Ventilation of industrial premises: rules for the organization of air exchange
The main work that the ventilation of industrial premises performs is the removal of used air and the injection of fresh air. With its help, in the shops and offices of the enterprise create a comfortable air environment that meets regulatory requirements.
It is difficult to overestimate the role of an effective ventilation system. Indeed, you must agree that only in conditions of clean air, normal temperature and humidity conditions can an increase in labor productivity be achieved.
To understand how to organize sufficient air exchange in a building, you need to understand the types and features of the operation of various ventilation systems.
We will tell you how natural and mechanical ventilation works, describe the methods for arranging local ventilation of the working area, and also explain the principles of calculating air exchange.
The content of the article:
Classification of ventilation systems
All existing ventilation systems group by 4 signs:
- By the method of moving air ventilation is called: natural, mechanical or artificial, combined when both options are present at the same time.
- In the direction of air flow ventilation systems are divided into supply, exhaust or supply and exhaust.
- At the scene ventilation systems are combined into 3 groups: general exchange, local, combined.
- By appointment emit a working and emergency systems.
The basis for the design of ventilation for workplaces in production are the norms prescribed in SNiP 41-01-2003. Natural and mechanical air exchange work according to different schemes.
While the processes that occur during natural ventilation depend on the heat and wind pressure and are practically not subject to man, forced air exchange is possible only with his active participation.
Scheme of action of natural air exchange
The ventilation of the premises, carried out in the first way, is nothing more than simple ventilation. It occurs without human intervention and is possible when the fences are not dense enough and allow air to enter the room both from the outside and from the inside.
The direction is influenced by pressure. If its indicators have a higher value from the outside, then the way opens for the penetration into the room of clean air from the street. Otherwise, warm air from the room finds a way out. Often these processes occur in parallel.
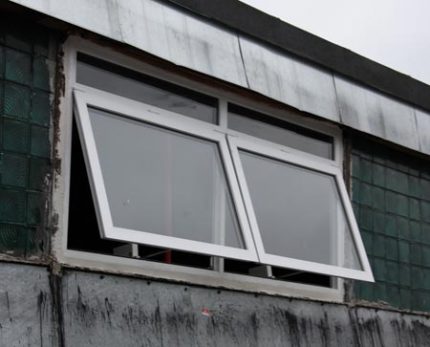
Active natural ventilation occurs unorganized due to accidental circumstances. It is observed in conditions when the air temperature outside and inside the building are very different.
Contributes to this process and the emergence of individual sections with high and low pressure indicators from the side of the body, intensively blown by the wind and from its more protected side, respectively. In this situation, infiltration is observed - air enters the room from the windward side, and goes outside with the leeward.
The air exchange coefficient characterizing the intensity of the process, with the natural method of ventilation does not exceed 0.5.
Unorganized ventilation can not provide comfortable conditions for people in the production room and working equipment. Specially designed systems must be present here.
Natural ventilation of an organized form is realized by aeration or using deflectors. Both the supply and removal of air from the room occurs either through openings in the building envelope, or through the air vents. In channel ventilation, a deflector is necessarily present.
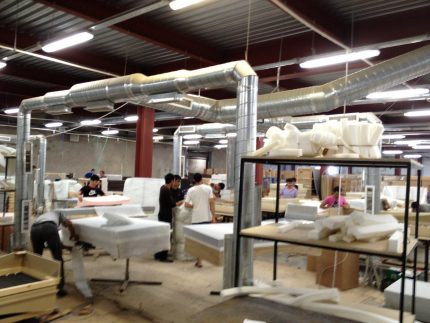
Natural ventilation using aeration
In workshops where the technology provides for the formation of heat in large quantities, aeration involves air exchange through light lamps and window openings under the influence of temperature and wind pressure. In cold shops, air assimilation occurs only under wind pressure.
When aeration is required, a compulsory accounting of wind rose is necessary, otherwise harmful emissions from pipes of neighboring enterprises may get into the production room. Nothing should interfere with the release of vapors or harmful gases through the light lamps.
The best conditions for ventilation are created by the location of the structure on the windward side with respect to harmful production. Opening and closing transoms must be automated so that they can be controlled from below.
Their different location allows you to adjust the supply of fresh air. Aeration is a more suitable option for large-scale workshops in which it is not possible to use mechanical ventilation due to its high cost.
