How to make a drill for a well with your own hands: the best homemade schemes
Do you want to equip a water supply system on your site by drilling a well yourself? Agree that the presence of a water supply and sewage system significantly increases the level of comfort when living in a private house or in the country. But the call of specialists to equip a well or well will cost quite expensive.
Have you decided to make a drill for the well with your own hands and choose a simple version of homemade? We will help you in this matter - the article contains useful information about the manufacturing process of home-made spiral type drills and drill spoons.
A list of necessary tools and materials is provided, thematic photos and useful video recommendations on the construction of a home-made drill are selected.
Our detailed instructions, equipped with step-by-step photos, will help to make a simple and uncomplicated drill even for a beginner.
The content of the article:
Rotary Hand Drills
For self drilling a simple device will be required under water. It includes a detachable pipe, which can be increased as the depth of the structure increases, a handle with which rotation will be carried out, and the drill is the main structural element.
There are two types of drills that are commonly used to perform rotary manual drilling of wells:
- spiral (screw) drill;
- drill spoon.
Both of these tools have such design features that allow you to perform drilling work without the use of additional equipment.
At its core, a spiral drill is a very large drill. It cuts into the ground with its sharp carbide cutting edge, the edge of which is sharpened in the form of a cone.
Above, the cutting surface of the tool is twisted in a spiral along the rod. The largest diameter of this spiral determines such an important parameter as the size of the future well.
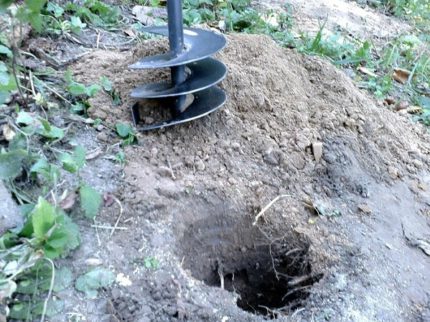
During rotation, the cutting edge is pressed into the ground and cuts it, after which it moves along the spiral strips and is pushed out with their help.
So in the direction of drilling creates additional emphasis. During the completion of the drilling of the well, the accumulation of residual soil extracted from the mine occurs between the turns of the screw. The auger drill has to be periodically removed to the surface to clean.
To make a spiral drill yourself, you can use a cylindrical rod to which a cutting spiral made of a steel strip is welded to the bottom. Earthwork can be carried out with such a tool even on crumbling and hard soils.
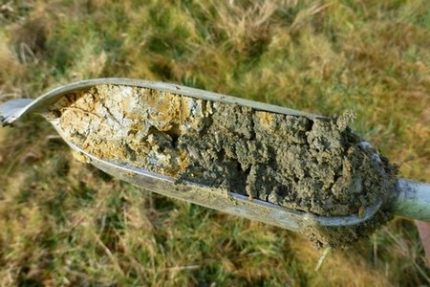
The composition of the drill spoon includes a metal rod, the end of which is equipped with a cylinder of a certain diameter. This cylinder has a longitudinal or spiral slot in its lower part. The method of soil capture served as the basis for the name of the drill with a spoon.
Relative to the axis of the metal rod, the spoon is shifted to the side by about 10-15 mm. Due to its displacement, this tool drills a hole whose diameter exceeds the same parameter of the spoon itself.
The increase in diameter is necessary for installation in the production of casing pipes, the diameter of which must be larger than the diameter of the drill.
When performing drilling operations with a spoon, casing pipes should be installed at the same time. It is most effective to use such a tool on plastic soils - sandy loam and loam.
Option # 1 - making a spiral drill
To make a drill on your own at home, on the core of which a spiral will be welded, is a difficult task. But to build a model easier everyone who has the skills to work with a welding machine, grinder and other tools.
We will prepare everything that we need for work in advance:
- welding machine;
- grinder (angle grinder);
- tape measure or other measuring instrument;
- steel rod of the length we need;
- steel disc.
We will carry out all stages of work in order. First you need to saw the steel disk into two identical semicircles. Now both parts of the freshly sawn disc must be sharpened.
