Press fittings for plastic pipes: types, marking, purpose + installation example
Metal-plastic pipes are connected by compression fittings for clamping and their analogues for crimping. Installation of pipelines in both cases does not require sophisticated equipment and high qualifications from the master.
The first method is simpler to implement, but not so reliable. But press fittings for metal pipes give the opportunity to form a durable system with minimal risk of rupture.
We will figure out what types of connecting elements are on sale, how to choose the right press fitting and carry out its installation.
The content of the article:
General description of crimp couplings
Press-fitting connection is one of the most reliable ways of joining metal-plastic pipes. The pipeline as a result of this installation is one-piece, but very reliable. If after assembly it will be necessary to change its scheme, then a lot will have to be redone again, but leaks are practically eliminated.
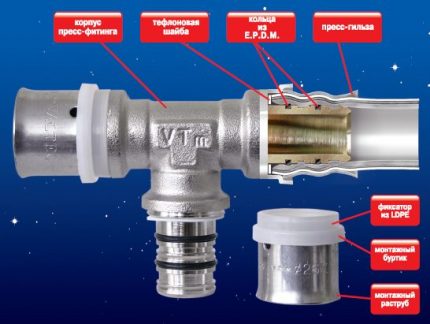
Press fittings are an integral form of joints obtained in this case by crimping a metal sleeve around the o-ring. Moreover, as a result of crimping, the ring is irreversibly deformed. Remove it and then reuse impossible. The geometry of the pipe itself changes slightly.
For metal-plastic pipes, fittings for crimping are made of such materials:
- brass;
- stainless steel.
The first option is more preferable. It is more reliable and durable in conditions of high humidity.
Unscrupulous manufacturers often use aluminum and other soft metals to make the fittings in question. They can be easily identified by weight - brass in the hands is obviously heavier than these fakes.
The use of such products for crimping metal pipes is strictly not recommended. They, by definition, are not able to tightly compress the fitting and pipe plastic.
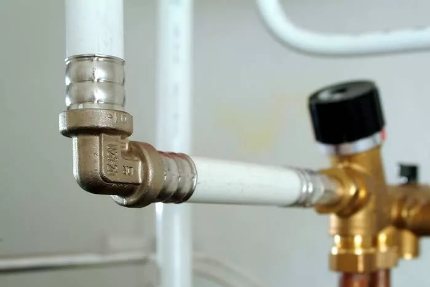
Each manufacturer of metal-plastic pipes recommends purchasing their own set of press fittings. And not in vain. Pipe products and fittings from different manufacturers can vary in diameter literally by a millimeter.
Quite a bit, but this is enough to reduce the reliability of the connection. It is better not to save here, at the risk of getting a rush and leak.
There is no single standard for shape and exact dimensions for fittings. Each of the manufacturers independently chooses these parameters for their products.
Some sellers offer universal press fittings, but this is a commonplace advertising ploy. The use of such connecting parts is inevitable and in the near future after installation will result in leaks.
Types of press fittings for metal pipes
The considered connecting elements in the plumbing market are:
- crosses;
- tees;
- angles;
- couplings with union nut;
- adapters with external and internal thread.
Such variety of fittings allows you to assemble a metal-plastic pipeline of any configuration and purpose. There are no restrictions here.
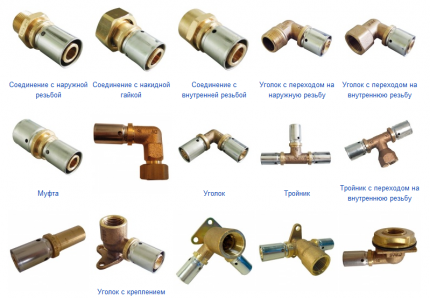
According to the method of crimping sleeves, press fittings are divided into crimp and sliding. In the first case, the ring is crimped with special pliers. In the second, it is pulled onto the fitting using a hydraulic or manual press.
Depending on their shape, press fittings are used for various purposes.
Type # 1: Crimp
The sleeve on such a press fitting can be a separate element or a component immediately fixed to the body. After the nozzle, the compression of the metal-plastic pipe on the fitting is carried out press pliers. This tool is specialized and is not intended for other purposes.
It can be used exclusively for mounting pipelines by squeezing a crimped metal ring.
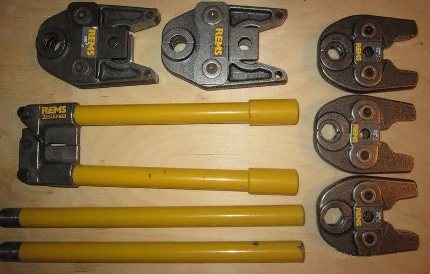
Installation of metal-plastic pipes with crimping press fittings is carried out as follows:
- The required pipe length is prepared - use for cutting pipe cutter for plastic pipes.
