Distribution comb of the heating system: purpose, principle of operation, connection rules
Owners of suburban cottages and private houses are increasingly abandoning the traditional one- or two-pipe wiring and prefer a manifold distributor. That allows more efficient use of fuel and create comfortable conditions in each room separately. Agree that refusing to reduce heating costs is irrational, especially since the temperature in the rooms will not suffer from this.
Have you also thought about connecting the collector and want to know more about this equipment? We will help you understand the topic - in this article we will examine in detail what the distribution comb of the heating system is and what its advantages are.
We highlight the significant disadvantages of its use, describe in detail the connection process, providing the material with visual photos. And also dwell on the basic connection rules, which it is desirable to observe. Here are some helpful video tips for installing and making combs yourself.
The content of the article:
The purpose of the distribution comb
Collectors (distribution combs) for heating are an important component of a modern heating system. In a simplified form, the comb can be thought of as a pipe with a plug at the end and several outlets in the form of nozzles that allow the coolant to be directed to individual points.
The number of taps can be different - it depends on the specific heating system and the number of heating appliances planned for connection.
Using the collector, the coolant flows in the heating circuit are optimized. It also smooths out pressure surges (water hammer), arising from the operation of boiler automation that regulates temperature conditions.
Heating combs are needed for arranging warm floors, but they are also used in radiator heating systems. Radiators are connected to the collector by beam pattern, i.e. Each of them has its own supply pipe and return, through which the coolant returns to the collector.
This heat distribution ensures uniform heating of the radiators and makes it possible to adjust the temperature in a single room or completely disconnect it from the heating system.
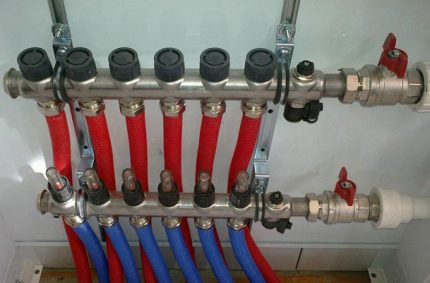
Another purpose of the comb is to connect additional devices - for example, in a house where there is already heating, a pool is built, and now it is required to provide water heating in it.
It is also possible to connect secondary energy sources to it - for example, solar panels.
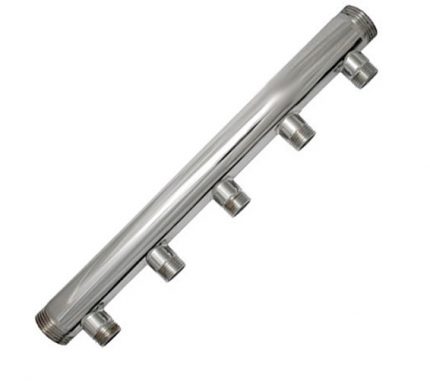
We list the advantages of acquiring a comb:
- uniform distribution of coolant, facilitating temperature control;
- local setting of set temperatures, heating only the necessary rooms;
- protection of the heating network from water hammer.
Commercially available distribution combs for today are cost-effective and high-tech equipment with a mass of sensors that monitor temperature, respond to deviations, signal malfunctions, etc.
Design of various types of combs
The most affordable will be a distribution comb with manual shut-off valves made in China or Turkey. The collet connectors located on it are put onmetal pipes.
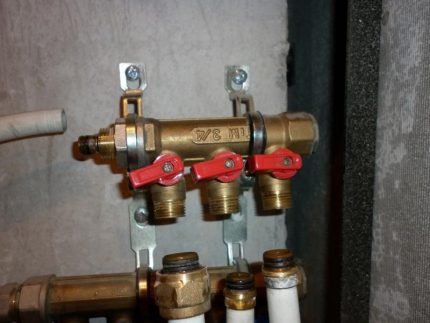
Threads at the ends are needed to connect the shutoff valves and the central supply / removal of hot water. In general, such a comb will cope with its function, but the term of its perfect service is not very long.
If disassembling the valves and replacing worn out seals does not lead to the initial tightness, you will have to buy a new manifold.
A comb with plugs on the return manifold (and on the direct one too) will be more complex in design. Instead, in the future, you can install flow meters and thermal heads. The forward and reverse combs in such models are already connected by a bracket for mounting on the wall.