It would be nice to do this part of the job to someone who knows how to sharpen tools, because the quality of the sharpening will depend on how easily the tool goes into the ground. And that means the overall speed of the work.
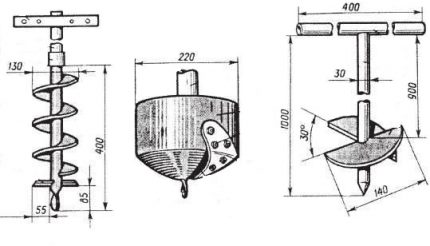
Theoretically, a spiral drill can be made using a steel spiral for this purpose. To do this, take a strip of tool steel, heat it, and then twist it into a spiral with a step corresponding to the diameter.
Then the strip should be hardened and finally welded to the rod. But it is practically impossible to perform such work qualitatively outside the factory.
Option # 2 - Build a Spoon Build
If the soil in your area is resistant to shedding, then it’s best to use a drill spoon to drill a well. It, as already mentioned, has the shape of a cylinder with a longitudinal slot in the side and a spiral-shaped gripping spoon at the bottom.
The length of such a cylinder usually does not exceed 70 cm, and the diameter of the tool can be different: it depends on the parameters of the well that we want to get as a result.
The soil that the driller will have to remove to the surface must penetrate the cylinder through the cavity and be held inside by adhesion and compression.
Before making a slot in the cylinder, you need to evaluate the quality of the soil in your area: the higher its flowability, the narrower the slot in the spoon.
There are two ways to make a drill spoon yourself:
- take sheet steel and twist it along a given diameter, giving the workpiece a cylindrical shape;
- use a piece of pipe that already initially has the shape we need.
Using finished steel pipe is, of course, much easier. To make a drill, you need a small segment of it. It remains only to make cuts at its end, to bend them and sharpen the edges. Instead of a pipe, you can use a used cylinder.
To perform the work we need:
- hollow steel cylinder;
- Bulgarian;
- apparatus for welding;
- steel bar or bar;
- drill for metal.
Using a grinder, cut a slot in the bottom of the cylinder. To facilitate the drill the process of entering the soil, you can weld to the rod strictly along its axis a conventional metal drill.
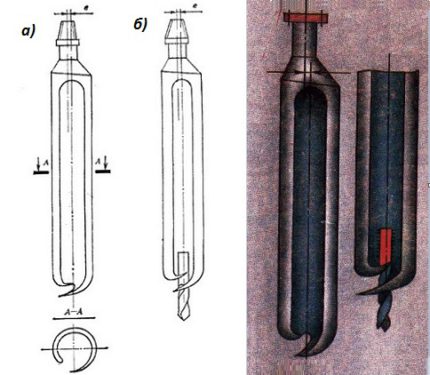
The method with sheet steel is more time consuming. The steel billet will need to be welded along the seam, and the cutting edge should be sharpened so that it easier to enter the ground. A weld needs to be fixed and the drill, placing it in the lower part of the cylinder.
If there is no suitable drill for metal, you can replace it with a narrow steel plate, after sharpening it on both sides. At the same time, drilling efficiency will not be lost. The length of such a plate is about 15 cm.
The finished spoon of a cylindrical shape remains to be welded to a metal rod, which moves to the side 10-15 mm from the line of the tool axis.
During the operation of the drill, this displacement will make the well larger in diameter. This happens because the longitudinal cutting edge of the drill spoon scrapes the soil from the side surfaces of the shaft.
Due to the fact that the diameter of the projectile is smaller than the diameter of the casing pipes, such a drill can easily be used inside the casing being constructed, which will greatly facilitate the procedure for their installation. The pipes themselves will protect the well from collapse.
The loads during the work of the drill-spoon are very high, therefore, for its manufacture it is necessary to use high-strength tool steel. The drill-strengthening elements should ideally undergo heat treatment and hardening processes.
You may also find useful information about popular well drilling optionsconsidered in our other article.
Bringing the rotary drill into working condition
It is not enough to learn how to make a drill for a well yourself. It is necessary that the finished drill can be used to perform work. To do this, provide it with a handle or handle, as well as a detachable drill pipe.
