Plastic sewer wells: varieties + installation features
The arrangement of sewage involves the installation of wells for system maintenance. If previously this task was carried out by reinforced concrete structures, today due to the heaviness of the structures and the complexity of their installation, they were replaced by polymer analogues.
What are the advantages of plastic sewer wells in front of traditional hydraulic structures, and what installation features they assume, we will consider in the article.
The content of the article:
Scope of plastic wells
In the post-Soviet space sewer wells erected mainly from reinforced concrete rings. To increase the tightness of the structure, the joints between them were sealed with cement mortar with fiber compaction of technical flax.
But under the influence of temperature fluctuations and other environmental influences, the interswave embedment cracked over time, concrete rings shifted relative to each other, as a result, the mine lost its tightness and partially collapsed.
Such a nuisance does not threaten modern plastic wells. The solidity of the product allows to achieve tightness of the joints.
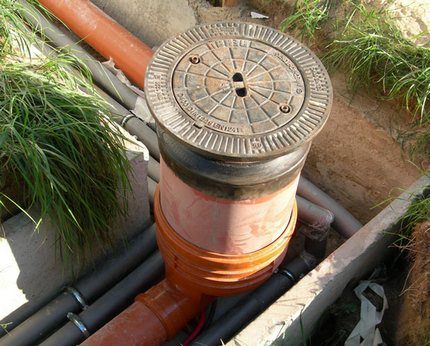
Ready-made sewer tanks made of plastic can be used both as stand-alone structures and as an addition to ready-made shafts made of concrete rings.
In the second option, they are reliable waterproofing sewer wells. A plastic sealed insert in a concrete or brick well protects the soil from seepage of sewage.
The main purpose of polymer wells is to connect sewer lines to each other.
But thanks to the design features, in addition to the main function, their application allows us to solve several problems at once:
- to provide conditions for monitoring the technical condition of the pipeline at the site of the nodal connection, changing the direction or diameter of the pipe;
- create conditions for laying branches of sewer pipelines at different levels;
- reduce / increase the flow rate of wastewater;
- guarantee access to the sewer section enclosed in the well for inspection and maintenance.
Large-sized collector sewer wells contain shut-off and adjustable equipment and pumps, if there is a technical need to stimulate the movement of flows.
Such hydraulic structures are used both for industrial sewage structures, and for the laying of household, storm, drainage networks.
Design features and production standards
Regardless of the type of material used, the design of sewage wells is the same. The construction is a shaft deepened into the earth of a cylindrical shape, at the bottom of which a kinet is arranged - a tray for two or three pipes with sewage.
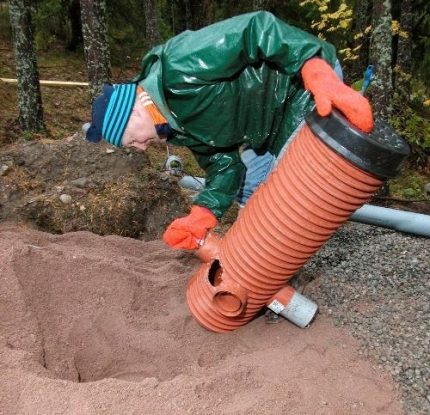
The extension of the structure is regulated by the use of extension cords and extension shafts. To gain the required length of the structure, they are joined together, creating a strong and tight connection.
Often, extension models are also used to extend the structure. Acting as connecting elements, in parallel with this, they serve as a continuation of the wall of the structure.
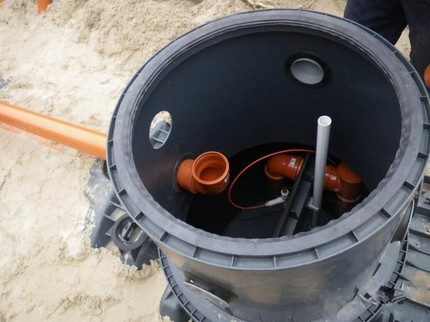
The upper part of the well is equipped with a ceiling with a hatch. When installing plastic wells, the choice is logical hatches made of polymersdue to which it is possible to ensure equally great durability of the entire structure.
The sizes of plastic models correspond to the dimensions of cast iron counterparts. When choosing a hatch, they are guided by its functional capabilities.
Depending on the degree of withstanding load, all types of sewer manholes divided into 4 categories:
- Standard "A15" It is used for installation on the green zone and pedestrian paths. It withstands up to one and a half tons.
- "B125" they are installed on sidewalks and in park areas and parking lots, where the load weight does not exceed 12.5 tons.
