The washing machine does not pick up water: causes of breakdown and possible ways to fix it
Water supply problems are one of the most common problems that many owners of washing machines are familiar with firsthand. But although modern devices immediately signal their malfunction with symbols on the display or with the wink of light indicators, it can be difficult to find the culprit of the breakdown.
Therefore, we will examine in detail why the washing machine does not draw water, what problems can be fixed independently, and when you need the help of a master. The repair options proposed by us in the article in some situations will help restore the washing machine without the involvement of specialists.
The content of the article:
Fault signals for popular models
If no water is supplied to the machine at all, the essence of the problem is clear. But sometimes the device simply does not receive enough water for a full wash or rinse: we see that the drum is not empty and can not navigate due to a malfunction.
In this case, the signals of the machine itself will help, which are displayed on the display immediately or after starting the diagnosis.
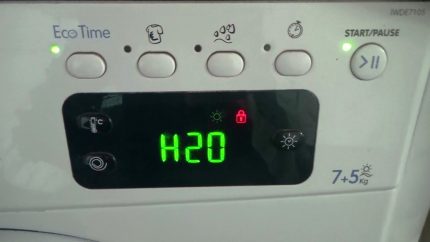
Water intake problem codes for some popular models:
- Asko - Water inlet fault or E01;
- Zanussi and Electrolux - E10 or E11;
- Candy - E02;
- Ariston, Hotpoint Ariston and Indesit - H2O;
- Samsung - E1;
- LG - PE or IE;
- Whirlpool - F01 or FH;
- Bosh - F01 or Aquastop.
If the washing machine is not equipped with a display, the flashing lights on the panel will indicate the causes of the malfunction. This code is programmed at the factory, so its value depends on the specific model, and the decryption table is attached to the product instructions.
Simple troubleshooting
Most often, problems with water intake arise due to improper operation of the washing machine. And some of them can be eliminated even without replacing parts without resorting to the services of a repair shop.
Problem # 1 - Water Outages
If the machine indicates a lack of water, the first thing to check is the presence of pressure in the water supply. Moreover, if there is water in the tap, the supply valve to the washing machine itself, which is installed directly on the pipe leading to the device, can be shut off.
The actions in this case are simple: if the valve is closed, it should be opened; if there is no water, postpone washing until it appears.
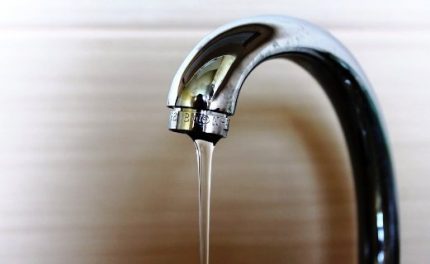
With insufficient pressure, the machine can start the program, but it will fill the drum for a very long time and constantly fail at the stage of water collection. Therefore, it is better to stop the wash and continue it when a normal stream flows from the tap.
Problem # 2 - clogged inlet hose or filter
Water is supplied from the water supply system to the washing machine tank through the inlet hose. In fact, this is a long flexible tube with nuts and fittings, one end of which is connected to the device, and the other is brought into the water supply system.
A hose is made of polyvinyl chloride reinforced with synthetic fibers or steel wire so that it can withstand the pressure of water, but, despite its strength, the material may fray over time and require replacement.
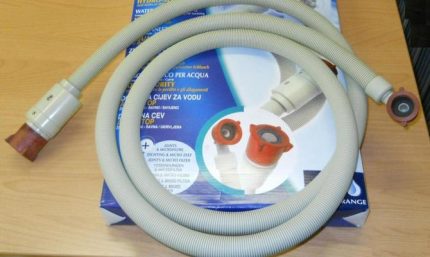
But most often the problem lies in the blockage, which blocks the narrow lumen of the tube and does not give the machine full access to the water stream.
To check this guess, you need to disconnect the hose from the machine, inspect the inlet filter and the inlet pipe.