Convenient Handle Making
The handle is an important structural element. It is necessary for the drill to be conveniently rotated. The handle design is also not as simple as it seems.
It can be envisaged that one person will be controlled with it, but sometimes more people can participate in drilling operations. The complexity of the process depends on the quality of the soil and on the depth of the future well.
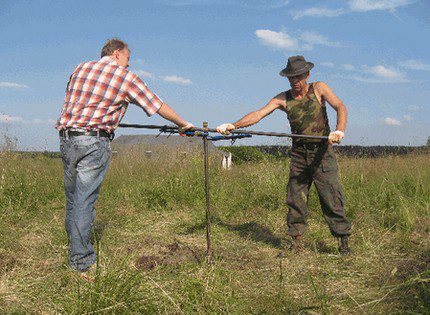
The handle is made of metal, which has a decent margin of safety. After all, this part of the drill needs to withstand significant loads without springing and without damping the applied forces. Welding is used to connect the handle and the upper edge of the split pipe.
Detachable drill pipe construction
The drill is a multifunctional tool. With its help, you can not only build a well, but, for example, dig a pole. If you use it for gardening, it is quite possible to do without a drill pipe.A one and a half meter base will be enough to dig a shallow pit.
But we need a drill in order to drill a fairly deep well with it. What to do in this case? The point is to leave the bar single-section and simply lengthen, no.
The length of the bar and the ability of the metal to resist torsional forces are inversely proportional. It will be impossible to work with a long single-section bar.
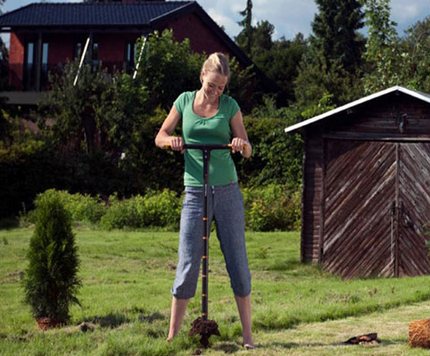
There is only one way out: you need to make such a drill pipe, which will consist of detachable sections. The length of one section, the split bar, should be 1 meter or slightly more. Such sections need to be built so much that as a result they reach the planned depth of the well.
You may also find the information about choosing a pipe for a well described in our article: Which pipes are best for the well: types, which to choose and why.
The extension of the length of the string of rods attached to the drill will be carried out gradually, as the drill will move deeper.
There are several options for connecting rods to a long drill rod, these are:
- Threaded coupling. To create such a connection, a thread is cut inside each section, which will correspond to the dimensions of the connecting element. The threaded sleeve is manufactured to the desired length. It remains for us to exclude the possibility of spontaneous unscrewing of the connection. A cotter pin is used for these purposes. This method is simple and reliable.
- Nut and bolt. Welded to the rods made from pipes of small diameter. This is a fairly simple but not reliable option. It will be necessary to weld on a thin-walled pipe, on which such a connection is unlikely to be durable. In addition, to fix such a threaded connection of the rods, additional efforts will have to be made.
- Welded couplings. They are cut from a pipe whose diameter is larger than that of the rod. Then tightly weld the sleeve to the pipe at one end of the section. On the other hand, on the other hand, insert the next section freely. Now you need to fix the sections so that they do not rotate. To do this, you can insert a bolt across the pipe and fix it with a nut on the other side.
To make a do-it-yourself drill for a deep well, several rods are connected. And it is better if their connection is extremely simple. Indeed, in the process of drilling the tool will rise to the surface so that it is freed from the ground.
Each rise of the drill is accompanied by its division into its component parts, and each subsequent descent - by a new assembly and build-up.
