How to make a do-it-yourself filter for a well: an overview of the best home-made options
The arrangement of a well in a suburban area will provide its owners with water. But without proper preparation, it cannot be used for cooking and drinking purposes. To perform preliminary cleaning, you can make a filter for the well with your own hands. Practical home-made will cost much less than the trading offer. And this is a lot, agree?
You can familiarize yourself with the information worthy of attention based on regulatory requirements by reading the article. The information contained in it will be useful to both independent masters and customers of drilling services. Knowledge of the design of the filtering device and the specifics of its care will also serve during operation.
The article describes the types of downhole filters that will help determine the best option. The construction technology was scrupulously disassembled, the technical details of the manufacturing and installation process are listed. For a better perception of impressive informational material, photos, diagrams and videos are given.
The content of the article:
The device and purpose of the downhole filter
All filters for a well have a similar structure. They work in single and multi-level water purification systems. Responsible for mechanical cleaning, preventing soil particles, grains of sand and other relatively large contaminants from entering the casing.
Filters consist of three main elements, located from top to bottom:
- Superfilter section. A part that plays the role of a kind of fitting when fixing the device to the casing.
- Filter element. A septum with openings preventing particles of contaminants from entering the filter.
- Sedimentation tank. A container for collecting large particles that managed to penetrate into the casing.
To improve cleaning, a multi-level system can be used, suggesting the presence of additional flow filterswhich are installed in front of the crane.
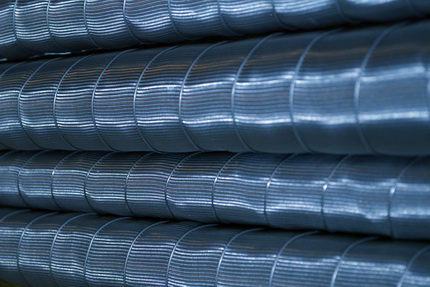
The devices used for primary cleaning are divided into two groups:
- Pre-filtered. A layer of marble chips or gravel is laid between the outer wall of the well and the surface of the casing, which “collects” contaminants and prevents rapid siltation of the filter.
- No pre-filtering.
The filter element of the variant without preliminary filtration is in direct contact with the aquifer.
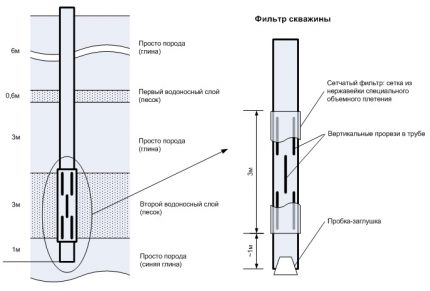
The main purpose of the downhole filter is to purify water from unnecessary impurities. However, the device removes only large contaminants, after-treatment after it is mandatory. This is the only way to reduce mineralization and hardness, reduce the concentration of fluorine, manganese and iron.
The choice of type of additional filtration system depends on the chemical composition of the water coming from the well. In addition to the main task, the filter for the well performs secondary functions.
A selection of photos will introduce the arguments in favor of using downhole filters:
It provides a long service life for the well and the equipment immersed in it, since it protects them from impurities that can fill the wellbore very quickly. In this case, the well will become silty, become inoperative and need cleaning.
It is important to understand that pump equipment It is not intended for long-term work with increased load, which is inevitable when lifting water with solid particles of contaminants dissolved in it.
Under such conditions, the pump experiences overloads and very quickly fails. In addition, the filter supports the walls of the well, protecting them from collapse and shedding of rock.
Materials for filtration equipment
The materials used are stainless steel, plastic and ferrous metals. Let us consider in more detail the features and characteristics of each of them.
The nuances of using stainless steel
The best material for making downhole filters is stainless steel. It is able to withstand high crushing and bending effects, and alloying makes it immune to oxidation.
Stainless steel pipes have a long service life, but their cost is quite high.
All operational characteristics of stainless steel are also characteristic of the filter mesh made of it and the wire used for winding on the part.
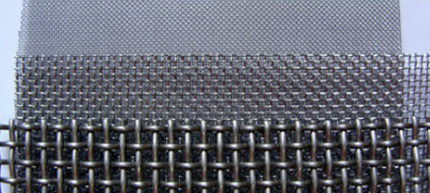
Features of the use of plastic
Plastic is another material that is widely used for the manufacture of filters.Plastic is absolutely inert, therefore it is not subject to oxidation processes. It is very easy to process and has a long service life.
The cost of plastic parts is low, which is very attractive for well owners.
