Welding machine for polyethylene pipes: which is better to buy and how to use it correctly
Polyethylene pipes are lightweight, easy to install and relatively inexpensive. To lay communications of this type, a welding machine for polyethylene pipes is needed. The correct use of equipment and compliance with the technology of work allows you to get a reliable, almost monolithic connection that will last for many years.
We will talk about how to correctly select a device for the formation of durable and tight joints. In our article, the features of welding sections of a polyethylene pipeline are described in detail. Those wishing to conduct work on their own will find useful recommendations.
Features of welding structures made of polyethylene
One of the useful features of polyethylene pipes is some design flexibility. Welding allows you to save this property at the junction of individual segments of the highway, which ensures uniform characteristics along its entire length.
Such pipes are cooked for both trench and trenchless layingif steel or fiberglass pipe is used as the main “case”.
Most often, two types of welding are used to connect polyethylene structures: butt and electrofusion (it is also thermistor). Before choosing the right equipment, you should become familiar with welding technologyto be observed when making connections.
When working with pipes made of polyethylene, the ends of the structures are first heated to the melting temperature, then they are connected and compressed under pressure. It sounds simple, but in practice, to get a quality weld, you need good professional skills.
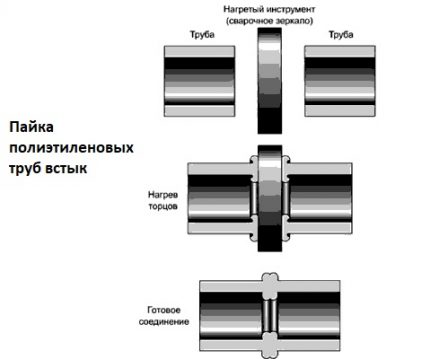
It is necessary to correctly determine the time of each stage, as well as the working pressure that will be exerted on the work surface during its heating and connection. Work is recommended to be carried out at an ambient temperature in the range of -15 ... + 45 degrees. This method is not suitable for structures with a wall thickness of less than 4.5 mm.
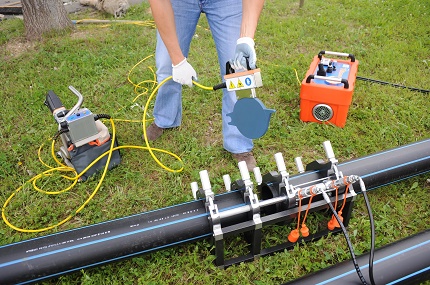
Butt welding can be performed by two specialists, while heavy equipment is not needed. Work time and energy costs for their implementation in this case will be very moderate.
In more detail, the operation scheme for butt welding is as follows:
- The ends of the communications at the points of connection should be cut to clean from contamination and eliminate bumps.
- After that, the ends of the pipes are heated using a welding machine to form the primary burr.
- Heating is continued for some time to reach the melting point of polyethylene.
- Now the welding machine is removed, and the hot ends of the pipes are neatly connected, forming the finishing burr.
- It remains to wait for the structure to cool and check the quality of the weld.
To trim the ends using a special tool - electric trimmer. This device allows you to cut strictly perpendicular to the axis of the structure.
Trimming is performed by microlayers until a continuous polyethylene tape is obtained at the cut point. The temperature and time of exposure of the heater to the ends of the pipes is determined taking into account the grade of material.
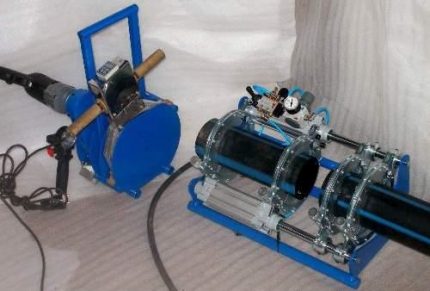
It is very important that the ratio of these indicators, as well as the pressure on the work surface, is maintained with maximum accuracy. This is the defining moment for a quality weld.
At the end of the heating stage, it is necessary to very quickly and at the same time carefully take the heater of the device to the side so as not to violate the integrity of the working surfaces and to avoid accidental contamination.
When connecting the ends heated up to the necessary level HDPE pipes it is necessary to provide the same pressure as when heating surfaces. Weld cooling should also be performed very carefully. The connected pipes must not be removed until the heated polyethylene settles.
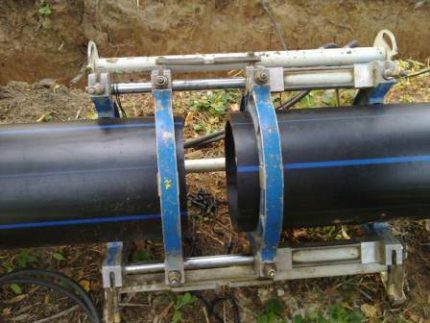
If all operations are performed correctly, a neat, symmetrical collar is formed at the junction of the elements. If the seam looks uneven or messy, it means that serious flaws were made during the welding process. The strength of such a compound will be very doubtful.
