Pipe cutter for steel pipes: types, tips for choosing a model and the nuances of competent operation
The implementation of various communication, construction and repair and installation works involves cutting steel pipes into fragments of the required sizes. For this, in everyday life you can use a simple improvised tool, for example, a hacksaw for metal.
But it is wiser and more practical to purchase a pipe cutter for steel pipes. This unit will speed up the process and make it much less complex and time consuming. Let's understand the varieties of this tool, the principles of its operation, as well as the features of the choice of equipment.
The content of the article:
- Classification of pipe cutters by type of drive
- Types of Separation Elements
- Design Features of Clamp Assembly
- How to choose a blade for a tool?
- The principle of operation of manual models
- What are electric pipe cutters?
- Steel pipe preparation and cutting
- Rules of operation and care
- Conclusions and useful video on the topic
Classification of pipe cutters by type of drive
Modern models of pipe cutters designed for cutting steel pipes of various diameters differ in the type of drive.
Hand held tools are considered the simplest and do not require special skills for use. Usually they are simply fixed in the processing area, made several revolutions and get a fragment with a clear cut. However, this option involves the use of significant physical effort and is not suitable for large-scale work.
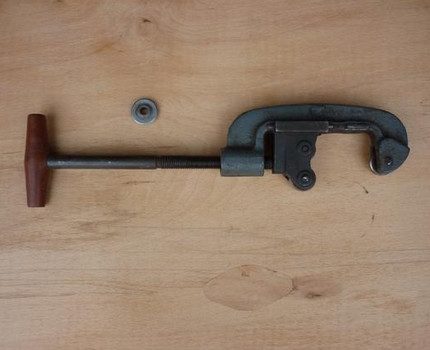
Electric units are made of more durable, wear-resistant materials, so they are suitable for active use, easily cope with intense loads and can qualitatively cut steel pipes of any diameter, including large ones.
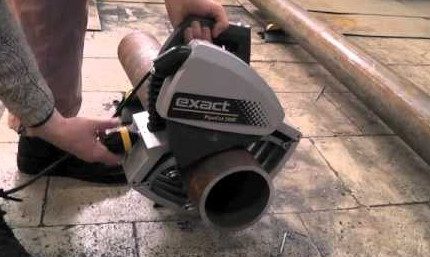
Pneumatic pipe cutters are professional equipment.They provide high precision processing and quickly make the necessary cut.
Cut pipes of any thickness (from thin-walled to 60 mm). They allow you to carry out the necessary work in a small room and have the function of boring the inner diameter of the pipe for subsequent welding.
They have high power and can easily cope with increased loads on an industrial scale.
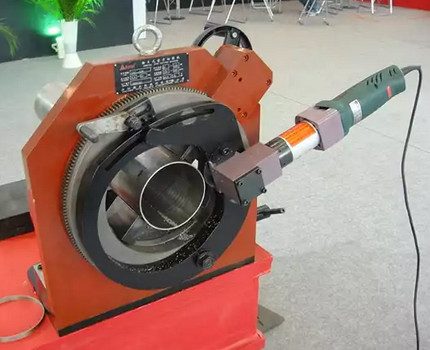
Hydraulic pipe cutters do not require an electrical connection, and the principle of fluid pressure is used in the work. Pumping through the pump, it acts on the piston and drives the unit. When the water pressure decreases, the cutting elements return to their original position.
Tools of this class are more powerful than manual ones, but they are inferior to electric devices in all respects.
The choice of the unit, first of all, depends on the amount of work that is planned to be performed. For a single use, a simple hand tool is enough, and for large-scale events (such as laying communications on a personal site) it is better to use the electric option.
If there is no opportunity to connect to the network, for household purposes you will have to consider buying or renting a hydraulic pipe cutter. In industry, the most productive use of pneumatic machines for cutting steel pipes.
Types of Separation Elements
Units designed for cutting steel pipes of different diameters, differ from each other in the type of trimmer.
Roller tools consist of 1-4 cutting and several feed rollers. A model with one drive roller allows you to process a steel pipe with a diameter of up to 50 millimeters, and a three-roller easily copes with a part having a cross section of up to 100 millimeters.
