DIY heating manifold: schemes and assembly features
The decisive task in the design of an autonomous heating system is the uniform distribution of the heat carrier. This task in the heat supply system is performed by a control and adjustment unit - a distribution manifold.
Uninterrupted operation and the reliability of the heating circuit largely depend on the competent choice of the device, high-quality installation and connection. If you want to install a heating distribution manifold with your own hands, then it is necessary to carry out calculations in advance and design the wiring.
We will help you in resolving these issues. In the article, we examined the design of the collector group, identified the pros and cons of the heating system with a comb, described the design and installation rules of the distribution unit.
The material is supplemented with practical advice on the selection of components, assembly and connection of the collector to the heating system.
The content of the article:
The role of the collector in heating
When arranging a water pressure unit, it is necessary to adhere to the rule: the total sum of the diameters of all branches should not be larger than the diameter of the supply line.
We apply this law to the heating system, but it will look like this: the output nozzle of the boiler with a diameter of 1 inch is allowed for use in a dual-circuit system with pipes with a diameter of ½ inch.
For a house with a small cubic capacity that is heated exclusively by radiators, this kind of system is considered productive.
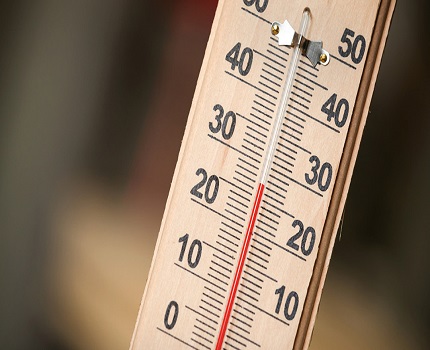
In practice, a private cottage is equipped with a more modernized heating scheme, where additional circuits are arranged:
- floor heating system;
- heating of several floors;
- utility rooms, etc.
When a branch is connected, the level of working pressure in the circuits becomes insufficient for high-quality heating of all radiators, respectively, and the comfortable atmosphere will be violated.
In this case, for a branched heating line, a balancing unit is equipped with a distribution manifold. Using this method, it is possible to compensate for the cooling of the heated coolant, which is typical of traditional one- and two-pipe schemes.
By means of equipment and valves, the necessary indicators of the temperature of the coolant for each of the lines are adjusted.
The main characteristics of the collector system
The main difference between the collector and the standard linear method of redistributing the thermal carrier is the division of the flows into several channels independent from each other. Various modifications of collector systems can be applied, differing in equipment and size range.
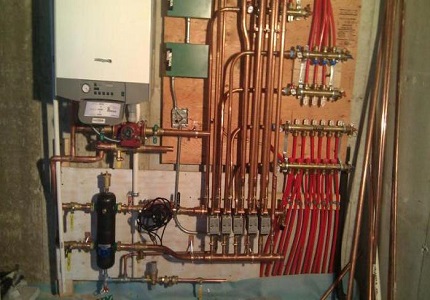
The design of the welded manifold is quite simple. To the comb, which is a pipe of circular or square section, connect the required number of nozzles, which, in turn, are connected to individual lines of the heating circuit. The collector installation itself is interfaced with the main pipeline.
Shut-off valves are also installed, through which the volume and temperature of the heated fluid in each circuit are adjusted.
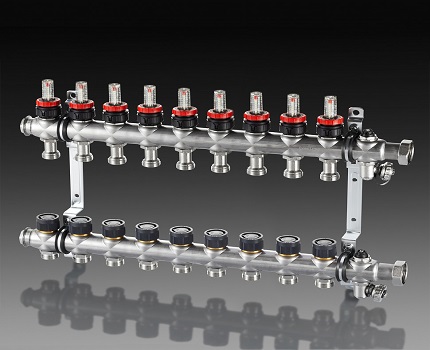
The positive aspects of the operation of the heating system, which is based on the distribution manifold, are as follows:
- Centralized distribution of hydraulic circuit and temperature readings occur evenly. The simplest model of a ring comb of a two- or four-loop type can quite effectively balance the indicators.
- Regulation of operating modes of the heating main. The process is reproduced due to the presence of special mechanisms - flow meters, kneading unit, shut-off and control valves and thermostats. However, their installation requires correct calculations.
- Service convenience. The need for preventive or repair measures does not require shutting down the entire heating network. Due to the valve pipe fittings mounted on each individual circuit, it is possible to easily block the flow of coolant in the desired area.
Nevertheless, there are drawbacks to such a system. First of all, the consumption of pipes increases. Compensation of hydraulic losses is carried out by installing a circulation pump. It must be installed on all collector groups. In addition, this solution is relevant only in heating closed systems.
