DIY installation of polypropylene pipes: technology for working with PP piping
Decided to make major repairs in the apartment? Then it is worth considering that without replacing the water supply, it will be inferior. Agree, it will be a shame if one of the pipes starts to leak immediately after the repair, and, well, flood the neighbors. An excellent alternative to outdated water utilities are plastic pipes.
To make a plastic wiring of the heating system or water supply in the apartment is quite simple. To carry out the installation of polypropylene pipes with your own hands, you only need a set of special equipment and a minimum of technical skills.
Next, we will tell you what tools are needed to work, and how to use them correctly. In addition, in the article you will find information on how to properly draw up a wiring diagram for a plastic pipeline, as well as step-by-step instructions for welding polypropylene pipes. To help the home craftsman, we have selected thematic videos.
The content of the article:
Anatomy of Polypropylene Tubes
Most polypropylene (PP) pipes are the same only at first glance. A more detailed consideration of them will allow you to notice the differences in the density of the material, internal structure and wall thickness. The scope of the pipes and the features of their installation depend on these factors.
PP material classification
The quality of the welded polypropylene seam and the operational characteristics of the pipes are largely determined by the manufacturing technology of the PP.
There are such varieties of parts, based on the material of their manufacture:
- PRN. Single-layer products made of homopolypropylene. They are used in industrial pipelines and cold water supply systems.
- RRV. Single-layer products from block copolymer PP.They are used for installation of floor heating networks and cold pipelines.
- Ppr. Single-layer products made from random copolymer PP. They are used in water supply and home heating systems with water temperatures up to + 70 ° С.
- PPS. Poorly flammable type of pipe with a working temperature of up to +95 ° C.
There are also multilayer reinforced parts made of PP.
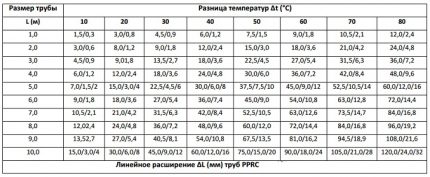
They have an additional internal aluminum shell, which dramatically reduces thermal elongations, facilitating wiring and safe operation.
The disadvantage of these products is the need before soldering the removal of the upper polymer layer and aluminum to the depth of penetration of the pipe into the fitting.
In more detail, the types of PP pipes by material of manufacture and fittings we examined in our other article.
What does the marking look like?
You can choose the required pipes and fittings for plastic wiring in the building market yourself. You only need to know the legend of the marking.
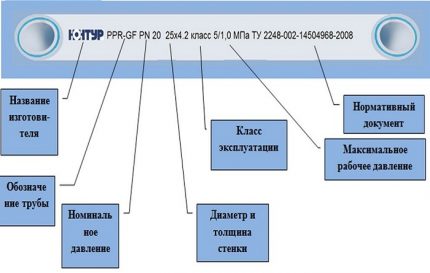
To determine the scope of polypropylene products, the main indicator is PN. This is an indicator of the nominal pressure in kgf / cm2 (1 kgf / cm2 = 0.967 atmospheres), at which the service life does not change. The base temperature of the coolant in the calculation is taken equal to 20 ° C.
In the domestic sphere, 4 main types of PP pipes with various PN indicators are used:
- PN10 - for cold water supply;
- PN16 - for cold and for warm water supply;
- PN20 - for hot water and heating systems;
- PN25 - for heating systems, especially the central type.
Products with PN25 often have a large linear length, therefore they are almost always reinforced with aluminum foil or durable fiberglass for less expansion when heated. We recommend that you deal with labeling of PP pipes for heating.
Appearance and internal structure
High-quality PP pipes have a perfectly round shape at the cut. The thickness of the walls and the reinforcing material should be the same over the entire circumference, there should be no ruptures of aluminum or fiberglass.