However, it is extremely rare to get the perfect cut without any roughness from roller units, and this moment is considered the main disadvantage of the equipment.
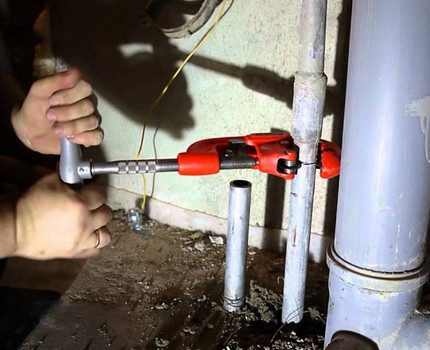
Incisors devices are an iron ferrule covering the workpiece. High quality and durable material of the working element allows you to use the tool for cutting pipes made of thin steel. The position of the cutters is additionally adjusted depending on the thickness of the metal and the total diameter of the pipe. The moving part of the unit moves with a threaded rod.
Simple models are equipped with only two cutters, and the rod element also serves as a handle. These tools are suitable for processing metal with a thickness of not more than 1 inch.
For pipe material with thicker walls, you will need to buy special cutters. The main advantage of the units is the ability to get a perfectly smooth cut that does not require subsequent countersinking.
Chain modules on the principle of impact resemble a chainsaw. They have a tensioning mechanism, pivoting levers and chains with rollers. A tool of this type can effortlessly cut a single-layer pipe material with a cross section of up to 3 centimeters.
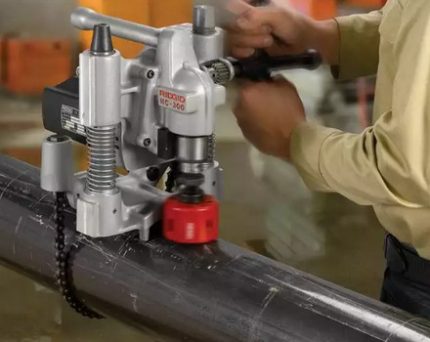
Turning the pipe cutter operates by means of identical interchangeable rollers that are securely fixed around the product. The unit is driven by a removable handle, and the working elements reliably and accurately carry out the cut.
The main advantages of the device include:
- the ability to quickly cut pipe structures with wall thicknesses up to 19 millimeters;
- effective work in difficult conditions (under water, at the bottom of trenches, in foundation pits, etc.).
Of the disadvantages, only one stands out - the high cost of the device, but in industrial production it quickly pays off. Therefore, the price does not become a stumbling block for owners of large enterprises engaged in commercial repair, installation, communication and construction activities.
A suitable pipe cutter should be purchased taking into account the size of the pipe that will have to be cut, where exactly the work will be carried out, and how important it is to get a smooth, accurate cut immediately that does not require further finishing.
Design Features of Clamp Assembly
Another important distinguishing feature of units designed for convenient cutting of steel pipe material is the design of the clamping unit. It can be clamped, lever and screw.
Manual clamp or “lock” devices work quickly and cleanly, easily withstand significant operational loads and cope with pipes up to 12 inches thick and up to 324 mm in diameter.
They have one long handle and one auxiliary. Thanks to this design, the operator does not have to apply excessive efforts for cutting, and the equipment is set up directly during operation.
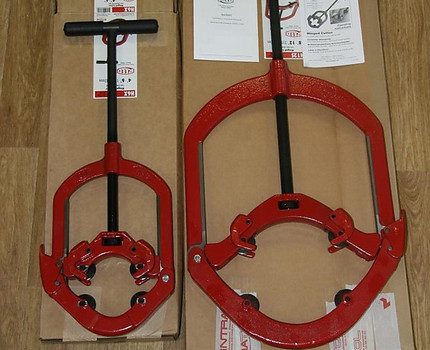
A huge plus of the equipment is the fact that a complete revolution of the device around the part is not required, so the material can be cut in cramped conditions, limited spaces, and even by rolling.
In lever models, the part is fixed by pressing the lever, and in screw models it is held in a constant position by reliable and strong screw elements. To prevent the pipe walls from wrinkling during processing, the part is clamped medium-strongly and held in this position until the moment of cutting off.
How to choose a blade for a tool?
