How to make an induction heater with your own hands from a welding inverter
Induction heating boilers are devices that have a very high efficiency. They can significantly reduce the cost of electricity compared to traditional appliances equipped with heating elements.
Industrial production models are not cheap. However, any home master who owns a simple set of tools can make an induction heater with his own hands. To help him, we offer a detailed description of the principle of operation and assembly of an effective heater.
The content of the article:
The principle of operation of the induction heater
Induction heating is not possible without the use of three main elements:
- inductor;
- generator;
- heating element.
The inductor is a coil, usually made of copper wire, with its help generate a magnetic field. An alternator is used to produce a high frequency stream from a standard home electrical network stream at a frequency of 50 Hz.
A metal object capable of absorbing thermal energy under the influence of a magnetic field is used as a heating element. If you correctly connect these elements, you can get a high-performance device, which is perfect for heating a liquid coolant and home heating.
Using a generator, an electric current with the necessary characteristics is supplied to the inductor, i.e. on a copper coil. When passing through it, a stream of charged particles forms a magnetic field.
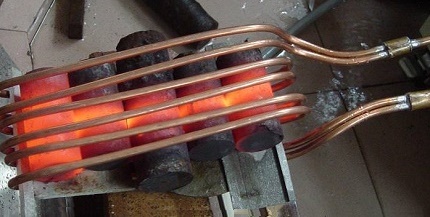
The peculiarity of the field is that it has the ability to change the direction of electromagnetic waves at high frequencies. If any metallic object is placed in this field, it will begin to heat up without direct contact with the inductor under the influence of the created eddy currents.
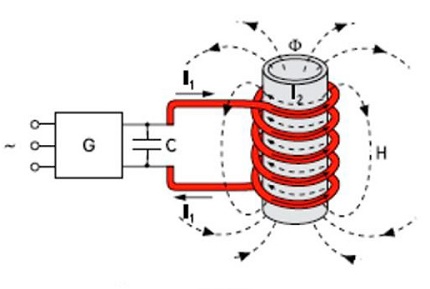
The lack of contact allows us to make energy losses during the transition from one type to another negligible, which explains the increased efficiency of induction boilers.
To heat the water for the heating circuit, it is enough to ensure its contact with a metal heater. Often, a metal pipe is used as a heating element, through which a stream of water is simply passed. Water simultaneously cools the heater, which significantly increases its service life.
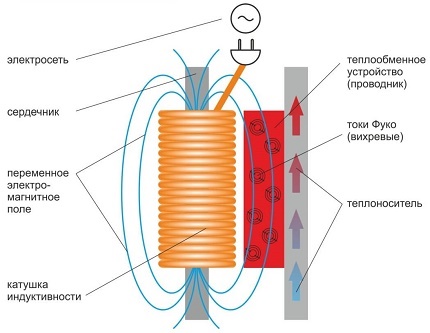
Advantages and disadvantages of the device
The “pluses” of the vortex induction heater are a great many. This is a simple scheme for independent manufacture, increased reliability, high efficiency, relatively low energy costs, long life, low probability of breakdowns, etc.
Productivity of the device can be significant, units of this type are successfully used in the metallurgical industry. By the speed of heating the coolant, devices of this type confidently compete with traditional electric boilers, the water temperature in the system quickly reaches the required level.
During operation of the induction boiler, the heater vibrates slightly. This vibration shakes off the limestone sediment and other possible contaminants from the walls of the metal pipe; therefore, such a device rarely needs cleaning. Of course, the heating system should be protected from these contaminants using a mechanical filter.
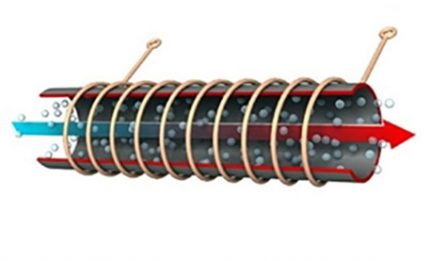
Constant contact with water minimizes the likelihood of burnout of the heater, which is a fairly common problem for traditional boilers with heating elements. Despite the vibration, the boiler works extremely quietly; additional sound insulation at the installation site is not needed.
Still induction boilers are good in that they almost never leak, if only the installation of the system is done correctly. This is a very valuable quality for electric heating, since it eliminates or significantly reduces the likelihood of dangerous situations.