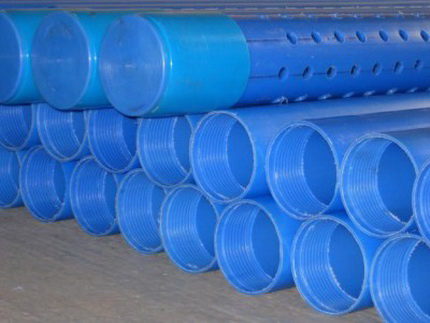
The main disadvantage of plastic is its low strength. As a result of this, it is not able to withstand the serious compressive loads that are characteristic of large depths.
Subtleties of using ferrous metals
Ferrous metals can be used as filters only for wells that supply water for technical purposes. This is due to the fact that they are oxidized by water, as a result of which iron oxide appears in it. Doctors have not proved that it is harmful to the body.
However, when the concentration of this substance is more than 0.3 mg / l, water will leave unpleasant yellow spots on plumbing, utensils and linen. Galvanized ferrous metals are also subject to oxidation.
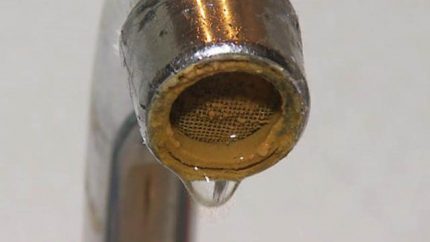
As a result, not only iron oxide but also zinc oxide appears in water. The latter irritates the mucous membranes and leads to indigestion.
Thus, experts strongly do not recommend the use of ferrous metals, including galvanized, for the manufacture of filters for the well.
This applies not only to the base, but also to the filter mesh, the lower sections of the casing, as well as the wire that is used in the fastening and manufacture of the structure. Otherwise, water obtained from a well with such a filter can only be used for technical purposes.
Thus, for deep wells, it is best to use stainless steel parts, and for shallow depths or in the case of using an additional casing, it is optimal to mount plastic components.
Structural types of filters
There are several types of downhole filters, each of which is designed for operation in certain conditions. The choice of design is determined by the geological characteristics of the water carrier.
Artesian wells are drilled in stable and hard calcareous rocks, which makes it possible to exploit them without a filter. The trunk is simply left open.
Good water pressure, which is typical for such wells, allows you to set submersible pump at an impressive distance from the bottom, so the feed water does not need rough cleaning.
There are almost no fine-grained impurities in the limestone, and the ingress of large rock particles into it is practically excluded. If the well is run in unstable gravel, wood or pebble rocks from large and fine inclusions, a filter is required.
Accordingly, the pump should be installed close enough to the water intake, which makes it mandatory to have a filter. Most often it is a hole or slot filter, which is designed only for rough cleaning. If there is no sand in the aquifer, the device will work efficiently and will last a very long time.
The most “capricious” are considered wells made in sandy soils. They deliver maximum trouble to their owners and drillers. Practice shows that they are most common, since sandy water carriers are most often located closest to the surface.
Sand wells cannot be operated without a strainer. Moreover, the life of the well largely depends on the quality of its manufacture and the material from which it is made. Let us consider in detail each of the types of downhole filters.
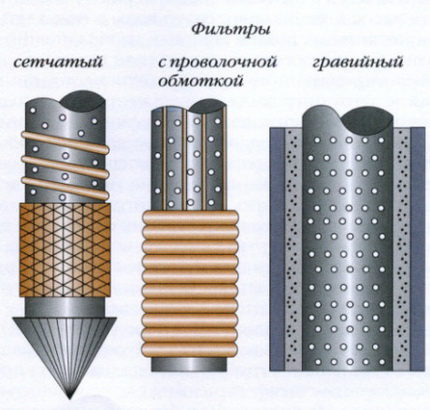
Option # 1 - Perforated Filter
Perforated structures are also called perforated, because they are a pipe with holes located in a certain order. Such filters are able to withstand fairly high loads, since the ring stiffness of the pipe does not decrease.
That is why they are allowed to be used at great depths, even with a high probability of soil movement. Experts recommend installing hole filters in low-pressure wells.
Over time, the performance of such a filter inevitably decreases, since the holes in the pipe are silted.
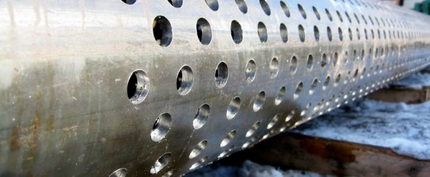
The device can be made independently. For this you need: a drill, grinding material, a plug made of moisture-resistant wood and a pipe of the desired diameter. It is better if it comes from an oil or exploration assortment.
