Warming of a wooden floor: popular insulation technologies + expert advice
Heat losses in the house pass not only through the walls and the roof, but also through the floor. The losses are especially high for floors made from natural materials. Therefore, warming the wooden floor will help to make the house warm, negate or reduce heat loss, as well as save on paying heating bills.
According to the requirements of the norms, the temperature in the living room should not be lower than +18 ° С, and in children's rooms +20 ° С. To achieve these indicators in the winter, it is necessary to conduct floor insulation.
Today, due to the abundance of materials, there are many technologies for thermal insulation work. Consider the most popular of them.
The content of the article:
Methods of warming wooden floors
The choice of technology depends on many factors, namely: the type of room, the height of the ceilings, the type of coating, the thermal conductivity of the materials, the budget and the requirements of the residents.
One of the key factors is the type of wood floor. There are three of them:
- parquet;
- boardwalks;
- plywood.
Boards or OSB boards are most often laid on logs. Plywood floors, as a rule, are used as rough, less often such material is laid on logs. These two types of floors can be insulated using any technology.
Special parquet dies or individual parquet slabs are laid both on concrete and on a wooden foundation. Such a floor can be insulated with a screed, any wood insulation, penofol or foam.
Consider the most popular technologies for warming wooden floors.
Method number 1 - insulation of floors on logs
This is the most common way of thermal insulation, especially if the floor is located close to the ground. With its help, large heat losses can be avoided.
Thermal insulation on lags is most often used for thermal insulation of floors in private homes.
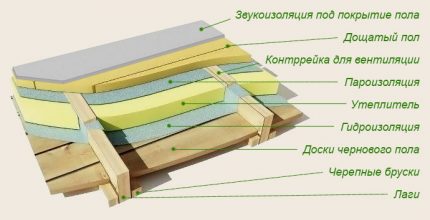
The work is recommended to be carried out in the following sequence:
- Wooden logs of a T-shaped form are installed at a distance of 45-70 cm, on them the boards of the rough floor are mounted with the help of special screws.
- Between the lags, the selected insulation is laid as tightly as possible, and the gaps are filled with sealant or polyurethane foam.
- Then, vapor or waterproofing is laid on the thermal insulation layer.
- At the end, clean floor boards are mounted, after which they are processed.
It is very important that between the insulating layer and the boards a ventilation gap of about 20-30 mm is formed.
If it is decided to use mineral wool or ecowool as a heater, then vapor barrier is necessary. It should be overlapped in 10-15 cm, and the edges should be up to 10 cm high. Special professional materials can be used, for example, a vapor barrier membrane or a plastic film.
Detailed instructions on how to insulate the floor on the logs can be found in this stuff.
Option number 2 - thermal insulation on the rough floor
It is ideal for rooms with high ceilings. The technology is a bit similar to the previous one.
The difference is as follows:
- bars are attached to the lags on the sides;
- after that, with the help of self-tapping screws or nails, boards are mounted on them;
- make sure that the size of the boards is equal to the distance between the lags;
- when all boards are installed, the surface of the subfloor is covered with vapor barrier. For example, film or glassine;
- then, between the lags, a heater is laid, preferably without gaps;
- after that, again the vapor barrier sheets, and, as the final stage, cover with treated boards;
- a clean floor can be covered with a special solution for shine or put some kind of coating.
If you want to insulate an existing, high-quality wooden floor, then you can use it as a rough one and lay a layer of insulation on it, but in this case the distance between the floor and the ceiling will be significantly reduced.
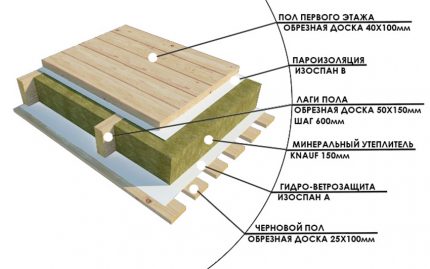
Option number 3 - the use of expanded polystyrene plates
This is the simplest thermal insulation scheme. This option is suitable even for rooms with low ceilings, since the thickness of the material is not very large.
