Repair of a gas boiler Vaillant: decoding of encoded irregularities in work and methods of dealing with problems
The gas equipment brand Vaillant, designed for heating systems, a lot of weighty advantages. Among them, high-quality assembly and the use of reliable components that ensure proper operation are leading. However, the resource of any equipment is not unlimited, and non-compliance with the rules does not affect the condition of the unit in the best way.
Even the most trouble-free appliances gradually wear out and become unusable. All about how to repair gas boilers Vaillant, you will find in our article. We will tell you how to identify a violation, identify a coding error and eliminate the cause of the breakdown.
You will receive detailed information about all types of damage and malfunctions characteristic of heating devices with the Vaillant logo. You will learn how to distinguish data on the state of the boiler from information on brewing or already formed defects. Our recommendations will help with preventative maintenance.
The content of the article:
Benefits of a self-diagnosis system
Vailant gas heating units are quite justified among the owners of country houses and apartment owners from the old housing stock. Reliable boilers rarely break, do not cause inconvenience to the owners, do not let the owners in the heating season.
The German company offers domestic consumers a wide range of boilers of traditional and condensation type. The range includes floor and wall models, atmospheric and turbine equipment of various capacities. A wide range of offers allows you to choose the right option for both the type of performance and power.
A significant advantage of heating equipment from a German manufacturer is the self-diagnosis system. A simple set of letters and numbers in the development provides the opportunity to timely identify violations and quickly correct the situation.
Let's work together to understand the hints encrypted by the manufacturer and what should be done to restore the boiler.
Error Warning Levels
To identify malfunctions and monitor the state of gas boilers, the manufacturer has developed a unique warning system. All information displayed on the unit display is divided into two groups. The first of them is designed for owners ignorant of the intricacies of the gas economy, the second - for the masters of service departments.
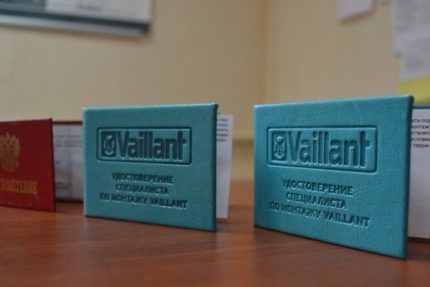
The principle of this division is justified by the level of the potential repair contractor. After all, not only the manufacturer of Vaillant boilers, but also all his “associates” warn that not all repair operations can be carried out by the owners of the units with their own hands. There are breakdowns, with the elimination of which an independent home master should not get involved at all.
The point is not even that after the intervention of an independent craftsman, the warranty obligations are automatically canceled. It is important that the gas equipment and the fuel processed therein are explosive, toxic, and fire hazard due to illiterate handling. And the result of the repair performed by the amateur is able to combine all of the above risks, adding to them damage to neighbors.
Given the above reasons, the diagnostic system is divided into two parts. The first part is available to the owner of the boiler. Guided by the information encoded by the manufacturer, the owner can eliminate the malfunction by methods available to him.
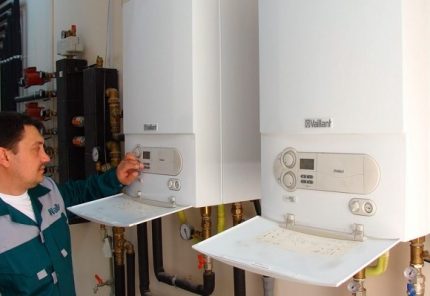
The second part of the encoded information about equipment errors is available only to gas workers, with whom the owner of the equipment must enter into a contract before installing the unit. According to the contract documentation, fuel is delivered, technical condition is monitored and repairs are carried out.
To access the second part of the error data, the gas service master enters a password that is unknown to the owner. It would seem that the owner does not need information about these errors at all, since all the operations behind this “barrier” are still inaccessible to him.
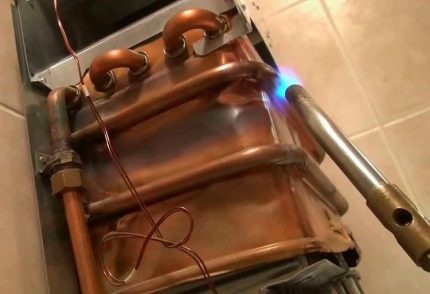
But! Recall how much money we invested in the organization of heating. Let’s think that a substantial amount was paid for the acquisition, connection, installation. And we will make sure that all work to restore the functioning of the unit is carried out in accordance with the manufacturer's instructions. Therefore, we find out what should be done when an error code appears on the display.
How to monitor the condition of the equipment?
