Insulation of steel gas pipelines: materials for insulation and methods of their application
Are you going to gasify the house or upgrade the gas supply? The gas pipeline is one of the most valuable and dangerous communications, therefore its reliable protection is extremely important.
Agree, damage to the gas pipe and leakage of this fuel can go unnoticed for a long time, and then lead to the most dire consequences. It’s better to carefully study and reinsure everything before arranging protection, right?
If you are interested in insulation of steel gas pipelines, in this article you will get answers to such questions: why is it needed, what happens, in what cases and how to use each type of insulation material, how to check the quality of the coating. We will mention all types of gas pipelines: from trunk pipelines to low pressure pipes, from above-ground to underwater, we will answer all questions that arise.
The content of the article:
Gas Insulation Functions
Today almost every building in every locality is connected to the gas pipeline, it is difficult to imagine the life of a modern person without blue fuel. Just imagine how many pipes are needed to implement such a supply chain!
They stretch above our heads, under our feet, deep in the earth, and even along the seabed. Each centimeter of this gas web must be reliably protected and absolutely safe, because a leak can lead to a large-scale accident, with destruction, and sometimes victims.
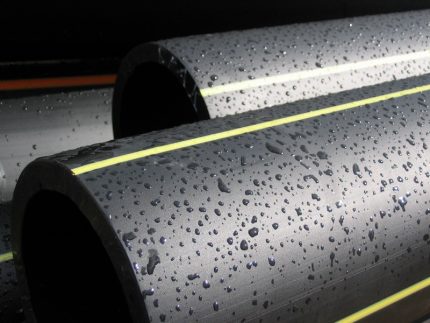
Polyethylene gas pipelines do not need additional protection, but they can not be used everywhere, and replacement is expensive, so most gas pipes are steel.
So that steel does not rust and does not collapse, it is treated with special compounds and materials that isolate its surface from the environment. The main functions of such coatings are protection against moisture, chemical influences, mechanical influences, as well as dielectric protection.
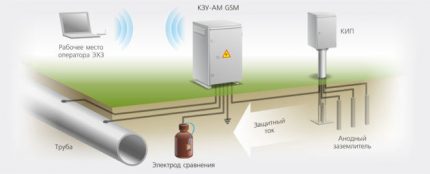
In addition to the coating, for reliable protection against stray and constant currents, electrochemical cathodic protection is organized on underground gas pipelines, which ensures the removal of these charges through a special conductor to the drainage substation.
For an overhead pipeline, the protection is less solid, because it is easier to update, and the pipes are exposed only to atmospheric moisture, regularly drying out. For offshore gas pipelines, on the contrary, in addition to reliable protection from an aggressive environment, an additional layer of weighting is required so that the pipe lies motionless at the bottom, under the waves.
Normative documents and their requirements
There are 3 main documents regulating the organization of the protection of gas pipelines. RD 153-39.4-091-01 "Instructions for the protection of urban underground pipelines from corrosion." As the name implies, it does not apply to the insulation of gas pipes, the diameter of which is more than 83 cm - intercity and international, as well as to pipes laid above the ground or under water.
GOST 9.602-89 - an adjacent document, which contains all the rules and calculations for the protection of underground gas pipelines. If the instruction explains how and from which to equip the insulation, then GOST indicates how much will be required - from meters of material and tools to equipment and labor hours of workers.
GOST R 51164-98 Steel main pipelines. General requirements for corrosion protection. This standard fills the gap in the Guidelines for trunk pipelines. Their protection should be especially reliable and has its own specifics, so the rules of its organization are listed in a separate document.
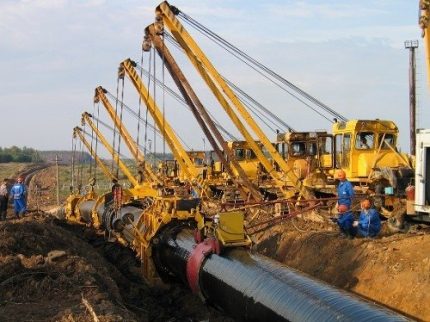
These documents govern the following issues:
- what types of materials are allowed to use on this type of gas pipeline in these conditions;
- how much reinforced insulation is needed, whether electrochemical protection is needed;
- who and when is required to provide the gas pipeline with the necessary protection;
- insulation coating technology at the plant and in the field, as well as for repairing damage;
- norms of consumption of materials and costs of other resources for work;
- the procedure for checking the quality of the coating and standards for quality indicators for all parameters for each type of insulation.