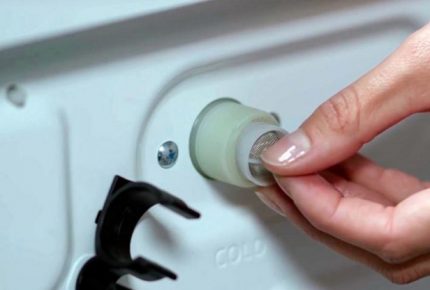
Cleaning is performed as follows:
- The water supply to the washer is shut off, if provided crane for machine, or in the whole system. The device is de-energized.
- The inlet hose is removed, washed with good water pressure and examined for creases and other damage.
- At the point where the tube is connected to the washing machine, a fine mesh will be visible - this is the filter. It must be carefully pulled out with pliers, cleaned with a small brush and rinsed with water.
- To test the filter, put a mesh on the hose, place it over the bath and open the water supply. If the water flow is under good pressure - everything is in order.
- At the same time, it is worth inspecting the pipe connecting the hose to the water supply system - it may also need to be cleaned.
Then you need to mount the system in the reverse order, connect the machine and check the water supply.
Problem # 3 - when closing, the hatch does not block
When the door of the washing machine closes with difficulty and without a characteristic click, the locking device does not work, without a signal of which the control board will not start the mode you selected.
There are several possible causes of failure:
- Sunroof cannot close tight due to damage to the plastic guide, which is under the tongue for fixation. Usually, such a breakdown occurs during prolonged use of the machine, when door hinges weaken from time or frequent use.
- A niche into which the latch tongue enters may become clogged due to a buildup of soap. In this case, you need to clean it from dirt and rinse. At the same time, inspect the tongue itself - a rod could drop out of it, which serves as a fastener.
- The most difficult problem is a malfunction of the board or programmer. If the controls responsible for blocking the hatch burned out on the control device, you will have to re-solder the tracks, replace damaged parts or the entire controller.
But the most common breakdown is the skew of the door due to hinges loosened when the device is operating at high speeds or mechanical damage. If the hatch does not close completely, tighten the fasteners or completely replace the hinges.
To do this, remove the front collar from the cuff, bend the elastic and use a key to tighten the nut connecting the hinges to the washer body to avoid twisting. Then unscrew the bolt and remove the hatch along with the mount.
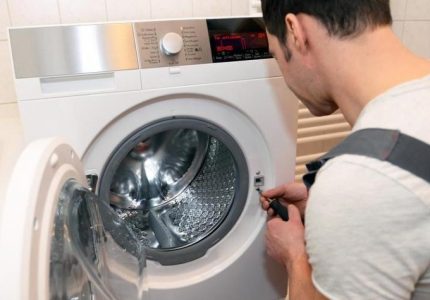
The door itself consists of an internal and external decorative flange, between which there is a glass “window”.
To disassemble it, you need to unscrew the fixing screws around the perimeter and carefully disconnect the elements. Now you can pull out the worn loop and replace it with a new one, then reconnect the halves with the “native” mounts.
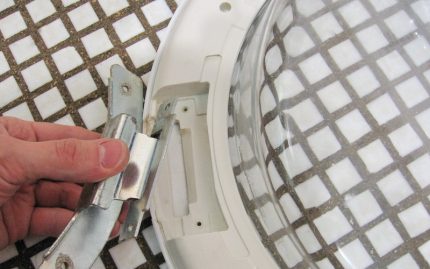
The device itself, which blocks the opening of the hatch, breaks. You can check its performance using a multimeter.
The lock must be removed from the machine, switch the toggle switch to test mode, connect one probe to zero, the second to the phase, and then also separately check the neutral and common contact. If 1 or 0 is displayed, the lock is defective and needs to be replaced.