In order to get information about a malfunctioning or already occurring malfunction, you need to use the diagnostic programs indicated by the company's programmers in the menu with a range from P.0 to P.6.
Entrance to the information system is as follows:
- We find two buttons on the control panel. On one of them should be an “i”, on the second “+”.
- We simultaneously activate both buttons. Hold them until “d.0” appears on the screen.
- Using the buttons with the signs “+” and “-”, we advance in the list of faults in order to reach the desired item in the diagnostics. We confirm what was found by pressing the “i” button, we get acquainted with the information presented by the system.
Note that entering the diagnostic mode even the first level allows you to change the settings. It sometimes happens that a bypass boiler is blocked, for example, due to a too high temperature set during setup before the first start-up. In solving such problems, it is not necessary to resort to the help of a master.
The operating parameters are changed by manipulating the buttons “+” and “-” already known to us. All changes should be fixed. New data is recorded when you press the button with the “i” icon and then holding it for 5 seconds to a minimum.
If the information provided by the boiler and the steps described in the manufacturer's manual do not lead to the desired result, call the wizard. He enters a password, which opens the next level of diagnostics. A certified repairman can see all the information about the errors in the Vailant gas boiler and all the codes assigned by the manufacturer.
In addition to errors of both levels, a high-tech system can notify about the technical condition of the unit. In this area, division is also provided. Status data is encoded with an alphanumeric combination starting with the letter “S”, error information begins with “F”.
Level 1 Problem List
For starters, consider what the owner will be able to "fight" on their own, without fear of receiving the complete unsuitability of the product and the deprivation of warranty.
In the list of situations available for correction, two options appear:
- The boiler does not work at all. Those. the device does not heat the coolant if it is single-circuit; it does not heat either the coolant or sanitary water if it is a dual-circuit model.
- The boiler heats the sanitary water, but does not heat the coolant. This problem is peculiar only to dual-circuit units.
Both of these positions have a number of completely removable causes and several solutions, which should be familiar to the prudent owner. However, before a detailed study of the situation, you should check whether the boiler is connected to the network at all and if one of the functions is turned off: heating or hot water.
Now let's look at typical causes and methods for eliminating them in case the boiler does not heat at all:
- The gas cock is closed. Both locking devices installed by gas workers at the gas inlet pipe must be opened.
- The supply of cold water is shut off. It is solved by opening the stopcock on the water pipe.
- Violations with power supply. The heating unit will interrupt operation if there is no power. If the power supply is restored, the boiler will start itself.
- The temperature is set too low. The owner of the boiler corrects the mistake made during the settings by trivial transfer of the unit to the required temperature regime.
- Water pressure drop (F22). The lack of pressure in the system for normal operation of the boiler will be reported by the encoding. Its appearance means that it is necessary to bleed air from the batteries and open the make-up valve located at the bottom of the device.
- Failure to light up (F28). If the third attempt to ignite the gas heating equipment did not lead to the intended result, you need to find the malfunction removal button on the control panel, press it and hold the position for at least a second. Failure again? Call the gas men.
- Chimney malfunction (F48). This signal indicates an increase in temperature of the exhaust flue gases. They could stagnate and overheat due to a clogged external chimney, which must be cleaned.
Note that the pressure drop is also signaled by indication S76. This code is from the boiler status monitoring group. However, to restore operation, the same actions will be required as when fixing error F22.
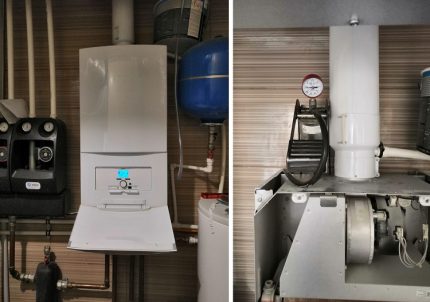
The second type of violations, determined by the operation of only DHW without heating coolant, is most often associated with the wizard errors made during the settings. You can change the temperature yourself. The manual attached to the boiler describes in detail how to perform this operation.
Second level error list
Now we will analyze the problems that only the master from the service department can decrypt. To control the actions of the contractor, if you are dear to a completely expensive unit, is also extremely useful. Especially if the repairman at first glance does not inspire due confidence.
Immediately make a reservation that if a dash is induced on the display, then there are no violations in the functional, most likely, the incorrectly set settings are disturbing. If several codes are displayed alternating with each other, then there are several violations. This means that the master will have to choose the correct sequence of troubleshooting.
Error F.0. Problems with the NTC temperature sensor located on the supply line. The reasons for the fact that the device has ceased to record the temperature are several. The sensor could fail by itself, or the electrical connection may be broken.