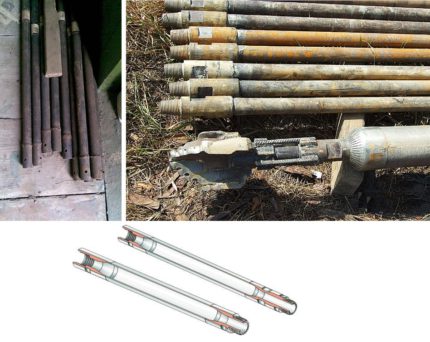
In addition to the drill itself for creating a well manually use other tools that are worth mentioning in this article.
For example, if the well is already ready, and it was not so easy to pull the tool to the surface of the earth, you can use the lifting mechanism, which works on the principle of a lever.
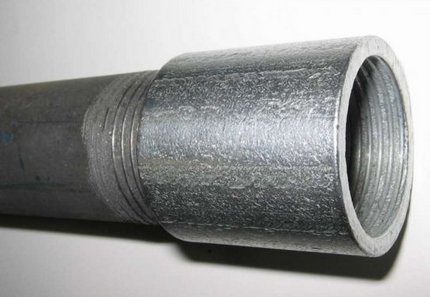
When the drilling procedure is delayed, and the drillers themselves lose their strength, devices that would help to scroll the drill inside the well and screw it when it is deepened would really help them.
Shock Rope Drill
It is possible to drill a well in the area not only by rotating the drill, but also by the shock-rope method.For this type of work you need a special installation, which can also be done independently from improvised materials.
Having such equipment, all the work can be done without any helpers at all, therefore, we will consider the process of manufacturing an impact drill.
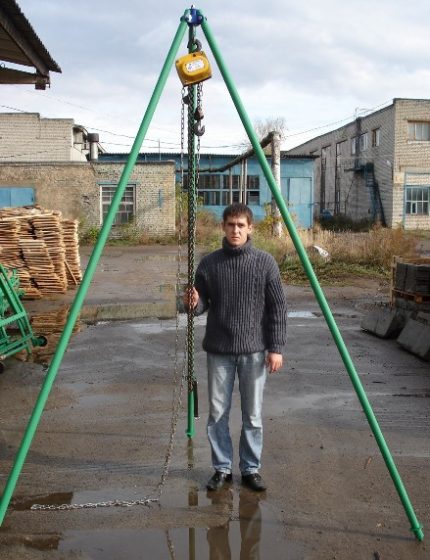
To understand what and how we will tinker, we will consider in general terms the essence of shock-rope work.
From a great height, a projectile pipe is thrown off to the place of the future water intake point designated with the help of a shovel or auger - well bore. An eye for the cable is welded at the top of the drill.
A hole in the upper part is cut to extract the drilled rock.
The lower edge is sharpened or equipped with teeth that optimize loosening the soil. 5 to 7 cm above the conditional bottom, a ball or flap valve is arranged inside the pipe to capture and hold loose rock.
Zhelonka - an indispensable tool for sinking loose sand, gravel, gravel. It is often used in combination with other drills. Alternate with a screw or glass, not able to remove loose and water-saturated deposits.
Non-cohesive particles of soil are trapped inside the choke thanks to a valve located at the bottom of the casing. The auger, bell, glass does not have such advantages.
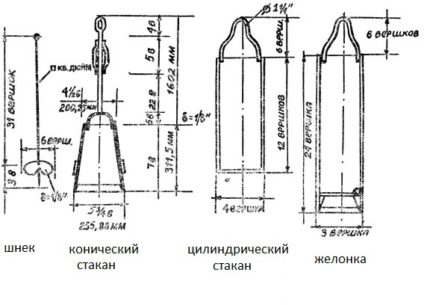
The drill drop procedure is repeated many times. The result of the process is a third filled with soil body and increasing by 30-40 cm hole in the surface of the earth.
The filled baffle is removed from the barrel with a winch, turned down the hole and cleaned with the blows of a heavy hammer.
Then the shock-rope drilling process is resumed and repeated until a well of the depth that was planned to be obtained is formed at the place where the drill fell.
It’s not necessary to buy a ready-made installation - you can make a bastion yourself for drilling and cleaning.