For steel pipe cutters, some specific features relevant, in particular, to working tool blades, are relevant. For high-quality performance of the cut, they must have a hardness of 15 ... 20 HRC exceeding the hardness of the processed pipe material.
This parameter can be determined by performing the so-called “spark test”. It will reveal the approximate percentage of carbon and will enable the identification of molybdenum, tungsten and manganese. In this way, it will become clear what is the initial hardness and what kind of steel was used to make the pipe.
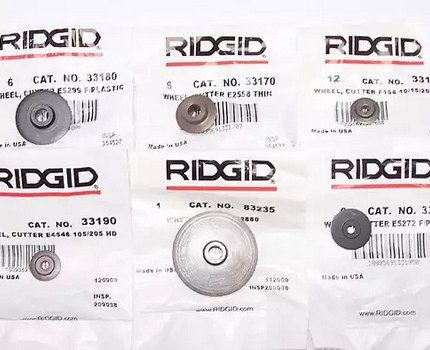
To conduct the test, the end part of the part is processed on an emery grinder and carefully consider the spark generated in the process:
- a more solid sparkling beam of light yellow color means low-carbon unalloyed steel;
- about the medium-carbon composition speaks of the same in color, but more branched beam with some bright flashes;
- standard quality steel gives a thin spark flow with short branches and almost no flash;
- alloy steel is characterized by increased strength and does not show a tendency to brittle fracture. The stream of sparks shines in a thick and rich yellow color, and instead of light flashes elongated shiny arrows are observed.
Having detailed information about the quality of the steel of which the pipe requiring processing is made, it will be easy and fast to select suitable equipment for cutting.
The principle of operation of manual models
In everyday life, the cutting of steel pipes is most easily carried out by a roller pipe cutter. This tool has several circular knives and easily copes with material with a diameter of up to 100 millimeters.
For large pipes, there are special devices that are equipped with not only cutting, but also guide rollers. This allows you to clearly fix the part of any size and ensures its longitudinal stability during processing.
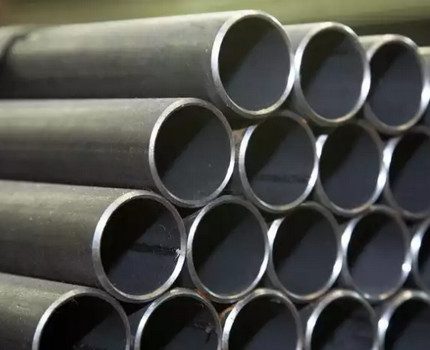
Pipes of large diameter (150-200 mm) should be cut with a rotary unit equipped with a telescopic mechanism responsible for turning the cutting rollers.
These structures provide the opportunity to carry out the processing of parts in adverse conditions (pits, excavations, trenches, etc.).
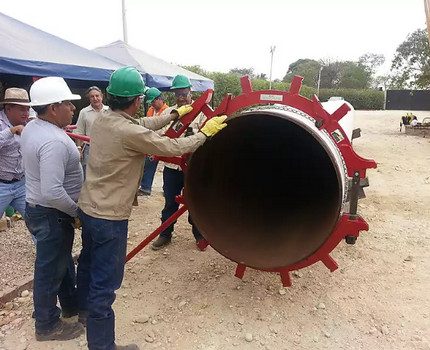
In a rotary device, the rollers are mounted around the outer perimeter of the pipe. When exposed to a lever equipped with a mechanical amplifier, they are pressed against the surface of the workpiece.
Additional movements increase feed and a gradual separation occurs. The cut is carried out not so much by the force as by the developed torque. The technology provides a flat, smooth clipping edge when working with even more durable alloy steel.
What are electric pipe cutters?
When it is planned to lay out a large-scale communication system or carry out global repair and installation work, it makes sense to abandon the hand tool and give preference to the electrical unit.
It functions perfectly both in stationary and in field conditions and makes it possible to complete processing as quickly and cleanly as possible.