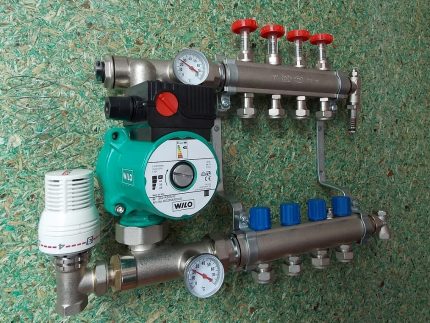
And finally, a complex and expensive, but the most efficient distribution comb with factory-installed flow meters and thermal heads.
The flow meters regulate the uniform delivery of the coolant to the destination, and with the thermal heads you can adjust the temperature for each outlet separately, just like for a heating radiator. More details types of thermal heads, the principle of their operation and installation features are discussed in our other article.
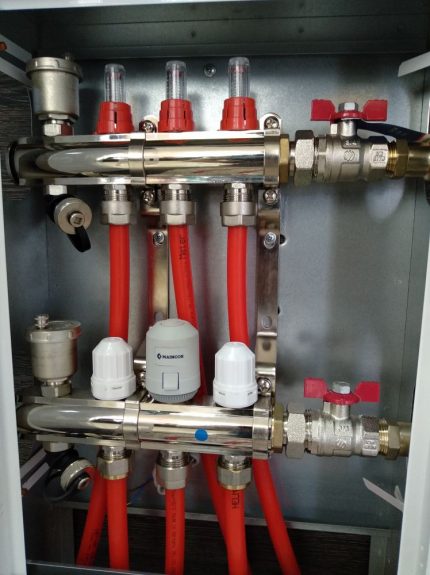
Even in the design process, you need to make a choice between different types of combs, but in any case, the collector system is a more preferable choice compared to conventional wiring according to criteria such as ease of use, durability.
Principle of operation of the distribution manifold
In modern heating systems, two types of distribution collectors are used - for boiler rooms and local ones. They have different dimensions and a slightly different principle of operation.
In the boiler manifold, the feed comb supplies the coolant to the links of the heating system, so it is equipped not only with taps, but also with circulation pumps. The second comb is the host.
In addition, pressure, temperature and a very important element are installed on the collector - water arrow. It maintains the optimum temperature difference between feed and return.
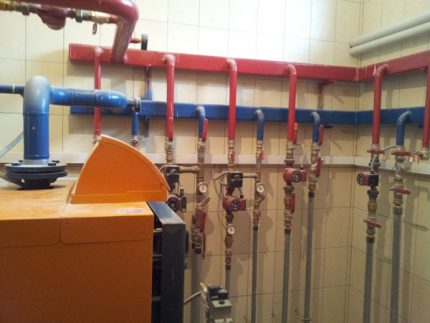
The local distribution comb differs from the central manifold installed in the boiler room, both in size and in principle of operation. In the heating system, there may be several.
If in the main collector the chilled water is completely replaced by hot water from the boiler, then in the small combs circulating water is diluted.
The coolant in them moves in a vicious circle until its temperature drops below a predetermined level.
Compliance with the temperature regime is controlled by a sensor, which, when the temperature drops critically, opens a valve that blocks the water from the boiler line. Hotter water comes in, mixing with the cooled.
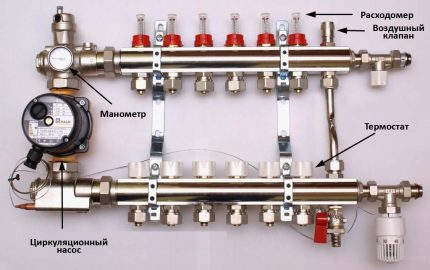
There are no hydroshots in such collectors, it is replaced by an additional circulation pump. He pushes the coolant in a circular space, periodically throwing a portion of hot water from the supply line.In this case, the same amount of chilled water returns there, but to the other pipe - the return one.
Local combs are used both in warm floors and for connecting radiators.
