Gas fittings and equipment: varieties + features of choice
The gas pipeline is an engineering structure, each element and node of which solves an important specific functional task and is responsible for the safety, quality and uninterrupted operation of the network. A variety of gas fittings and equipment vary in complexity of execution, according to the material of manufacture, according to purpose and type.
Armature for gas pipelines is an extensive class of devices and devices that are mounted on gas pipelines, as well as on devices. With their help, shutdown / inclusion, change of direction, quantity, pressure of the gas stream or complete removal of gases are carried out. A wide range of these parts is classified, so that you can quite easily deal with the classification of gas fittings.
Let’s take a look at all the variety of fittings for gas pipelines and the features of its choice.
The content of the article:
Purpose of gas fittings and equipment
Gas fittings and gas equipment are intended for installation on pipelines used for transportation, supply and distribution of blue fuel. With the help of these mechanisms, the supply, change in pressure, quantity, direction of the gas stream is turned on and off. The valves are characterized by such basic characteristics as nominal pressure (nominal) and nominal diameter.
Under nominal pressure is takenmax pressure at a temperature of 20 degrees, at which a long service of various connections of elements and units with the pipeline is guaranteed. Conditional pass (DN) is a characteristic that is used in pipeline networks as a common parameter of the connected parts.
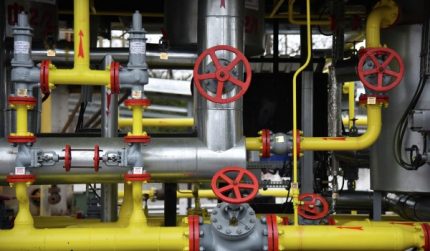
Most of the varieties of reinforcement consists of a shut-off or throttle device. This is a structure in the form of a housing outside closed by a lid.
The shutter moves inside the case. As a result of the movement of the bolt relative to its seats, the area of the section through which the gas passes changes. This process causes a change in hydraulic resistance.
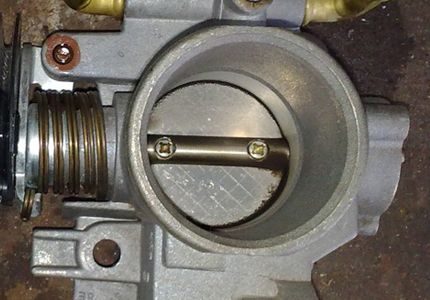
The shutter and seat surfaces in contact during shutdowns of the gas pipeline are called sealing surfaces. In devices of the throttle type of the surface of the shutter and seat, which, in turn, form an adjustable passage for transporting the working medium, are called throttle.
Classification of fittings for gas pipelines
All existing varieties of gas valves, depending on its purpose, can be divided into:
- locking. Fittings used for periodic shutdowns of individual sections gaswires, devices, equipment. This type includes gas tapsgate valves;
- safety. Serving to prevent the risk of increased gas pressure more than the established norms. This type of valve includes a relief valve;
- regulatory. Designed to change and maintain pressure within specified limits. These are dampers, gates, etc .;
- reverse action. To prevent changing the direction of gas movement;
- emergency and shut-off. For quick auto termination gas movement in the direction of the emergency section in case of violation of the specified mode. This type of valve includes a safety valve;
- condensate drain. The one that removes in automatic mode, condensate accumulating in condensate- collectors and in the lower sections of pipeline networks;
- control Determines the pressure of the passing mass, temperature, etc.
According to the control method, valves can be of two types: managed and automatic. The first is driven by manual manipulation or by means of a drive: pneumatic, hydraulic, electromagnetic, electric.
The manual control process is time consuming and time consuming. More often, the drive is installed and the possibility of emergency control in case of accidents remains. And the second one works with devices auto work.
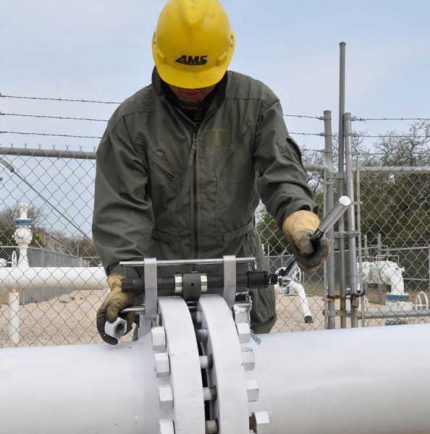
By the method of connection, equipment and any fittings for gas supply systems are:
- flanged - used for fittings with a passage for a medium larger than 50 mm. Connection to pipes is made by screwing up the flanges. The main advantage of such a connection is the possibility of multiple reinstallations great strength and reliability. Universal applicability can also be noted. As a disadvantage, only a large mass and large dimensions of such parts are distinguished;
- coupling - used to connect equipment with a passage of 65 mm or less. The connection is made using couplings with a thread located inside. The disadvantage of coupling joints is that the thread is gradually erased;
- hoe with threaded external thread. One device is screwed into another device;
- welding - these are rarely used today non-separable connections. The advantages of this method are reliable tightness and minimizing maintenance measures.The disadvantages include the difficulty arising from the need to repair the dismantling of the connection when the section of the gas pipeline is simply cut off;
- nipple - the fittings are connected using a nipple;
- couplers - the nozzles are connected to the pipe flanges with studs and nuts, which are located along the fittings;
- nipple - the fittings are connected using a fitting, a union nut and o-rings. This is a reliable dismountable connection method.