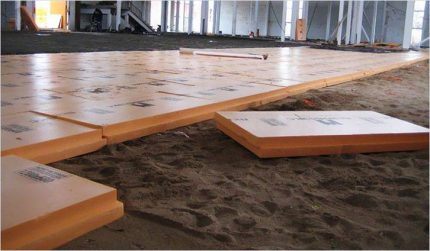
Laying technology consists of several stages:
- On a flat coating / foundation, lay a layer of insulation. For example, polystyrene foam or mineral wool.
- If the foundation is uneven, then it should first be leveled with a cement mixture.
- 50 mm thick polystyrene plates are laid on the floor in one layer, if this is an apartment.
- Plates do not need to be additionally fixed.
- Then the insulation should be covered with a vapor barrier if it is the first floor or laying is on the ground.
- After this, two layers of drywall boards are laid, which are fixed using conventional screws. You can also use a cement screed or sheets of plywood.
- The cement screed should be laid in two layers, and the insulation should be covered with a plastic film so that the screed does not penetrate between the plates.
- After the screed has completely dried, the final floor can be laid.
If to lay a laminate, then under it it is worth using a special thin substrate. All layers of materials are laid with a run of seams.
Screed is used as one of the layers of insulation. Dry screed is used only after shrinkage of wood, sometimes this process takes quite a long time.
From a physical point of view, a screed is a mixture of cement and sand in different proportions. There is a finished product in stores, but you can create it yourself.It requires increased waterproofing, as it can be deformed due to moisture.
Floating screed is somewhat different from the previous one. Although also composed of a mixture of cement and sand. It is poured directly onto the insulation sheets and therefore does not have close adhesion to the floor.
As a heater, most often with a floating screed, polyfoam or a material similar to it is used. This type of insulation is rarely used for wooden floors.
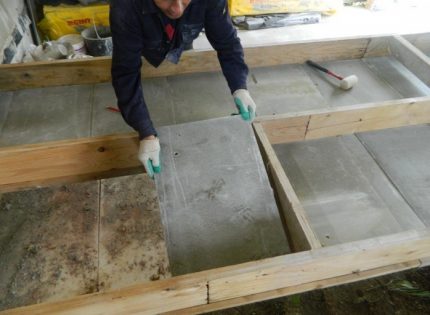
Option number 4 - underfloor heating system
Underfloor heating can be mounted directly on a wooden base. If the boards are rotten, then they should be replaced. To work, you will need drywall or gypsum plasterboard (gypsum fiber sheets), a foil substrate, a thin pipe, equipment for supplying and heating water.
Please note that underfloor heating should not be placed under bulky furniture. Since the sofas and cabinets will heat up, energy efficiency may fall.
The electric underfloor heating system requires the installation of special heaters under the final coating. Complex work of such a plan is best entrusted to specialists.
The whole system works from the mains, so it is worth protecting yourself from power surges and unplanned outages.
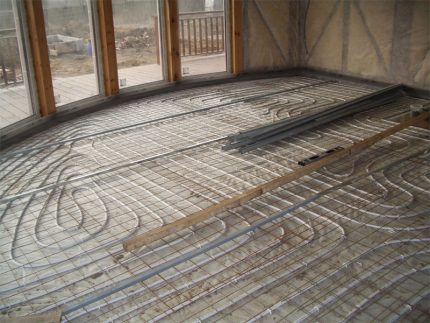
Installation of such a floor, both water and electric, is quite time-consuming and complicated, as well as an expensive process.
Work technology:
- lay in layers the foil substrate with the foil up directly onto the wooden floor and fix it with a construction stapler;
- sheets of drywall 9.5 mm thick are laid on it and fastened with screws;
- stack a tube of sewn polyethylene, fixing it with special plastic clips;
- as a substrate for the tube, you can use special fixing mats or reinforcing mesh;
- fill the structure with a plaster bulk floor;
- at the last stage, the pump-mixing unit should be assembled and installed and the entire system connected.
