Plumbing pipe connection methods: an overview of all possible options
In order for the water supply systems and the circuits along which the coolant circulates to perfectly perform their own duties, their components must be correctly assembled and correctly connected. The result of the efforts of plumbers should be tight so as not to create problems for the owners and their neighbors. Do you agree?
All relevant pipe connection methods that ensure the normal operation of the system are given in our article. We have described in detail the technological options depending on the material from which the articulated parts are made and on the category of the pipeline. Our tips will help you achieve the perfect result.
The content of the article:
Overview of plumbing fittings
All known methods of connecting pipes can be attributed to two classes - detachable and one-piece. In turn, detachable connections are flange and coupling. One-piece methods include compounds such as socket, collet, butt welding, glue.
Connections, which, if necessary, can be disassembled and then returned to their place, greatly simplify maintenance and repair of pipelines. These compounds are used mainly in the formation of internal communications.
The advantage of the method is its simplicity in execution. No chemical or thermal effects are used here. A malfunction of the pipeline connected by this method is easy to identify and eliminate.
A tight fit during the plumbing connection of pipes is ensured by the use of special parts. There are 2 types of joints related to the detachable type: flange and fitting. The first is used when it is necessary to joint large-diameter pipes, and the second are more suitable for home pipelines.
Introduces varieties, characteristics and marking of polypropylene pipes and fittings used in the connection next articlewhich we recommend reading.
Fittings used in plumbing systems are installed at control points, on bends, branches. They are cast and compression. In terms of functionality, the following types of fittings can be distinguished:
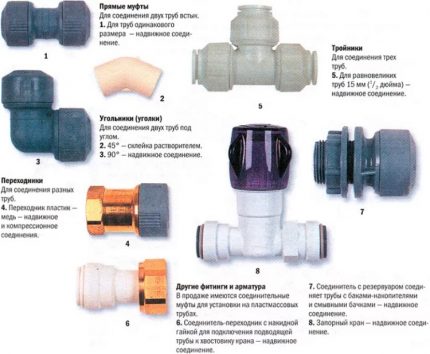
A set of fittings is selected depending on the specifics of a particular pipeline. According to the method of attaching them to the pipe, fittings are clamped, threaded, press, threaded, used for welding and soldering.
Let out fittings for plastic pipes, they are used in the formation of crimp and press joints. Fittings are used for joining polypropylene pipes, which are used both in gluing and welding. For copper pipes make fittings for both press joints and soldering.
The process of assembling a metal-plastic pipeline using compression fittings will present the following selection of photos:
Bell-shaped method of connection
A socket is a mounting extension designed to create a reliable connection. The principle is based on the fact that the end of a pipe having a smaller cross section is inserted into a pipe of a larger diameter. Seal the connection by using a sealant placed in the socket or by gluing with a composition resistant to water.
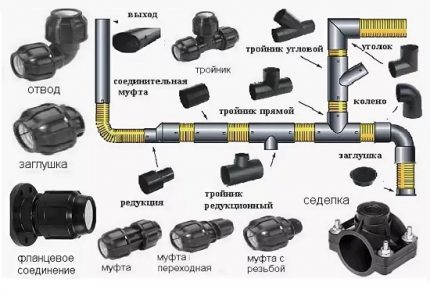
Depending on the pipe material and their diameter, one of several existing options for a bell joint is chosen: with a sealing ring, without a ring, welding, gluing.
O-ring joint
Without a sealing ring, cast iron pipes are most often connected. The inserted pipe is shortened, the end face is processed so that there are no nicks and mother-in-law in it. In the socket insert the tail of the articulated pipe.
The resulting gap is filled with a rope of oiled hemp or flax tarred strands.First, the sealant is laid in a ring and choked in the socket, tapping with a hammer on a special wooden spatula or screwdriver. It is important to ensure that the ends of the material do not fall into the pipeline.
Continue layer-by-layer laying of the seal until the socket is filled to 2/3 of its depth. For the last layer, an untreated sealant is used, because oil or resin will deteriorate adhesion when filling the remaining space in the socket with cement.
To obtain a solution, cement of grades 300 - 400 and water for its dilution are needed. The components are taken in a ratio of 9: 1. Cement is tamped in a bell and covered with a wet rag for better setting.