Modifications of collector assemblies
Before proceeding with the collection of the collector assembly, it is necessary to determine its functional load. The equipment can be mounted in several sections of the heat main. Based on this, the necessary equipment, dimensions and level of automation of the working cycle are selected.
In fact, for the full operation of such a node, two devices are needed. Using a comb, distribution is made along the contours of the thermal carrier from the central supply pipe. The return collector channel is represented by the collection mechanism and the point of departure of the cooled liquid into the boiler.
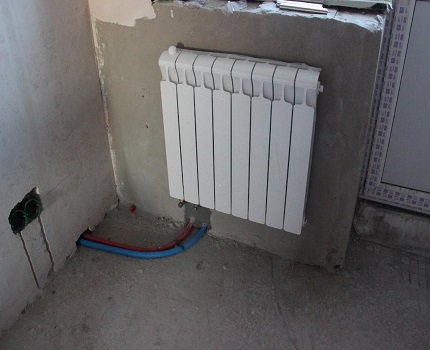
Installation of a home-made distribution group may be required when arranging water heated floors or to prepare standard heating with radiators.
Distinctive features of both options are their sizes and accessories:
- Boiler room. Welded collector group is made of pipes with a diameter of up to 100 mm. A circulation pump and shut-off valves are installed at the feed. The return ring is equipped with shut-off ball valves.
- Floor heating system. A similar configuration is present in this kneading unit. With its help, it is possible to significantly save on the consumption of thermal carrier, especially if flow meters are additionally installed. More information about the mixing unit in the underfloor heating system is written in this article.
Each of these solutions provides an individual installation scheme. Correct installation of all elements can be carried out only after detailed miscalculations of all parameters of the operating point.
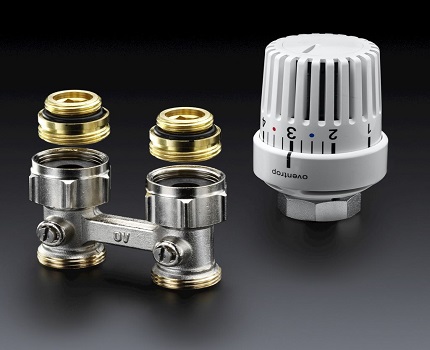
There are also differences in the required amount. circulation pumps. In the boiler room, each line is equipped with this device. For underfloor heating, only one is provided.
Distribution node design
There is simply no universal scheme for a beam-type heating project. Each case is individual, therefore, the unit is completed with the necessary devices in a private way. However, it is worth familiarizing yourself with generalized recommendations and rules.
Rules for installing a comb
Collector installation is not possible in the apartment. However, there is an exception to the rule - in some houses when arranging all communications, additional valves are mounted, through which the heating circuits are connected. Such a device allows for individual wiring of the collector.
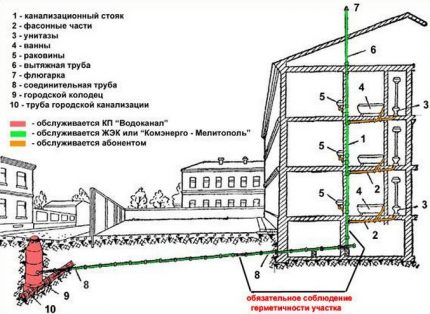
Schematic arrangement of heating should be designed so that the location Mayevsky's crane was on the comb. This option is considered optimal, because over time, accumulated air will need to be released from the circuits.
Features of the radiation group
The beam group of the wiring has many nuances, but some of them are also characteristic for heating of another modification.
Features of the comb system:
- The circuit should include expansion tank, with a volume of more than 10% of the total volume of the thermal carrier.
- The optimal location of the expansion tank is on the return pipe in front of the circulation pump, since there is a lower temperature regime.
- If thermo-hydraulic distribution is used, the circuit is designed so that the tank is placed in front of the main pump, which is responsible for the forced movement of water in the boiler piping.
- Installation of the circulation pump is carried out in a strictly horizontal position. If you do not adhere to this rule, the device will lose cooling and lubricant during the first air lock.
The distribution group can be assembled from various materials: polypropylene or metal. Selection is based on work skills and the availability of tools for connecting parts.
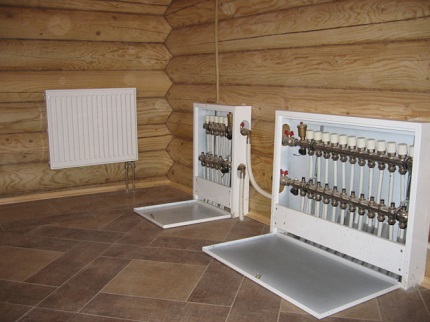
Also important is the process of selecting pipes for the installation of a distribution group.