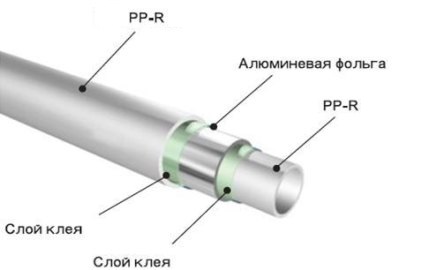
Reinforced pipe traditionally consists of three layers: inner and outer polypropylene and medium aluminum or fiberglass. The surface of the pipes should be smooth, without sagging and recesses.
The color of the material can be green, white or gray, but the quality and characteristics of the pipes are completely independent of this.
Advantages and disadvantages of PP
The advantages of PP pipes during the installation of internal heating and water supply are obvious and are confirmed by their undivided dominance in this area.
The properties that make this product a priority for the assembly of house communications are:
- noiselessness;
- impact strength;
- ease;
- resistance to corrosion;
- durability;
- tightness of connections;
- cheapness;
- immunity of internal walls to raids.
But polypropylene pipes have negative aspects that cause inconvenience during installation:
- lack of flexibility;
- strong elongation when heated;
- the need for special tools when connecting individual products.
Specialists who daily assemble PP pipes have long developed ways to compensate for these shortcomings, so there are no special alternatives to polypropylene.
Preparation for installation of PP pipes
It is impossible to make water piping with one hands and pipes, so you should understand the heating and water supply schemes, the necessary tools, connection methods and the materials used.
Assembling a water supply system from PP pipes involves a number of traditional steps:
Stage # 1. Project drafting
Before purchasing material for the installation of heating and water supply, it is necessary to determine their wiring diagram.
There are four main ways to connect batteries to the heating circuit:
- flowing;
- with unregulated bypass;
- with valves;
- with a three-way valve.
The final choice of installation option is usually determined by the financial capabilities of the owners of the apartment, because stop valves are expensive.
Features of the installation of heating from polypropylene we examined in detail in this article.
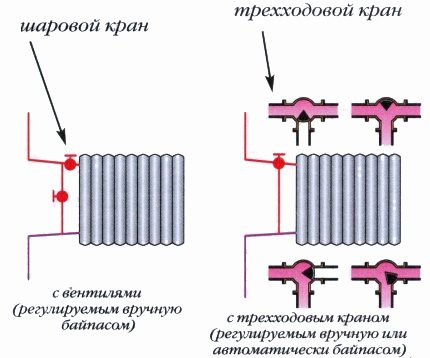
The water supply also has the basic schematic diagrams of wiring design, but there are only two of them: collector and tee (traditional in apartments).
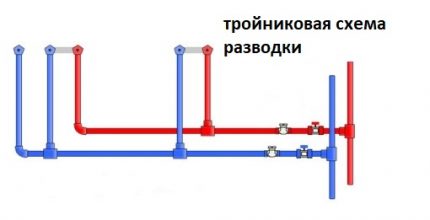
The tee pattern is also called sequential. It involves holding along all plumbing fixtures a single pipe, from which bends are successively made using a tee.
The collector circuit involves the installation of a collector in the form of a flute at the water inlet to the house. It allows you to compactly make several bends in different directions.
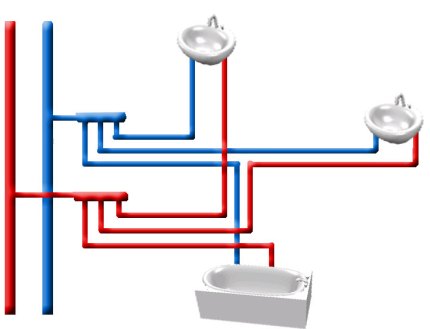
The wiring can be done inside the walls or in the open. The first option requires detailed calculations, taking into account the elongation of the pipes during heating.
We recommend that you familiarize yourself with water distribution schemes from PP pipes.
Stage # 2. Tool preparation
A significant disadvantage of independent work with polypropylene pipes is the need to use a special tool. The price of an installation kit of equipment is from 100 to 200 dollars.