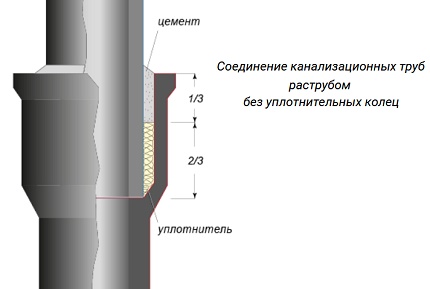
Sometimes, instead of cement, an asbestos-cement mixture made from M400 cement and high-quality asbestos fiber in a ratio of 2: 1 is used.
Water is added immediately before installation in an amount of about 11% by weight of the dry mixture. Instead of cement-based sealants, bituminous, silicone sealants, clay are used, the last layer of which is strengthened by applying bitumen or oil paint.
Bell joint with O-ring
This method is most often used when building an intra-house sewer system. A rubber ring sandwiched between the bell and the pipe inserted into it gives a tight connection. Therefore, the method is not only simple, but also reliable.
The sealing ring to some extent smoothes out the differences between the axles between the two pipes to be connected. However, this is only if the axes on each meter of the composite pipeline are offset by an amount that does not go beyond the pipe wall thickness.
If this condition is violated, then the likelihood of leakage as a result of uneven deformation of the seal increases.
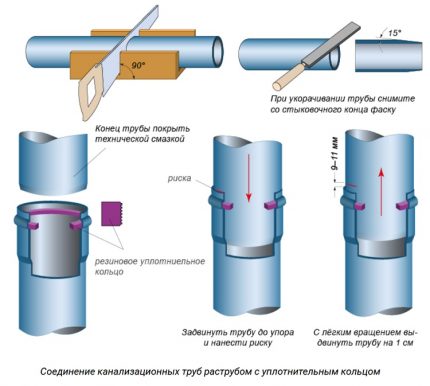
To determine the pressing depth of the free pipe end into the socket, the sealing ring is temporarily removed. Then, placing the pipe in the socket to the stop, mark the place where the inserted part is in contact with the socket.
During installation, the pipe is slightly extended relative to the mark - by 0.9 - 1.1 cm. This distance will make it possible to balance the internal stresses that appear in the system during temperature fluctuations.
Before placing the ring, it is recommended to dip it in soapy water and squeeze a little. This will greatly simplify its insertion into the socket recess. In order to minimize distortion, some manufacturers began to produce fittings with an angle of 87 ° instead of 90 °. The pipe enters the socket at a slope and the ring does not warp.
If there is a need to connect pipes made of materials of various kinds, transition pipes are used. A nozzle size such as the inner diameter should correspond to the outer section of the connected pipe. In the case of articulation of the socket of the polymer pipe with a pipe made of cast iron, a double sealant is applied to the end of the second and the pipe is mounted.
Bonding plastic pipe parts
By gluing, they connect the PVC pipe to the bell. For better adhesion, the socket inside and the tail of the inserted pipe are treated with emery so that the surface becomes rough.Then the chamfer is removed, the treated parts are degreased using methylene chloride as a primer.
Before making the connection, check the pipes for compatibility. A pipe of a smaller diameter should enter the socket freely, but not too much. Then the line marks the border for applying glue - this will help to join the parts without errors.
On the surface of the elements to be connected - 2 thirds of the socket recess, as well as the fully calibrated pipe end, evenly apply glue thin layer. The pipe is inserted into the socket and rotated a quarter of a turn to improve contact between the connected elements. The joined parts are held until the glue sets.
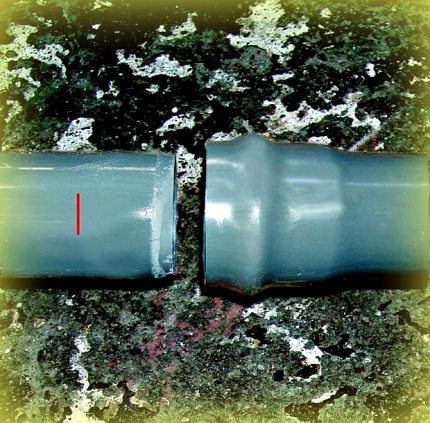
The process takes only 20-30 seconds. If a uniform layer of glue appears at the junction, it is immediately removed with a piece of clean cloth. From bonding to complete stabilization of the joint and testing the pipeline for leaks, at least a day must pass.