In addition to the above, there are other ways to connect gas valves, but they are used, not so often.
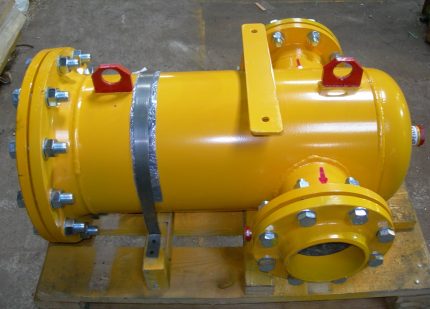
Also, do not forget that the functionality of the pipeline and the reliability of the entire gas distribution system will depend on the quality of the connection made.
Symbols for gas valves
The fittings used in the gas industry are standardized. Each part must have a cipher consisting of 4 parts.
The first 2 digits of the code are the type of reinforcement:
- 11 - valves for pipelines;
- 14.15 - shut-off valves;
- 16 - check valves;
- 17 - safety valves;
- 19 - check valves;
- 25 - control valves;
- 30, 31 - shutoff valves;
- 32 - shutters.
In second place in the cipher is the symbol of the case material: carbon steel - s,acidresistant stainless steel - nzh, gray cast iron - h, malleable cast iron - kch, bronze, brass - br, vinyl plastic - vp, alloy steel - hp, aluminum - a.
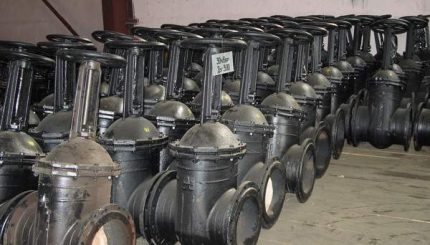
In third place in the cipher is the serial number of the part. On the fourth is the designation of the material from which the o-rings are made: bronze or brass - b, stainless steel - stainless steel, rubber - p, ebonite - e, babbit - bt, o-rings are absent - bq.
Features of shutoff valves
Shutoff valves are most commonly found in gas systems. It is used to adjust gas pressure and acts on the same principle as in water conduits. However, parts in the gas industry have higher safety requirements.
If the gas concentration in the air reaches a critical value, then all the slightest spark is enough and a real catastrophe can happen.
According to the type of movement of the functional mechanism, stop valves for gas pipelines are divided into the following types:
- crane - in the tap, the locking element with the body of revolution moves, while rotating around its axis. With respect to the direction of flow, it can be arranged arbitrarily;
- gate - in this part, the disk-like element rotates around its axis at an angle or perpendicular to the flow;
- valve - in the part, the locking body on the spindle moves reciprocally parallel to the flow;
- gate valve - in it, the adjustment element moves perpendicular to the flow.
It can be summarized that shutoff valves include devices that are designed to tightly shut off sections of a gas pipeline. These devices must guarantee shut-off tightness, speed of action, low hydraulic resistance and ease of maintenance.
Valve operating principle
Most often, on pipelines from different types of valves for gas equipment, valves can be found. They are used when it is necessary to shut off the gas flow in gas pipelines with nominal diameters from 50 mm to 2000 mm, when the working pressure is in the range of 0.1–20 MPa.
In valves, the gas flow is controlled by changing the position of the shutter relative to the sealing surfaces. Spindlenon-retractable when opened, it does not extend out of the lid. When it is rotated to open the hole, the running nut is screwed onto it by raising or lowering the shutter. In this type of gate valve, the running gear is located inside the working medium, therefore it is more susceptible to the negative effects of corrosion.
Equipment with a sliding spindle moves the spindle and shutter by rotating the threaded sleeve, while the upper part of the spindle extends upward. The advantage of this design is the absence of environmental influences on the chassis.
Gate valves differ in the device of constipation into 2 types. Wedges have a shutter with sealing surfaces located at a certain angle to each other. They are also made with a hinged shutter consisting of 2 discs and a continuous wedge. Parallel valves have a shutter consisting of 2 discs, between which there is a wedge spacer.