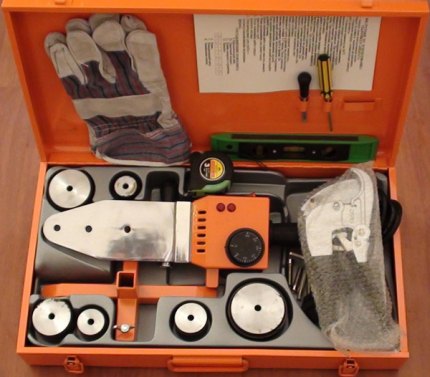
Such a set should include:
- electric welding machine with a stand or simply soldering iron for PP pipes;
- pipe shears;
- a shaver for removing the outer layer and aluminum from reinforced pipes;
- calibrator and chamfer to control and regulate the diameter of the parts;
- nozzles for heating soldered elements.
In addition to special equipment, for the installation of PP pipes, you will need an adjustable wrench, marker, tape measure and other general business tools.
If one-time installation works are planned, then you can rent a soldering set.
Stage # 3. Selection of polypropylene fittings
For welding PP pipes among themselves in various combinations, as well as for connecting them to plumbing fixtures, PP fittings are used.
They include;
- adapters;
- nipple bends;
- couplings;
- threaded couplings;
- tees;
- stubs;
- crosses;
- detachable connectors;
- Ball Valves;
- clamps.
A few tips for choosing fittings and installing pipes:
The quality of polypropylene and the wall thickness of the fittings can also vary, so you need to choose them according to the marking of the pipes.
Stage # 4. Connection scheme selection
There is a fundamental difference in soldering pipes with a diameter of up to 63 mm and from 63 mm. Pipes that are equal to or larger than this size are welded end-to-end, and which are smaller are joined by a bell-shaped method.
The latter involves the formation of a joint due to the fact that the molten cut-off end of the pipe enters a few centimeters into the extended socket of the fitting.
In the same way, the connections of two pipes to each other by means of a coupling are also performed.
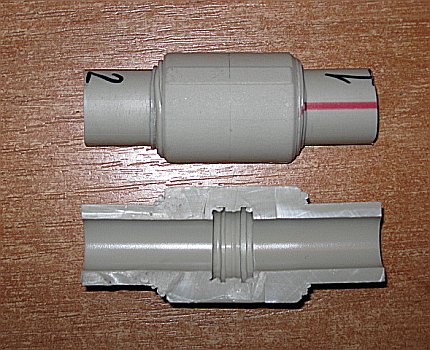
Depending on the presence of threaded parts, the connections of PP products can be:
- detachable;
- one-piece.
Detachable connections involve soldering to the ends of the connecting parts of two threaded fittings with external and internal threads.
The one-piece type is the above-described bell-shaped method of joining by soldering two polypropylene products.
To learn more about the technology of welding pipes made of polypropylene, go to this link.
Step-by-step instructions for welding PP pipes
After purchasing all the necessary pipes and fittings, you can begin to weld them. This process will be examined step by step, with illustrations, so that no questions remain.
Step # 1 - pipe trimming
This process is done using pipe cutter. If the cut is chamfered, the longer edge can form an influx when soldering and narrow the inner passage of the fitting.
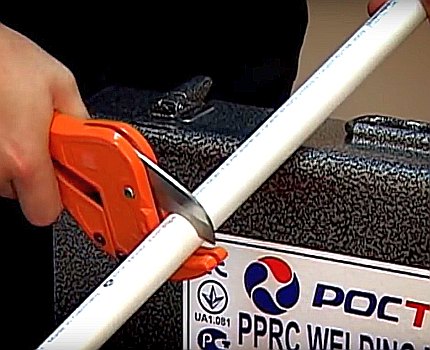
Pipe cutters have a maximum diameter limit, so you need to choose the model that suits the purchased pipes.
Step # 2 - pipe processing and chamfering
After trimming, it is necessary to form a small chamfer on the part, which will be inserted into the socket. To do this, hand calibrators of various sizes or attachments for a screwdriver are used.