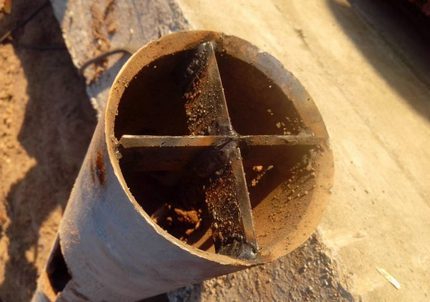
To create one drill in this case is pointless, therefore, we will tell you how to build the entire drilling rig together with the shell.
- Choose a place, where, according to our calculations and assumptions, the well should be located. We outline it by making a small indentation with an ordinary shovel.
- We install a tripod over the pit 2-3 meters high. We equip the top of the tripod with a well-fixed block for the rope. You will also need a winch, which we attach to the supports. It’s good if there is an electric winch, but a manual winch is also suitable.
- Prepare the hammer drill itself. For this purpose, we will need a thick-walled pipe, the diameter of which corresponds to the size of the mine of the future well.
To make a drill, we take a strip of thick metal and weld it to the upper end of the pipe, placing it perpendicular to the longitudinal axis of the projectile.
On the axial line of our pipe in a welded metal strip we drill a hole corresponding to the thickness of the rope on which the projectile will be fixed.
The bottom end of the pipe also needs processing: you can make a gear or ring sharpening on it. If there is a muffle furnace, you can harden the drill in it after the grinding procedure.
Drill for shock-rope drilling is not so easy to clear from the soil that has accumulated in it. To speed up this routine operation, you can make not a window-hole, but a vertical slot, passing through almost 2/3 at the top of the pipe.
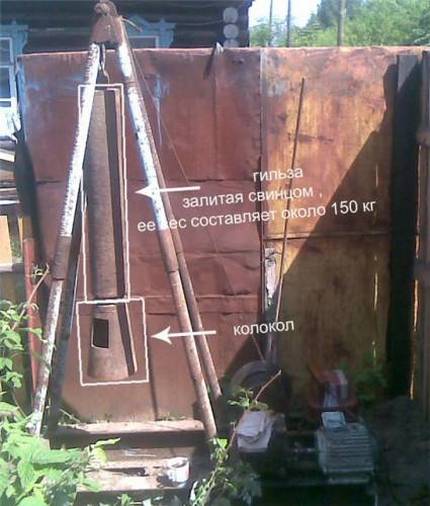
The heavier the drill, the faster you can achieve the desired result, but you must take into account the power of the winch, which will pull the drill with soil from the wellbore.
So, if its power still allows, the projectile can be weighted by placing removable metal loads in the upper part of the pipe.
You may also be interested in information on well completion, flushing after drilling and winter insulationconsidered in our other article.
Conclusions and useful video on the topic
This video clearly and readily describes how to make a reliable and functional spiral drill using available materials and easy-to-use tools.
Obviously, a person with skills in working with a welding machine and the most common locksmith tools will cope with the manufacture of a drill with his own hands.
Using a homemade shell, you can manually perform drilling work at your summer cottage. This will significantly reduce the total costs that were planned to provide water to your territory.
Have you made a homemade drill of a different design? Or do you know the secrets of improving the projectile? Perhaps you do not agree with the theory and recommendations set forth in our article? Please write about this in the comments below.
I have been working with such an installation for many years. Very compact and quite fully assembled all in one place.
I would not choose between a screw drill and a spoon drill. It is necessary, if possible, to have both. Under different conditions, penetrations come in handy. Well, I made a three-legged bed wooden. Still, a couple of logs are easier to find in any holiday village, and it is quite structurally resistant material!
Actually, this auger drill is actually good, but it is rather inconvenient to use it in sandy, gravelly soils, on gravel and pebbles. It is difficult to raise drilled incoherent rock to the surface. On my own I can say how I was tormented when I was drilling holes for racks. The depth is only 50 cm, but considering that I needed to drill 23 holes, it took me all this until 17 hours.
But this is with the situation that a lot of rubble and pebbles came across. Drilling on clay soils is much easier and simpler.
Incorrectly holds the grinder, and even without a casing ...
The Bulgarian does not forgive mistakes!