How to make rings for a cesspool of concrete or plastic
Doing something with your own hands is a fascinating task, especially if you end up with something to be proud of. In addition to moral satisfaction with the results of your efforts, you can also save well by making rings for the cesspool in your area.
It’s easy to find materials for this, and the result depends only on strict adherence to technology. Therefore, in this article we will talk about how to independently make rings for a cesspool, and what is required for this.
The content of the article:
The technology of manufacturing rings from concrete
To make a home septic tank serve for many years, it is better to make it not from brick, but concrete rings. Buying them is not difficult, but in order to make them yourself you do not need to be a great professional.
It will cost less, and you don’t have to adapt the cesspool to the standard size, when you can choose any convenient designer for yourself.
Getting to the implementation of the plan, you must first decide on the place - choose a fairly spacious and flat area. A lot of concrete mix will have to be prepared, so a concrete mixer will be required.
Since the products are heavy, when moving them can not do without lifting devices.For molding rings need special forms.
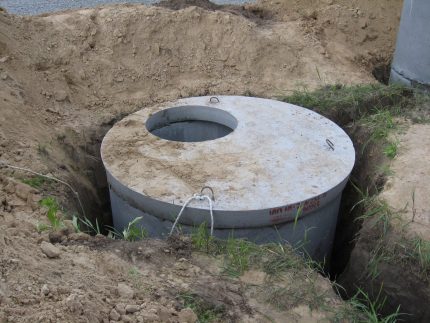
Molds for making rings
The shape for the rings has a simple geometry: a pair of cylinders - internal and external. The diameter difference should be equal to the wall thickness, and this is about 1.5-2 cm.
You can get them in many ways. The easiest way is to buy a factory product with an inner cone-shaped core and an outer ring, reinforced with stiffeners and a vibrator mounted on it.
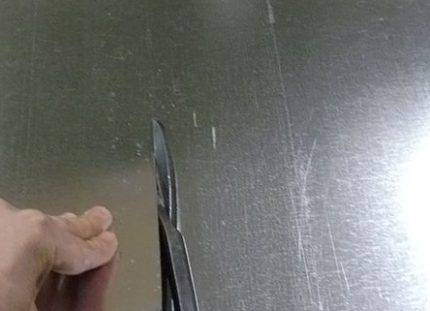
After installing this form on a flat platform, reinforcement is laid in it and pour it with a solution. Shrinkage of the mixture at each stage of filling will provide a vibrator. This prevents the formation of air pores in the body of concrete walls. Reinforcement - an operation is not necessary, but desirable, since the product is stronger.
Even easier - take 2 metal barrels with suitable parameters or pipes. It is possible to make cylinders from sheet metal. Sheets are interconnected by canopies - door or window. The most affordable way - making molds using planed boards.
Making molds from boards
To make such a shape, boards from 2 to 5 cm thick will be required. The outer and inner cylinders are made collapsible, consisting of several wooden rings. Well-crafted boards are stuffed on the rims for the outer cylinder.
The inner cylinder must also be easily assembled and disassembled. They make it, according to the same rules as the outer part of the form, but sheathed not by the inner, but by the outer diameter. After assembling the mold, a gap of 1.5-2 cm should remain between the cylinders.
To obtain the product with the required parameters, you must first calculate the dimensions of the form. Suppose, for a cesspool, rings with a diameter of 840 with a wall thickness of 140 mm and a height of 890 mm are needed. To calculate the inner diameter use the formula: Dv.n. = D + 2h, where D = 840 mm, h = 20 mm (thickness of the cladding board).
These values are substituted into the formula: Dv.n. = 840 + 2 x 20 = 880 mm. If we take the width of the ring equal to 100 mm, then the diameter of the ring on outdoor = Dn.v. + 2S = 880 + 2 x 100 = 1080 mm.
Given the fact that you need to make a ring with a wall thickness of 140 mm, the outer diameter of the wooden core is: Dн.в. = D - 2B - 2h. Here D is the diameter of the product, B is the thickness of the finished ring, h is the thickness of the board. Dv = 840 - 2 x 140 - 2 x 20 = 520 mm.
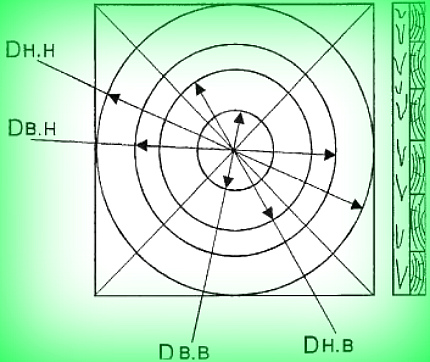
If in the formwork being manufactured the width of the inner wall ring is also equal to 100 mm, then the core should have an inner diameter of Dv.v. = Dn.v. - 2S = 520 - 2 x 100 = 320 mm.