Failure of individual parts
If the visual inspection and cleaning of the contaminants did not give a positive result, most likely, the machine signals the breakdown of certain parts responsible for taking water to the desired level.
In most cases, you can do with their cleaning or restoration, but sometimes the replacement of failed elements is also required.
No. 1 - malfunction of the water supply valve
From the water supply to the washing tank, water enters due to high pressure, and the inlet (filling) valve controls this pressure. It works like this: a current is applied to the coil, creating an electromagnetic field, under the influence of which the shutter opens and gives access to the flow from the water supply.
When the tank is full, the control module gives a signal that the power supply to the valve winding has been cut off, as a result of which the shutter lowers and blocks the water.
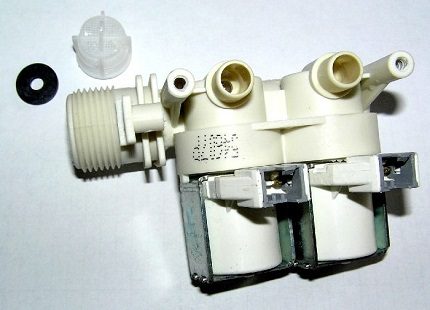
To inspect the valve, you must first dismantle it. To do this, de-energize the device, remove the inlet hose and mesh, and at the same time rinse the filter.
Then open the cover of the machine, disconnect the wiring from the part, the nozzles and, depending on the type of fasteners, bend the latches or unscrew the bolts. It remains to turn the valve and pull it out of the machine body.
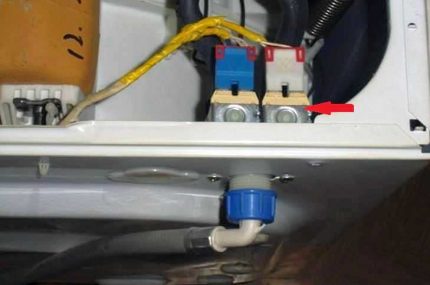
Detailed information on disassembling washing machines of different models is presented in this article.
Now you can check the health of the item. First, the inlet hose is connected to the valve, water is supplied and inspected for leaks - the operable shutter will not pass. Then measure the resistance on each coil with a multimeter. A normal value is 2-4 kOhm.
You can also verify the correct operation of the shutter by applying a voltage of 220 V alternately to each section: the valve should open, and de-energized should close.
Of course, you can try to give a “second life” to the part by replacing the burned-out winding, but there is no guarantee of the success of such a repair. Therefore, it is much easier to buy a new valve, because it is inexpensive, but it changes simply - it is enough to assemble the structure in the reverse order.
But if the electronics is working, it is possible that the valve is clogged or a foreign object has entered that interferes with normal operation. In this case, you can disassemble the part and clean it.
No. 2 - failure of the pressure switch and instructions for replacement
The water level sensor - pressure switch controls the filling of the machine’s tank. This is a small round-shaped element made of plastic, to which a loop of wires and a tube leading from the pressure vessel are connected.
It works like this: when a tank is dialed, a pressure is applied through the tube corresponding to the desired water level for each mode, depending on which the relay opens / closes the contacts.
If the pressure switch breaks down, the machine may simply not draw water, refusing to work on the washing and rinsing program or, on the contrary, constantly drain it without holding it in the tank.
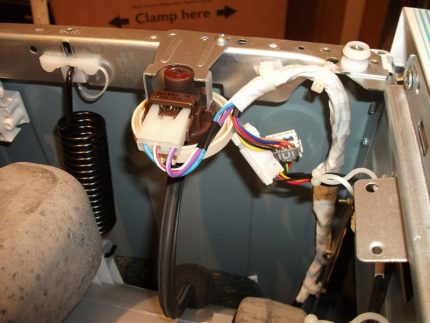
To check the operation of the pressure switch, unscrew the mounting bolts, disconnect the wires and hose. It is held by a clamp, which should either be pressed out with pliers or simply unscrewed.