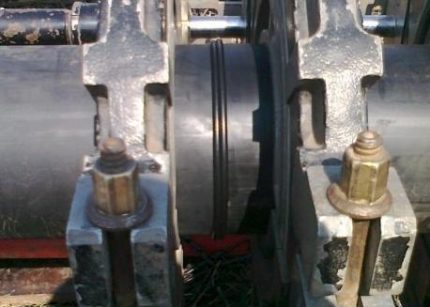
If it is necessary to connect pipes with thin walls (less than 4 mm), it is recommended to give preference to electrofusion welding, which is also called thermistor welding. This option also allows you to create a high-quality connection, while the process of performing work is even easier than using the butt method.
To perform welding of this type, the following steps should be performed:
- To clear from contamination the surface of the ends and the part of the pipe that will be under the coupling, with a good margin.
- Degrease work surfaces.
- Remove the oxide layer.
- Install the coupling on work surfaces.
- Center the design.
- Perform heating and welding of the joint.
- Wait until the weld point has completely cooled down.
All preparatory work should be carried out with great care, since the presence of even the smallest contaminants can significantly impair the quality of the connection. If foreign substances accidentally fall onto the surface after removing the oxide layer, the cleaning should be repeated.
The cooling process has the same requirements as when using the butt method. Any change in the position of the pipe during this period can be fatal to the weld. Electrofusion welding is performed using fittings, in which metal heating spirals are laid in the manufacture.
To start the process, you should install the fitting at the junction and attach it to the welding machine, which will perform the heating.During the welding process, the fitting material expands, providing the necessary pressure and sufficient sealing. At the end of the work, the power is disconnected, and the fitting remains at the junction.
Another interesting method of welding polyethylene pipes - the socket. This is the least popular option, which, unlike the technologies described above, can only be used for laying internal communications. It is also a fairly simple method, technically very similar to the process of soldering pipes from polypropylene.
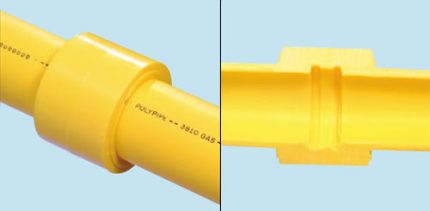
Socket welding can be recommended in rooms where the layout of the pipeline is complex, replete with slopes and turns. To perform operations of this type, almost the same soldering iron is used as for polypropylene structures, and the equipment settings are not much different.
How to cook polyethylene?
Based on information about the features of welding structures made of polyethylene, you can determine the main points that should be considered when choosing suitable equipment:
- pipe characteristics: polyethylene grade, diameter, wall thickness, etc .;
- features of the configuration of the pipeline;
- place of laying pipes (indoors or outdoors);
- acceptable degree of process automation;
- suitable welding technology, etc.
For welding butt pipes use special equipment.
At the disposal of the masters there are devices with which you can perform welding in manual, automatic and semi-automatic mode. The easiest way to master the work of a handheld device, but it is intended only for pipes of small diameter.
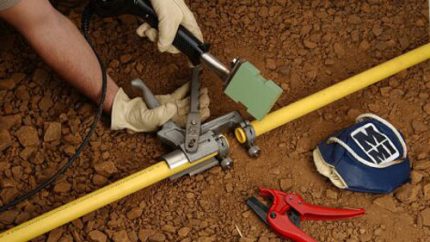
Parameters will have to be determined from the tables. The accuracy of welding on hand-held equipment is not always high enough to successfully work with these types of units, some experience is required. Semi-automatic devices are much more convenient, they are equipped with hydraulics: a station and a centralizer, which greatly simplifies the manipulation.
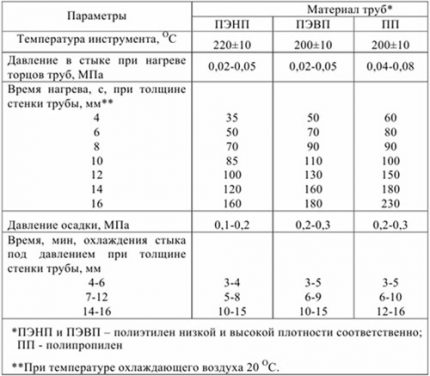
These devices are used to connect pipes of a larger diameter than when working with manual equipment. Although the movement of the elements of the device is automated using hydraulic devices, the welding parameters still have to be set according to the tables.
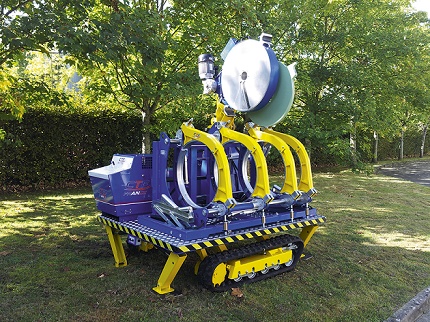
Here, the process is completely controlled by the computer processor. The wizard only needs to enter the necessary parameters, for example, the material from which the pipe is made, the diameter of the structure, SDR, etc.