If plastic is selected, make sure it is safe for humans. The size of the holes depends on the type of rock, so we select the diameter of the drill based on its particle size distribution. The holes in the pipe body can be linear or staggered.
Their number is selected in a ratio of 1: 4, that is, the fourth part of the entire pipe should have perforation. The holes are placed with a minimum pitch of 2-3 cm.
The hole filter manufacturing operations are performed in the following sequence:
- We lay the pipe on a horizontal surface and proceed to the marking. From one end we note the length of the sump, about 50 cm. Directly behind it is the filter part, on which we mark the holes. Do not forget that it occupies ¼ of the entire pipe.
- We drill the first hole. We position the cutting tool relative to the surface of the pipe at an angle from 30 to 60 °. We drill in the direction from bottom to top relative to the assumed vertical placement. The result is oval holes of a larger area.
- Similarly, we carry out all the necessary holes in accordance with the marking.
- Using the grinding material, we carefully clean all the holes obtained.
- Raise the pipe, install it vertically. Carefully free the internal cavity of the filter from chips that could remain in it and close the holes.
- We take a wooden cap and close the bottom of the pipe with it.
Homemade hole filter for the well is ready.
Option # 2 - slotted models
Slotted filters are very similar to hole filters, but are equipped with slots instead of holes.
Which may be located as follows:
- Staggered horizontally. A segment with slots is performed, the block following it is cut with a rotation of 45 °. This makes it possible to ensure the necessary structural strength without special stiffening belts.
- Vertically. The distance between the slots should be at least 10 mm. Such systems are similar to wire filters for a sand well.
- Horizontal with multiple slots. The distance between the sections with perforation, which is called the stiffening belt, should not be less than 20 mm, otherwise the pipe will lose the necessary strength. Slot pitch - at least 10 mm.
Slotted filters are used in unstable soil, where the percentage of pebbles, gravel or gravel is high. They can be used in case of high threat of rock collapse. A distinctive feature of the slotted filter is a higher well debit.
This is due to the fact that the area of the slot located on the core frame exceeds the hole area of the hole filter by about a hundred times. The main drawback of the design is the high probability of clogging of cracks with fine-grained sand.
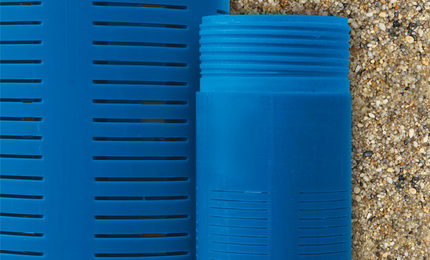
To make a slotted type filter yourself, you will need: a pipe, metal or plastic, a wooden plug and a milling tool, or gas cutter (burner). It all depends on how the slots are made.
The operations are performed in the following sequence:
- We lay the pipe on a horizontal surface and mark it out. We retreat from one edge about 50 cm, it will be a sump. Then we outline the location of the slots, not forgetting about the stiffness belt, if the cracks are horizontal.
- Based on the marking, we make slots in any suitable way.
- We raise the pipe and release its inner part from chips and contaminants that could get there during the operation.
- We install a stub.
The filter is ready for operation.
With the procedure for the construction of a well filter, a photo gallery will be presented:
Option # 3 - strainers
Such systems are designed for installation on clay-sand aquifers.
The mesh filter is a base in the form of a hole or slit structure, onto which a fine-mesh mesh is fixed for finer filtration. The size and shape of its cells may vary.
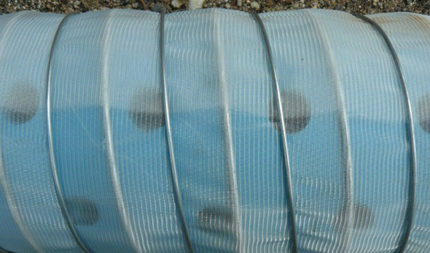
Such a system is considered quite durable and strong. Its main drawback is considered to be reduced productivity, since small holes in the grid create a fairly strong flow resistance.
In hard water, such filters quickly become clogged with particles of glandular compounds.
The grid that covers the structure can be:
- standard with square cells;
- keeperconsisting of several layers;
- galunnoy with cells of complex shape.
The type of soil determines the choice of mesh. For gravel and coarse-grained sand, a cypress or standard mesh is selected, for fine and medium-grained rocks, a galunny one. Cell sizes can vary from 0.12 to 3 square meters. mm To correctly determine the size, use the sample method.
They collect soil from the well, then sift it through different mesh patterns. One that retains at least half of the particles of soil can be considered suitable for work.To determine the size of the cells and, accordingly, the soil particles, a handful of soil from the well is poured onto graph paper.