To repair existing pipelines, fittings are used in the form of repair couplings or products with an elongated socket. The pipe section is cut out, the chamfers are removed at the ends, and special glue is applied to the ends. The sleeve is put on the bottom of the pipeline.
A sleeve with a long socket is put on the top of the pipeline until it stops, if necessary, a shaped part is mounted on it. The coupling is moved together with the shaped part down until it contacts the lower part of the pipeline. The sliding sleeve is moved upward so that it covers the joint area.
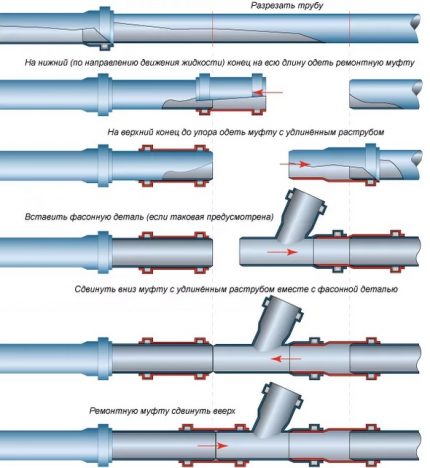
If even after this there is a leak, the joint is filled with silicone sealant. The bottom and top are determined depending on the direction of movement of the transported substance.
Using resistance welding
To apply this method of connecting pipes, you must have a welding machine. It can be mechanical or manual, but always equipped with a special tool that heats the elements to the required temperature.
When using bell-shaped technology in the connection of pipes, a xiphoid-shaped device is used. It is a set made of metal and consisting of a sleeve designed to heat the outer surface of the pipe and the mandrel (pin), fusing the part from the inside.
An important point is the selection of the kit. Its parameters should correspond to the diameter of the assembly.
The technology of bell-shaped pipe joints using resistance welding is simple:
- A restrictive clamp is put on the inserted pipe. The distance between the edge of the pipe and the clamp should equal the depth of the socket plus another 2 mm. The difference between the diameter of the clamp inside and the outer diameter of the jointed pipe should be 0.2 mm.
- The kit is heated, pre-installed on the device.
- Put the bell on the mandrel, and the smooth tail of the pipe on the sleeve until it stops.
- Perform heating for the set time.
- Remove the parts from the kit at the same time and connect them, keeping the parts from displacement until the melted material hardens.
Welds are inspected to identify possible distortions, voids, uneven seams.
On the outer surface of the parts there should be no defects that appear in case of exceeding the permissible temperature. Visually, the outside of the weld should be in the form of a symmetrical roller having the same width and distributed evenly around the perimeter of the pipe.
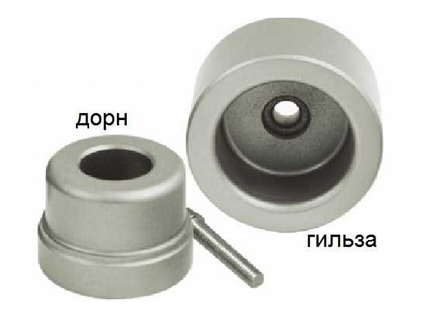
The maximum height of the roller on a pipe with a wall thickness of up to 1 cm is a maximum of 2.5 mm. For pipes in which this size exceeds 1 cm, a roller height of 3-4 mm is considered acceptable. The edges of the welded joint can be offset relative to each other by no more than 10% of the pipe wall thickness.
PP pipe welding technology in detail given here. We recommend that you familiarize yourself with the content of our article.
It is recommended to weld pipes of polymer pipes with a diameter of more than 50 mm and a wall thickness of more than 4 mm on a stationary or mobile device with a disk heating element:
Clamp fitting
The concept of a collet connection of pipes means the use of a clamping or collet fitting. With its help, it becomes possible to implement a variant of a collapsible joint of pipeline elements made of unequal materials. Features of its implementation described here. The clamping fitting is selected based on the type and diameter of the pipe.
The docking algorithm for plastic pipes is as follows:
- The hole of the desired pipe segment is calibrated using a calibrator and the inner chamfer is removed using the chamfer.
- Disassemble the fitting by twisting the nuts from the ends and removing the round seals from the fittings.
