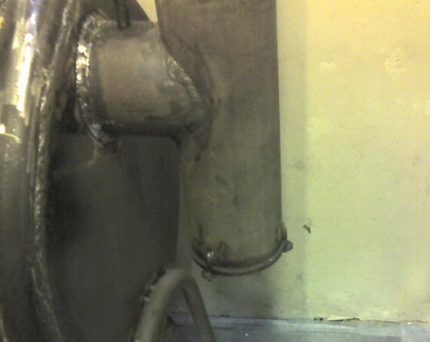
Resin clogging for the Buleryan furnace is almost inevitable. Over time, resinous layers accumulate and clog the device. This is expressed in a noticeable reduction in the efficiency of its work, a decrease in traction, problems with the free movement of the gate. So it's time to clean up the stove.
A lightweight version of such a cleaning is to heat the device with aspen wood. Unfortunately, the practical benefits of such a measure are small and short-lived.
The best way to eliminate tar pollution is through burning. To do this, the furnace is greatly melted with an open ash pan, actually calcining all the channels. As a result, tarry deposits burn out.
On the basis of the Buleryan stove, you can organize an autonomous heating system:
Some craftsmen use oxygen to burn the furnace, bringing the nozzle of the cylinder to the ash hole. This is an extremely dangerous operation that violates fire safety regulations. Careless handling of an oxygen cylinder near an open flame can cause an explosion.
As fuel for the Buleryan furnace, you can use not only firewood, but also wood waste (shavings) or special briquettes. An important condition is the low humidity of the fuel. The less moisture, the less resin is formed inside the stove, and the less often it will have to be cleaned.
During operation of the furnace, it is necessary to select a mode of operation in order to obtain maximum heat with minimal resin formation. If the best option is found, cleaning will need to be performed only a couple of times during the heating season.
Conclusions and useful video on the topic
You can see the real experience in manufacturing Buleryan furnace from improvised materials here:
The independent manufacture of such a device is not an easy task. But the result is a high-performance and convenient heater. Experts note that with proper installation and compliance with operating conditions, the service life of the Buleryan furnace is almost unlimited.
Share with your readers your experience in the manufacture and use of the Buleryan furnace. Please leave comments on the article, ask your questions, participate in discussions and attach photos of your homemade products. The feedback form is located below.
An interesting design, built on a well-known principle. For a long time I plan to collect such things in a house in gardening (I do not see the point of putting a full-fledged stove in a room of 15 square meters.) But the article noticed one drawback - it is indicated that the furnace is assembled from metal sheets.
I would like to understand what kind of metal it should be. From personal experience I know that not every tin can withstand prolonged high temperatures and burns out elementarily. And it’s still not entirely clear whether it is possible to establish any protection against excess odors generated during the combustion of fuel and falling into the pipes (I think that such a hit cannot be avoided). Maybe something like a catalyst on the exhaust pipes? Thank.
At the expense of the thickness of the metal from which the stove will be made, then here you need sheet metal with a thickness of at least 3 mm. But even more than 5 mm does not make sense to use for a stove with a heating capacity of 15 squares.
As for smells, here it is necessary to carefully weld all the seams in the tubes of bulleryan, to ensure normal traction, to work out the mechanism of the furnace door. Together, these measures should minimize odors that arise from the combustion products of solid fuels.
And about the pipes on bulleryan, they are not always used in the Cossacks of chimneys, they can be deaf. Through them, the air in the room just warms up faster, but there are also solutions where side pipes are used as chimneys.