Grids for filters can be made of different materials:
- Metal - brass or stainless steel. Such products are durable, their cells can be easily cleaned if necessary. The main disadvantage of brass products is the high probability that during installation the mesh cells can be deformed, which makes it difficult for water to enter the filter column.
- Fiberglass or carbon fiber. They do not deform during installation, they have a long service life. The main difficulty in operation is cleaning the net.
Normal flushing will not be enough; more sophisticated methods will have to be used: chemicals, electrical discharges, or hydrodynamic shock.
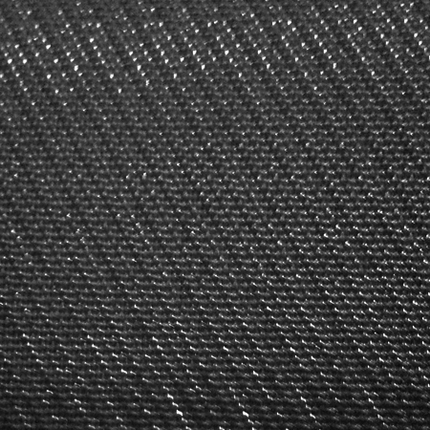
For self-manufacturing a mesh filter you will need: a pipe made of plastic or metal, a wooden plug, a mesh, a wire with a cross section of at least 3 mm, a soldering iron and a drill or a milling tool, depending on the chosen method of perforation.
Getting started:
- We put the pipe on a flat horizontal surface and apply marking for perforation on it.
- In accordance with the marking, we perform holes or slots.
- On top of the perforation, we impose the wire. We wind it at an inclination of 30-45 °, while the distance between adjacent turns should be 2 ± 0.5 cm. Every 5-10 cm we carry out spot soldering, fixing the wire to the base.
- We check the quality of the completed winding, if necessary, repeat the soldering.
- We put a mesh on the wire and wrap the pipe body with it and fix it.
In the case of a metal mesh, we use soldering, soldering the canvas to the wire, and fix the plastic parts with metal wire.
Option # 4 - wire filter
Such a device can be considered a kind of mesh filter with the difference that instead of a mesh, a special wedge-shaped wire is wound on a base with a spiral. The size of particles retained by such a filter is determined by the shape of the wire and the pitch of the winding.
Filters of this type favorably differ from mesh counterparts in high strength and long service life, which is due to the greater thickness of the wire compared to the mesh. It is clear that we are talking about high-quality frame-and-rod products, which are almost impossible to accomplish on their own.
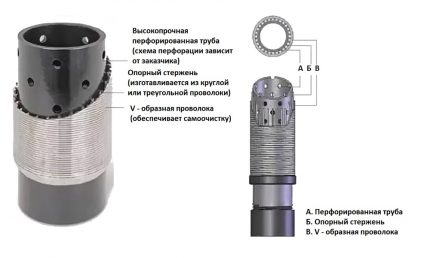
At the same time, strainers more easily tolerate local damage. In the event of the destruction of one or several cells of the grid at once, in this section it will pass larger particles of contamination into the column. However, the rest of the filter will fully retain its properties.
For wire filters, a different thing is common.If the winding is damaged, the product loses its filtering properties in the interval between two adjacent points of fastening of the winding to the frame in the rush area. In addition, the cost of strainers is much lower. This is due to the fact that they are easier to manufacture.
High-quality wire filters are almost impossible to make on their own. If you still really want to try, you will need a metal pipe of the desired diameter, a plug, a milling tool or a gas cutter, metal rods, a soldering iron and a wedge-shaped wire.
First, the base is made in the form of a slit filter, the width of the slots of which must correspond to the average diameter of the rock particles. On the prepared frame we lay 10 or 12 metal rods with a diameter of at least 5 mm.
They will not allow the wire to lie directly on the frame and close its holes. The base is ready, you can start winding the wire. A feature of manufacturing a wire filter is that it is wound on a frame under tension. It will be easier to wind up using a lathe.
If this is not possible, the operation is performed manually, which is very time consuming and requires special care and patience. During the winding, the turns of wire laid with the required pitch are necessarily fixed to the base by soldering.
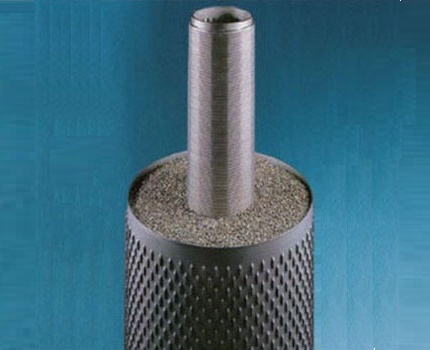
Option # 5 - gravel backfill
Small sized smooth fragments of hard rock or gravel can be considered a natural filter with a fairly high cleaning effect.