The absence of leaks is due to the non-contact method of transferring thermal energy to the heater. Using the technology described above, the coolant can be heated almost to a vapor state.
This provides sufficient thermal convection to stimulate the efficient movement of the coolant through the pipes. In most cases, the heating system does not have to be equipped with a circulation pump, although it all depends on the features and layout of a particular heating system.
Sometimes circulation pump necessary. Installing the device is relatively easy. Although this will require some skills in installing electrical appliances and heating pipes. But this convenient and reliable device has a number of disadvantages that should also be reckoned with.
For example, the boiler warms not only the coolant, but also the entire working space surrounding it. It is necessary to select a separate room for such an aggregate and remove all foreign objects from it. For a person, a long stay in the immediate vicinity of a working boiler can also be unsafe.
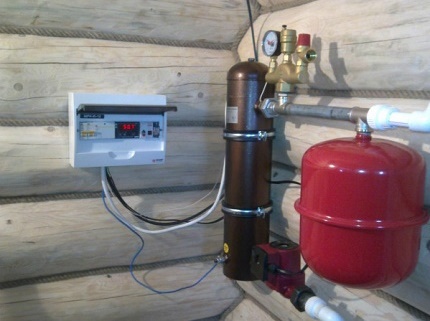
For the operation of the device requires electricity. In areas where there is no free access to this benefit of civilization, an induction boiler will be useless. And where frequent interruptions in electricity are observed, it will demonstrate low efficiency. If the device is handled carelessly, an explosion may occur.
If the coolant is overheated, it will turn into steam. As a result, the pressure in the system will increase sharply, which the pipes simply cannot withstand and will break. Therefore, for normal operation of the system, the device should be equipped with at least a manometer, and even better - an emergency shutdown device, a temperature controller, etc.
All this can significantly increase the cost of a home-made induction boiler. Although the device is considered almost silent, this is not always the case. Some models, for various reasons, may still produce some noise. For a device made independently, the likelihood of such an outcome increases.
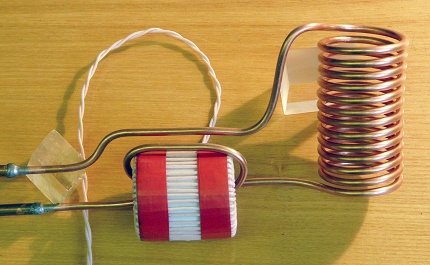
Homemade steps
To make such a device yourself is not so difficult. To do this, you will need:
- Make a heating element.
- Make an inductor coil of copper wire.
- Take a ready-made alternator.
- Connect the heater with coil to the heating system.
- Connect the coil to the generator.
- Connect power to the system.
- Make a test run to check the operation of the unit.
In industrial models, a metal pipe with thick walls is used as a heater, but it is very difficult and does not make much sense to provide sufficient power for a home-made device to heat such an element. An induction coil can heat any metal, so the heater can be modified.
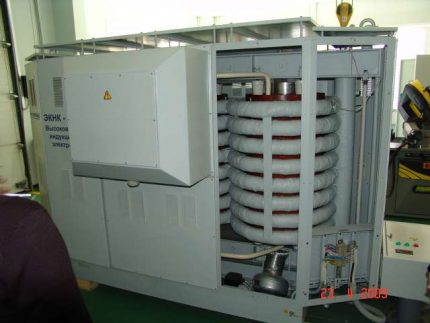
A piece of plastic pipe is used as a housing for an induction heater from a welding inverter. It should be slightly larger in diameter than heating pipes. The length of the pipe for the heater can be approximately one meter, the inner diameter can vary between 50-80 mm.
To connect the heater to the system, install adapters in the lower and upper parts of the housing. The lower part of the pipe must be closed with a grill, then a filler consisting of small particles of metal is placed inside the body. You can get filler, for example, from wire, bar, narrow metal pipe, etc.
The length of the segments can be varied arbitrarily. Most often, steel wire with a diameter of 6-8 mm is used for this, which is simply cut into small pieces. Some masters recommend cutting it into long rods of approximately 90 cm, i.e. almost along the length of the heater.
