Press for fuel briquettes: options for manufacturing installations for pressing sawdust with your own hands
Drowning with sawdust or shavings is a common thing for the inhabitants of our country, borrowed in European countries. Their popularity is due to the cheapness of raw materials and its good specific calorific value during combustion. By creating a homemade briquette press, you can get high-quality fuel almost for nothing.
We will talk about how to make a simple and inexpensive machine for the manufacture of briquetted fuel. In the article we have proposed, the design is given, assembly tips are given. The production technology and requirements for the source wood material are given.
The content of the article:
Briquette Technology
Production of pellets and briquettes from woodworking waste by pressing is a long-established process. Therefore, when creating a home-made machine for obtaining high-quality "Eurodroves", you do not need to invent anything, but you can apply existing practices.
Description of the physics of the process
The use of loose wood material for heating finds its application in small boiler rooms and stoves. Sawdust gives the same energy as a tree of similar mass and moisture, but storing it in its natural state leads to the appearance of dirt and dust. Therefore, such waste is pressed into briquettes of various shapes.
With some assumptions, we can say that wood consists of fiber (cellulose) and its binding substance - lignin. Each instance of sawdust and shavings retains its integrity thanks to this polymer. In order to establish strong bonds between the individual pieces, they must also be glued.
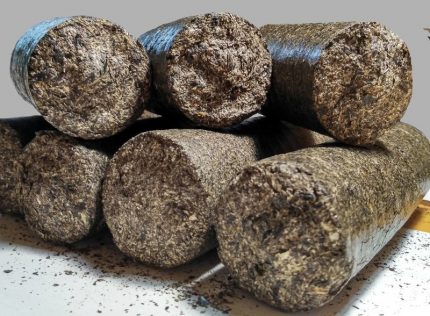
During pressing, strong pressure is generated on the sawdust, as a result of which lignin is released from them and holds the material together in a mold. This connection, of course, is not as strong as in solid wood, but it is enough so that the resulting briquette does not fall apart.
The amount of lignin in wood of relatively dry mass depends on the tree species:
- fir: 30%;
- pine: 27%;
- spruce: 27%;
- aspen: 22%;
- birch: 19%.
The higher the percentage of lignin, the less pressure is needed to isolate it. Therefore, it is easier to independently produce briquettes based on sawdust from fir than from birch.
In addition to the classic press for production bulk fuel there is still an extrusion machine. The essence of his work is that under the influence of the screw, the substance passes through a gradually narrowing channel.
As a result, very high pressure is created. However, the implementation of this option at home is complex and requires specific knowledge, so it is better to stay on models with a mold.
Use of adhesive
In the industrial production of pressed fuel, machine tools are used to create a pressure in the range of 500 - 3000 atm. For some manufacturers (for example, the German company “RUF”), briquette formation occurs due to a combination of compression with a force of 2000 atm. and heating the feed to a temperature of 150 ° C. The density of such products reaches 1.2 kg / dm3.
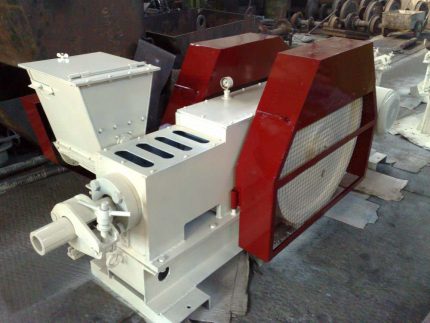
If you make a briquette press from improvised material with your own hands, then you will not be able to achieve such characteristics. Therefore, products will definitely have a lower density and be more prone to spillage.
Compensate for insufficient lignin release and achieve greater strength sawdust briquettes possible by adding a third-party adhesive, such as:
- Slurry. The required mass fraction of this binder dissolved in water is from 5 to 10% of the total weight.
- Wet corrugated board.
- The cheapest wallpaper adhesive diluted in water.
The percentage of corrugated board or glue is determined experimentally, since it depends on the size of the sawdust, their moisture content and the pressure created in the mold.
Requirement for Raw Materials Used
Even when using industrial equipment, it is difficult to obtain high-quality briquettes or pellets from wood waste if their thickness is more than 4 mm. The size of the material for home-made devices should be less. This is due to lower pressure and lack of heating of the raw materials.
Ideally, the sawdust diameter and chip thickness should not exceed 2 mm. The vast majority of wood waste is suitable for these parameters.
But there are times when the raw material is clogged with small branches, wood chips or a pickle (pieces of bark). Then, before pressing, to obtain a homogeneous mass, it is necessary to carry out preliminary preparation - to grind the material by passing it through a crusher.
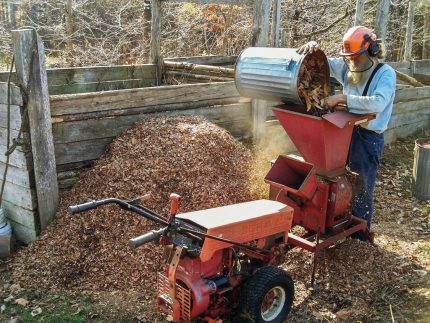
To achieve a good briquette density, raw materials clogged with grass, sand or soil should be avoided. The soil and plant layer, unlike clay, does not have astringent properties, so the pressed product will easily crumble.