- "S250" used in the construction of sewers, the laying of which is carried out under city roads. Products withstand loads up to 25 tons.
- "D400" the most durable structures, capable of withstanding up to 40 tons, are designed for highways.
Hatches of the A15 standard can be installed directly on a well shaft, and their analogs of the B125, C250 and D400 categories - on a unloading ring or a telescopic telescopic tube.
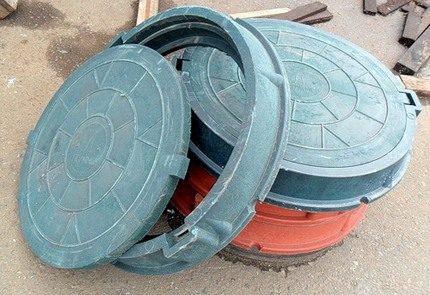
The neck is a transition element between the shaft and the hatch. Its main purpose is to receive and compensate outside loads that can damage the shaft and pipes leading to it. For this reason, it is a corrugated or telescopic structure.
The telescopic part of the shaft can be extended, taking the most convenient position for examining the state of the surface of the walls and access during repair work. The unloading ring at both ends is equipped with a thread, which makes the connection as tight as possible.
In the walls of the structure, holes are provided for summing the inlet and outlet pipes.
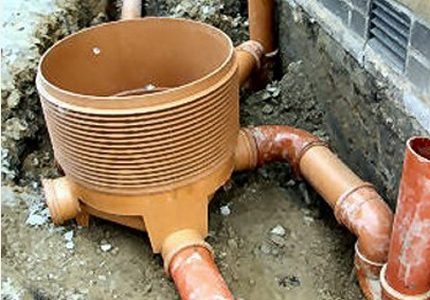
There are two types of wells, depending on the size of the structure:
- Diameter up to 1 m with an unattended mine. Compact inspection structures are installed at a shallow depth.
- Diameter over 1 m. The design allows you to easily maintain equipment and, if necessary, repair the structure.
The well itself is made of the same material that is used in the manufacture of ordinary sewer pipes. It can be structured or double-layer polyvinyl chloride (PVC), polyethylene (PE), polypropylene (PP).
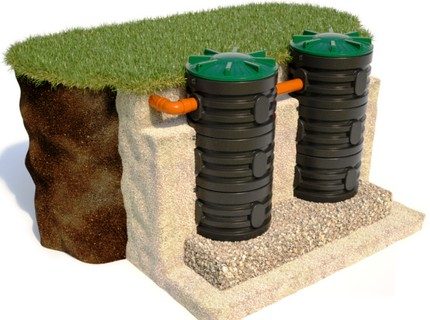
No less popular are models made of corrugated plastic. This solution simplifies the task of regulating the height of the tank and allows you to partially compensate for the load on the bottom, thereby significantly extending the life of the structure.
Both well options are available with both single and double walls. To withstand soil contraction from the outside, the products are equipped with stiffeners.
Advantages and disadvantages of plastic models
Structures made of composites with a polymer base are in no way inferior to traditional reinforced concrete ring-shaped modules. And in some respects, polyethylene and polyvinyl chloride wells are even superior.
Among the indisputable advantages of plastic wells for arranging a sewage system, it is worth highlighting:
- Affordable cost. The price, depending on the dimensions of the structure, types of plastic and the number of nozzles, varies from 5 to 50 thousand rubles.
- Lightweight design. The weight of the product even with a diameter of more than one meter does not exceed 100 kg.
- High compressive strength. The walls of the structure are able to withstand the high pressure created both inside it and from the outside.
- Easy transportation and installation. Installation of the structure can be performed without involving additional labor and the use of small-scale mechanization.
- Low thermal conductivity. Polymer formations are resistant to high temperatures. The trough part of the structure is also characterized by increased wear resistance. An exception can only be silting and overgrowing of elements.
- Resistance to corrosion and frost. A plastic well or a polymer liner made according to standards without losing practical qualities can withstand up to -60 ° C.
With proper use, polymer products can last more than half a century.
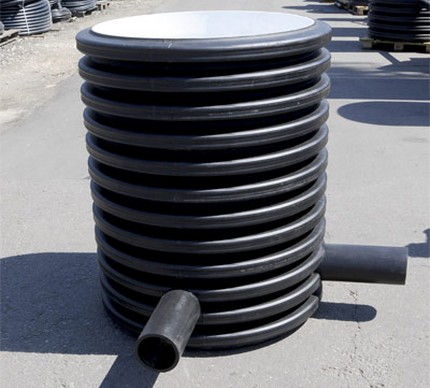
Not so long ago, products made of polyvinyl chloride were considered not strong enough and frost-resistant in comparison with concrete structures. But modern compounds are able to easily withstand frosts to -70 ° C, so they can be used in any climatic zone.