- From the end of this segment, the inner chamfer is removed.
- To get rid of the ovality that occurs as a result of squeezing the plastic with a cutting tool, a caliber is used.
- A crimp ring is put on the pipe.
- A dielectric gasket and o-rings are put on the fitting, and then it is pressed into the pipe.
- The metal clutch is crimped using press tongs.
If everything is done correctly, then on the ring two pronounced depressed strips should form on the entire circumference. Moreover, these zones of maximum compression should not coincide with the places where rubber o-rings are placed on the fitting.
When crimping, it is imperative to avoid the formation of excess voltage in the sealant material. Do not allow excessive squeezing.
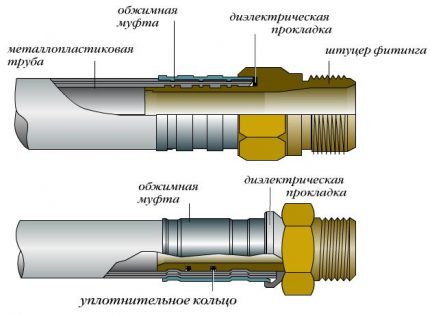
Sealing gaskets are designed to compensate for temperature deformations in the walls of the pipe. If you squeeze them during the crimping of the press fitting, then the rubber will lose its elastic properties, and then, when the temperature of the water changes, the plastic will gradually collapse.
As a result, instead of 20-30 years declared by manufacturers, the press connection will last from 5-10 strength.
The pipe on the fitting must be fully inserted. To prevent plumbing from making mistakes here, many crimp couplings have small holes through which white plastic is perfectly visible. It is only necessary to make a little effort, and then squeeze the fitting with pliers.
The resulting compound can safely be bricked into concrete. Without leaks, it will last as much as the metal-plastic pipes themselves.
Type # 2: Press-fit (sliding)
The second option of press fittings does not imply crimping the ring, but pulling it onto the pipe into which the fitting is inserted. A similar connection is obtained no less durable than in the first case with crimping.
Only for installation of metal-plastic pipes by fittings using a pressing method, not a pliers are used, but a special press.
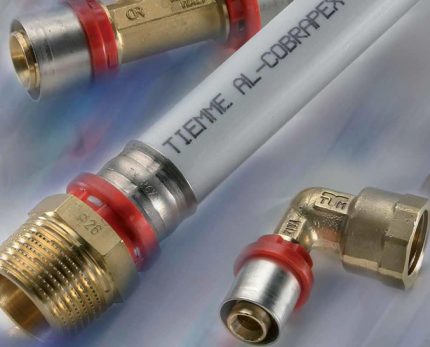
To connect plastic pipes with press-fit press fittings, four steps must be performed in sequence:
- Put a metal ring on the pipe.
- Extend the diameter of the pipe by treating its end with an expander.
- Push the fitting into the intended place for it until it stops.
- Clamp the sliding sleeve with the jaws of the press and press it onto the fitting.
This method involves the use of an expander in addition to the press tool. It is designed to expand the pipe at the cut point. Without this, it is impossible to pull it onto the fitting. All diameters are designed in such a way that it is impossible to do it manually without preliminary preparation.
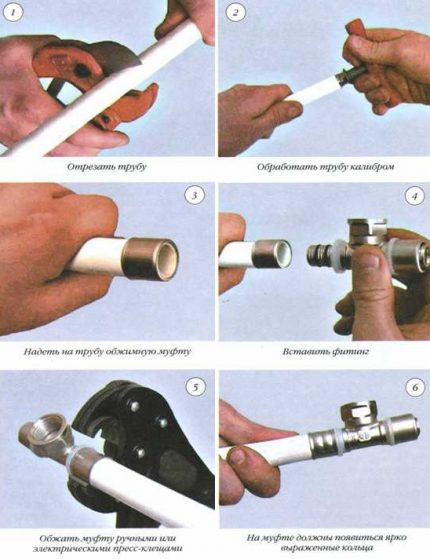
Reliability of the connection is ensured on the one hand by a sliding ring, and on the other, by the properties of cross-linked polyethylene, of which metal-plastic pipes are made. After expansion and nozzles on the fitting, this plastic tries to regain its original size.
The inevitable and tight compression of the fitting connector occurs. And from above all this is still pulled together by a ring of metal.
For the installation of sliding press fittings, the tool is available both manual and battery-powered, as well as electric from the mains. If you have to connect a lot of pipes, then you should choose the second option. For one-time work, a cheaper manual analogue is quite enough. Special efforts when crimping this fitting is not necessary.