Both tools have built-in knives that form a chamfer with standard parameters.
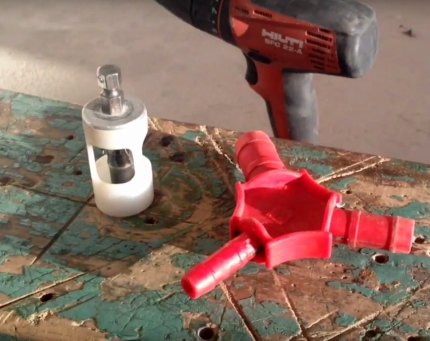
To get a cut, you need to put the pipe on the manual calibrator and scroll it around the axis several times with pressure.
On reinforced pipes, in addition to the chamfer, the top layer of PP and aluminum foil is removed using a shaver. It has the appearance of a cylinder with handles and is suitable only for one specific size.
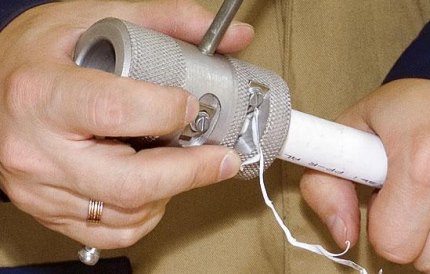
After forming the chamfer and removing the aluminum foil, you need to wipe all the parts clean.
Step # 3 - preparing a soldering iron
The soldering temperature of polypropylene pipes varies from 260 to 280 ° C, but for lovers it is better to use unregulated soldering irons or heating to 260 ° C. We recommend a closer look at the values soldering temperatures of polypropylene.
Before switching on, it is necessary to put double-sided nozzles (mandrel and sleeve) on the soldering iron and place the device on a cross-shaped stand.
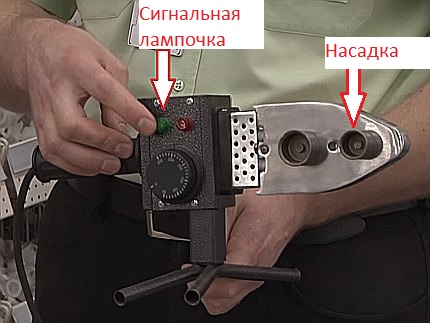
Then turn on the soldering iron. When the temperature reaches 260 ° C, the green indicator light will light up.
Step # 4 - heating and joining parts
It is recommended to work with pipes with gloves. To heat the parts, it is necessary to simultaneously attach one connected part to the mandrel, and put the second into the sleeve.
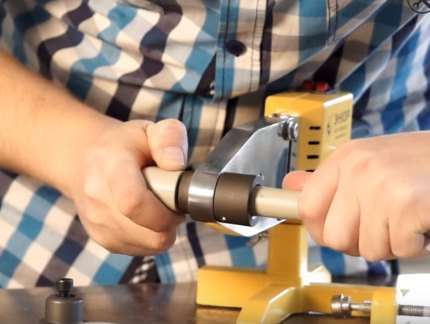
To comply with the depth of the connection, you can make a marker in advance on the pipe with a marker and focus on it when sticking the product into the socket.
The table below shows the standard time for heating, connecting and cooling pipes, depending on their diameter, as well as the depth of insertion into the socket. When working in a cold room, the heating time can be increased by 1-2 seconds.
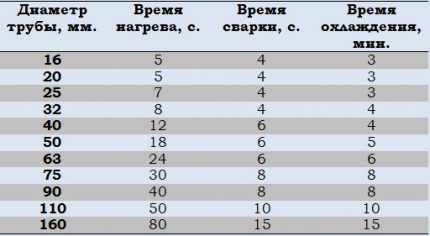
After heating, the parts to be joined with the force by direct movement must be joined to the intended line. It is important to prevent rotation of parts.
Shifts of the pipe and fitting relative to each other are allowed only for 4-12 seconds. After that, any progress will have a very negative effect on the quality of the connection.