The only drawback of plastic structures is that although they have thick walls and additional stiffeners, they should be installed very carefully, as there is a risk of deformation of the container.
In addition, they are in most cases subject to repair. Any chip or crack on the wall leads to the disposal of the product. For this reason, it is extremely important to choose only high-quality and durable products.
Types of sewer wells
By purpose, polymer sewer wells are divided into three types: viewing, absorption and water intake.
Viewing models with kinets
Viewing models are mounted on potentially hazardous sections of the pipeline. Their main purpose is to provide access for monitoring the state of the system, the placement of special equipment and the need for maintenance of the structure. Not a single sewer pipeline can do without them.
Without fail, they are installed in places:
- turn of the highway;
- branch connections;
- changing the slope and diameter of the pipes.
One manhole can combine up to three to four traffic streams.
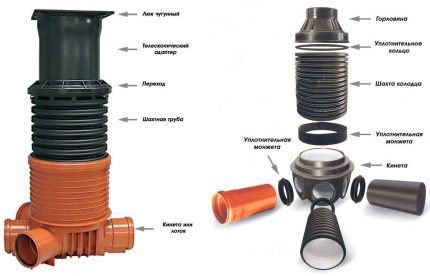
When arranging a sewer system, inspection plastic wells are placed at a distance from each other, regulated by regulatory documentation. The larger the diameters of the installed hydraulic structures, the greater the normative permissible distance between them.
Additional information on different types of inspection sewer wells is provided in this article.
Absorption drainage structures
Structures of this type are installed where there is no possibility to freely dispose of wastewater. They are cylindrical plastic shafts with a depth of two meters and a diameter of one and a half meters.
Unlike manholes, models of the absorption type do not involve the installation of a thrower. Instead, the bottom of the tanks is equipped with a grid or lined with materials that have a drainage effect: gravel, crushed stone or crushed brick.
The same material is also used as a sprinkling of the outer walls of the well.
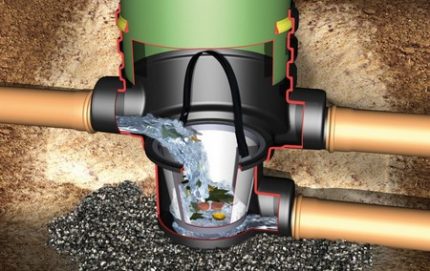
The minimum insertion height of the drainage pipes into the walls of the plastic well is 40 cm. Thanks to this solution, the bottom of the tank, in addition to the main task, serves as a sand trap, which traps sedimentary particles of sand and other inclusions present in the water.
A simple drainage well can be built with your own hands, more in the article - How to make a drainage well with your own hands and bring pipes to it
Water intake storage tanks
The main function of water intake wells is to accumulate wastewater until it is pumped out, transported, and transferred to treatment facilities. The option of "final destination" depends on the degree of water pollution.
Since storage tanks are designed to hold tons of fluid, they are quite impressive in size.
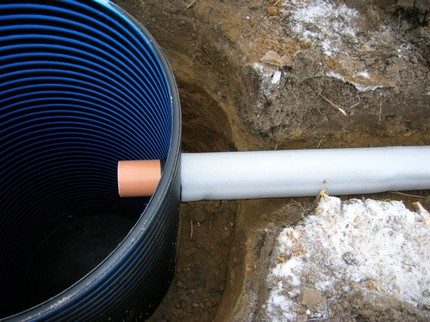
Water-receiving plastic tanks have completely sealed walls and a bottom. One of the prerequisites for the arrangement of water intake wells is that the lid is leakproof.
This is necessary in order to prevent overflow of the sewage system after heavy rainfall.
Competent selection criteria
The price of polymer wells consists of three main parameters:
- Material quality and wall thickness.
- Dimensions of the structure (inner diameter and height).
- The number of nozzles.
On sale meet monolithic and prefabricated models. The price of monolithic products is much lower than prefabricated analogues.
Wells with a monolithic body are used in those cases where it is necessary to ensure high compressive strength of the walls of the structure.