Thus, in these documents the whole process of pipe insulation is described step by step, from the factory outlet to the inspection after installation and during operation. There is no space left for creativity, because these are security issues.
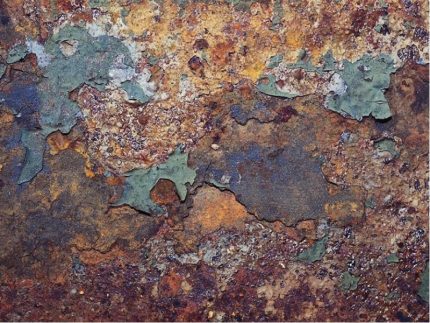
There are also separate lists listing all recommended materials and manufacturers of insulation for gas pipelines.
Given the complexity of the work and a considerable number of standards that must be observed, do not even expect to cope with the insulation of the gas pipeline yourself, and the gas service will not accept the work performed by an external master.
Types of materials for insulation
Based on operating conditions and ease of use, there are many types of coatings for insulation of gas pipes. Elevated gas pipelines are enough to protect with 2 layers of primer and 2 layers of paint or enamel.
Pipes that will serve on the seabed are covered with a layer of concrete on top of the main insulation, for weighting and additional protection.
Next, we will talk about the means of protecting steel pipes underground.
Polymer protective coatings
Extruded polyethylene - The most progressive and universal protection. It is used on pipes with a diameter of 57 - 2020 mm, adheres tightly, forms an ideally uniform continuous layer, protects against temperature and mechanical influences, and is also convenient to use.
In such a coating, the steel pipe is practically not inferior to the polymer analogues in terms of protection characteristics. This protection consists of only 2 layers - a hard bonding adhesive and, in fact, polyethylene. Despite this, such a coating of a very reinforced type on pipes of large diameter can reach 3.5 mm.
Extruded Polypropylene It is specific for its high mechanical strength: it is possible to drag pipes through it with wells, for closed laying methods, and not worry that the insulation will be damaged by friction or hooking on stones and soil. Externally and in structure, this type of insulation does not differ from polyethylene, only 0.3-0.5 mm thinner.
Polymeric adhesive tapes there are polyethylene and polyvinyl chloride, while the former are preferable, since they are 4 times stronger glued and better protect pipes. More often, sticky PET tapes are used for repair and insulation of joints of pipes coated with extruded polyethylene, but there are also pipes wrapped by them at the factory along the entire length.

There is also a combined PET coating in which the primed pipe is first wrapped with adhesive polymer tape, and over it is protected with a layer of extruded polyethylene. It is used on pipes with a diameter of up to 53 cm, and the total thickness does not exceed 3 mm.
Bitumen mastic insulation
Such insulation is fundamentally different in composition and properties, primarily in the method of application. The adhesion of bitumen to both the pipe and the layers between themselves is ensured by heating and melting of the material itself, and not by an adhesive primer, as in the case of PET.
Such a coating is applied to a special bitumen primer, and consists of 2 -3 layers of mastic, each of which is reinforced, and an external paper protective wrapper. As a result, a continuous coating is formed that completely repeats the shape of the pipe, where the reinforcing fiberglass or mesh is soldered into the thickness of the shield.
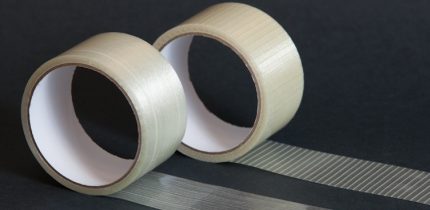
In addition to bitumen, mastic itself contains various inclusions - polymer, mineral or rubber - providing different material properties. Also, modifying additives and plasticizers are added to it, which add elasticity, flexibility, resistance to critical temperatures and durability to natural hydrophobicity and adhesion.