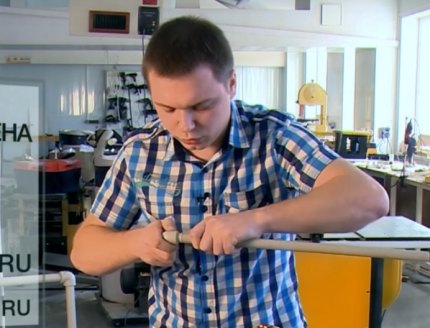
After joining, it is necessary to allow the polypropylene to cool for the time indicated in the table. It is advisable to look at the resulting inner seam to make sure that the influx does not block the passage. Otherwise, you will have to solder the parts. This ends the soldering process.
To avoid popular mistakes during plastic welding, we recommend that you familiarize yourself with soldering rules and errors.
How to fix the pipeline?
A good wiring of heating or water supply is not only the quality of the connection, but also the realization of knowledge on how to assemble the assembled polypropylene pipes.
Proper fixing of the plastic wiring to the walls will prevent it from sagging and warping when heated with hot water.
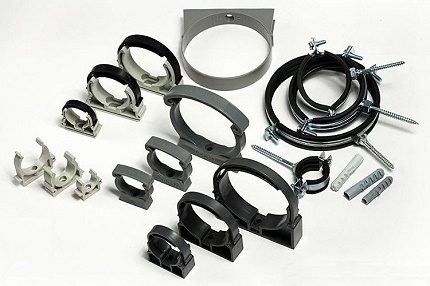
For fixing pipes used: clips (single, typesetting, with clamp) and clamps (studs, paired, wall).
New models are constantly appearing on the market, therefore clamp selection and clips are best made directly in the store.The clips basically provide free movement of the pipes along the axis, and the clamps firmly fix them in one position.
A particularly dangerous consequence of improper installation is neglect of the thermal stretching of the pipes.
The length of simple PP pipes can change when heated by 10-15mm / 1m. When they are rigidly fixed, deformation occurs in the areas of adhesions, which can lead to rupture of the connection. To relieve tension, these types of compensators are used:
- Z-shaped;
- U-shaped;
- L-shaped
- ring.
Rules for working with the compensator:
After soldering the expansion joints and attaching the pipes to the clamps and clips, you can begin testing the assembled system.
Conclusions and useful video on the topic
The algorithm for soldering polypropylene pipes is best remembered after watching the corresponding videos. The types of fittings and the features of their welding will also be shown.
Types of soldering irons and instructions for soldering polypropylene pipes:
Secrets of installing PP pipes:
Types of fittings and the rules for their soldering:
The above-described technologies for installing polypropylene pipes and fittings are simple and do not require professional skills. Video materials clearly demonstrate the stages of the soldering process, which can be mastered independently in a few minutes.
Therefore, to assemble water piping with your own hands, it is enough to purchase the necessary materials, find equipment and follow the action algorithms described in the article.
Do you want to assemble a plastic pipeline, but haven’t fully figured out the nuances? Ask for advice - we will try to answer you as detailed as possible.
Or maybe you are a specialist in soldering PP pipes and want to share valuable tips with beginners? Write your recommendations in the comments section - many home craftsmen who first encountered soldering polypropylene will be grateful to you.
Before proceeding with the installation of a water supply system in a country house (cottage), I trained in the use of a soldering iron for plastic pipes. It was necessary to build a trellis for cucumbers, tomatoes and clematis. It seems that everything turned out exactly. After that, he began to conduct water in the house. The task was not difficult, since only cold water was planned to be supplied to the house. It was not necessary to bring hot, heating. Decided not to put a bath and toilet. Therefore, my first experience was quite successful.
In my opinion, polypropylene pipes marking pipies are the most reliable. I installed cold and hot water, normally withstands temperature extremes.By the way, does anyone know the shelf life of the pipes before the operational period ?! I have laid pipes with a production date of 1999, I think that for their intended purpose they can no longer be used and it is better to take them to the country.
Explained very accessible and clear. Thank!