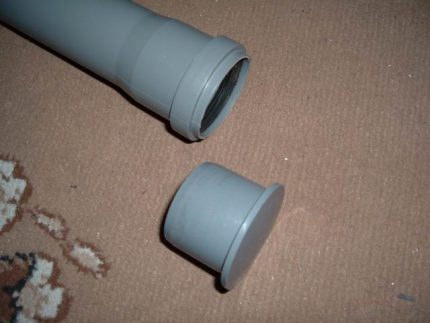
The higher the magnetic resistance of the steel of which the wire is made, the better it will heat up. Depending on the size of these pieces, a protective mesh is also selected, which is mounted at the bottom of the case. The filler is filled up or laid in a pipe to the very top. After that, the upper part is also covered with a net.
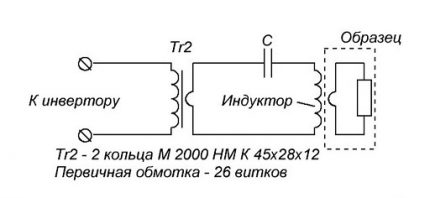
Thus, a home-made heater for an induction boiler looks like a thick plastic pipe, stuffed with pieces of metal and closed on both sides with a grid. Above and below the heater has adapters for connection to the heating circuit. The polymer pipe for the heater should have sufficiently thick walls.
In addition, any plastic for these purposes is not suitable, the material must tolerate the effects of quite strong heating and at the same time not emit any hazardous substances into the atmosphere or coolant. Now you should make an induction grid. To do this, take a copper wire and wind it directly on the heater body.
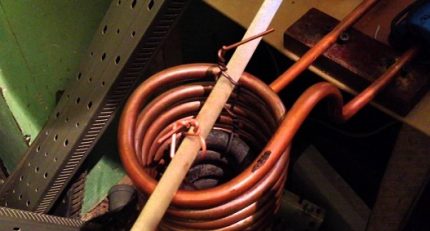
The more turns of wire, the better. It is believed that the induction coil should have at least 90 turns. The inductor is wound onto the pipe very tightly, there should be no gap between the turns.
For winding, a copper insulated wire of 1-1.5 mm is suitable. A thicker cable is not needed here, since it will also complicate the work on the winding, it will be more difficult to arrange the coils closely.
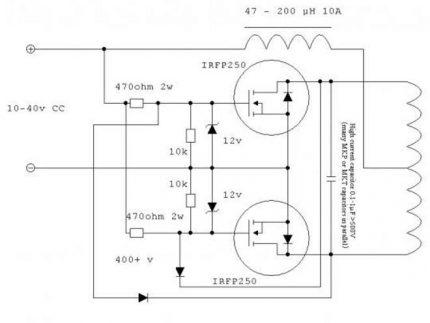
The presence of gaps can lead to noise due to vibration, which accompanies the operation of such a unit. Over time, this situation can lead to destruction of the insulation, which will cause inter-turn circuit.
Above and below, in addition to adapters, stopcocks should be installed. They are needed to provide the opportunity, if necessary, to shut off the water in the heating circuit.
When installing the heater, it should be remembered that its lower end should be directed to the return pipe, designed to collect the cooled coolant in double pipe heating system. The easiest way to get an alternating field generator is to take an inverter from the welding machine.
The contacts of the induction coil are connected to the poles of the inverter.As soon as the power supply is connected to the unit and it is included in the network, a home-made induction boiler will start working.
For the manufacture of such a device, even an inexpensive welding machine is suitable, for example, a Chinese-made model that allows you to adjust the current strength, starting at a level of 10 A. A temperature regulator sensor should be installed near the adapter on the feed. The welding inverter is connected through this thermostat.
At the outputs, rectifier diodes must be installed. To do this, you will have to open the body of the welding machine and solder the wires to the output, then attach them to the diodes. If you connect without diodes directly, then a rectified voltage current will flow to the winding, and the coil will work as an electromagnet, not as an inductor.
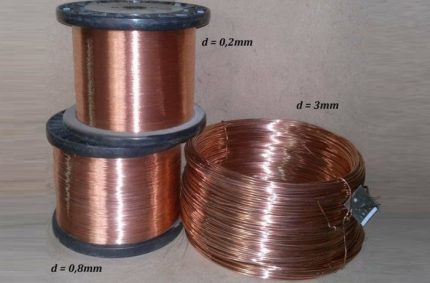
Some modern welding machines have a touch sensor that starts when the electrode touches the work surface. This moment must be taken into account so that the sensor either works at the right time, or does not affect the operation of a home-made boiler.