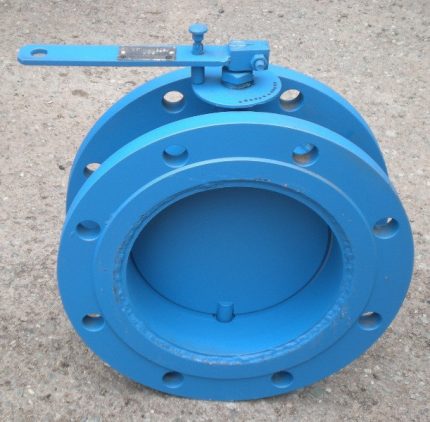
For gas pipelines designed for pressures up to 0.6 MPa, valves made of gray cast iron are used; for pipelines in which pressure is applied under a pressure greater than 0.6 MPa, steel.
But what are the advantages of gate valves in comparison with the rest of the valves? In the open position, slight flow resistance is noted, except for this there are no turns of the gaseous medium. Gate valves have a short construction length. They are easy to maintain and provide the ability to move gas in any direction.
Separately, in this category, you can highlight the flaps. They relate to shut-off and control equipment, due to which the gas flow is regulated, it is also possible to stop its flow in the gas pipeline. The shutters consist of a housing, a locking disk element, a drive shaft.
The valves can be used over a wide range of temperatures or pressures. They have a simple design, low weight and low metal consumption. The dampers have a short construction length and a minimum number of elements. A big plus is the affordable price.
The pressure on modern gas pipelines is monitored by many sensitive sensors that record the slightest deviations and transmit information about them to the controller.
What are cranes for?
In addition to the above devices, valves and valves, necessary for the quickest connection / disconnection of the device or regulation of the flow rate of the working medium, belong to shutoff valves. These parts by the shape of the shutter can be divided into ball, cylindrical, conical.
In order to achieve higher sealing in the valve, a special grease is introduced under pressure between the sealing surfaces. It is tucked into the hollow channel at the top and, by screwing the bolt, is pressed through the channels into the existing gap between the plug and the body.
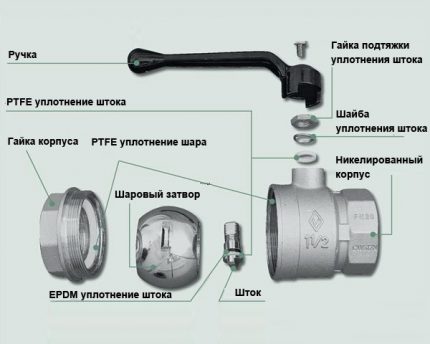
The cork rises slightly, the gap increases and ease of rotation is ensured. Brass gasket and ball valve prevent grease from being squeezed out and gas leaking out.
In addition to valves requiring lubrication, simple slewing valves are used in gas pipelines. They can be divided into tension, stuffing, self-sealing. They can be installed on above-ground gas pipelines, intra-object gas pipelines, on auxiliary lines (on purge gas pipelines, etc.).
Condensate collectors and expansion joints
To collect and remove water and condensate at the lowest levels of gas pipelines install condensate traps.
They can be of different capacities: a large capacity is necessary if the transported gas has a high humidity, less suitable for transporting dry gas. In addition, depending on the pressure of the passing medium condensate traps differ on low, medium, high pressure devices.
Low pressure devices - This is a container with an inch tube brought out under a gas carpet. The tube ends with a sleeve and plug. Condensation is removed through it, measured pressure, the gas line is blown.
Medium and high pressure devices additionally equipped with another protective tube and a crane on the inner riser. On top of the riser there is an opening for balancing the pressure of the working medium in the case and in the riser. Without an opening, the condensate would fill the riser under gas pressure, which could lead to its rupture at low temperatures.
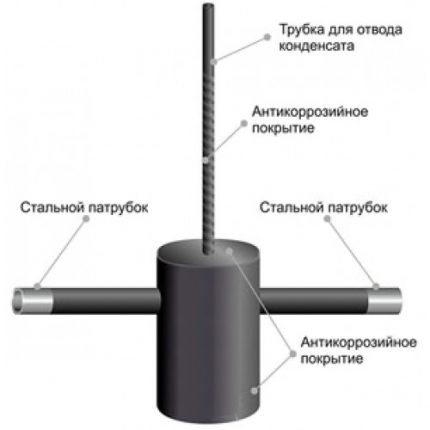
Under the influence of gas pressure is carried outautomatic pumping condensate. When the tap is closed, the gas counteracts the condensate and it slides down. When the faucet opens, condensate rises to the surface.