- Put the union nut on the end of the pipe, then the fitting collet.
- Insert the fitting shank into the pipe, applying a force so that it fully engages.
- Manually tighten the nut on the fitting body.
- Repeat the same manipulations with the second pipe, then join the connected parts and tighten the union nut without twisting 1-2 turns.
Tighten the nut carefully so as not to damage the pipe. In the process, the clamping ring is deformed, due to which the end of the pipe and the side of the fitting cartridge are tightly pressed against each other.
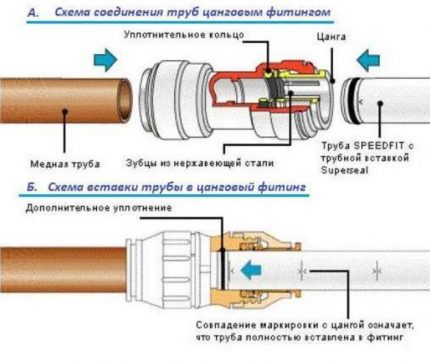
Experienced plumbers recommend that when tightening the tightening nut, the first turns are performed manually, and then use a ring wrench.
Collet connections are mainly used in the assembly of copper pipelines:
Threaded Formation
A thread is called a spiral or helical surface by which a threaded connection is made. The use of threaded pipe joints in plumbing systems is a classic installation method.
It is used where it is possible to periodically monitor the joints, because thread tends to weaken under the influence of various factors.
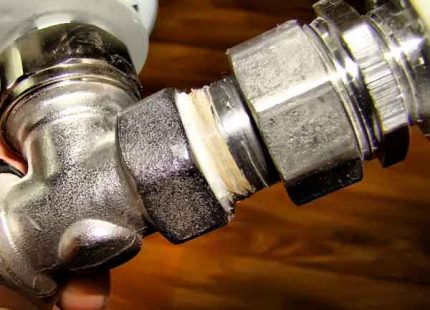
There are different types of pipe threads. Each of them is characterized by such parameters as the surface profile on which the thread is applied, the direction, location, number of thread starts.
The list of the most popular types of pipe threads includes:
- cylindrical or whitward;
- conical;
- round;
- Npsm
The first of them is denoted by the letter G, has 2 accuracy classes. The profile visually resembles an isosceles triangle. At the top - an angle equal to 55⁰. Pieces of pipeline with a diameter of up to 6 inches are connected with inch threads, to which special tightness requirements are imposed. With a larger diameter value, welding is used.
An inch-type conical thread is used for conical joints and for creating joints of a conical thread made on the outside and cylindrical inside the pipe. The letter R marks the external thread, internal - Rc, LH - directed to the left. The thread plus sealant acts as a sealant.
To connect often dismantled plumbing fixtures: water shut-off valves, faucets, mainly use round thread. Designate it with the symbols of Kr.
The table summarizes the main parameters of the thread for the pipe, which can be do it yourself. An important value for an inch thread is its pitch. This is the distance between adjacent ridges or troughs. Its value along the entire length remains unchanged, otherwise the thread will be inoperative
The NPSM thread profile has the appearance of a triangle and an angle of 60 °. The size range in inches is from 1/16 to 24. This thread of the American standard is a kind of cylindrical thread. It differs from domestic only in profile angle size.
Conclusions and useful video on the topic
The author talks about the nuances and problems that arise when connecting pipes during the installation of sewers:
The author of this video shares the method of solving his problem:
Properly connecting the pipes is very important. Articulation has always been the weakest point in the pipeline. If it is executed with errors, then, as a result, leaks, blockages, and sometimes pipe ruptures will occur.
Therefore, before proceeding with the independent installation of plumbing communications, you need to study all the existing connection methods. If things seem complicated, you can always turn to plumbers.
Tell us about your own experience gained during the assembly of plumbing systems. It is possible that you know the nuances of editing and forming connections that will be useful to site visitors. Please write comments in the block below, post photos with the steps of the process, ask questions.
Is it necessary to use a sealant when making threaded connections? If so, which one is better to use? Linen, fumlent or Tangit thread?
The sealant is not needed everywhere, depending on the type of connection. As for which one to choose, flax is the last century, not everyone can use the fum tape correctly, and this is more a temporary option, modern polymer and anaerobic sealants should be used.