When using tables, welders operate with concepts such as:
- pipe wall thickness;
- heater operating temperature;
- diameter of the structure;
- end heating time;
- size of burr;
- pressure of welding and preheating;
- heating and readjustment time;
- time to create pressure at the stage of settlement of the structure;
- cooling time.
The temperature of the heater depends mainly on the characteristics of the material from which the pipes are made. To determine this parameter, not only tables are used, but also graphs.
High quality differs butt welding equipment of the Swiss manufacturer “Georg Fischer”. The assortment is very diverse, characterized by European quality and justifiably high price. Relatively inexpensive are the KL Line and Weld Line ruler models.
They allow you to cook designs with a diameter of 630 mm or less, are characterized by a simplified design, providing increased reliability of the unit. Suitable for the installation of water pipes and sewers, incl. and pressure.
GF Line welding machines from the same manufacturer have a more complex device and are more expensive. These are automatic devices using SUVI technology. Such units are often used when laying gas pipelines, they are suitable for working with pipes with a diameter of 160-1200 mm.
For electrofusion welding, devices that automate the process to varying degrees can also be used. The quality of welding depends not only on the type of apparatus, but also on the quality of its performance, as well as on operating conditions.
Professional pipe layers prefer to use units for work. They are equipped with a scanner that scans the barcode provided by the pipe manufacturer.
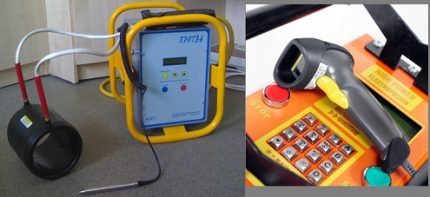
It encrypts a complete block of information about the features of this material. After scanning, all necessary settings will be set. If the pipes are clean and prepared, you can immediately start soldering. Good devices for electrofusion welding not only control every stage of welding work, but also give a warning in case of an error.
When choosing the type of apparatus, the following feature of the welding equipment should be considered. Thermistor devices are suitable for working with pipes of almost any diameter, since heating is carried out through a coupling of the appropriate size. But devices for butt welding need to be taken for a specific diameter of the structure.
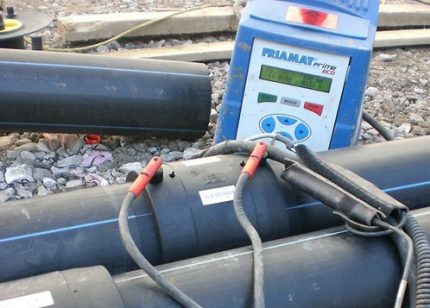
Thermistor devices for welding, in addition, have a very reasonable price in comparison with analogues for butt welding. But it should be remembered that when they are used, electro-couplings will have to be paid separately. For pipes of small diameters, the couplings are not so expensive, but when working with large structures, the difference in price can become noticeable.
The fact is that polyethylene pipes of small diameters (110 mm and less) are delivered in bays. In this way, seamless and flexible communication up to 200 meters long can be obtained.
For the installation of such a design, a minimum number of connectors will be required. But when it comes to pipes with a diameter of more than 110 mm, the buyer is not provided with bays, but pieces with a length of only 12 mm or less.
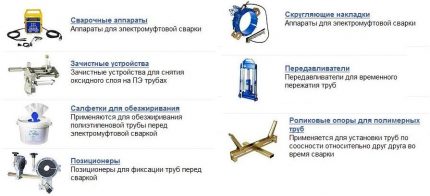
Obviously, for the installation of such a pipeline, a significant number of electrical couplings will be needed to connect many 12-meter sections. Electrofusion welding equipment is compact in size.
If the work needs to be carried out in cramped conditions, this option may become the only possible one. The minimum diameter of structures using electrofusion welding can also be almost anything, starting from 20 mm.
Attention should also be paid to the possibility of repairing the pipeline if such a need arises. Even the geological features of the site where the bookmark is being made are relevant sewer pipeline or water lines. For example, in seismically hazardous areas, butt welding is unacceptable, the thermistor method is mandatory for use.
When choosing welding equipment, you should pay close attention to issues such as the availability of warranty obligations, access to after-sales service, the possibility of regular certification of the device, etc. A reliable seller must have permits for equipment that is usually produced abroad.
Conclusions and useful video on the topic
Comparison and useful tips for choosing welding machines:
This video demonstrates the step-by-step process of assembling a welder for pp pipes with your own hands:
Choosing a suitable welding machine for pipes made of polyethylene is not so difficult. It is better to give preference to products of well-known manufacturers in an acceptable price category. With precise adherence to welding technology, a reliable connection can be obtained.
Tell us about how you chose a welding machine for assembling a polymer pipeline at home or in the country. Share the arguments that determined your choice. Please leave comments in the block below, post a photo on the topic of the article, ask questions.
Can you say something about the welding machine for Protva PE pipes? They offered for suspiciously little money. I doubt whether to take it.