Then inspect the device itself and its tube for mechanical damage and blockages. If the hose is clogged, it should be removed and washed, and the contaminated contacts of the pressure switch should be cleaned.
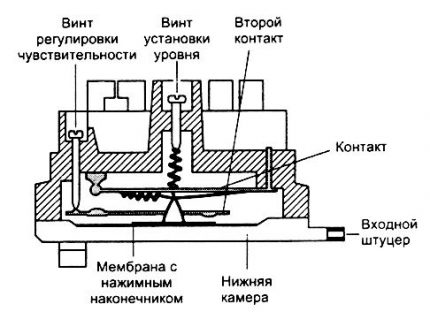
If no blockages are found, you can check the pressure switch with a small length (10-15 cm will be enough) of a hose of the same diameter as the tube removed from the sensor.
To do this, you need to attach one end of the new hose to the sensor inlet, and blow or immerse the second inlet into the water tank - clicks will be heard at the serviceable element.
You can also use a multimeter for testing - conductivity indicators should change with increasing pressure.
If the pressure switch is out of order, you need to buy a new device that is suitable for your model of washer. You can check by the marking indicated on the part itself. Then connect the tube, insert the contacts and fix the sensor with bolts, that is, reassemble and check the operation of the machine.
No. 3 - board failure or programmer failure
In the event of a control device malfunction, the machine simply does not receive an “order” to draw water. The easiest way to fix an electronics failure is to turn off the device for 10-20 minutes, then plug it in and try to restart the desired program.
Perhaps the controller will reboot and the machine will start working. But take a note that such a failure is the first bell indicating the upcoming washing machine repair in future.
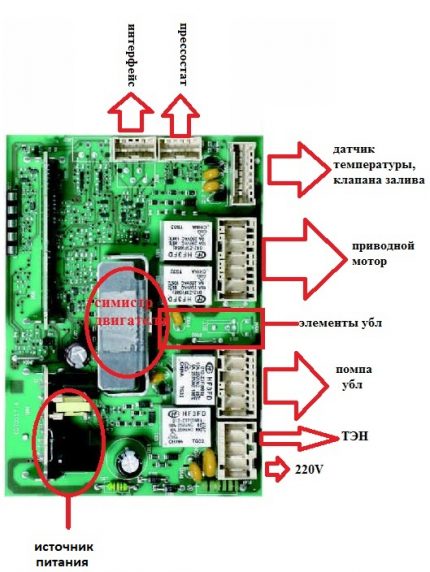
Most often, the electronics of the washing machine fail for the following reasons:
- High humidity in the room, where the device is installed, leads to the fact that the contacts damp and go away. You can try to remove and dry the board (even blow it with a hairdryer at low speeds) and subsequently make sure that the humidity level does not exceed 70%.
- Penetration of water into the control unit. Much depends on the make and manufacturer of the machine. In some models, for example, Samsung and LG, The "brain" of the device is completely sealed and protected from such troubles, but in the same Indesit or Ariston the board may get wet during washing or when carrying the appliance.
- Mains or low voltage. For the washing machine, you need to provide a dedicated outlet, and connecting through the stabilizer will help to level the differences.
- Kink of power cord, old socket or plug with faulty contacts - All these nuances must be eliminated and, if necessary, replaced worn parts.
If you suspect a malfunction of the main chip, you need to ring with a multimeter all the elements that are responsible for managing the set of water.
The most common problem is a breakdown of the simistor controlling the filler valve, an element by the signal of which the machine starts to collect water. But paths, soldering, burnout, diodes, relays, or resistors in the valve control circuit may also burn.
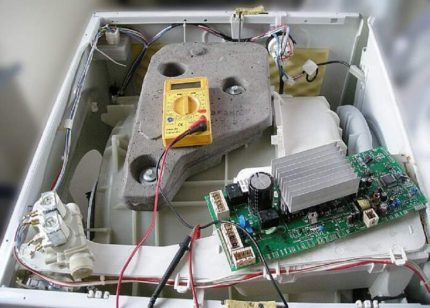
Visually identify the malfunction by the following symptoms:
- The chip has areas of a changed color, darkened tracks, soot or tan.