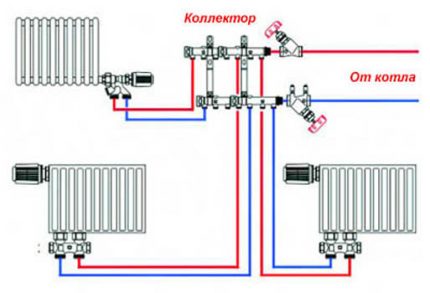
In order to achieve highly efficient functioning of the heating system within the whole house as a whole, it is recommended to integrate into it both the central distribution manifold and the required number of local combs. Together, they will give the desired result.
Calculation of the throughput of the combs
The calculation of the parameters of the distribution comb includes the determination of its length, the cross-sectional area of its section and pipes, the number of heat supply circuits. It is better if the calculations are done by engineers through computer programs, in a simplified version they are suitable only at the preliminary design stage.
In order to maintain hydraulic balance, the diameter of the inlet and outlet combs of the collector must match, and the total throughput of the nozzles must equal the same parameter of the collector pipe (rule of total cross sections):
n = n1 + n2 + n3 + n4,
Where:
- n - collector cross-sectional area 4
- n1, n2, n3, n4 are the cross-sectional areas of the nozzles.
The choice of comb should correspond to the maximum heat output of the heating system. What capacity the factory product is designed for is written in the technical passport.
For example, a distribution pipe diameter of 90 mm is used for power not exceeding 50 kW, and if the power is twice as high, then the diameter will have to be increased to 110 mm. This is the only way to eliminate the risk of unbalancing the heating system.
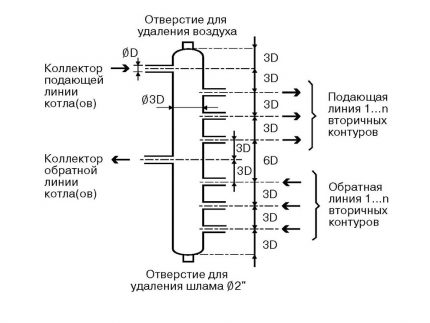
The rule of 3 diameters is also useful (see the figure above). As for calculating the performance of the circulation pump, the specific consumption of water in the heating system is taken as the basis.
Each pump is calculated individually - along the contours and for the entire system. The figures obtained in the calculation are rounded up. A small margin of power is better than its shortage.
Connection rules and installation features
Installation of the comb begins with the attachment of its brackets to the wall, where it will be located openly or in the cabinet. Then it will be necessary to connect the main pipes to the ends from the heat source and begin strapping.
Option # 1 - no additional pumps and hydraulic pumps
This simple option assumes that the comb will serve several circuits (for example, 4-5 radiator batteries), the temperature is assumed to be the same, its regulation is not provided. All circuits are connected to the comb directly, one pump is involved.
The characteristics of the pumping equipment must be correlated with the performance of the heating system and the pressure created in it. So that you can choose the best pump that is ideal for the characteristics and cost, we recommend that you familiarize yourself with rated circulating pumps.
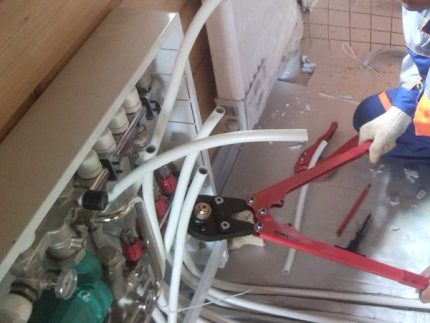
Since the resistance in the circuits is different (due to different lengths, etc.), it is necessary to ensure the optimal flow of the coolant by balancing.
For this purpose, balancing valves are not placed on the return combs. They can be regulated (although not exactly, but by eye) the flow rate of the coolant in each circuit.
Option # 2 - with pumps on each branch and a water gun
This is a more complex option, which will be needed if necessary to power consumption points with different temperature conditions.
So, for example, in radiator heating, water heating ranges from 40 to 70 ° C, a range of 30–45 ° C is enough for a warm floor, hot water for domestic needs needs to be heated to 85 ° C.
In the harness, a hydroarrow will now play its special role - a segment is deaf from both ends of the pipe and two pairs of bends. The first pair is needed to connect the hydraulic gun to the boiler, distribution combs are joined to the second pair. This is a hydraulic barrier creating a zone of zero resistance.