There are also tapes connecting bitumen as glue and special polymer tapes. The main 2 types of such coatings are PALTwith heat-shrinkable tape, and LITKOR, from a polymer-bitumen tape. The latter, in particular, is necessary to protect the connections between pipes with different types of insulation.
Materials for insulation of small elements
Base terminals, corners, elbows, condensate collectors and other shaped elements of gas pipelines also need protection.
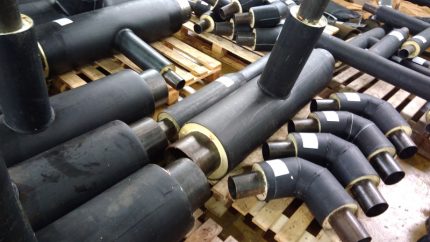
There are special coatings for this: PAP-M105 and Half. The first is two layers of cured glass fiber reinforced polyester resin.
Semiur consists mainly of polyurethane, supplemented with technological additives and divided into the main component and hardener. Using these two compounds, molded joints are isolated at the factory, in the workshops, and directly on the track.
How is insulation applied?
The main part of the insulation is applied to gas pipes, and often on the fittings of the gas pipeline, in the factory, even at the stage of their production. However, during the installation of the pipeline, it becomes necessary to insulate the joints, which is carried out under route conditions - that is, directly at the installation site.
In addition, in the field, the same materials are used to repair the protective coating, if not more than 10% is damaged, and occasionally even a complete re-isolation of a separate area. Also manually, directly on the highway, insulate tanks.
If possible, the welds and fittings are insulated with the same coating as the main pipe - or as similar as possible.
Insulation of the gas pipeline is possible at temperatures above -25 ° C, and for polymer adhesive tapes - above +10 ° C. If it is raining or snowing, there should be a reliable overhang over the work site, which will make it impossible for rain to fall on the insulated surface.
On pipes of an overhead gas pipeline
This type of gas pipeline is located in the least aggressive environment, and therefore the risk of rust is significantly reduced. In addition, it is much easier to notice and repair the damage on it, therefore, isolation of overhead gas pipelines as such is not required.
To protect against precipitation and atmospheric moisture, according to the standards, a coating of 2 layers of primer and 2 layers of paint, enamel or varnish is sufficient.
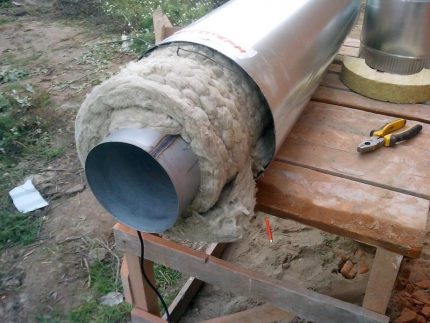
However, in case of difficult operating conditions, thermal insulation of gas pipelines is applied - greases, glass-enamel coatings, as well as aluminum or zinc casings, which should not touch the pipe itself.
Underground gas pipeline insulation
In the ground, pipes are constantly exposed to moisture, and often chemical compounds and stray currents. All this can lead to metal corrosion and gas leakage, so they try to provide insulation as reliably as possible.
Each underground steel gas pipeline is doubly protected: passively - with an insulating coating of the pipe, and actively - through the removal or suppression of current by cathodic protection.
Most of the materials that we talked about earlier can be used both for basic, factory insulation, and on the track. We will discuss the main stages and subtleties of such work further.
Polyethylene and polypropylene insulation at the plant is implemented in several stages:
- Pipe drying.
- Blast cleaning to a metallic luster.
- Pipe heating.
- Application of a glue base on a rotating pipe.
- Application by extrusion, stocking or winding of a tape of a polyethylene layer.
- Sealing with a special roller with a fluoroplastic shell.
- Water cooling to 70 - 80 ° С.
- Quality control of the resulting coating.
All processes are fully automated, because computer accuracy is the key to product quality.