The main factors to consider when choosing contour elements:
- Acquisition of pipes only in bays. Due to this, connections are not made in the wiring mounted under a concrete screed.
- Heat resistance and tensile strength must be determined individually, based on the technical data of the heating system.
Due to the predictability of the performance of autonomous heating, you can use polypropylene pipes. They have no unwanted compounds and are sold in solid lines of 200 m.
The material is heat-resistant and can withstand up to 95 ° C with an acceptable level of tensile pressure of 10 kg / 1 cm2.
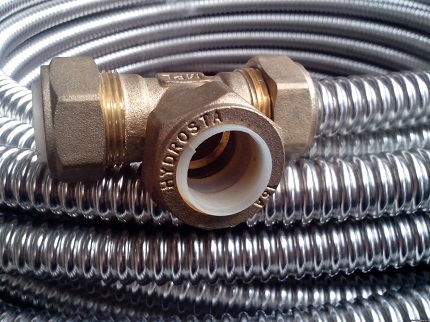
For a multi-story building, it is preferable to choose a stainless steel corrugation pipe.
This material shows excellent technical capabilities to cope with such a load:
- preheated coolant up to 100 ° C, which is more than enough for the heating circuit;
- pressure up to 15 atm .;
- fracture pressure up to 210 kg / 1 cm2.
Fittings designed for polypropylene can be plastic or made of brass. The fitting is equipped with a snap ring, which is strung on the pipeline.
An important characteristic of polypropylene pipes is the memory for machining as a result of which plastic deformation of the substance occurs.
For example, when stretching the pipes with an extender and installing the nozzle in the connector, after a certain time the pipe will return to its previous state and compress the part. The contact can be fixed with a snap ring.
Calculation of the heating collector
Initially, for the manufacture of a thermo-hydraulic comb, it will be necessary to calculate its main parameters - the length, diameter of the branch pipes and the number of branches of the heat main. You can calculate these characteristics yourself or use special software.
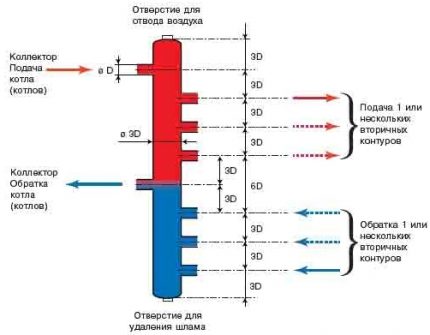
The hydraulic balance of the structure is a basic condition that requires compliance. Applying the rule of three diameters for the hydraulic separator, you must perform the following action - summarize the diameter of the cross-section of the connected circuits.
As a result, we obtain an amount equal to the diameter of the main pipe connected to the supply line. The use of this principle reduces the likelihood of imbalance in the entire heating system.
As a place for the distribution unit use a special cabinet or enclosure. When arranging the system, it is necessary to adhere to the permissible minimum distance between two heat-conducting input and output lines - 6 diameters.
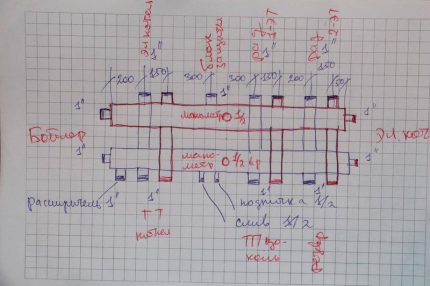
Also relevant is the question of the correct selection of the performance of the circulation pump. For this, it is necessary to calculate the specific rate of water consumption of the system and, based on the results, make the choice of the pump.
If the circuit is complicated by several combs, a miscalculation is performed for each individual circuit and, in general, for the entire system.
Self-assembly of equipment can be carried out by means of a pipe with any type of section. This aspect does not affect the operation of the device, and does not increase local losses. Due to the circulation pump, they will be compensated.
Rules for the selection of components
Having completed all the calculations, the next step will be the selection of the necessary set of mechanisms. The simplest set consists of valves. However, with such a device it is difficult to regulate the power of individual heating lines.
To solve this problem, crane boxes are installed on the feed comb, through which a smooth adjustment is possible. Rotameters are mounted on the return manifold.
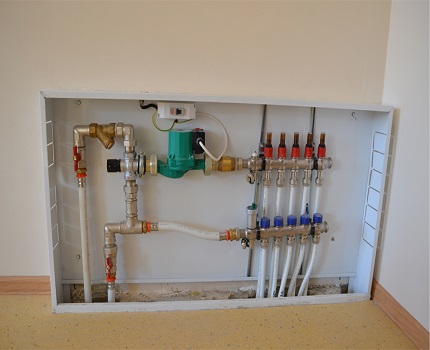
For warm water floors, the configuration scheme will be different.