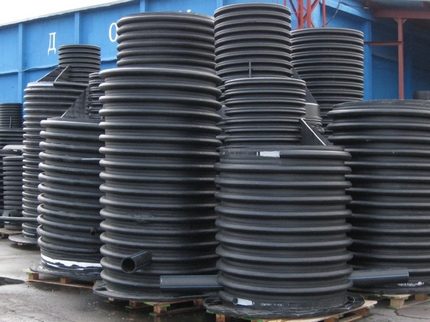
Due to the static nature of the internal volume of the structure, when choosing wells with a monolithic body, it is important to correctly evaluate the amount of water that will flow into it.
Keep in mind that there are models in which the supply pipes are already integrated. But there are also options where you need to carry out the insertion of the inlet and outlet pipes yourself.
Prefabricated structures allow you to create wells of any height. They consist of components, each of which is equipped with a sealing ring, which ensures the tightness of the structure.
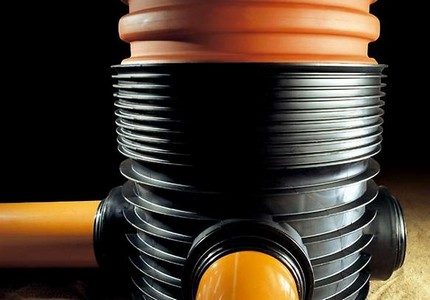
When purchasing a plastic well for the discharge of technical effluents, pay attention to the type of material used. It must be resistant to aggressive environments, because during operation it will be exposed to the presence of organic solvents present in it.
Models made of polyvinyl chloride are famous for their incombustibility and high resistance to chemicals. If you need high tightness and resistance to temperature extremes, it is worth choosing models made of polyethylene. They perfectly compensate for soil pressure in the cold season.
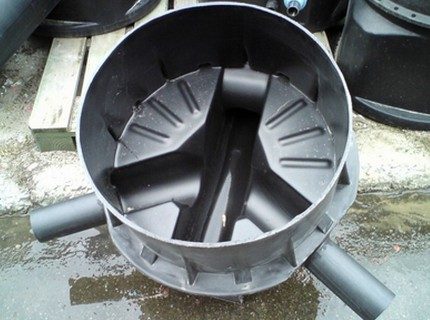
On soft soils, where there is a high probability of a load on the walls of a hydraulic structure, it is recommended to install polypropylene wells. They have high indicators of wear resistance and ductility. They can be welded.
Do not try to reduce the item of expenses, refusing to buy from kineta. The damage to such a “saving” is many times greater than the direct financial gain.
The absence of a wastewater chute makes it difficult to remove drains from the well. In most cases, this leads to frequent contamination of the system with large fraction debris, which creates a lot of resistance to the flow of wastewater, and as a result, the structure quickly wears out and fails.
Wells made of polyethylene of standard dimensions can be purchased at hardware stores. A mine of specified dimensions can also be ordered on an individual project.
Basic installation rules
The installation technology of polymer wells is not much different from the installation process of similar sewer structures made of other materials.
The work is carried out in several stages:
- Digging a pit. Having measured the dimensions of the installed structure, they dig a pit 10-20 cm wider.
- Foundation preparation. When arranging a storage facility, the bottom of the pit is lined with a 20-centimeter layer of pebbles, and then cemented. For the construction of a drainage structure, the bottom is concreted only along the perimeter, and the inside is lined with a 40-centimeter layer of gravel or gravel.
- Installation of a well. Using a tripod, ropes and cables, the container is lowered to the bottom of the pit. To prevent displacement and increase the reliability of fixation, it is fixed in a predetermined position by metal chains or belts.
- Connection of sewer pipes. To seal the joints and give them strength when connecting the outlet openings of the pipes, sealing cuffs are used.
- Perform backfill. Before filling, if the container is not protected by anything on the outside, it is recommended to fill the tank with water to avoid deformation due to pressure drops.
- Installation of the hatch. First, a support ring is installed in which there are technological holes, and then a cover is placed in the ring so that it is aligned with the corresponding grooves.
During the work, the current SNiP for work on installation of sewage systems.
Conclusions and useful video on the topic
Step-by-step installation technology is graphically presented in the video:
The technology for creating sewer wells made of plastic:
The use of plastic wells for the construction of sewers greatly facilitates and reduces the cost of work. This is a worthy alternative to the usual reinforced concrete structures. Heat-resistant, sealed and easy-to-install elements are easy to assemble, quickly install and require virtually no maintenance.
Looking for a suitable sewer well model? Or have experience using such installations? Please leave comments on the article, ask questions and share the skills of installing wells.