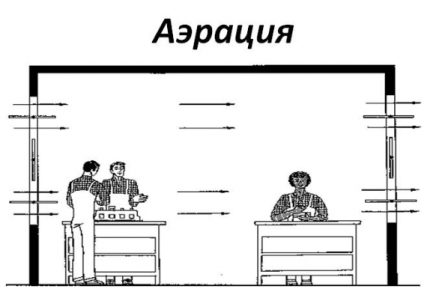
The recommended height of the air supply to the room with this type of ventilation is a minimum of 0.3 and a maximum of 1.8 m in the warm period and at least 4 m in the cold. The best option is the air vents of a special design on 3 levels. When warm, fresh air passes through transoms located below, and dirty air leaves through the top.
The middle row of vents provides air flow at subzero temperatures. While the air mass reaches the floor level, it manages to warm up.
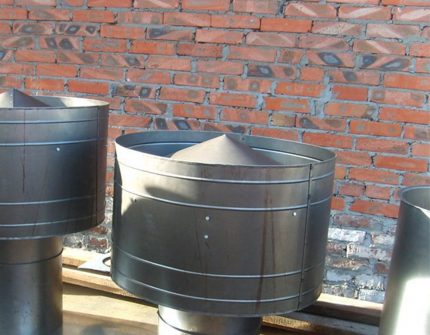
In industrial buildings of small volumes on channels or pipes intended for drawing, install baffles. With their help, exhaust air is removed from the workshops where there is a general exchange hood.
And also they are used for the removal of heated gases from furnaces, presses, and furnaces. When installed, they proceed from the trajectory of the prevailing air flow.
Artificial or mechanical ventilation
Being more perfect than natural, this type of ventilation requires significant financial and operational investments. In such a system, there may be devices not only purifying, but also ionizing, moisturizing, warming the air.
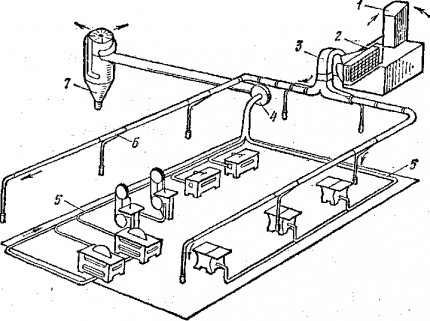
Mechanical ventilation can be either supply or exhaust or combined, that is, supply and exhaust.
Its advantages are obvious:
- clean air intake and its processing - heating, drying, moisturizing;
- air mass movement over significant distances;
- clean air delivery directly to the workplace;
- dirty air removal and its cleaning;
- work independence - the effectiveness of the system does not depend on environmental conditions.
Basically, exhaust and intake systems work together, but sometimes they recommend using only one of these two types.
Task supply ventilation - ensure the supply of a working room with air that has a beneficial effect on human health.
It is used where production processes are accompanied by large heat releases containing a small amount of harmful substances. Clean air entering the air ducts is distributed to the workplace through the use of distribution nozzles.
Systems that remove air from a room containing various pollutants are called exhaust systems.This type of air exchange is used in industrial premises where there are no harmful emissions and the minimum value of such a parameter as the rate of air exchange is not ruled out.
It can be warehouse, auxiliary, household premises. Air supply is provided by infiltration. The task of effectively removing contaminated air and cleaning it well suction systems.
In case of need for active and reliable air exchange supply and exhaust ventilation. In order to somehow protect the slightly contaminated premises from the adjacent workshops with a high level of pollution in the system, a little pressure is created.
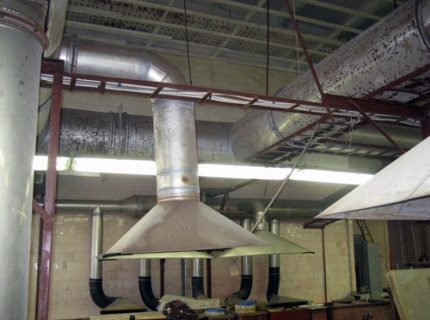
At the stage of design work to create a supply and exhaust ventilation system, the air flow rate is calculated, for which the formula is used:
Lots = 3600FWwhere
F - total area of openings in m²,Wo - the average value of the speed at which air is drawn in. This parameter depends on the toxicity of the emissions and the type of operations performed.
The exhaust hoods may be at different heights. The main thing is that polluted air currents do not change their natural trajectory. Emissions with a specific gravity higher than that of air are always in the lower zone, therefore, devices for their intake must be placed there.
In the autumn-winter period, the air supplied to the room must be heated. To reduce costs use recirculationproviding for the heating of part of the purified air and returning it to the room.
For PVU work with recovery 2 rules must be observed:
- At least 10% of fresh air is supplied from the outside, and the content of contaminated impurities in the return air does not exceed 30% with respect to the maximum permissible capacity.