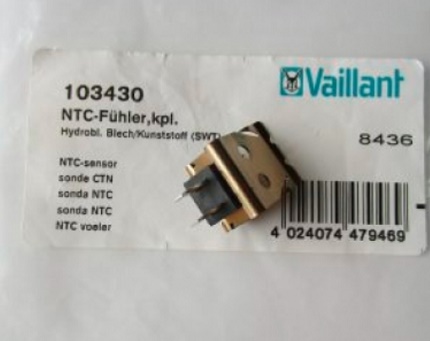
In all cases, the boiler is disassembled to detect violations. If a weakening of the plug connection with the electronic board is detected, it is restored. If a replacement device or wire is required, it is produced.
Error F.1. Problems with the NTC temperature sensor mounted on the return pipe. All actions taken to eliminate the previous error are performed in the same order.
Error F.5. Failure of the flue gas sensor outside the boiler. By analogy with the previous errors, you need to check the plug connection with the electronic board and ring the wiring. If the cause was not found as a result, you will have to change the sensor.
Error F.6. Opening the flue gas sensor within the boiler. They also check the cable, cable connections, plug-in connection with the electronic board and the device itself. Based on the results of the identified failures, contacts are restored, the wire or the recording device itself is changed.
Errors F.10; F.11; F.15; F.16. Short circuit: errors 10 and 11 - short circuit of the temperature sensors at the supply and return, codes 15 and 16 - short circuit of the flue gas sensors from the outside and from the inside. When registering the short circuit of all the listed types of sensors, they are replaced.
Error F.20. Temperature fuse tripping. It is necessary to check whether the temperature sensor is correctly installed and connected on the supply line. Most often, the fuse blows without a real reason if the assembly of this section of the circuit was not performed correctly. Less commonly, this happens due to a sensor breakdown.
Error F.22. Dry boiler operation or lack of water in the unit. This is a signal that there is a leak in the device or that the pump cannot handle the transfer. However, if a leak is not detected, then the whole problem is in the pump: either it is broken, or the electrical connection is damaged. The problem is solved by replacement.
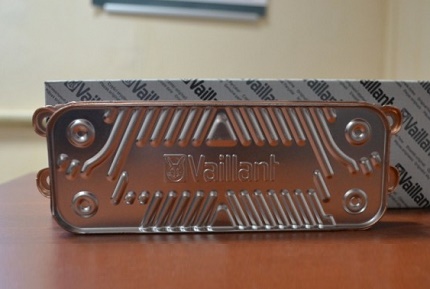
In addition, a device that could block the operation of the boiler when the temperature limit was exceeded could break. It does not make sense to repair it; as a rule, this type of switch is replaced.
Error F.23. The readings taken by temperature sensors at the inlet and outlet of the boiler vary greatly. It occurs most often due to insufficient volume of water in the unit or its too slow movement. The pump is to blame - it is either broken or blocked.
Error F.26. The fuel flow supplied by the gas valve of the stepper device is not determined. In this case, the problem must be sought in the wiring of the gas valve or in the electrical circuit used to connect it. There may be no contact between the stepper motor and the electronic board.
Error F.28. It is impossible to ignite the boiler, even after numerous attempts, the unit does not start. The most common causes of problems include irregularities in the system of gas supply to the combustion chamber. It is necessary to check the gas valve, it is possible that it is simply incorrectly configured, and not broken.
A company supplying gas to a consumer in accordance with a concluded agreement may fail. Too much air may be in the blue fuel, the proportion of which exceeds the norm for burning. It is possible that fire protection worked.
If everything is in order with the gas supply system, problems should be sought in the gas supply valves. It is necessary to check the electromagnetic valve, the ignition device, including its plug, the transformer, the wiring used in the connection and its terminals. After making sure that the listed devices are working, they begin testing the ionization cable and the control board.
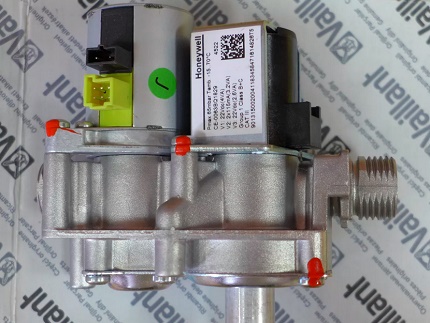
Error F.29. The flame went out during heating of the coolant, after which the unit does not ignite at all. In this case, the ignition transformer interrupts the supply of fuel. It must be checked, cleaned, or replaced. Also worth checking out boiler grounding: is it arranged and how correctly is everything done.