Within the same room there may be several pipes connected to the boiler. Each of them forms a contour. Such circuits can be switched on in turn if the room is large, or all at once.
Detailed instructions for arranging a warm floor on a wooden floor read Further.
We examined the most popular technologies for warming wooden floors. Each of them has its own advantages. The type of material that is best suited for the job also depends on the technology.
A few words about the materials
Today on the market there are a large number of diverse thermal insulation materials. We will consider the most popular and often used.
The insulation should have a certain set of qualities. Therefore, you should pay attention to: weight, environmental friendliness, thermal conductivity, compressive strength, moisture resistance, service life. In addition, the insulation should have medium, and preferably high adhesion to a wooden surface.
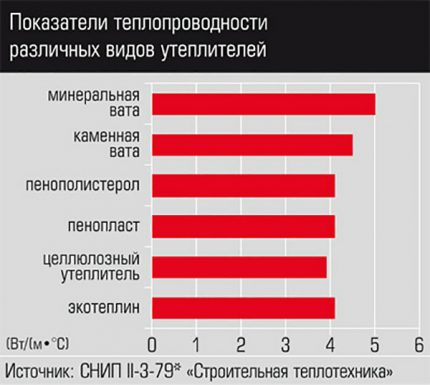
Also, one of the criteria for choosing a heater is its thickness. This indicator is critical for residents of multi-storey buildings.
In addition, the choice of material is influenced by the type of foundation and flooring, the presence of a basement, and also the features of operation - permanent living space or a summer house.
Cotton wool (mineral, stone, glass wool). This material requires high-quality waterproofing, as any cotton wool quickly gets wet.
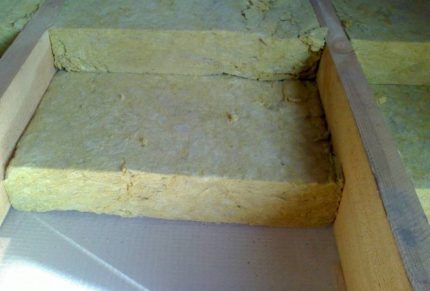
Most often used for warming a wooden floor mineral wool in conjunction with good waterproofing. Mineral wool is produced in the form of rolls and pressed plates. It is easy enough to work with it, as it is light and cut without difficulty.
To insulate the first floor, it is worth using mineral wool 20-30 mm thick, and for second floors and higher - 10-15 mm.
The classic of warming is laying mineral wool between the logs or directly on the rough floor.
Another popular insulation is sawdust. They are of several types: wood, sawdust granules, sawdust concrete, wood concrete. They require very high quality waterproofing. You need to use prepared sawdust, which lay in a dry place for at least 5-6 months. This material is best not to be used for warming living quarters, as it quickly gets wet and starts to whirl.
Sawdust, in order to reduce heat loss, should be laid in a thick layer, not less than 30 cm. This is the best option for warming a cottage or outbuildings.
No less popular material is expanded claywhich is made from clay. This is a cheap and environmentally friendly insulation. It is most often used for dry screed or just fall asleep on the rough floor or between the logs.
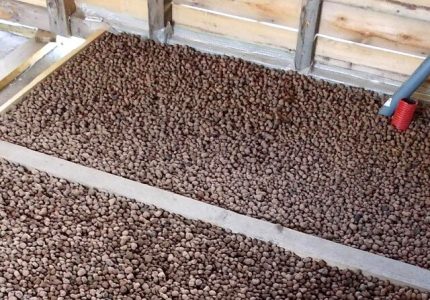
Styrofoam or extruded polystyrene foam can be used in rooms with high humidity. These materials are quite dense in structure and sheets of various thicknesses can be purchased.
Polyurethane foam It can also be used as a thermal insulation material. For its laying, special spraying equipment is used. You can use it on any foundation, and the foam itself can last up to 10 years.