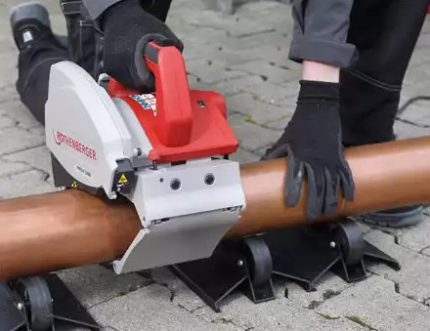
By the type of construction, electric pipe cutters are one-piece and detachable. One-piece assemblies are located on the outer surface of the part and are fixed using a self-centering clamp.
They have compact dimensions and do not require a large space around the pipe in order to carry out full-fledged processing.
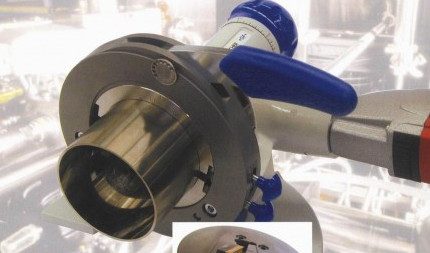
Detachable machines for cutting steel pipe material are easily attached to any part segment. The device consists of interchangeable modules and is located on the outside of the surface.
Despite the fact that the working elements take up minimal space around the pipe, the cut during cutting is very accurate and does not require additional processing.
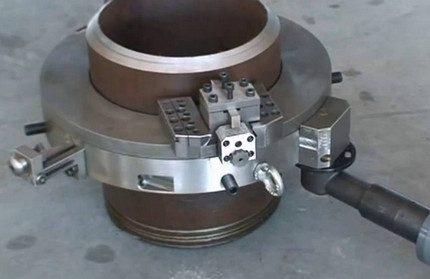
The cut-off element in the device is a pair of incisors with a step stroke of 0.01 cm. An electric motor activates the tool, working from a 220 V network.
Thanks to the high-strength detachable case, consisting of two parts, the unit can be installed on an already functioning pipeline and can quickly eliminate a sudden breakdown or carry out the necessary maintenance of any complexity.
To increase the processing speed, one of the cutters is mounted on the edge of the tube, and the second in the process is cut off the chamfer. The device is fixed by special cams. Usually there are from 4 to 8 pieces.
For complete control of all processes, the device is equipped with a servo drive. It makes it possible to closely monitor the torque and timely adjust the speed of cuts.
Steel pipe preparation and cutting
Before proceeding with the cutting, the pipe material must be properly prepared:
- Wet the area of intended separation with oil. This will reduce the temperature of the metal during operation, clean the external perimeter and partially remove the scale.
- Using a clamp, secure the pipe in the holder, focusing on the cut line previously marked with a marker.
- Using the stem, move the cutting head around the perimeter of the part. Gradually increase the feed, performing the necessary cut.
- If the knives have the necessary strength and a good level of sharpening, the cut-off point will turn out smooth and will not require further processing.
In models designed to cut small diameter pipes (not more than 30 mm), the stem is combined with the handle. When it is set in motion, clipping itself occurs.
Small diameter pipe cutting
For cutting steel pipe material of small diameter, the part to be processed is clearly fixed by the clamping mechanism of the pipe cutter. The handle of the tool is rotated clockwise so that the cutting element comes into contact with the surface of the metal.
Then they make another turn of the handle, making sure that the beginning and end of the notch line are in contact, creating a clear closed circle without interruptions and other violations.
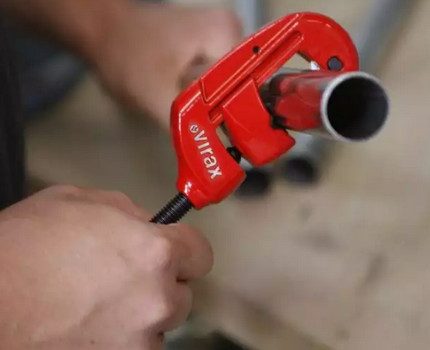
If these parameters are met, the tool handle is shifted another half-turn, pulling the cutting element closer to the pipe. When the cutters clearly enter the metal, the scrolling is slightly accelerated and rotates with the handle until clipping occurs.
Large diameter steel pipe cutting
In everyday life, cutting steel pipes of large diameter is practically not in demand. Basically, material of such dimensions is processed on an industrial scale. For this purpose, enterprises buy very powerful, expensive equipment.