When operating gas pipelines, the temperature difference can reach several degrees. Such a large magnitude of the change can cause stress of several tens of MPa. Therefore, to ensure the normal operation of the gas pipeline, compensators must be used. They can be lens, U-shaped, lyre-shaped, etc.
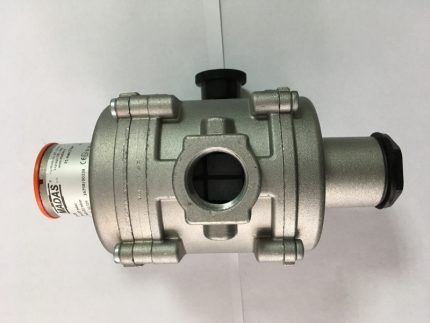
Lens and bellows expansion joints are more common. U-shaped and lyre-shaped expansion joints are made of bent, often seamless pipes. Their main disadvantage is the large size. On pipelines in mountain andseismohazardous areas setrubber fabric devices that are capable of accepting deformations in both longitudinal and transverse directions.
Pipeline fittings
During the installation of the gas pipeline, it may be necessary to connect pipes of different materials or different diameters. In this case, a connecting flange element — auxiliary parts of the docking — is built into the network.
This category of fittings includes flange adapters, clamps, plugs, couplings, bends, crosspieces, tees, in a word details, in the design of which there is no provision for a locking-regulating mechanism.
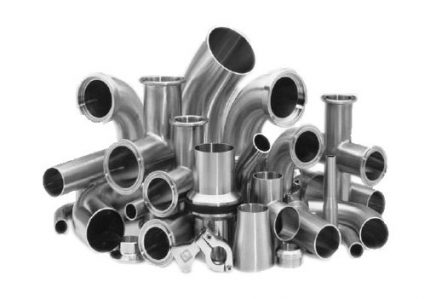
For branching the pipeline are tees and bends. They are installed in cases where the pipe reaches the distribution site for a settlement, but this point is not final.
With the help of control valves, the pipeline is divided and part of the gas transported goes to the village, and part is transported further.

DevicesInstrumentation in gas pipeline systems
In addition to all of the above, numerous devices are used in gas pipeline systems Instrumentation and automation (instrumentation and automation).
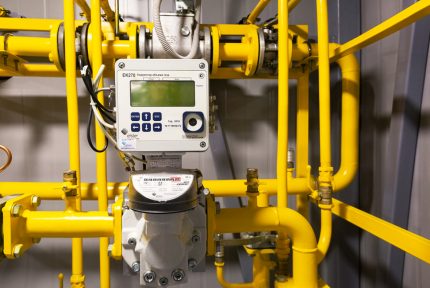
The most popular devices used in gas systems are:
- gas detectors;
- equipment for emergency shutdown of the incoming gas;
- equipment for measuring the volume of past gas;
- electronic regulators of the past volume of gas;
- autonomous power supplies;
- gas valves for automating various processes and optimizing the operation of pipelines;
- gas regulators to regulate the volume of the medium passing through a section of the pipeline.
Such devices are high-tech equipment operating in a wide variety of conditions.
Features of the selection of fittings and equipment
Choosing fittings for gas pipelines special attention should be paid to the chemical and physical properties of the material from which it is made.
The most popular materials for the manufacture of gas fittings are cast iron and steel. This is due to the requirements for an increased level of strength and reliability. Polymer elements that are perfectly suitable for water pipes are not applicable here, in addition, they can easily be damaged.
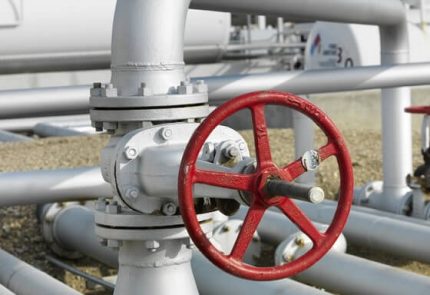
Experts do not recommend the use of equipment with bronze sealing inserts on gas pipelines. This is due to the fact that hydrogen sulfide is present in the LHG, which can have a negative effect on bronze and copper alloys.
Conclusions useful video on the topic
You can find out how maintenance of valves on the gas pipeline is performed from the following video:
The design features of the wedge and hose valves will be discussed in this video:
All gas pipelines are classified as hazardous facilities, so the choice of gas fittings and equipment should be taken very seriously and, if necessary, consult with specialists. Only high-quality gas shut-off valves can provide ease of maintenance, speed of repair, and high tightness of pipeline components.
If you have questions about the topic of the article, or you can supplement our material with interesting information, please leave your comments in the block below.