It is able to retain even very small elements of pollution and has the ability to self-clean. Based on this, fine gravel can be used as an additional filter.
For this purpose, it is placed in the water intake zone of the well. The effectiveness of such a filter depends on the characteristics of the gravel and the height of its layer. The more particles of impurities settle on gravel, the less they will get into the main filter, which will significantly extend the well’s work.
There are two types of gravel filters:
- Backfill. It is a layer of material filled directly into the well through the openings of the annulus. It can be used only for structures whose diameter does not exceed 10 cm in the area of the filter part.
- Assembled on the surface. The gravel mixture is stuffed into the cavity between two layers of filter material from wire or mesh. Such a contour after stuffing is lowered into the well. The width of its walls does not exceed 3 cm.
You can only make the filter of the first type on your own. First of all, you need to cook gravel. Work should be taken with great responsibility, since the quality of the filter depends on the quality of the material.
First, select the diameter of the gravel. It should be on average 5-10 times smaller than the diameter of the downhole pipe.
We select all elements by size, calibrate. It is desirable that they be the same size. If the material is very dirty, you may need to rinse it. When arranging a filter from gravel, preparatory work begins at the stage well drilling.
You may also be interested in information on methods. well drilling and how rock it after drilling.
The hole for it is carried out taking into account future dusting, that is, a little larger than required diameter. After the well is ready, prepared gravel is poured from the mouth. Dusting thickness - not less than 50 mm.
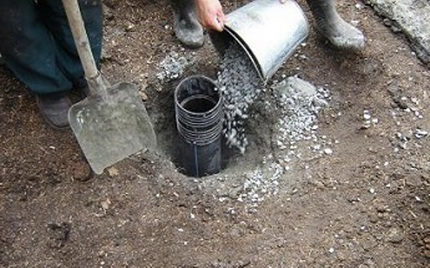
Practice shows that even a novice home master can make a filter for a well on their own. Such designs are easy to manufacture and install.It is important only to correctly determine the type of filtering device and correctly select the material from which it will be made.
Conclusions and useful video on the topic
Step-by-step instruction on manufacturing a strainer:
And this video will acquaint you with the sequence of work on the production of a downhole filter from a plastic pipe:
If everything is done according to the rules, the filter will last a very long time, cleaning the water supplied to the house from pollution and protecting downhole equipment from overloads and premature failure.
Do you have a makeshift filter in your well made according to one of the instructions discussed in the article? Tell us if it was difficult for you to collect it and what nuances you encountered.
Or did you have questions during the construction of the filter device? Feel free to ask for advice, leaving your question in the comments section - we will try to help you.
My family and I live in a village, we do not have a water supply system, and the entire population uses water from wells and boreholes. I also made a well, I used materials from stainless steel, the water is clean without any impurities. And the well has been in service for about ten years and there are no problems so far.
It is interesting to know, but how did you determine that the water is clean and free of impurities? Well, clean okay - by eye, but the presence of impurities to taste or what? Even if the water has a normal taste and is colorless, it is not a fact that it is pure in terms of chemical and bacterial composition. Therefore, the very first thing after drilling a well is the delivery of water from it for laboratory analysis. Especially in your case, when the well is used as the main source of water, including drinking. And according to the result of the analysis, you need to look at what filter should be selected for the well, is there enough of a simple homemade one or will you have to buy a more serious thing.
Very topical issues that require priority attention when developing a well and providing subsequent water supply from it. There are impurities in any water, although the well will be three times artesian. If it is planned to drink water from a well, first of all a chemical analysis will show whether the water is suitable for this or if it will be necessary to filter the water.
Further, for some reason, many people believe that well pumps will work in any water. This is not true! For example, there are classes and series that are designed to work in water with a high iron content or high sand content. Appropriate technologies and materials are used to protect against such factors.
Pumps that are used in wells with a high content of sand particles, when the models are not designed for this, are often brought for repair. At the same time, people are frankly surprised and indignant that the manufacturer refuses them warranty service.
Only six months ago they made a well in the country. The water tastes good, sort of clean. But he drew attention to the fact: when I collect water in an enamel bucket and leave it in it for a while, a sandy sediment appears at the bottom. Worried - such water will lead to kidney disease. Made a fiberglass mesh filter.We have to periodically clean it, but the water quality has become much better.
Have you tried to pump the well normally? To reduce the amount of sand in the water to the minimum values. Plus, the pump may be too powerful for your well.
Filters are needed, but it would also be nice to fix the root cause too.