Express instruction for filling rings
The process of manufacturing concrete rings with pouring mortar into the formwork made of the board, the steps will present the following photo selection:
The above steps were essentially preparation for the filling work. Now you can proceed to the direct manufacture of concrete rings:
Production of reinforcement belts
It will be necessary to prepare round ribbed steel with a thickness of 0.8-1 cm, from which a reinforcing ring is knitted.
Rings, the number of which depends on the height of the product, are interconnected vertically using segments of reinforcement. It is advisable to maintain a distance between reinforcing belts of about 25 cm. It is recommended that a step of 35 cm be observed between reinforcing pieces installed vertically.
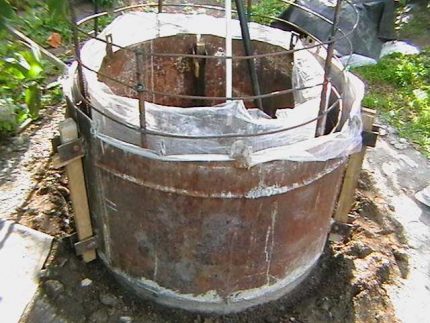
For the convenience of transporting the finished product upward of the reinforcement cage, a workpiece is tied in the form of wire loops. You can also use steel mesh with a minimum thickness of 0.4 cm for the reinforcing cage. A ring is formed from it and the edges are fixed with a wire.
Concrete pouring
You can start manufacturing rings at a temperature not lower than 8 and not higher than 22 ° C. Formwork elements are inserted one into the other, having previously been lubricated with machine oil - this will subsequently facilitate their dismantling. In the gap between the cylinders insert the frame from the reinforcement.
To give stability to the reinforcement, it is fixed with wedges. Subsequently, the wedges are removed as the mold is filled with concrete.
Prepare a solution in the following proportions:
- Fresh cement not lower than M400 - 1 part.
- Granite or limestone crushed stone with low-rounded grains no larger than 0.2 cm in size - from 4 to 5 parts.
- Quartz sand with a grain size of 0.22 cm maximum - from 2 to 3 parts.
- Water - a maximum of 0.7% by weight of cement.
Specialists have their own secrets of preparing a concrete mixture. Sometimes they add potassium glass to it in order to increase the water resistance and plasticity of the mass. To increase the strength of the composition, a component such as PVA glue is introduced into it. The fluidity of the mixture is increased by adding detergent.
It is important to immediately spend the prepared concrete, therefore it is better to immediately calculate the right amount of mix for one pour.
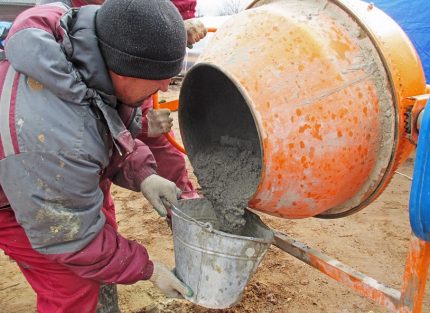
By eye, stiffness can be determined by placing the mixture on a horizontal plane. If it tends to drain quickly when tilted, the mixture is very liquid. The average plasticity of the mixture is indicated by its slow sliding.
When the mixture is stuck and does not slip, it means that it is slightly plastic, and if the mass does not even change its shape and remains lumpy, this indicates its rigidity.
To navigate in such a matter as selecting the number of components needed to prepare 1 m 1 of concrete, you can use this table.
Brand solution | Cement M 400 (kg) | Crushed stone (kg) | Sand (kg) | Water (L) |
75 | 170 | 1053 | 945 | 210 |
100 | 210 | 1080 | 870 | 210 |
150 | 235 | 1080 | 855 | 210 |
200 | 286 | 1080 | 795 | 210 |
250 | 332 | 1080 | 750 | 215 |
300 | 382 | 1080 | 705 | 220 |
Since the rings for the cesspool are reinforced, concrete of little stiffness is more suitable here. When using Portland cement M500, the norms for M400 are multiplied by 0.88. For other brands take other factors.
Having prepared a mixture that resembles a thick dough in consistency, the first layer is sent to the formwork with a thickness of about 10 cm. Then the beating is performed: a steel rod with a diameter of 20 mm is taken and the material is carefully compacted.