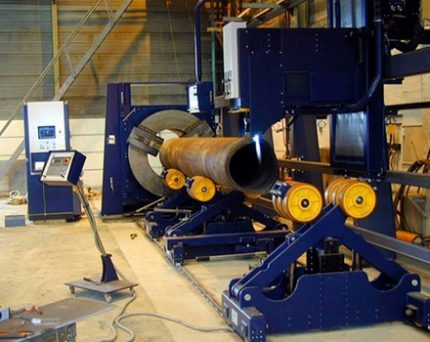
If, nevertheless, a need suddenly arises for cutting large-diameter pipes, it is not necessary to purchase professional equipment.
You can use the usual grinder available in the arsenal of each owner, and, having installed a cutting element for metal on it, make a quick, accurate and high-quality cut-off. But when working with this tool you should not forget about precautionary measures.
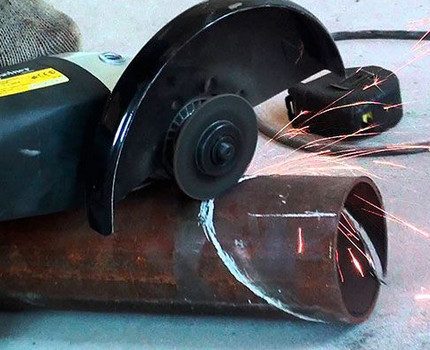
Nevertheless, the grinder is suitable only for the implementation of one-time cutting-cutting works. For regular large-scale events, it makes sense to acquire a more hardy and strong unit.
More information about the various types of pipe cutting equipment can be found in this stuff.
Rules of operation and care
In order for the pipe cutter to serve for a long time and reliably, efficiently cut off and not spoil the pipe walls during operation, it is very important to choose the optimal level of clamping of the steel part.
Do not over tighten the workpiece. This can cause a mismatch in the beginning and end of the cut line, creating an unaesthetic appearance of screw threading on the part.
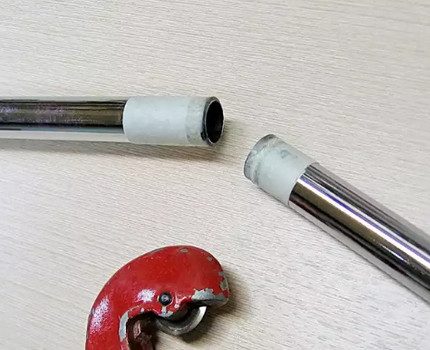
The rotation of the mechanism should be uniform, but not very fast. Otherwise, the walls will hesitate and excess cut metal will form at the cut-off point.
For correct and long service after work, the surface of the cutting roller, feed screw and guide rollers are cleaned with a special tool, and then treated with grease.
The external surface is inspected for dents or other damage, and the chips are ground so as not to interfere with subsequent work. The cutting elements (cutter or roller) are examined for blunting and, if necessary, immediately replaced.
For storage, the pipe cutter is left in a dry and warm place. After such procedures and comfortable storage conditions, the device will remain operational for a long time and will easily cope with all tasks.
Conclusions and useful video on the topic
How does a pipe cutter work: a detailed video instruction on how to use a manual pipe cutter equipped with a pipe clamp. The reliable unit has good power and can handle parts with diameters from 32 to 365 mm.
Cutting steel pipes by a roller pipe cutter: the video clearly shows the process of cutting steel pipe material with a diameter of 3 to 150 mm by a roller unit.
The manual model copes well with one-time jobs, and the electric drive is suitable for larger repair and installation activities.
A detachable pipe cutter for steel in operation: how a detachable cutting apparatus works with steel pipes is clearly visible in this video.The device has a useful function that allows partial cutting of the pipeline even without access to the end of the system.
The device is equipped with an electric or pneumatic drive and provides maximum cutting accuracy when using the minimum space around the pipe for operation.
Knowing all the nuances described above, choose the optimal pipe cutter model no difficulty. For additional advice before buying it is worth contacting the store staff. They will talk in detail about the proposed models and describe all the pros and cons of products of various brands.
Looking for a pipe cutter for home use? Or have experience using such devices? Share it with our readers. Please tell us which model you have chosen, are you satisfied with your purchase? Write comments under the article.