Penofol - A fairly popular material for thermal insulation of Russian production. Insulation sheets with dense reflective foil. Several types are available. The classic version is made in the form of sheets of polyethylene foam coated with foil. There is also a self-adhesive Penofol S, and one side of which is coated with moisture-proof glue and a release film, and on the other there is aluminum foil.
Popular also considered fiberboardhaving excellent sound insulation. It is made from sawdust poured with grout. Available in the form of plates.
Isolon insulation is produced in the form of rolls, has low thermal conductivity. There is a standard silver color, but other bright colors. It has excellent sound insulation, despite the fact that the sheets are quite thin.
Most often, heaters are used in the form of rolls, so they are easy to stack.
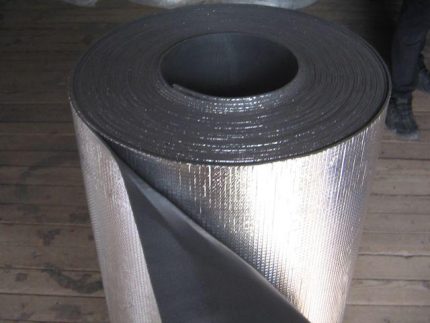
Useful tips from experts
If you plan to conduct thermal insulation work yourself, then read the tips from professionals:
- all gaps should be treated with sealant or foam, otherwise additional heat loss may occur;
- if you stack several layers of insulation, it is worth considering that each new layer should be laid perpendicular to the previous one;
- materials for thermal insulation of the first and second floors of one house may differ;
- To protect the wooden floor from groundwater, it is worth using as a waterproofing the usual building film around the entire perimeter. It must be fixed with sealant;
- waterproofing can be carried out using PVC boards, or from roofing felt, or using an ordinary plastic film, or make isoplast waterproofing;
- Some experts recommend laying a vapor barrier after laying the insulation. As a material for vapor barrier, you can use a film, parchment or other suitable material.
Before buying all materials for insulation work, we advise you to consult with specialists.
Conclusions and useful video on the topic
A few video examples of how you can insulate the floor with your own hands for both specialists and beginners.
The video provides an overview of one of the technologies for warming a wooden floor in a cottage or a country house:
A popular and inexpensive technology for floor insulation, which anyone can handle:
We examined the most popular technologies for floor insulation and types of thermal insulation materials. If this is relevant for you, then you can choose the appropriate option for yourself. But before the final choice, consult with a specialist and remember that cheap is not always bad.
Do you know a different way of warming a wooden floor? Please tell people about him who first encountered this issue. Leave your comments, ask questions, share experiences in the block below.
On warm floors, this is what I want to add: firstly, this is not one of the options for insulation, but an addition to insulation. If there is no thermal insulation (or it is bad), then heating the floor with electricity is the same as heating the street. Money for electricity will only fly in vain.
On laying an electric floor, there are very simple options, without any tricks there, pouring screeds, etc. Film floor, for example. In general, you can just lay it under the laminate, and it will work perfectly and serve as additional heating. and one can, by the way, dispense with outside experts. If you understand very little in electrics, mats will not be a problem to connect.
Question on polystyrene foam. I want them to insulate the floor, but someone was hanging noodles at work for their wife that this is the material for the foundation and facades, but inside they can’t be insulated, it seems to be harmful. Nonsense?
I always liked the advisors that come across to women, often these are the same “specialists” of female colleagues who are “in the subject” of all construction and engineering subtleties.
Extruded polystyrene foam is used for the following types of insulation work:
- insulation of internal walls;
- insulation of external walls;
- insulation of ordinary and warm floors;
- insulation of the foundation.
As you can see, the material is used both for external insulation work and for insulation work inside the building. Of course, there are temperature restrictions: it cannot be used near heating appliances and in rooms with high temperatures. Since when heated above 80 * C harmful toxins will be released. In this case, to be safe, many use other materials inside the buildings.
The scheme of laying the plates of extruded polystyrene in the photo in the application.