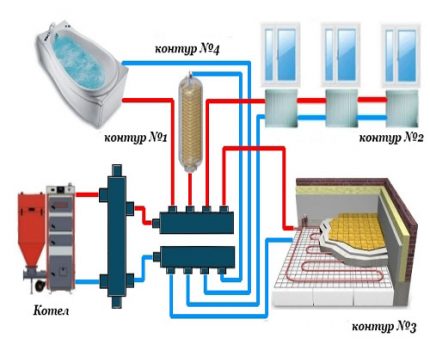
On the comb itself are mixing units equipped three way valves - adjusting temperature devices. Each pump outlet operates independently of the others its own pump, providing a specific circuit with the necessary amount of coolant.
The main thing is that in power these pumps do not exceed the total main boiler pump.
Both options considered are used in the installation of distribution manifolds for boiler rooms. Everything you need is sold in specialized stores. There you can buy any assembly or element-wise (based on the savings due to self-assembly).
To further reduce future costs, heating distribution comb can do it yourself.
The collector for the boiler room is in close proximity to the heating equipment and is exposed to high temperatures, which only metal can withstand.
Not so stringent requirements for thermal stability are imposed on the local distribution comb; not only metal pipes, but also polypropylene, metal-plastic pipes are suitable for its manufacture.
For a local distribution manifold, it is easiest to choose the right combs from those commercially available. In this case, the material from which they are made - brass, should be taken into accountsteel, cast iron,plastic.
More reliable cast scallops, eliminating the possibility of leakage. There is no problem connecting pipes to the combs - even the most inexpensive models are threaded.
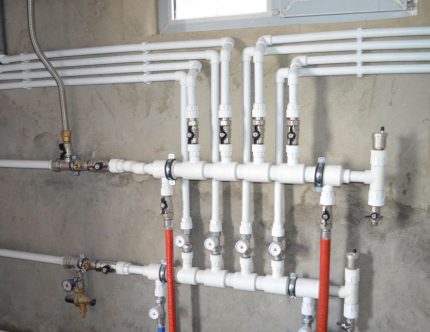
Craftsmen can solder a collector made of polypropylene or metal plastic, but you still have to buy threaded tips, so the product will not come out much cheaper for money than a finished one from the store.
Outwardly, it will be a set of tees, interconnected by tubes. The weak point of such a collector is insufficient strength at high temperatures of heating the coolant.
The comb can be round, and rectangular, and square in cross section. Here, the transverse area comes first, not the cross-sectional shape, although from the position of hydraulic patterns a round one is preferable. If the house has several floors, it is better to install local distribution manifolds on each of them.
What you need to know about the cons?
After the advantages of using distribution dies in heating systems have become clear, it makes sense to dwell on some of the minuses:
- High price. Collectors are made of durable high-quality metal, the cost of which is above average. High precision locking equipment is also expensive. The more circuits the comb serves, the higher the cost of equipping it.
- Volatility. Collector heating without a circulation pump does not work.Therefore, we must prepare for an additional payment of electricity.
- High flow rate. Pipe consumption in collector heating systems several times higher than in ordinary ones, since each device needs to be pulled a separate loop. All this complicates and increases the cost of installation.
The collector system, according to experts and those who already use it, is the most modern, reliable and efficient.
But at the same time, its arrangement and operation are expensive.
Conclusions and useful video on the topic
Installation of heating equipment with connection to a distribution comb:
Do-it-yourself comb making:
Compared to the traditional organization of the heating system, distribution combs increase its efficiency, and only the financial issue somewhat inhibits consumer interest in this method of heating. But if there is enough money, the use of distribution dies is your ideal choice.
Have you implemented a collector heating system in your home? Or just planning to equip it and you don’t understand something? Ask questions - we will try to answer them.
Or maybe you used a comb to connect a warm floor system? Share your personal experience in assembling and installing the system - leave your comments in the block below.
A fairly detailed description of all the processes required to install such a heating system. I, as a person who is knowledgeable in this, since I worked for several years in the company for installing heating appliances, I can say that even a novice person with this instruction will be able to install everything. Moreover, I even discovered some secrets for myself. Thank you so much)