- It is forbidden to use recirculation in production where explosive dust is present in the air mass, microorganisms that can cause various diseases, emissions related to hazard classes 1-3.
The choice of type of ventilation at the scene depends on the weight of the emissions, their concentration, temperature. Generalized ventilation allows you to divert the entire volume of dirty air, regardless of where it comes from.
The most widely used channel option. Here, for the advancement of air through special air ducts, an ejector installation or use a fan - axial or centrifugal type.
If there are no air ducts, then the system is called channelless. Ventilation equipment in this case is mounted directly in the wall or in the ceiling. The main condition is the presence of natural ventilation.
The possibility of the appearance of emissions with a high degree of explosion hazard in the room does not allow the installation of ventilation equipment on the air ducts, therefore, in these cases, ejectors are used.
The supply general ventilation artificial ventilation system is often connected to central heating. Outside the building, air inlets are organized for fresh air.
The mines are located above the roof and above the ground. The main thing is that there should not be any industries with harmful emissions near the receivers.
The air sampling openings themselves should be at least 2 m from the ground, and if the production is located in the green zone, the minimum allowable distance from the ground level to the bottom of the opening should be 1 m.
The principle of operation of general exchange ventilation is simple:
- the fan draws in air masses through the air heater;
- the air is heated and moistened;
- air flows into the building through special ventilation ducts.
The volume of incoming air is coordinated by valves or dampers designed for this purpose.
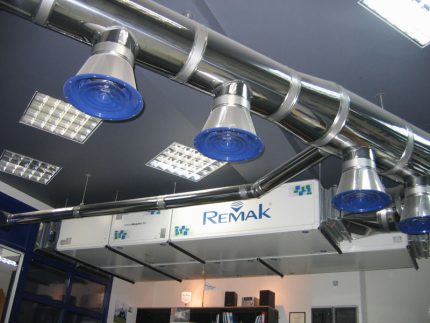
General exchange artificial ventilation of supply and exhaust type is open and closed. In the first case, these are 2 independent systems, one of which pumps air, and the second - in parallel, removes the previously neutralized waste.
These systems are suitable for workshops where substances of 1-2 hazard classes are released, and the production itself belongs to categories A, B, C.
In addition to working ventilation in potentially hazardous production facilities, an emergency version must also be present. They make it mainly exhaust. For rooms belonging to categories A, B, E, the system is equipped with a mechanical drive.
All elements of the system must comply with the requirements of the EMP. In workshops of category B, D, D, the presence of a natural ventilation motive is permissible if the performance is provided under the most adverse weather conditions.
The grilles and pipes of the emergency ventilation system are located in places of the highest concentration of hazardous substances.
There is no need to install umbrellas on pipes and shafts of emergency ventilation. The holes themselves should not be placed where people are constantly located. This will worsen the local microclimate.
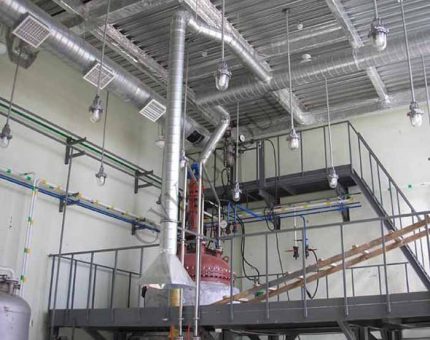
Supply emergency ventilation is installed in workshops, where in case of emergency, there will be an emission of vapors or gases that are lighter than air. Switching to emergency ventilation should occur automatically as soon as the normal system fails.
Local ventilation
Local exhaust eliminates the exhaust air in places where it is polluted. The set of production hoods includes exhaust fans, pipelines, ventilation grilles.
Local ventilation, designed to remove substances belonging to hazard classes 1 and 2 from the equipment, is arranged so that when the ventilation system is turned off, equipment start-up becomes impossible.
In some cases, provide for redundant fans and supply local suction with automation. Such ventilation is divided into 2 types - supply and exhaust. The supply type of ventilation is performed in the form of thermal curtains, air showers.
Thermal curtains from the air
Apertures that remain open for a long time (more than 40 m per shift) or open quite often (more than 5 times) contribute to the hypothermia of people in the room. The operation of drying plants emitting pollution leads to negative consequences.
In these cases, air curtains are arranged. They act as a barrier to cold or very superheated air.
Air and air-thermal screens are designed so that in cold weather when opening the openings, the temperature in the shops does not fall below the mark:
- 14 ° C - during the execution of work that does not require great physical effort;
- 12 ° C - when the work is classified as moderate;
- 8 ° C - when doing hard work.