It is also necessary to observe the condition on the percentage of the amount of bark - it should not be more than 5%. It is impossible to measure this, but visually the sawdust with a significant volume of the obzol look darker. Sawdust must be dry. Increased humidity leads to greater friability of the briquette and a decrease in its specific calorific value.
You can dry the raw materials in the summer either in the sun or in a ventilated room. In winter, drying should be carried out in the veranda or other utility room with a small positive temperature. For more intense evaporation, you can use forced ventilation.
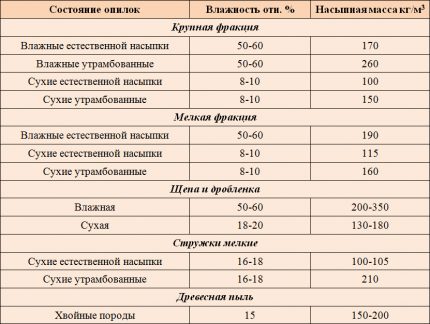
If the pressure in a homemade press for the manufacture of sawdust briquettes is insufficient to isolate lignin, then the raw materials are not dried, and together with an additional bonding agent, on the contrary, they are soaked in water. In this case, better uniformity is achieved with mixing, and excess moisture will be removed by tamping.
The main elements of the press
The main elements of an ordinary press are a mold (a glass in which loose substance is placed), a piston and a pressure-generating mechanism. It is easy to make them yourself, as they are typical for briquetting machines.
Mold device
A glass where sawdust or shavings are poured is called a mold or a chamber. The briquette parameters will depend on its geometry.
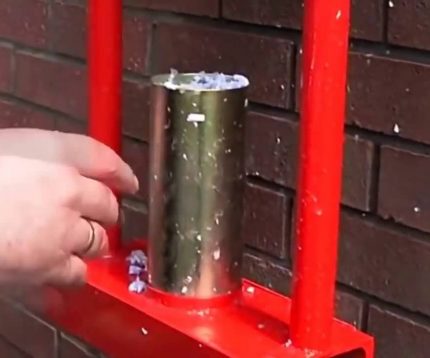
Typically, a chamber is constructed from a piece of steel round or profile pipe. The base of the piston, which enters the glass, is cut out from a thick-walled (at least 3 mm thick) plate.
In the manufacture of the mold, the ratio of the following values must be taken into account:
- cross-sectional area of the mold (s, cm2);
- pressure applied to the piston (u, kgf);
- specific pressure on raw materials (p, kgf / cm2).
These values are related by the ratio:
p = u / s
Briquettes using an additional binder hold their shape well if they are formed at a specific pressure of more than 150 atm. (1 atm. ≈ 1 kgf / cm2) Based on the possibility of the created force by the piston, the cross-sectional area of the chamber is calculated.
For example, if there is a hydraulic jack of 10 tons, then:
s < u / p = 10000/150 = 67 cm2.
For such conditions, a profile square pipe with a side length of 80 mm or a round pipe with a nominal diameter of up to 90 mm is suitable.
The length of the resulting briquette (l) depends on the height of the mold (h), the density of raw materials in the original dry (q1) and briquetted (q2) condition:
l = h * (q1 / q2)
In addition, after the first compression, you can again add chips to the glass and repeat the procedure. In this way, you can bring the length of the resulting product to almost the height of the pressing chamber.
In the process of compressing sawdust, moisture is released from the briquette. In order for it to freely exit, the camera is perforated with small but often located holes.
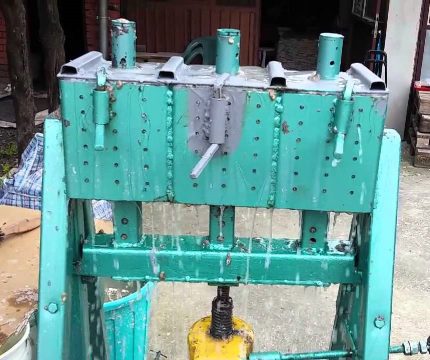
After the briquette is formed, it must be pulled out of the mold. Using a spring and a false bottom, as is often recommended on the Internet, is impractical. High pressure completely compresses the spring, therefore, over time, its shape is curved, as a result of which it loses its properties.
Therefore, you must either make a removable bottom of the mold and push the briquette, or build a collapsible glass. In the second case, he will need to make an additional shirt from the bar.
Available ways to create pressure
There are three common ways to achieve pressure, which are well suited for a self-made press for producing fuel briquettes: the use of a lever, a hydraulic jack or screw. Each of them is good in its own way, and their implementation in practice is not very complicated.
Using muscle strength and leverage
Usually, a metal pipe is taken as a lever. It should not bend under the influence of the muscular strength of a person. For example, a reinforced water pipe with a diameter of 40 or 50 mm and a wall thickness of 4 - 4.5 mm is well suited.