In this way, fill the entire volume between the two cylinders. Having completed the work, they close the product from direct sunlight, throwing on top a piece of dense fabric.
The formwork is removed after an incident of 14 days, left in the same place for another 4 days, not forgetting to periodically water it. If filling is performed with a less thick mixture, then the process is called casting. Formwork from products obtained by the second method is removed after a week.
Shells will remain on the surface and fill them with cement mortar. On products made by the second method, fewer shells are formed.The oil that covered the surface of the cylinders is removed. More tight connection of rings provides the lock.
To get this element, 2 more rings are added to the mold, forming a compatible mounting chamfer in the form of a protrusion on one product and a neck on another. This will allow you to firmly fix the rings during installation, protecting them from displacement.
A known method of manufacturing rings, excluding from the process such a time-consuming operation, as transportation of the finished product. For this, a mold for the ring is made at the place where it is subsequently supposed to dig a cesspool. First, the ring is cast, and then soil is selected under it and gradually lowered to the bottom, completely immersed in the pit.
When the upper edge of the product is flush with the ground, a new formwork is built on it. Make the next ring and again select the soil until the edge of the product is flush with the ground. Continue to make new rings until the desired depth of the cesspool is reached.
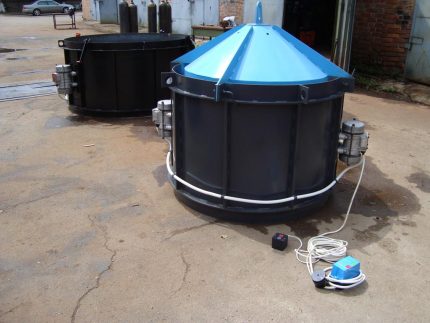
The highest quality products are obtained if it is possible to use the technology of vibrocompression, which provides for the installation of the mold on a special vibrating plate with a drive.
The slab performs oscillatory movements of small amplitude and high frequency, which allows to maximize compact the concrete mass.
The use of plastic rings
Advantages of plastic rings for a cesspool in their small weight, durability and ease of installation. For their manufacture, the starting material is low-pressure polyethylene, which is characterized by excellent strength characteristics.
The most common size is a height of 150 cm, a diameter of approximately 95 cm, a wall thickness of 25 cm.
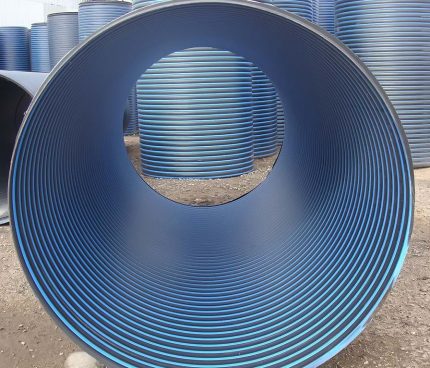
The ring, without harm to its integrity, perceives large mechanical loads due to the ribbed body. For one cesspool, as a rule, no more than 3-4 rings are required that perform the function of the walls.
For the bottom and top of the cesspool, other details are used: the bottom, the hatch, the ring to frame the hole, which is used to connect to the sewer.
If you compare plastic rings with concrete ones, in addition to low weight, you can see a number of other advantages of the former:
- Quick installation using your existing lock system.
- Ease of dismantling.
- Complete tightness.
- The ability to replace a failed ring.
- No reaction to moisture. Plastic will never get wet and will not corrode.
- Neither aggressive chemistry, nor waste products living in waste and soil, bacteria influence plastic.
- Smoother inner surface, not contributing to the accumulation of plaque on it.
Affordable price.
The light weight of the structure can sometimes cause its displacement under the influence of groundwater.To prevent this from happening, when pouring the bottom of the pit, special metal hooks are inserted into the concrete screed. Using these devices, light plastic rings are securely fixed.
And how to waterproof a septic tank with a plastic insert can be found in this stuff.
Sometimes the first ring is lowered into the cesspool on an still unfinished screed. This is much easier than fixing it with hooks and cables. There is a negative side to this - you will have to make great efforts if you need to dismantle the structure.
Having decided to make a cesspool of plastic rings, you need to decide on a place for it.
Sanitary standards regarding the location of any septic tank are the same:
- at least 5 m from the front door of the house and windows;
- not less than 3 m from the road and the boundary with the neighboring section;
- 15 m or more from a well or well with drinking water;
- the availability of access to the work of a cesspool machine;
- lack of fruit trees near the pit.