If workplaces are located near gates and technological openings, screens or partitions are installed. The air-thermal curtain near the doors facing the outside should consist of air with a maximum temperature of 50 ° C, and at the gate - no more than 70 ° C.
Local exhaust using special suction
The local exhaust system using special suction first captures and then removes harmful impurities in the form of gases, smoke and dust.
This is a kind of air shower, the task of which is to inject fresh air at a fixed place and lower the temperature in the inflow zone. It is used in production, where workers are exposed to high temperatures and radiant energy with an intensity of more than 300 kcal / m² per hour, radiated by heating and melting furnaces.
There are such installations, both stationary and mobile. They must provide a blow rate of 1 to 3.5 m / s.
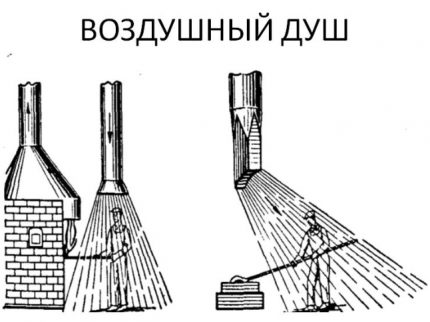
There is such a thing as an air oasis, which is the same device included in the local ventilation system. It creates a microclimate with predetermined parameters in a certain part of the production room.
Purified air supplied to a given alienated zone is usually subjected to special heat and humidity treatment.
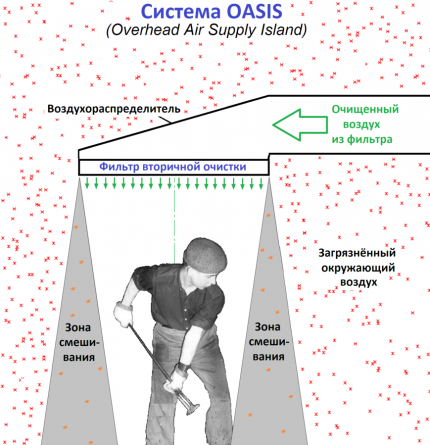
If the local suction device is approached directly to the place of release of substances polluting the space, it will be possible to remove air containing a higher percentage of them than with general exchange type ventilation. Local ventilation can significantly reduce air exchange.
Air exchange calculation
If harmful substances are not emitted as a result of production activities, the amount of air required for ventilation is calculated by the formula:
L = N x Lnwhere
N - this is the number of people who are usually indoors, Lн - the volume of air required for 1 person, measured in mᶾ / h. Normally, it is from 20 to 60 mᶾ / h.
Using a parameter such as air exchange rate, the calculation is performed according to the formula:
L = n x S x Hwhere
n - the rate of air exchange in the room (for the production room n = 2),S - area of the premises in m², and H - its height in m.
Conclusions and useful video on the topic
Here is all about the intricacies of all kinds of ventilation systems:
System Installation Details:
Whatever ventilation system is chosen, it must have two main properties: competent design and functionality. Only when these conditions are met at the factory will an optimum microclimate be maintained for health.
Have something to supplement, or have questions about the organization of ventilation of industrial buildings? Please leave comments on the publication. The contact form is located in the lower block.
Regarding emergency ventilation installed in class B, G, D rooms. As the author advises, the presence of ventilation of natural motivation is permissible. However, in this case, the main problem of emergency ventilation will be the constant pollution of blowers, grilles, as well as some electrical elements of the ventilation circuit.At the same time, the infa presented here indicates the need to comply (PUE) with the “Rules for the Operation of Electrical Installations”, which directly prohibit the risks of any ingress of water and precipitation onto the wiring. So, we must mention the additional insulation of electrical circuits in this case.
Any ventilation is polluted, Vasily. There is a maintenance schedule for cleaning. Classes of electrical wiring, electric drive are laid during the design. If necessary, designers lay pipe sealed wiring, similar to an electric drive. The author listed all the factors, recalled the PUE, did not miss anything. Re-read the text in the screenshot (attached to the comment).
It is often observed that exhaust ventilation of industrial premises is inefficient. Many errors and miscalculations are made even at the installation stage: dust collectors, for example, are not installed where needed, the diameter of the pipes and the total channel length of the ventilation pipes are not calculated correctly. Traction is insufficient where necessary, and redundant where not necessary.
Installation of ventilation, Nikolai, is carried out according to the project. The customer is required to control the work of the contractor. If his engineering services are not qualified, experts are invited. The total length of ventilation ducts is determined by the project, and not calculated. After completion of installation work, testing is carried out - design flaws are eliminated by the designers, and then adjusters make adjustments.