For assembly, you will need these elements:
- Stop valve. Installation is made on connecting branch pipes. With the help of this armature, a complete or partial shutdown of the coolant inflow is carried out. Automatic modification is recommended.
- Rotameters. Such elements are mounted on the reverse collector. They perform a similar function, like the previous element, only in the return pipe.
- Kneading knot. By mixing the flows of hot and cold water, the desired operating mode of heating is optimized.
The manifold kit must be equipped with a safety group led by a pressure gauge, air valve, thermostat and circulation pump. It can be supplemented by servos, the control of which is reproduced through the control electric unit. Thus, the operation of the system can be automated.
The subtleties of self-assembly
Before the manufacture of the collector, it is necessary to draw up a diagram with the location of all the elements of the assembly. As a manufacturing material, it is better to choose steel pipes with a square type of section. This type is simple to process, which significantly reduces the labor costs for installing the nozzles.
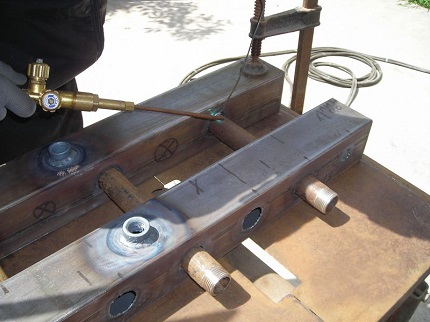
The phased production process of the prefabricated design of the distribution unit is as follows:
- Marking and cutting of the main body. According to the design scheme, it is necessary to mark the profile pipe. Using a gas cutter, holes are made in the marked areas.
- Connection Preparation. A thread is cut on the nozzles by means of a die.
- Picking. Next, the prepared pipe sections are welded to the body. Their fixation must be carried out by tack welding. Then, during the main welding, the workpieces are welded along the edges.
- Fasteners. Brackets for mounting are welded to the unit.
- Cleaning and topcoat. After stripping, the body is primed and covered with heat-resistant paint for metal products. The feed and return circuits are painted in two different colors for ease of determination.
If polypropylene pipes are used for manufacturing, it is worth paying attention to the presence of a reinforcing layer in them. In its absence, the plastic structure may be subject to deformation from the present temperature.
For those who do not have special tools, you can assemble a comb from separate finished elements. It is better to select components of one company.
Installing the comb in the heating system
The primary task is to check the distribution manifold for leaks in the joints. Installation is implemented according to the design scheme. Depending on the material used for the manufacture of the main unit, the connection conditions are determined.
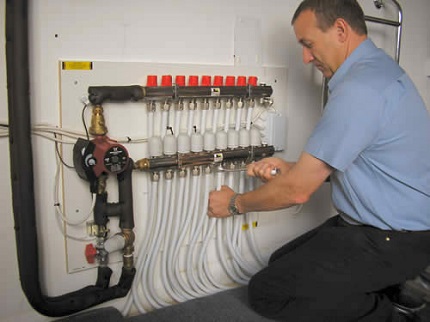
The choice of connection technology depends entirely on the modification of the device used.
In addition to the exposure level, during installation, you must follow these rules:
- electric and gas type boilers are connected to the upper or lower nozzles;
- in the end part of the structure, a circulation pump is mounted;
- the contours can be connected at the top or bottom of the comb;
- indirect heaters and solid fuel boilers must be connected to the side of the distribution group;
- the entire hydraulic separation unit for the underfloor heating system is placed in a protective box - this reduces the risk of damage to the components of the collector.
At the finishing stage, it is necessary to carry out a control run of heating in order to timely determine the hidden or obvious shortcomings of the construction made.
For more information on organizing a radiant heating system using a distribution comb, see this article.
Conclusions and useful video on the topic
Detailed technical process of assembling the collector group:
Ready-made combs for arranging a warm floor, equipped with not always the necessary functionality, due to their high cost, are not available to the general public. Let's see how to assemble a budget version of the design with your own hands:
The implementation of the distribution group can also be carried out using polypropylene pipes. How to do this, you can find out from the video:
The correct selection of components and installation of the collector unit is the key to effective and reliable operation of the heating main. Due to the minimum number of compounds, the risk of leaks is minimized. An important plus is the ability to control and configure each heating circuit.
Share with your readers your experience in assembling and connecting the distribution manifold. Please leave comments on the article, ask your questions and participate in discussions. The feedback form is located below.
Good and efficient heating system. After installing the collector and connecting a warm floor and radiators to it, it became much warmer in our house than with batteries only. This is especially true for children's, bathrooms, where enhanced insulation is needed. Accordingly, the system is designed so that the coolant is delivered to these places with the optimum temperature for heating. In addition, the collector system can be controlled by choosing the most favorable heating mode.