The next step is to determine the volume. The basis is the daily water consumption for 1 person living in the house. The generally accepted norm is 200 liters. A pit is torn out, a concrete screed about 200 mm high is arranged at its bottom, strictly controlling horizontality.
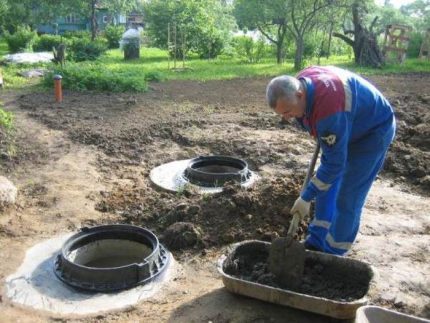
Between the walls of the dug hole and the corrugated surface of the rings, a gap of at least 30 mm should remain. From the bottom side, 20 cm of reserve is also left. If the bottom of the cesspool is not planned to be concreted, this parameter is increased to 0.5 m.
When the last option is selected, it is necessary to arrange a filter layer consisting of gravel and sand, separated for the impossibility of mixing them, with geotextiles. In the manufacture of plastic rings, their design already includes thermal insulation in the form of a longitudinal-hollow layer, but if severe frosts are observed in your area in winter, additional insulation will be useful.
To install a heat-insulating layer, it is necessary to take a panel of reflective material with such dimensions that, after lowering the rings, the entire surface of the pit is covered. Material with a reflective layer will not allow heat to escape into the ground. Its edges are fixed along the perimeter of the top of the pit with twine.
The rings themselves are dipped alternately using cables. A small effort is applied to each of them to connect with the previous one. For this design, special grooves are provided.
The cable with which the rings were immersed is tied at one end to a metal hook immured into the formwork, and the other is thrown onto the opposite side of the pit and fixed there. Get an additional strengthening of the rings.
Now you can start backfilling the tank. Usually, the earth is poured from the outside of the rings. But if the groundwater is high, a mixture of cement and sand in a ratio of 1: 1 is placed in the gap between the tank and the pit.
Simultaneously with this operation, it is necessary to add water to the tank, making sure that the level of the poured earth is 200 mm lower than the water level. If this is not done, cracks may appear on the plastic under the influence of the pressure created by the soil.
It remains to cover the pit airtight hatchthat protects the cesspool from rainwater entering it. In addition to the hatch with a diameter of 0.7 m, you need to install a ventilation pipe with a cross section of 100 mm, which will exhaust gases from the pit.
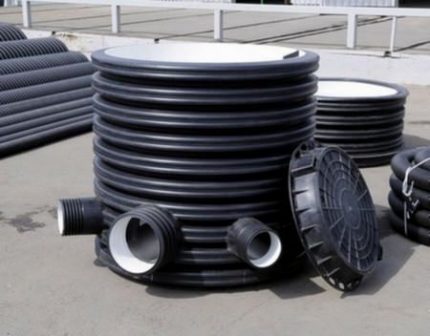
To clean sewage, you can buy a special tool containing living bacteriathat feed on organic matter and process it to a more liquid state.When there is no bottom in the cesspool, most of its contents will go into the ground. In a closed cesspool, more waste accumulates, so it has to be pumped out often.
Conclusions and useful video on the topic
Here you will see how concrete rings are made in a suburban area:
In this video, we will talk about the manufacture of demountable forms with which concrete rings are formed:
Following the recommendations given in the article, you can make rings for the cesspool yourself. If this process seems to you very laborious, you can always buy concrete rings or plastic. As for their installation, then in this matter our article will be useful to you.
Do you have questions about the topic of the article? Or maybe they themselves have built concrete rings for a septic tank, and can you give practical advice to our readers? Leave your comments, upload photos of homemade products, share your manufacturing secrets in the block under the article.
I had problems with money. It was not possible to hire specialists who would do everything for me. Therefore, guided by the Internet, I tried to organize everything myself. He took the forms for rent, they didn’t give me a lot for acquaintance. In principle, nothing complicated, knead the solution, pour into a mold and wait until it hardens. Well, then instilling these rings is generally straightforward. I don’t trust plastic rings.
If you make the rings yourself without a vibrating press, then another simple option is possible. For the mold, only the inner cylinder is made. It is placed in a pit, which is 20-30 cm wider than the cylinder. The solution is poured into the space between the cylinder and the earthen wall. After solidification, the inner cylinder rises higher and the process repeats. So that the enclosing soil does not take water from the solution, cellophane is laid on the outside.