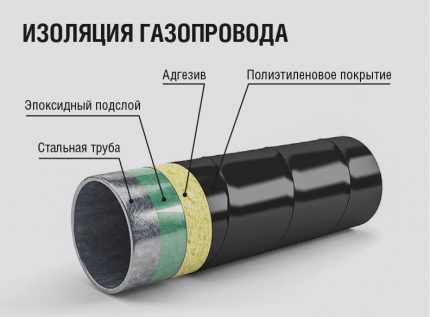
In the field, all stages must be preserved, but implemented at the expense of portable equipment - grinders and sandblast cleaners, gas-burners and blowtorches. In addition, there are special sets of materials for insulation of joints and repair of damage - for example, shrink PET cuff or adhesive polymer tape.
To apply bitumen insulation, the pipes are also cleaned, but with the help of metal brushes, leaving a clean but not smooth surface. The primer, consisting of bitumen and gasoline, is poured onto the cleaned pipes and rubbed with towels, and in the conditions of the route with rags or brushes.
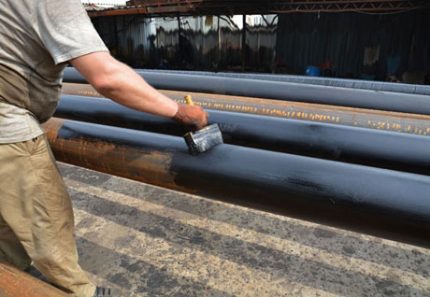
No more than a day later, it is necessary to apply the main coating: 2-3 layers of mastic, separated by reinforcing material and protected from the outside with a layer of paper.
For reinforcing use fiberglass, non-woven polymer fabric or mesh. They are wound spirally, evenly, with a slight tension and overlap.
Field Insulation
If it is necessary to repair damage to the insulation of an underground gas pipeline, or to connect pipes with different types of insulation, it is important to choose the materials used correctly.
PALT and LITKOR coatings are used only in highway conditions. Both are applied to the bitumen primer, but for the first one it is necessary to first apply a layer of bitumen and reinforce it, and then wind the tape directly onto the hot mastic. In the second case, bitumen is the lower layer of the tape itself, so it is immediately wound on the primer, previously melted with a burner.
Despite the resemblance, you should not confuse Litkor tapes with sticky PET tapes, because the use of an inappropriate primer will hopelessly ruin the quality of the insulation.
Pipes with extrusion PET coating are repaired with special heat-shrinkable patches or LITKOR bitumen-polymer tapes. When factory coated with adhesive PET tape, it is used for repairs, such as Polyethylene. This is only possible in the warm season, because the tape does not stick in the cold and does not tolerate melting.
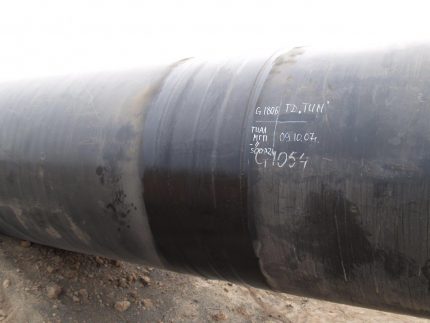
The bitumen coating is repaired with the same bituminous mastics with reinforcement, bitumen-polymer tapes LITKOR or similar roll material Isoplast-P.
It is always possible to connect different pipes in absolutely any combination with LITKOR tapes, and if there is no bitumen in the native coating of both pipes, then direct connections can also be insulated with Polyethylene adhesive tapes.
Pipe insulation under water
Gas pipelines that will serve on the seabed are especially insulated, because this environment is dangerous both by chemical and mechanical damage, and pipe malfunctions, as a rule, indicate interruptions in international gas supplies.
The main part of the pipe protection is obtained at the factory. After cleaning and drying, they are opened with an epoxy compound, then an adhesive is applied, and a plastic layer is applied over it. At this stage, the pipes are similar to similar pipes, except for the first epoxy layer, which is duplicated on the inner surface.
However, this is not all: cathodic protection is already installed on the prepared pipes at the plant, and then a reinforcement cage is built and the outer concrete layer is poured, often with iron ore as a filler.