- Burnt varnish was found on the damping coils.
- The “legs” of the microcircuit are darkened or the tan marks are visible at the processor installation site.
- The "caps" of the capacitors have become convex or torn at the cross notch.
If you have experience working with microcircuits, you can try to clean the “suspicious” connections with a contact cleansing fluid.
If it is only a matter of soot or contamination from the ingress of soapy water, the conductivity of the contacts should be restored.
But if this does not help, you should replace the elements that have not passed the test with a multimeter, solder the re-burned tracks and solders and, if necessary, reflash the board.
It is worthwhile to start an independent electronics repair if the warranty period of the device has already expired and you are confident in your skills in working with a soldering iron and a multimeter.
But if there is no experience in such "resuscitation", you can completely replace the board with an identical one or contact a service center for help.
Conclusions and useful video on the topic
For a better idea of the upcoming repair work, we suggest studying step-by-step video instructions on how to troubleshoot various problems in which the washing machine will not be able to draw water into the tank.
How to clean the inlet hose filter:
Dismantling the inlet valve of the washing machine and cleaning it:
Dismantling and repair of the hatch lock device:
Principle of operation, performance check and replacement of the pressure switch:
As you can see, most problems with the water intake of the washing machine are quite affordable to solve on their own, and component parts for modern appliances can be easily found on the market. But if the cause of the breakdown is in electronics, it is better to entrust its repair to an experienced master.
Have you ever had to repair a washing machine yourself? Please tell us what was the reason for the poor water intake, was it possible to fix the equipment. We look forward to your comments, questions and advice on the implementation of the repair - the contact form is located below.
My LG car didn’t get water. Locked the door, but that's all. Called the master. I looked, looked, came to the conclusion: a problem with the motor.Changed the motor - nothing has changed. I checked the filter on the inlet hose, it may be clogged, but everything is fine with it. Changed the electronic module, it worked! Fixed a breakdown for 4 thousand rubles just! Buying a new washer is expensive, and it's a pity when the old one is only three years old.
We have a washing machine from old models, it is not so smart that it would signal a breakdown. It downtimes stop working, and you already guess what happened there. When we were faced with the fact that water was not poured into the tank, we first of all checked the water inlet hose, it turned out to be clogged. Yesterday all day the water went bad and was mixed with impurities, and it got silted up. In general, we cleaned it, and everything became normal.
Machine Hotpoint Ariston, water is poured, but much less than necessary for washing. After 10 minutes, error H20 pops up. I checked the simplest thing - the valves are not blocked, the hose and filter are not clogged. Apparently, you have to call the wizard. Or something else you can see?
Hello. Error H20 is very similar to the water formula in code writing and the manufacturer resorts to this method intentionally. It indicates that a problem has occurred with the gulf of water. Reasons may vary. For instance:
1. Water is not supplied at all.
2. The water pressure is too weak.
3. Clogged filter mesh.
4. Incorrect connection of the washing machine due to which self-draining occurs.
5. The problem with the control board.
6. The water inlet valve is out of order.
7. Faulty pressure switch.
8. Problem with wiring or contacts.
9. The inlet hose is kinked.
The machine does not draw water and does not close the door to lock ... the filter and hose are clean, what is the reason?
Hello. And here the reason is in the door, and not in the gulf of water. If the door does not lock, there will be no water supply. It is necessary to check the lock on the door or the control board, which can not set the desired command. That is, either the door does not close due to mechanical damage or the control board cannot close it (damage, something burned out, control glitch, program malfunction, and so on). What you need to do ... Try moving the washer to another mode and turn it on. If the problem persists, call the wizard.