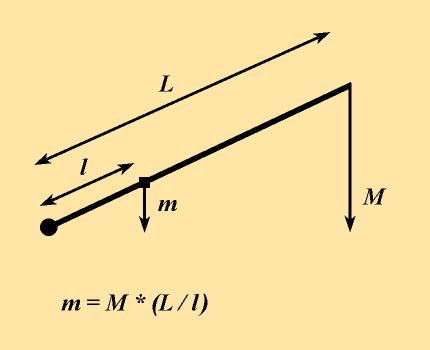
The length of the lever and the distance from the fulcrum to the connection with the piston is chosen not only focusing on achieving the desired pressure. Another important parameter is the depth of immersion of the piston in the glass (h, cm).
It is calculated by the formula:
h = R * (l / L)
Here R (cm) is the height to which the end of the lever will lower.
It is desirable to make the design so that the immersion depth of the piston is sufficient to form a briquette without re-compression with a preliminary addition of material. This will greatly increase the pace of production.
The required piston immersion depth (h, cm) can be calculated by knowing the initial dry (q1) and briquetted (q2) the density of the raw materials and the height of the glass (H):
h = H * (1 - q1 / q2)
If for any reason an error has occurred (as a rule, due to incorrect determination of the value of the initial density of the raw material) and the depth of immersion of the piston is not enough to give the product the necessary hardness, then it is not necessary to digest the entire structure.
You can either reduce the height of the glass, or, filling the sawdust, press one briquette in two or three passes.
Hydraulic jack application
Hydraulic devices such as familiar bottle jacks are used to create strong pressure. As a rule, in a farm where there is a car or other equipment, there are such hydraulic units, however, their carrying capacity may be insufficient.
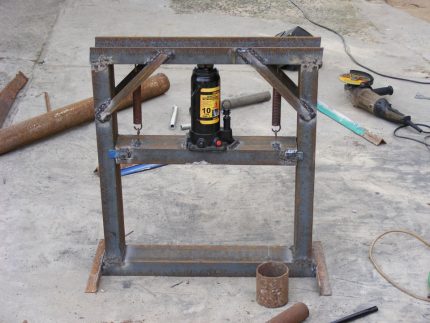
Jacks are inexpensive. So, models designed for 30-40 tons can be purchased for less than 5 thousand rubles. And with such indicators it is already possible to obtain briquettes of large cross-section or several (3-5) copies of the usual size at once.
To obtain several briquettes at the same time, the right amount of molds is put in a row. The middle movable frame must be strong so that it does not bend over time. It is best done from an I-beam or a thick-walled profile pipe.
The pressing process itself takes longer than when using a lever design. However, the use of a powerful hydraulic jack allows to achieve much greater specific pressure on the workpiece. Briquettes are more even and dense and already have an attractive presentation.
Screw pressing mechanism
The principle of operation of a manual screw press is similar to a lever one, only the applied force is transmitted at an angle of 90 °. The larger the diameter of the handle and the smaller the thread pitch, the greater the pressure increase ratio.
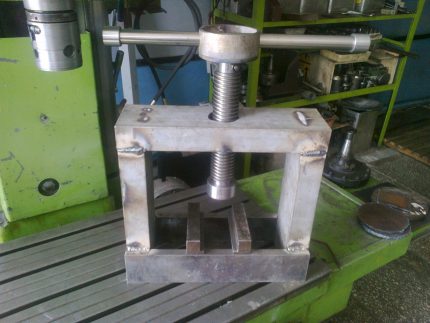
This design also allows you to create more pressure than a machine based on a lever mechanism. A significant minus is the slowest work rate among the options presented.
However, the pluses include:
- simplicity of design;
- the opportunity to buy such a press for little money with little refinement for the needs of briquetting;
- small size.
When working with a screw press, you should not use it “to the stop”, when there is already not enough physical strength to crank the mechanism. In this case, the force exerted by a person acts on the thread on the one hand, and the resistance force of the obtained briquette on the other (under 90 °). This will lead to rapid wear of the thread or its breakdown.
In order not to overdo it and not break the mechanism, it is necessary to achieve a sufficient result on test specimens and either install a latch or make a marker on the thread marking its maximum permissible position.
Conclusions and useful video on the topic
Create a homemade lever press. Production of the main parts and a description of the principle of operation:
Improving the design of the machine and the briquetting process itself:
A machine for the simultaneous production of several briquettes based on a hydraulic jack:
It is not difficult to make a machine for sawdust briquetting on your own. You can choose from the lever, hydraulic or screw principle of creating pressure. But you need to remember that the quality of the manufactured products will depend not only on the assembled mechanism, but also on the preparation of raw materials.
A properly set process will help to provide your economy with high-quality and cheap fuel and even arrange its implementation.
Want to talk about how they made briquettes for heating with their own hands? There are valuable recommendations on the topic of the article, which you are ready to share with visitors to the site? Please write comments in the block below, here post photos and ask questions.