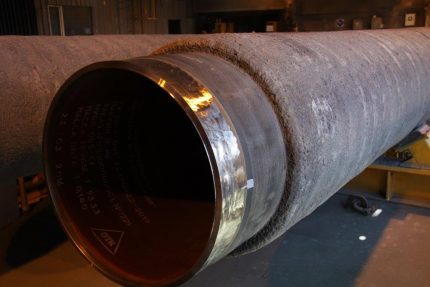
As a result of such a multilayer finish, the weight is 1 mp pipes can reach 2 tons. It is very problematic to transport such tubes, therefore they are not produced too long, and for every kilometer of the offshore gas pipeline there are several tens of welds, each of which must be reliably insulated.
Connection and isolation of joints takes place on a special barge equipped with everything necessary. Here the pipes are welded, the seam is carefully cleaned using a shot blasting machine. Trunk pipes They have a huge diameter, so they are heated with induction rather than propane burners - it turns out faster, more uniformly and safer.
Then a primer is applied and a heat-shrink sleeve is installed, fixed with a lock plate. The cuff warms up first in the middle, along the weld, and then gradually shrinks with the help of gas burners all from the center to the edges. After quality control of this stage, a lining casing is installed for filling the foam. After it dries, the pipe is lowered to the bottom and covered with gravel.
Insulation Quality Check
The protection of steel gas pipelines is a responsible measure, therefore, each operation performed must be carefully checked, with the preparation of an act of hidden work performed and their entry in the pipeline passport. No matter how high-quality and correctly selected the insulation material, it will not cope with the functions assigned to it if the technology of the work was violated.
The main parameters of the finished coating to be checked are the thickness, continuity and adhesion to the pipe. Measure them with special electronic devices: thickness gauges, spark flaw detectors and adhesimeters, respectively. They do not damage the coating, so they allow you to control all dubious points without unnecessary costs.
In the factory
At the plants and production bases, the coating thickness is checked for 10% of the pipes of each batch, in 4 places on different sides in a circle on each pipe, as well as in questionable areas.
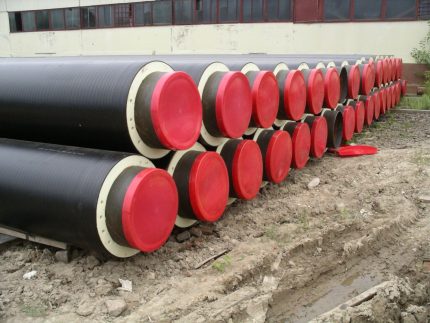
The adhesion, or the adhesion force to the metal and between the layers, the standards also require checking for 10% of the production in the party or every 100 m.
The continuity of the coating, that is, the absence of punctures, bullying and other end-to-end violations, is checked on all isolated products throughout the area.
In addition, the dielectric continuity of the coating, impact strength, peeling area after cathodic polarization and other tests can be checked. When insulating with bituminous coatings, a sample for physical properties is taken from each batch of mastic, at least daily.
At the place of installation or repair
In route conditions, the quality of insulation is also checked, for continuity - always and completely, and for every 10th insulated weld for thickness and adhesion.
In addition, the overlap width on the factory coating is checked, as well as the insulation relief - for the absence of corrugations, wrinkles, airbags and other defects.
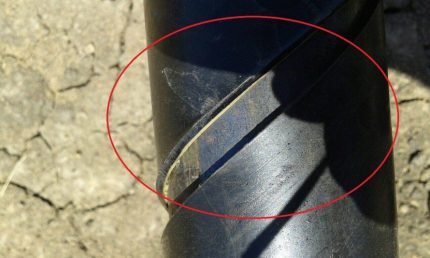
In addition, the continuity of insulation is regularly checked on existing gas pipelines. To do this, they do not even need to be dug out, and if there is a suspicion of damage, the pipes are exposed and not only the thickness, continuity and adhesion are checked, but also the dielectric properties of the insulation.
Conclusions and useful video on the topic
Now you know everything - or almost everything - about the purpose and materials for insulation of various steel gas pipelines, and also have an idea of the features of their application and quality control of protection.
And for greater clarity, we offer to watch a video, which details the insulation of welded joints with a bitumen-polymer tape:
Installing a heat shrink sleeve on the weld:
Perhaps you have already encountered similar works, watched their progress or were directly involved. Please complete or rate the information provided. We will be happy to know your opinion in the discussion below.