Error F.36. The boiler is blocked by an exhaust gas sensor. First of all, it is necessary to check the chimney duct, if necessary, it must be restored or cleaned. If there was no congestion or a strong narrowing in the channel due to growths of burning, it means that the sensor itself or its connection to the electric circuit is faulty.
Error F.49. Voltage drop on the electronic bus. This is the result of a short circuit on the bus or the connection of two different-polarity sources to it.
Error F.61. Problems with gas valve control. Occurs due to a short circuit in the electromagnetic part of the gas valve or due to a short circuit in the cable insulation. Another cause is a malfunction of the electronic control device.
Error F.62. Change the delay in activating the gas valve. Consequently, the tightness of the valves supplying gas and regulating its pressure is violated.
Error F.63; F.64. Damage to the electronic board or sensors connected to it. It is necessary to check the sensors connecting the wiring to the board and the electronic board itself.
Error F.65. Heated electronics. Too high temperature of the electronic control device is due to the proximity of the heating devices or because of the failure of the electronic board. Between the electronic control system and any equipment that generates heat during use, the distance specified in the device manual must be observed.
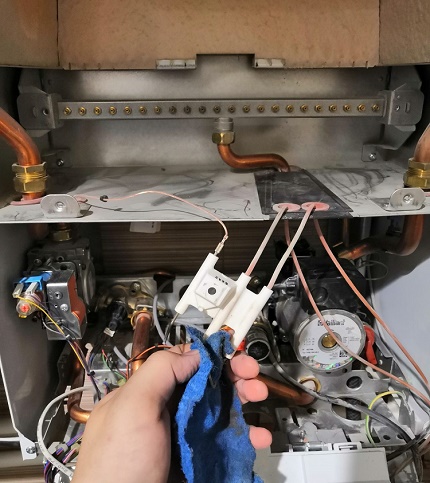
Error F.67. The ionization device does not work. Traditionally, the device itself, the electronic board and the electrical circuit connecting them are checked.
Error F.70. Not all functions are displayed on the electronic board and / or display or not at all. It is solved by replacing the wrong option.
Error F.71; F.72. The sensor values for the flow and discharge lines are incorrect. Check sensors, electronic circuit board, wiring, and electrical connections.
Error F.73. Demonstration of incorrect data by pressure sensor. The pressure sensor itself is broken or the electrical circuit between the board and the device that fixes the pressure values in the system is broken.
Error F.75. Lack of response of the pressure sensor to pressure fluctuations. If the sensor does not react in any way to a sharp increase and drop in water pressure, it means that it is faulty and will have to be changed. True, it happens that the reason is not in it, but in the circulation pump, then you will have to change the pump.
Error F.77. Damage to the exhaust gas damper. There is a slight smoke in the room with the boiler. You should immediately arrange a volley ventilation and call the wizard to check the device and carry out repairs.
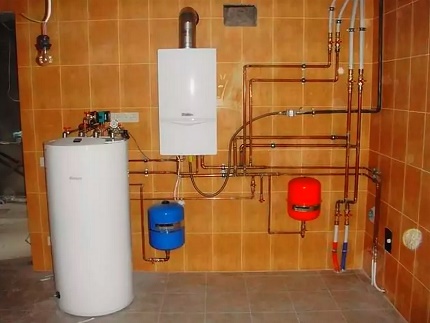
We considered only violations in the operation of atmospheric boilers. The error lists of traditional turbocharged and condensate models are slightly different, which is justified by the difference in design solutions and differences in the principles of operation. A complete list can be found in the briefing for certified gas manufacturers accredited to carry out repairs.
An important advantage: all Wilant boiler models are equipped with the so-called “error memory”. It displays ten extreme violations in operation, recorded by the boiler electronics. You can find this position in the board menu by simultaneously pressing two buttons “i” and “-”.
If, after reading the information about violations, do not press any of the keys for 4 seconds, the boiler electronics will automatically return it to its previous operating mode.
Conclusions and useful video on the topic
Video clip with F.75 error correction analysis and visual representation of the unit components:
Video repair manual for the boiler control board:
Valuable recommendations of an experienced owner to transfer the boiler to work in accordance with the season:
In order to be less likely to encounter equipment breakdowns, you must clearly follow the manufacturer's instructions, which are thoroughly spelled out in the manual attached to the product. Compliance with operational requirements is a guarantee of uninterrupted operation. But if a violation occurs, our tips will help you quickly find the cause.
Do you want to share your own experience in restoring the heating system with a Vailant boiler or similar unit? Do you know the technological subtleties of repair, which are worth sharing with site visitors? Share useful information and photos on the topic of the article in the comment box below.