Differences from compression analogues
Due to inexperience and ignorance of all the nuances of installing pipes made of metal-plastic, press fittings can be confused with compression fittings. They also have a fitting and a sleeve. Only the compression of the latter is carried out not by a tool, but by means of the union nut available in the design.
The main difference between these parts is the different type of connection obtained as a result of the installation. The compression option, if necessary, can be disassembled, but with the oppressed, this will not work. It is only possible to cut off the press fitting from the pipe to replace it with a new one.
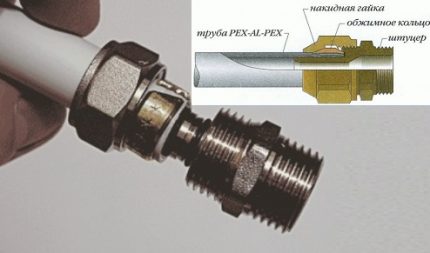
However, the likelihood of leaks in the press joint is practically zero. It is not for nothing that this installation method is recommended for underfloor heating under the screed and when monoling the pipelines into the wall.
Cases when such fittings begin to flow in concrete are extremely rare in the practice of plumbers. This is more an exception to the rule.
On the other hand, the installation of both types of press fittings requires specialized tools. And to tighten the nuts of the compression products, only a couple of wrenches are needed.
As a result - on one side of the scale “expensive tools + higher reliability of the joint”, and on the other “absence of unnecessary expenses + slightly higher risk of leaks”. The choice is only for the master and owner of the house where the pipeline is laid.
Features of installation and selection of fittings
Cross-linked polyethylene plastic pipes were not originally intended for welding and gluing. Welds on them after a couple of months will still crack and split. And the glue is not used because of the resistance of this plastic to solvents and its low adhesion. It remains for installation to use only specialized fittings.
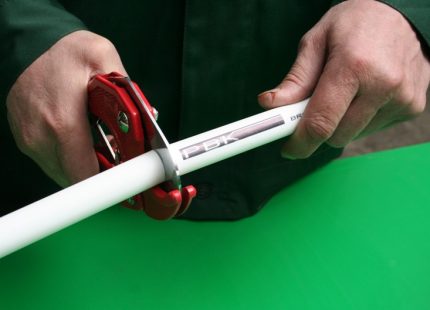
When choosing a press fitting, the focus should be on the crimp ring. It should be made of durable metal. And no seams on this metal surface, only cast seamless stamping. Any seam is a point for destruction.
It is better to immediately reduce or completely eliminate the likelihood of a rupture of the pipeline with flooding of the house. It's not worth pursuing cheapness here for sure.
The sizes of the press fitting are indicated in the marking both on the ring and on its body. Similar information is contained on the pipe. Everything should match.
Once again - do not purchase fittings and metal pipes different manufacturers.In most cases, this discrepancy leads to problems at the installation stage, and then during operation.
After crimping the fitting, do not bend the pipe next to the latter. This can lead to excessive stress in the connection. It is also unacceptable to apply any lateral force to the press fitting. It itself will not be damaged, but the plastic nearby can collapse.
Additional information on the installation and crimping of plastic pipes is given in the articles:
- DIY installation of plastic pipes: connection technology + wiring examples
- Pressure testing of metal-plastic pipes: instructions and tips for performing work
Conclusions and useful video on the topic
Installation of the fittings in question should not cause problems. However, the nuances when performing the connection of metal-plastic pipes do exist. And before you begin, we recommend that you watch the video instructions below to avoid newbie mistakes.
Comparison of compression compression fittings and press fittings:
Step-by-step instructions for crimping press fittings:
Overview of the pros and cons of crimp fittings:
Manufacturers of metal-plastic pipes give their products a guarantee of up to half a century. However, the pipeline system of them will work all these decades only if the fittings are installed correctly. Do not skimp. To assemble a pipeline made of metal-plastic, exclusively high-quality connecting parts should be purchased.
Press fittings must be compatible with the mounted pipes. The best option is when all the components are made by one manufacturer. Fortunately, their selection on the market is now extensive, there are plenty to choose from.
Is there anything to supplement, or have questions about the use of press fittings for plastic pipes? Please leave comments on the publication. The contact form is located in the lower block.
And what specific fittings for plastic pipes can you recommend? The price is not important (within reasonable limits), the main thing is that the quality is.
If you are interested in specific manufacturers, then not everything is so simple. The rule is, the more expensive, the better in this case it is better not to apply. And for big money, believe me, you can buy a frankly bad fitting.
The question is still not clear which type of connection you are interested in:
- crimp fitting;
- coupling;
- saddle insert;
- corner fitting, etc.
Metal or propylene? What fitting material? If you just recommend normal manufacturers for the price / quality ratio, then this is: Koer, Klondajk.