If an inexperienced master has problems with the alteration of the welding machine, it is better for him to seek professional advice.
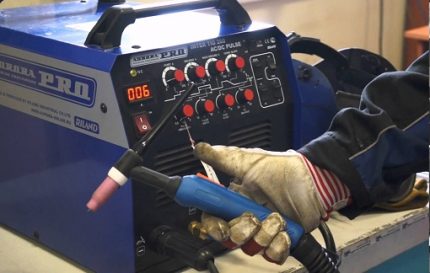
If everything is done correctly, the welding machine can be used for its intended purpose in the future. It will be necessary to unsolder the conductors with diodes and reassemble. Under the influence of high-frequency alternating current, an induction coil will create a magnetic field.
The metal inside the polymer case will begin to heat up and transfer heat to the water that circulates through the heating circuit. The device will need only a few minutes to warm up the coolant.
The location for the induction heater should be selected correctly. The unit should be located 800 mm below the ceiling, and at least 300 mm should separate it from the walls and furniture.
A few words about security
Home-made induction boilers are usually not equipped with control and protection systems, which makes them unsafe. Therefore, before turning on the unit, you must make sure that the cavity of the housing is filled with liquid coolant.
If the polymer case of the heater is subjected to constant heating without washing with the heat carrier, it will simply melt, sometimes this leads not only to deformation of the heater, but also to its complete damage.
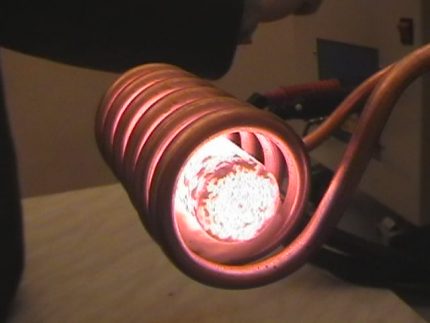
Falling out of a hot metal filler from a molten body can also be dangerous. In this case, you will have to almost completely dismantle the device and make a new heating element for it.
Connection to the power supply should be carried out via a separate cable from the shield. Of course, it is necessary to carefully seal all contacts with insulation. The inverter of the welding machine also needs to be grounded, this is an important point for safety.
In this case, you need a cable with a cross section of at least four millimeters. Some experts recommend giving preference to a six-millimeter cable. To prevent overheating of a home-made induction heater due to the lack of water in the system, it is recommended to install an overpressure valve at the heater inlet.
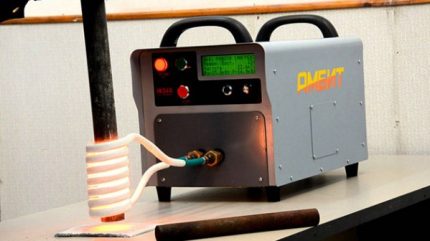
A home-made device of this type, not equipped with special protective equipment, is a potentially dangerous object that requires constant monitoring. Therefore, you should spend a little more money, but purchase the necessary devices.
At the same time, it does not hurt to evaluate the costs, perhaps buying a ready-made induction boiler will cost not much more. Industrial devices are usually equipped with all the necessary protection.
Features and step-by-step manufacturing technology of another version of a home-made induction boiler for the heating system given here.
Conclusions and useful video on the topic
Clip # 1. Overview of induction heating principles:
Clip # 2. An interesting option for manufacturing an induction heater:
To install an induction heater, you do not need to obtain permission from regulatory authorities, industrial models of such devices are completely safe, they are suitable for a private house, and for an ordinary apartment. But the owners of homemade units should not forget about safety.
Please comment on the material we have proposed for review. Ask questions about interesting or obscure points. Perhaps you have your own experience in the construction or installation of an induction boiler? You can tell and post unique photos in the comments section below.
Energy sales will not be happy. Where inductive energy is used (electric motor, starter coil), reactive energy always arises, which neutralizes the active energy in the network. Induction devices must be used with a condenser compensatory installation, selected according to the power of the boiler. Although the home meter reagent does not record the power supply organization, harm will be done.
Vladimir, this is the reasoning of an absolute amateur. In all such devices, the 50 Hz AC power is first rectified by diodes that are loaded on electrolytic capacitors, and only after that, a voltage of about 310 volts of a direct current source is converted by the inverter into a high-frequency AC voltage, which works for heating.
Found someone to regret ...